Збагачення вугілля
Процеси збагачення вугілля полягають у розділенні гірничої маси на основі відмінностей у властивостях її складових (густини, змочуваності, крупності, твердості та ін.). Послідовні прийоми механічної обробки гірничої маси, здійснювані з метою зміни її якості або розділення на продукти різної якості, називаються технологічними операціями.
Вступ
Вугілля є одним із найважливіших видів паливно-енергетичної сировини. Частка вугілля у світовому енергетичному балансі складає близько 25 %. Запаси вугілля, які економічно доцільно розробляти, досить великі (вони в багато разів перевищують запаси нафти і газу), і в майбутньому вугілля може відіграти головну роль у вирішенні проблеми задоволення зростаючої потреби в енергії.
Вугілля використовують для багатьох цілей, зокрема для виробництва металургійного коксу, хімічних продуктів, електроенергії, електродної продукції, карбіду, при агломерації залізних руд і для інших технічних і технологічних потреб. Основні споживачі вугілля – теплові електростанції (42 %), чорна металургія (20 %), котельні й комунально-побутове господарство (16 %) та інші (заводи напівкоксування, установки з виробництва електродних наповнювачів, адсорбентів, термографіту, сульфовугілля та ін.).
Зольність вугілля для коксування не повинна перевищувати 8–10 %. Збільшення зольності коксу на 1 % спричиняє його перевитрати на виплавку чавуну в доменній печі на 2,5 % і зниження продуктивності печі на 4 %. В енергетичному вугіллі підвищена зольність призводить до зниження теплоти згоряння. Вугілля, яке використовують для виробництва синтетичного бензину, повинно мати зольність не більше 5–6 % при вологості 2 %; для виготовлення електродів необхідне вугілля із зольністю не більше 2–3 %. Підвищення зольності вугілля на 1 % знижує його ціну на 2,5 %.
Для задоволення потреб економіки Україна щорічно використовує близько 100 млн т вугілля, з яких майже 80 млн т видобувається вітчизняними підприємствами Донецького, Дніпровського і Львівсько-Волинського вугільних басейнів.
Зі зростанням видобутку безперервно збільшується абсолютна маса вугілля, що направляється на збагачення, сортування і брикетування. Ріст обсягу збагачуваного вугілля обумовлюється вимогами підвищення їхньої якості, що визначає економічну ефективність використання вугілля. Крім того, внаслідок погіршення гірничо-геологічних умов видобутку вугілля, широкої механізації виробництва та інших причин його якісна характеристика за зольністю, гранулометричним складом, вологістю і вмістом сірки погіршується.
Вуглезбагачення – крупна підгалузь вугільної промисловості. Сучасні вуглезбагачувальні фабрики – потужні повністю механізовані підприємства з частковою або повною автоматизацією окремих технологічних процесів і операцій, оснащені передовою технологією і високопродуктивним обладнанням. Основний напрямок технічного прогресу в вуглезбагаченні, який забезпечує підвищення технологічних і техніко-економічних показників, – це концентрація виробництва в результаті будівництва нових великих фабрик, реконструкції і технічного переобладнання чинних підприємств на основі передової технології і нової техніки.
На вуглезбагачувальних фабриках застосовуються високоефективні методи збагачення: важкосередовищна сепарація, відсадка і флотація. У великих масштабах освоєна технологія збагачення у важкосередовищних гідроциклонах. Постійно зростає роль флотації вугілля, яка дозволяє вирішити дві важливі задачі – припинення випуску енергетичного шламу на фабриках, що переробляють коксівне вугілля, і переведення фабрик на раціональні схеми обробки шламових вод з повністю замкненим водно-шламовим циклом. Усе частіше застосовується технологія збагачення енергетичного вугілля дрібних класів. Збагачення вугілля в останні роки спрямовано на вирішення задач комплексного використання їхньої органічної і мінеральної складових. Особливого значення набуває розширення галузі застосування вугілля для виробництва газів, рідких палив та інших технологічних потреб, зокрема для виготовлення електродів і вуглецевих блоків, які застосовуються як відновники при електротермічних процесах виробництва кольорових металів, агломерації залізних руд та ін. Визначаються технічні можливості широкого використання мінеральної складової вугілля в глиноземному виробництві й виробництві будівельних матеріалів. Велика роль приділяється розробці й освоєнню високопродуктивного обладнання, без якого неможливо створити потужні й ефективні збагачувальні фабрики. Окремі види вітчизняного обладнання не мають аналогів за кордоном, наприклад, крутопохилі сепаратори типу КНС для збагачення розубоженої гірничої маси, апарат для кондиціонування флотаційної пульпи АКП-1600, відсаджувально-фільтрувальна центрифуга НОГШ-1320Ф, трипродуктові гідроциклони. Темпи розвитку збагачення вугілля повинні випереджати темпи збільшення його видобутку, що обумовлює необхідність подальшого удосконалення техніки і технології збагачення вугілля, особливо в галузі комплексного і раціонального використання органічної та мінеральної складової вугілля.
