Брикетування вугілля
Брикетування вугілля — фізико-хімічний процес отримання механічно і термічно міцного сортового продукту — брикету, що має задану геометричну форму, розміри і масу.
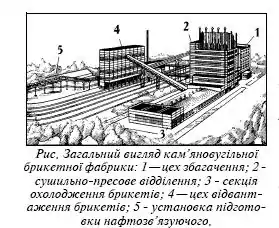
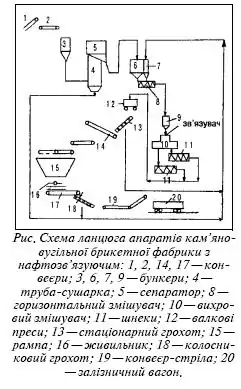
Загальна характеристика
Брикети використовуються у коксохімічній, металургійній, хімічній та ін. галузях промисловості, також як побутове паливо. У залежності від властивостей корисних копалин і призначення брикети повинні задовольняти наступним вимогам:
- а) мати атмосферостійкість, не руйнуватися від температурних коливань і атмосферних опадів;
- б) мати достатню механічну міцність, витримувати досить високі ударні навантаження і чинити опір стиранню і вигину;
- в) мати достатню пористість, що забезпечує хорошу проникність газів при високих температурах горіння;
- г) містити мінімальну кількість вологи, яка обумовлює додаткові витрати енергії на випаровування і знижує газопроникність брикетів;
- д) бути температуростійкими, не руйнуватися від впливу високих температур.
Вуглебрикетне виробництво дозволяє отримати високоякісне і транспортабельне паливо, скоротити втрати вугілля при зберіганні, перевезеннях і спаленні, запобігти самозайманню вугілля, залучити для коксування додаткові ресурси неспікливого вугілля, ефективно використовувати низькоякісні місцеві види палива, збільшити видобуток бурого вугілля для використання в енергетиці.
Брикетування вугілля здійснюється зі зв'язуючими і без зв'язуючих. За призначенням вугільні брикети бувають побутовими і промисловими. Побутові брикети можуть бути овальної, подушкоподібної або будь-якої іншої округлої форми масою 30-50 г. Для надання їм підвищеної термічної і механічної міцності, також властивостей бездимного палива їх іноді піддають термообробці. Промислові брикети служать сировиною для напів'коксування бурого і коксування кам'яного неспікливого вугілля. Вони можуть виконувати функції теплоізоляційного матеріалу, замінюють дефіцитний графіт, використовуються як основний матеріал для отримання різних електродів.
Брикетування як технологічний процес
Брикетування — як технологічний процес грудкування корисних копалин — складається з ряду виробничих операцій:
- 1) Підготовка сировини до пресування: дроблення, грохочення і висушування; підготовка зв'язуючих речовин: дозування, змішування зі зв'язуючим (у малаксері), нагрівання і охолодження шихти перед пресуванням.
- 2) Пресування шихти з додаванням необхідних домішок, що визначаються в залежності від фізико-хімічних властивостей і складу матеріалу, що брикетується.
- 3) Обробка свіжих брикетів з метою їх пришвидшеного затвердіння (охолодження, пропарювання, карбонізація, висушування, відновне випалення і ін.).
- 4) Складування і навантаження готових брикетів.
Механізм брикетування кам'яного вугілля зі зв'язуючим
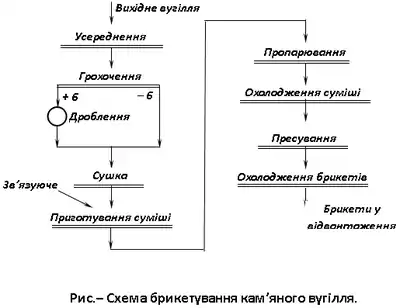
Формування структури брикетів зі зв'язуючими розглядають як один з випадків склеювання роз'єднаних твердих частинок за допомогою клеїв. Основу структуроутворення складають стохастичні процеси взаємного розташування і адгезійної взаємодії окремих контактуючих елементів системи. Агрегатоутворення визначає прилипання і склеювання. Прилипання — як початковий стан процесу склеювання — пов'язане з утворенням впорядкованої клейової плівки на поверхні твердих частинок. Для прилипання характерний в'язкотекучий (іноді рідкий) стан зв'язуючого. Подальші процеси призводять до структурування клею і набуття агрегатом максимальної міцності. Роз'єднані тверді частинки, вкриті зв'язуючим, об'єднуються (склеюються) в брикет.
