Прийом і складування корисної копалини на збагачувальній фабриці
Прийом і складування корисної копалини на збагачувальній фабриці — перша операція, з якої починається технологічна підготовка корисної копалини до збагачення, є її вивантаження або прийом з шахти, кар'єру (розрізу), рудника.
Способи прийому сировини, які застосовують на збагачувальних фабриках
Основні способи прийому мінеральної сировини:
- безпосередньо з шахти (рудника) через кліть або скіповий підйомник і конвеєрний транспорт;
- із залізничних вагонів з самовивантаженням;
- із залізничних вагонів з вивантаженням їх вагоноперекидачем;
- по пульпопроводах у вигляді гідропульпи;
- від розрізів автомобільним транспортом.
Найбільше розповсюджені перші три способи.
Прийом корисної копалини у вигляді гідропульпи застосовується, якщо її видобувають гідравлічним способом. Цей спосіб транспортування приводить до переподрібнення корисної копалини. Крім того, фабрика повинна мати ємності для акумулювання пульпи, апарати для видалення великої кількості води і розвинену водно-шламову схему для прояснення оборотних вод і уловлювання шламів.
Автомобільний транспорт при порівняно невеликих відстанях перевезень може успішно конкурувати із залізничним, як більш мобільний.
Безперервний спосіб подачі корисної копалини дозволяє ефективніше використовувати обладнання підготовчих операцій і запобігати непродуктивних простоїв через нерівномірності надходження сировини.
Спосіб доставки корисної копалини на збагачувальну фабрику залежить від її відстані від гірничодобувного підприємства (шахти, кар'єру, рудника).
Конвеєрний спосіб доставки корисної копалини застосовують при невеликих відстанях між фабрикою і шахтою (розрізом). Відповідно до цього способу піднята скіповим підйомником або кліттю корисна копалина по жолобу направляється у бункер, розташований поряд з копром. З бункера корисна копалина живильником видається на стрічковий конвеєр і направляється у відділення попереднього дроблення, а потім на подальшу підготовку перед збагаченням. Конвеєрні лінії для надходження корисної копалини з шахти у підготовче відділення фабрики звичайно розташовані у критих галереях. Граничний кут нахилу стрічкових конвеєрів для рядового вугілля 20о, для дроблених руд — до 25о.
Приймальні пристрої сировини (руди, вугілля) як самостійні об'єкти передбачаються на фабриках, що переробляють корисні копалини декількох родовищ, а також при розташуванні фабрики на значній відстані від гірничодобувного підприємства. Приймальні пристрої, віддалені від цеху дроблення, призначені для збагачуваного матеріалу крупністю не крупніше 350—400 мм, що дозволяє транспортувати його стрічковими конвеєрами. Цій крупності відповідають продукт крупного дроблення і корисні копалини, які безпосередньо видаються на гора з шахт. Якщо на збагачувальну фабрику корисна копалина доставляється залізничним транспортом «Укрзалізниці», продуктивність приймальних пристроїв, фронт розвантаження, число вагоноперекидачів, грейферних кранів, продуктивність стрічкових конвеєрів та іншого обладнання приймального відділення повинна забезпечити мінімальний час розвантаження маршрутного состава і виключення простою залізничних составів.
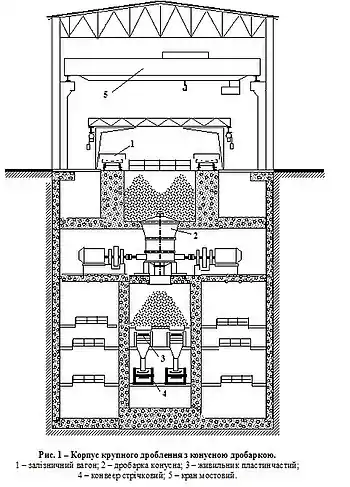
Місткість приймальних пристроїв залежить головним чином від режиму роботи фабрики. На збагачувальних фабриках застосовують приймальні пристрої бункерного і складського типів.
У більшості випадків на рудних збагачувальних фабриках приймальні пристрої сировини поєднують із корпусом крупного дроблення. Для руди, що містить грудки розміром більше 400—500 мм, приймальних бункерів великої місткості звичайно не споруджують (великі капітальні витрати). Руду в дробарку завантажують або безпосередньо з вагонів (дробарки ККД-1500/180) і автосамоскидів (дробарки ККД-1200/150), або живильником важкого типу з бункера невеликої місткості (дробарки типів ЩДП і ЩДС).
Прийом сировини із залізничних вагонів з самовивантаженням
Перший тип приймальних пристроїв
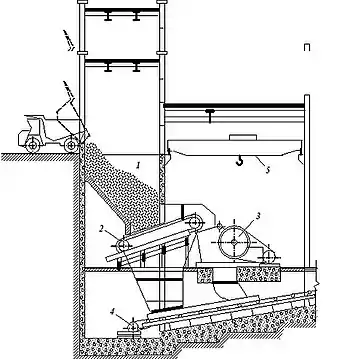
Перший тип приймальних пристроїв (рис. 1) застосовується при вивантаженні корисних копалин крупністю до 350—450 мм. Корисна копалина надходить на збагачувальну фабрику у саморозвантажних залізничних вагонах типу думпкар вантажопідйомністю до 140 т по одній або двох залізничних коліях (залежно від продуктивності збагачувальної фабрики). Якщо для крупного дроблення на збагачувальній фабриці використовуються конусні дробарки ККД-1500/180 і більшого типорозміру, вивантаження корисної копалини здійснюється безпосередньо у дробарку (дробарка працює «під завалом»). Розвантаження дробленого матеріалу з бункера і подача його на стрічковий конвеєр здійснюється пластинчастими живильниками. Пристрої цього типу можуть застосовуватися для рудних збагачувальних фабрик, які працюють на привізній сировині, для групових і центральних вуглезбагачувальних фабрик.