Збагачення вугілля реалізується головним чином гравітаційними методами та флотацією. При цьому для збагачення вугілля використовуються майже всі гравітаційні процеси.
Продукти збагачення вугілля
Продукт, що надходить в операцію, зветься вихідним або живленням операції. У процесі переробки гірничої маси одержують наступні продукти: концентрат – продукт із найбільшим вмістом горючої маси і найменшим породних компонентів; промпродукт – проміжний продукт, що за вмістом горючої маси не є кондиційним концентратом чи відвальними відходами і потребує подальшої переробки; промпродукт – це суміш зростків вугільних і породних компонентів та суміші їхніх розкритих зерен (мікст); відходи – продукт із найбільшим вмістом породних мінералів і найменшим органічної маси.
Процеси збагачення
За технологічним призначенням процеси переробки вугілля на збагачувальних фабриках підрозділяються на:
- – підготовчі процеси, призначені для розкриття компонентів гірничої маси, розділення її на машинні класи, попереднього знешламлення тощо. До підготовчих операцій в схемах переробки вугілля відносять операції дроблення і грохочення.
- Дроблення – процес руйнування грудок під дією зовнішніх сил для отримання продукту заданої крупності. Дроблення застосовується для підготовки вугілля перед збагаченням (розкриття зростків, зниження крупності), а також при приготуванні шихти для коксування і брикетування.
- Грохочення – процес механічного розділення вугілля за крупністю на просіюючих поверхнях. На вуглезбагачувальних фабриках застосовують грохочення: попереднє (відділення крупних грудок для наступного дроблення), підготовче (розділення вугілля на машинні класи), остаточне (розділення концентрату на товарні сорти), зневоднююче (відділення основної маси води з продуктів збагачення, відділення суспензії, знешламлення);
- – основні, або збагачувальні процеси, призначені для власне розділення вихідного продукту на концентрат, відходи та промпродукт, для чого використовують відмінності в фізичних і фізико-хімічних властивостях частинок вугілля і породи.
- Гравітаційні процеси збагачення вугілля на сьогодні одержали найбільше розповсюдження. Вони основані на використанні різниці у густині, крупності і формі вугільних і породних частинок і отже різної швидкості їх руху у середовищі (воді, повітрі. суспензії). На вуглезбагачувальних фабриках застосовують такі гравітаційні процеси: збагачення у важких суспензіях, відсадку, гвинтову і протитечійну сепарацію. Гравітаційні процеси використовують для збагачення вугілля в широкому діапазоні крупності від 0,2 мм (гвинтові сепаратори, важко-середовищні гідроциклони), до 200–300 мм (важкосередовищні сепаратори).
- Флотація основана на використанні різниці в фізико-хімічних властивостях частинок вугілля і породи (частинки вугілля – гідрофобні, частинки породи – гідрофільні). Флотація використовується для збагачення тонких і дрібнодисперсних класів вугілля крупністю до 0,5 мм;
– допоміжні, або заключні процеси, застосовувані для згущення, зневоднення, знешламлювання, знепилювання і регенерації оборотних вод.
- Зневоднення продуктів мокрого збагачення вугілля здійснюють різними способами залежно від крупності матеріалу. Продукти крупністю більше 13 мм зневоднюються на грохотах, елеваторах з перфорованими ковшами, а також у дренажних бункерах. Для зневоднення дрібних класів крім названих способів застосовують центрифугування, а в зимовий період і термічну сушку. Найбільші труднощі складає зневоднення продуктів флотації і шламів, для зневоднення яких застосовують згущення, фільтрування і термічну сушку. При згущенні і фільтруванні відбувається також процес регенерації оборотних вод.
- Знепилення – процес відділення з вугілля частинок пилу розміром менше 0,5 мм. Знепилення здійснюється двома способами: мокрим – на грохотах і у гідроциклонах (знешламлення) і сухим – на грохотах і в повітряних класифікаторах різних конструкцій.
Глибина збагачення вугілля
Глибина збагачення вибирається у такий спосіб:
- – коксівне вугілля з високими виходом і зольністю класу –0,5 мм переробляють за схемами із глибиною збагачення 0 мм;
- – коксівне вугілля з низькими виходом і зольністю класу –0,5 мм переробляють за схемами із глибиною збагачення 0,5 мм, а клас –0,5 мм додається до концентрату в незбагаченому вигляді;
- – глибина збагачення енергетичного вугілля становить 6, 13, іноді 25 мм. У цьому випадку глибина збагачення залежить від відстаней, на які перевозять вугілля, і від потужності котельних установок. На великих котельних установках, обладнаних пиловугільними топками, можливе спалювання високозольного вугілля при високих к.к.д. Тому вугілля, призначене для спалювання у великих котельнях, при невеликих відстанях перевезення звичайно не збагачується;
- – енергетичне вугілля гідровидобутку переробляють за схемами із глибиною збагачення 0,5 мм, іноді 0 мм.
За нормами технологічного проектування рекомендується в проектах збагачувальних фабрик приймати глибину збагачення вугілля 0 мм, але при цьому питання про найвигіднішу глибину збагачення повинно вирішуватися на основі техніко-економічних розрахунків.
Схеми збагачення вугілля
Схему збагачення вугілля вибирають залежно від його властивостей і призначення.
За глибиною збагачення можна виділити такі технологічні схеми:
- – збагачення тільки крупних класів розміром більше 25 (13) мм із роздільним або спільним відвантаженням продуктів збагачення і незбагачених відсівів;
- – збагачення крупних і середніх класів розміром більше 6 (3) мм зі спільним або роздільним відвантаженням продуктів збагачення і незбагачених відсівів;
- – збагачення зернистого вугілля крупністю більше 0,5 мм зі спільним відвантаженням продуктів збагачення і незбагачених шламів;
- – збагачення всіх класів крупності.
За якістю концентрату і асортиментом продуктів збагачення технологічні схеми розрізняють:
- – з випуском одного товарного продукту. Схема набула поширення при збагаченні енергетичного вугілля таких марок, з яких не виділяють сорти за класами крупності, наприклад, вугілля марки П;
- – з випуском одного товарного продукту і розділенням його на сорти за класами крупності. Схема застосовується при збагаченні антрацитів і енергетичного вугілля, з якого виділення сортів за класами крупності є доцільним, наприклад, при збагаченні вугілля марок Г і Д;
- – з випуском двох товарних продуктів (концентрату і промпродукту). Схема використовується при збагаченні вугілля для коксування та інших технологічних цілей. Застосовується у випадку, якщо до якості концентрату висуваються підвищені вимоги, що визначає збагачення усього рядового вугілля (крупного, дрібного, шламів). Одним з різновидів цієї схеми може бути випуск концентратів двох сортів – зі зниженою зольністю для технологічних потреб і з підвищеною зольністю для енергетичних цілей;
- – з випуском двох товарних продуктів і поділом одного з них на сорти за класами крупності. Схема набула поширення при збагаченні газового вугілля для коксування, якщо доцільним є виділення крупного класу для комунально-побутових або спеціальних потреб, а також при глибокому збагаченні антрациту з випуском концентрату для технологічних цілей, що зв’язано з виділенням промпродукту.