Другий тип приймальних пристроїв
Другий тип приймальних пристроїв (рис. 2 ) призначений для вивантаження сировини крупністю до 350 мм, що надходить на фабрику в саморозвантажних залізничних вагонах вантажопідйомністю до 125 т або в автосамоскидах вантажопідйомністю до 110 т. Цей тип приймальних пристроїв застосовується у тому випадку, якщо для крупного дроблення використовуються конусні дробарки меншого типорозміру або щокові дробарки. Вивантаження корисної копалини здійснюється у приймальний бункер, з якого вона пластинчастим живильником подається у дробарку або на колосниковий грохот для попереднього відділення дрібних класів. Розвантаження дробленого матеріалу здійснюється безпосередньо на стрічковий конвеєр. Приймальні бункери можуть використовуватися як акумулюючі, у цьому випадку їх місткість визначається режимом і продуктивністю фабрики (на одну-дві зміни).
Різновидом цього типу приймальних пристроїв є пристрій прийому сировини з підвісних канатних доріг, який використовується при розташуванні рудника і фабрики в гірських районах або у місцевості з дуже пересіченим рельєфом.
Прийом сировини із залізничних вагонів з вивантаженням їх вагоноперекидачем
Прийом сировини із залізничних вагонів з вивантаженням їх вагоноперекидачем призначений для вивантаження сировини крупністю до 350 мм. При цьому способі використовують піввагони вантажопідйомністю 60, 93 і 125 т. З точки зору механізації розвантажувальних робіт цей спосіб є найбільш ефективним. На вуглезбагачувальних фабриках застосовують вагоноперекидачі двох типів: роторні і з боковим розвантаженням.
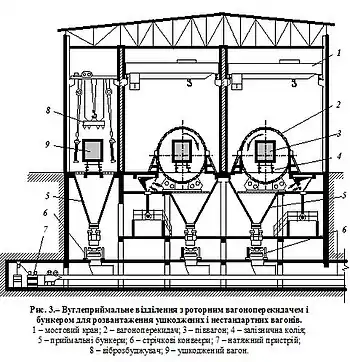
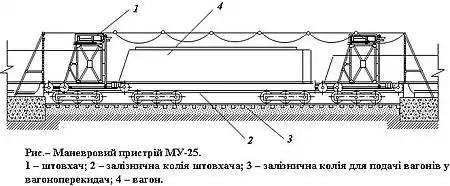
На рис.3 наведене вуглеприймальне відділення з роторними вагоноперекидачами. Розвантаження вагона здійснюється при його повороті без вертикального переміщення. У цьому випадку приймальні бункери вимагають значного заглиблення, що пов'язане з необхідністю виконання великого об'єму земляних робіт.
При розвантаженні вугілля вагоноперекидачем з боковим розвантаженням вагон піднімається більше ніж на 4 м над рівнем залізничної колії і спорожняється при обертанні навколо осі, розташованій поза вагоном. У цьому випадку приймальний бункер розташовується вище рівня залізничної колії і для його спорудження виконання земельних робіт не потрібне.
Вагоноперекидачі з боковим розвантаженням призначені для розвантаження піввагонів вантажопідйомністю 60 і 93 т, але цей тип вагоноперекидачів на вуглезбагачувальних фабриках застосовується значно рідше.
Точну постановку вагонів при достатньо великій швидкості (30 циклів/год), переміщення їх (до 28 вагонів одночасно) у зоні вагоноперекидача у обох напрямках забезпечується електроштовхачем або маневровими пристроями МУ-25 і МУ-25А (рис.4 ). У тих випадках, коли при розвантаженні вугілля застосування локомотиву не є доцільним, використовують маневрові пристрої МУ25 і МУ25А. Ці маневрові пристрої з тяговим зусиллям 0,25 МН забезпечують точне встановлення вагонів при достатньо великій швидкості і їхнє переміщення в зоні вагоноперекидача у обох напрямках.
Якщо руда містить багато дріб'язку, котрий не допускає бункерування унаслідок високої злежуваності (наприклад, боксити, марганцева руда), то прийом її здійснюється на наземний склад, обладнаний грейферним краном. Узимку волога корисна копалина змерзається, що значно ускладнює її прийом. Найефективніший засіб розвантаження вагонів зі змерзлою сировиною — застосування тепляків-розморожувачів. Час находження вагонів у тепляку-розморожувачі залежить від ступеня промерзання вугілля і становить 2—4 год. Незважаючи на порівняно довгий час розморожування, загальний простій вагонів під розвантаженням у цьому випадку виявляється меншим ніж при розвантаженні змерзлого вугілля без відтаювання.
Див. також
Література
- Білецький В.С., Смирнов В.О. Технологія збагачення корисних копалин. — Донецьк: Східний видавничий дім, 2003. — 272 с.
- Смирнов В. О. Проектування збагачувальних фабрик : навч. посіб. для студ. спец. "Збагачення корисних копалин" вищ. навч. закладів / Смирнов Валерій Олександрович, Білецький Володимир Стефанович. — Донецьк : Сх. вид. дім, 2002. — 296 с. : рис. – Бібліогр.: с. 289–290. http://vesna.org.ua/txt/biletskv/fabr/index.html