Особливості збагачення вугілля у сучасних умовах
У сучасних умовах видобування, які характеризуються підвищеним вмістом породних домішок у вугіллі, особливо у крупних класах, поширення набули схеми із застосуванням ефективних процесів збагачення: важкосередовищної сепарації, відсадки, флотації, гвинтової сепарації. Схеми збагачення вугілля і процеси, що їх реалізують, вибираються у залежності від багатьох факторів, основними з яких є: призначення вугілля, його мінералогічний, гранулометричний і фракційний склад, вологість, вміст в зольність крупних і дрібних класів, глибина збагачення. Збагачення вугілля крупністю більше 0,5 мм здійснюється гравітаційними процесами, крупністю менше 0,5 мм – флотацією. Але технологічні схеми вуглезбагачувальних фабрик значно відрізняються, що у першу чергу обумовлюється характеристикою збагачуваного вугілля і вимогами до якості і асортименту товарних продуктів збагачення.
Сучасні умови видобутку характеризуються підвищеним вмістом породних домішок у видобутому вугіллі, особливо в крупних класах. Тому основною метою збагачення вугілля є видалення мінеральних домішок (породи), що потрапили при видобутку з покрівлі і ґрунту пласта, а також у вигляді прошарків. Крім того, збільшення вмісту дрібних і тонких класів в рядовому вугіллі спричинило значне утворення шламових продуктів, у тому числі крупнозернистих шламів крупністю 0,5–3 мм. Це обумовило необхідність знешламлення вугілля перед гравітаційними процесами збагачення і класифікації шламів перед флотацією. Зміна якості рядового вугілля, необхідність скорочення втрат з відходами, підвищення вимог до охорони навколишнього середовища, асортименту і якості товарних продуктів збагачення, а також збільшення потужності фабрик і прагнення до однопоточності визначили напрямки розвитку технологічних схем, апаратурного оснащення вуглезбагачувальних фабрик і застосування збагачувального і допоміжного обладнання високої ефективності і великої продуктивності. Один з таких напрямків – усунення суттєвого розходження в технологічних схемах збагачення коксівного і енергетичного вугілля по відношенню до глибини збагачення. При цьому зберігається відмінність у схемах, яка визначається режимами розділення і полягає у тому, що при збагаченні коксівне вугілля розділяється на три продукти (концентрат, промпродукт, відходи), а енергетичне – на два (концентрат, відходи).
Комплекс підготовки вугілля до збагачення
Комплекс підготовки вугілля до збагачення (підготовча класифікація) включає обладнання для розділення на машинні класи і знешламлення дрібного машинного класу. Слід передбачати :
– при глибині збагачення 25 мм і вологості менше 7 % – суху класифікацію ;
– при глибині збагачення 25 мм і вологості більше 7 %, а також при глибині збагачення 13 мм незалежно від вологості, як правило, суху класифікацію з подальшим знешламленням крупного машинного класу (при вологості рядового вугілля більше 12 % для кам'яного вугілля і антрацитів і вмісті глинистих частинок в породі більше 50 % суху класифікацію передбачати не слід);
– при глибині збагачення 6 мм і вологості менше 7 % – суху класифікацію з подальшим знешламленням крупного класу;
– при глибині збагачення 6, 0,5 і 0 мм і вологості більше 7 %, а також при вмісті глинистих частинок в породі більше 50 % – мокру класифікацію з подальшим знешламленням надрешітного продукту;
– при збагаченні дрібного машинного класу для знешламлення перед відсаджувальними машинами – установку конусних грохотів (для вугілля з породами, що не розмокають, і вмістом фракцій густиною менше 1300 кг/м3 до 10 % допускається застосування багер-класифікаторів);
– при збагаченні дрібного машинного класу для знешламлення перед важкосередовищними гідроциклонами – установку конусних грохотів або багер-класифікаторів (перша стадія) і вібраційних грохотів (друга стадія).
Збагачення коксівного вугілля
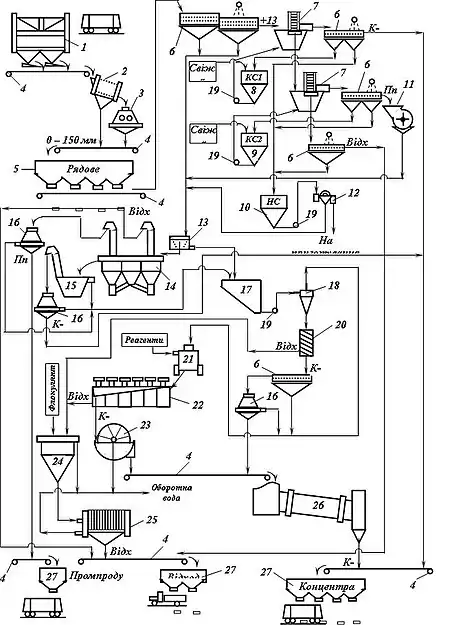
Типова схема збагачення коксівного вугілля наведена на рис. 1. Рядове вугілля, що надходить на збагачувальну фабрику, у відділенні вуглеприйому піддається сухому попередньому грохоченню (грохоти ГЦЛ) і дробленню (дробарки ДДЗ). Підготовлене за крупністю рядове вугілля надходить у головний корпус збагачувальної фабрики, де його розділяють на машинні класи (грохоти ГІСЛ), знешламлюють (грохоти ГК) і направляють на збагачення.
В умовах збагачення вугілля з підвищеним вмістом породних домішок воно здійснюється із застосуванням у схемах ефективних процесів: важкосередовищної сепарації, відсадки, флотації, гвинтової сепарації.
Важкосередовищна сепарація використовується для збагачення крупних класів вугілля і антрацитів дуже важкої, важкої і середньої збагачуваності, усіх категорій збагачуваності при вмісті класу +13 мм у гірничій масі понад 20%, а також для вугілля легкої збагачуваності при вмісті породних фракцій понад 30 %.
Технологічні схеми збагачення крупних машинних класів у магнетитовій суспензії розділяють за числом стадій збагачення, числом кінцевих продуктів і призначенням.
Підготовка крупного машинного класу до важкосередовищного збагачення в сепараторах типу СКВ, у першу чергу полягає у ефективному його знешламлюванні. Свіжа суспензія перед надходженням у сепаратор розділяється на транспортний і висхідний потоки. Густина розділення залежно від характеристики збагачуваного вугілля і вимог до якості концентрату приймається від 1650 до 2050 кг/м3.
Відділення суспензії і відмивка обважнювача (магнетиту) здійснюється на вібраційних грохотах типу ГІСЛ. При цьому відмивання обважнювача здійснюється за допомогою двох рядів бризкал, на перший з яких подається злив сепараторів (типу ЕБМ) системи регенерації, а на другий – технічна вода. Схема збагачення у дві стадії з виділенням трьох кінцевих продуктів (концентрату, промпродукту і відходів) застосовується для коксівного вугілля середньої і важкої збагачуваності.
Основний і найбільш економічний варіант – виділення в першій стадії сепарації концентрату; виділення в першій стадії відходів застосовується при їхньому високому виході (більш 50 %) і наявності порід, що розмокають в рідині. Робоча суспензія високої і низької густини подається у відповідні сепаратори для створення транспортного і висхідного потоків.
Збагачення у важкосередовищних гідроциклонах застосовується при переробці дрібних класів коксівного вугілля і антрацитів дуже важкої і важкої збагачуваності, а при підвищених вимогах до якості концентрату – середньої збагачуваності. Важкосередовищні гідроциклони можуть використовуватися також для перезбагачення промпродукту і грубозернистого шламу. Технологічні схеми важкосередовищних гідроциклонних комплексів для збагачення дрібного вугілля так само, як і схеми збагачення крупних класів, відрізняються за числом стадій розділення, числом продуктів збагачення і своєму призначенню. Технологічні схеми збагачення в гідроциклонах типу ГТ складніші від схем збагачення в сепараторах, тому що вимагають створення тиску на вході в апарат, більших в 3–4 рази витрат суспензії і складнішої системи регенерації суспензії в зв’язку зі значним шламоутворенням у гідроциклоні.
До якості машинного класу, що надходить на збагачення в гідроциклони, висуваються підвищені вимоги, і насамперед щодо вмісту шламів. Щодо крупного класу знешламлення здійснюється за класом 13 (25) мм, дрібного звичайно – за класом 0,5 мм.
Схема збагачення за одну стадію в двопродуктовому важкосередовищному гідроциклоні з одержанням двох кінцевих продуктів (концентрату і відходів) призначена для збагачення дрібного енергетичного вугілля і антрацитів крупністю 0,5–13 (25) мм.
Схема збагачення за одну стадію в трипродуктовому каскадному гідроциклоні з одержанням трьох кінцевих продуктів (концентрату, промпродукту, відходів) і одержанням у першій секції апарата концентрату, у другій промпродукту і відходів, призначена для збагачення дрібного коксівного вугілля крупністю 0,5–13 (25) мм, перезбагачення промпродукту відсадки дрібного машинного класу 0,5–13 мм, а також для збагачення коксівного вугілля одного машинного класу 0,5–40 мм (при порівняно невеликому виході класу + 40 мм).
Відсадка застосовується для збагачення дрібних класів вугілля й антрацитів легкої і середньої збагачуваності. Допускається застосування відсадки для збагачення дрібних класів вугілля й антрацитів важкої збагачуваності, а також для збагачення крупних класів вугілля легкої збагачуваності при вмісті породних фракцій менше 30 %. Для вугілля, що видобувається гідроспособом, а також вугілля легкої збагачуваності з вмістом класу +13 мм менше 20 % варто застосовувати ширококласифіковану відсадку.
Залежно від характеристики вихідного вугілля, вимог до якості кінцевих продуктів і техніко-економічних міркувань можуть бути застосовані різні схеми з використанням відсадки. При роздільному збагаченні крупних і дрібних класів вугілля відсадкою воно розділяється на грохотах і направляється у відсаджувальні машини типу МО, у яких розділяється на три продукти (концентрат, промпродукт і відходи). Промпродукт, одержуваний у результаті збагачення крупного класу, дробиться до 13 мм і направляється на збагачення разом із дрібним машинним класом. При збагаченні коксівного вугілля у некласифікованому вигляді його розділення на класи відбувається тільки в подальших стадіях. Концентрат і промпродукт після відсадження піддаються грохоченню за розміром 13 або 25 мм із метою виділення дрібних класів перед їх зневоднюванням у фільтрувальних центрифугах типу ФВВ, ФВШ або ФВІ.
На фабриках, які збагачують енергетичне вугілля і де виділення промпродукту не передбачається, відходи виділяються в обох секціях відсаджувальної машини. Іноді важкий продукт другої секції направляють у вигляді циркулюючого продукту в ту ж машину.
Крупний концентрат зневоднюється на грохотах, промпродукт і відходи – у елеваторах. Зневоднення дрібного концентрату здійснюється у дві стадії: у елеваторних класифікаторах і центрифугах (ФВВ, ФВШ, ФВІ), зневоднення промпродукту – у зневоднюючих елеваторах і центрифугах, зневоднення відходів – у елеваторах.
Гвинтова сепарація застосовується для збагачення вугільних шламів і відсівів легкої і середньої збагачуваності крупністю 0,1–3 мм. Живлення гвинтових сепараторів (СВ) бажано знешламлювати. При вмісті в живленні понад 15–20 % глинисто-мулистого матеріалу попереднє знешламлювання обов’язкове. Концентрат гвинтових сепараторів послідовно зневоднюється на грохотах типу ГЛВК, центрифугах ФВВ і сушиться сумісно з флотаційним концентратом. Залежно від зольності живлення гвинтова сепарація може застосовуватися як самостійно, так і в поєднанні з флотацією.
Флотація – це найефективніший метод збагачення вугільних шламів. Схеми флотації, що приймаються, визначаються маркою збагачуваного вугілля, його зольністю, вмістом тонких класів і проміжних фракцій, складом неорганічної частини і особливо наявністю глинистих порід, що піддаються розмоканню, вимогами щодо якості кінцевих продуктів і техніко-економічними показниками. Для флотації вугільних шламів застосовують машини типу МФУ.
При низькій зольності вихідних шламів (не більше 18—20 %) і легкій збагачуваності рекомендується проста, так звана пряма схема. При флотації шламів більш важкої збагачуваності і більшій їх зольності застосовують різні схеми з перечищенням концентрату. Найбільшого поширення набула схема з перечищенням концентрату останніх камер у машині основної флотації. Іноді при особливо високозольних шламах застосовують схеми з перечищенням усього концентрату основної флотації. Перечищення концентрату може здійснюватися або в окремій флотаційній машині, або в окремих камерах машини основної флотації. Перечищення в окремих машинах або камерах доцільніше, тому що для цієї операції потрібний режим, відмінний від режиму основної флотації.
Зневоднення флотаційного концентрату здійснюється фільтруванням у дискових вакуум-фільтрах типу ДУ і сушінням. Відходи флотації сумісно з відходами гвинтових сепараторів згущуються у циліндроконічних згущувачах типу С-10 і зневоднюються у фільтр-пресах типу ФПМ. Застосування у технологічних схемах фільтр-пресів дозволяє здійснити на вуглезбагачувальних фабриках замкнений цикл по воді.
Збагачувальне обладнання великої одиничної продуктивності у поєднанні з високопродуктивними транспортними пристроями дозволяє застосовувати раціональні технологічні схеми, які забезпечують скорочення довжини трактів, числа одиниць обладнання, енергоємності і трудомісткості виробничих процесів на збагачувальних фабриках.
Перспективні технологічні схеми
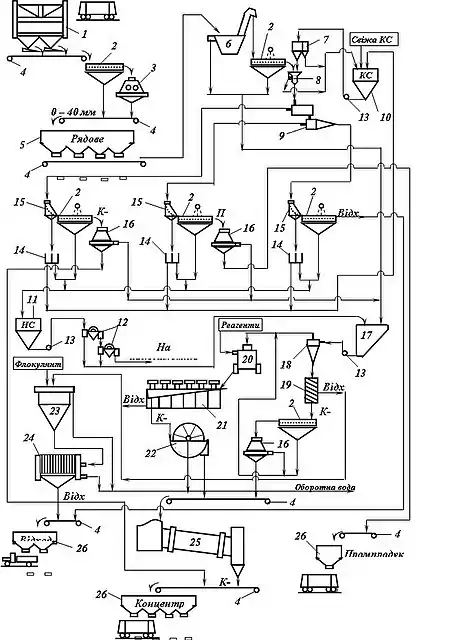
Перспективними технологічними схемами для реалізації цих напрямків є:
- – при збагаченні вугілля для коксування важкої збагачуваності – технологічні схеми зі збагаченням усього вугілля у циклонах з важким середовищем, гвинтовою сепарацією і флотацією шламів (рис. 2.);
- – при збагаченні вугілля легкої і середньої збагачуваності – технологічні схеми з розділенням крупних класів у важкосередовищних сепараторах на три продукти з відсадкою дрібних класів сумісно з дробленим крупним промпродуктом, гвинтовою сепарацією і флотацією шламів. У цих схемах повинен бути вузол обробки відходів збагачення шламів до товарної паливно-сировинної добавки при виробництві стінових матеріалів;
- – при збагаченні антрацитів і енергетичного вугілля – технологічні схеми з застосуванням важкосередовищних сепараторів для збагачення крупних класів, циклонів для збагачення дрібних класів антрацитів і двопродуктових відсаджувальних машин для збагачення дрібних класів кам’яного вугілля, гвинтової сепарації для збагачення крупнозернистих шламів і флотації – для тонкозернистих шламів. У цих схемах також повинен бути вузол обробки відходів збагачення шламів до товарної паливно-сировинної добавки при виробництві стінових матеріалів.
Див. також
- Вугілля
- Збагачення корисних копалин
- Вуглезбагачувальні фабрики України
- Утилізація відходів вуглезбагачення
- Нетрадиційні методи гравітаційного збагачення вугільних шламів
- Збагачення вугільних шламів на конусних сепараторах
- Збагачення вугільних шламів на гідросайзерах
- Вугільний концентрат
- Відходи вуглезбагачення
Література
- Смирнов В. О., Сергєєв П. В., Білецький В. С. Технологія збагачення вугілля. Навчальний посібник. — Донецьк: Східний видавничий дім, — 2011. — 476 с.
- Обогащение ультратонких углей / А. Т. Елишевич, Н. Д. Оглоблин, В. С. Белецкий, Ю. Л. Папушин. — Донецк: Донбасc, 1986. — 64 с.
- Білецький В. С., Смирнов В. О., Сергєєв П. В. Моделювання процесів переробки корисних копалин: Посібник / НТУ «Харківський політехнічний інститут», Львів: «Новий Світ- 2000», 2020. — 399 с.
- Білецький В. С., Олійник Т. А., Смирнов В. О., Скляр Л. В. Основи техніки та технології збагачення корисних копалин: навчальний посібник. — К.: Ліра-К 2020. — 634 с.