Прилипання і склеювання залежать від фізичних і хімічних властивостей клею (зв'язуючого) і твердого тіла. Особливе значення мають температура, ступінь полімеризації, полярність і структура зв'язуючого, а також природна сумісність взаємодіючих речовин. Збільшення температури інтенсифікує дифузію клею в пори і тріщини твердого тіла. Збільшення тиску в місці контакту сприяє рівномірному розподілу клею по поверхні частинок. Зі збільшенням часу контакту зростає глибина проникнення молекул зв'язуючого в пори і тріщини. Зі збільшенням шорсткості твердих частинок зростає дійсна площа контакту, поліпшуються умови проникнення зв'язуючого в мікро– і макродефекти; крім того, на нерівній поверхні шматочків можливе заклинення клею в макродефектах, що сприяє прилипанню.
Вплив зв'язуючого зумовлений його специфічними властивостями. Зі зменшенням молекулярної маси збільшується його рухливість і воно краще розтікається по поверхні твердого тіла, легше дифундує в пори і тріщини. Однак воно не створює достатнього зчеплення між частинками — брикет не має необхідної механічної міцності. Зв'язуючі з великою молекулярною масою малорухливі, високов'язкі, мають малу дифузійну здатність, що суттєво погіршує контакт «вугілля-зв'язуюче» і в результаті негативно впливає на міцність брикетів. Оптимальну клеючу здатність має зв'язуюче із середньою молекулярною масою.
Полярність зв'язуючого сприяє виникненню хімічних і дифузійних взаємодій, однак, підвищена полярність посилює структуру, знижує дифузійну активність і в'яжучі властивості клею.
Гранулометричний склад визначає сумарну поверхню зерен, кількість і величину пустот в структурному каркасі брикетів, вміст гострокутних зерен, рельєф твердої поверхні і наявність пилоподібних частинок. Підбір суміші частинок різної крупності полягає в забезпеченні найщільнішої упаковки. Щільність упаковки тісно пов'язана з розміром зерен. Наявність пилоподібних частинок приводить до зростання витрат зв'язуючих, але сприяє ущільненню і зміцненню брикетів. Міцність брикетів тим нижче, чим однорідніше ситовий склад.
Внаслідок нагрівання досягається тонкошарове розтіканням зв'язуючих по твердій поверхні і посилення зв'язку в їх адсорбційних шарах. Для посилення міцності брикетів при слабому нагріванні необхідно збільшити витрату зв'язуючого.
Надлишок вологи не дозволяє зв'язуючим міцно прилипнути до твердих частинок, механічна міцність брикетів знижується. Фізична суть процесу пресування полягає в пластичній деформації матеріалу під тиском. Під пластичністю брикетної суміші розуміють її здатність змінювати свою форму під впливом зовнішніх сил без утворення тріщин і зберігати отриману форму після зняття тиску. Пластичність росте із збільшенням температури і характеризує придатність суміші до пресування, відображаючи рухливість суміші, кут внутрішнього тертя, зчеплення, прилипання і пружність.
Структурна міцність брикетів остаточно набувається в процесі охолоджування. Брикет, що виходить з процесу, має температуру, близьку до температури розм'якшення зв'язуючого. Охолодження брикетів здійснюється повітрям.
Як зв'язуюче при брикетуванні кам'яного вугілля і антрацитів використовують важкі залишки переробки смолистих нафт, кам'яновугільний пек, сульфід-спиртова барда, побічний продукт переробки деревини на целюлозу по сульфатному методу, гумати натрію і амонію, сланцеві бітуми, смола напів'коксування і фуси напів'коксування, а також суміші перерахованих вище органічних речовин.
Технологія брикетування кам'яного вугілля зі зв'язуючим
Брикетування як відособлений технологічний процес грудкування корисних копалин складається з таких виробничих операцій :
1) підготовки сировини до пресування: дроблення, просіювання, подрібнення і сушіння; препарування зв'язуючих речовин; дозування компонентів брикетної шихти, їх перемішування, нагрівання та охолодження брикетної шихти перед пресуванням;
2) пресування брикетної шихти шляхом прикладання необхідних зусиль, ураховуючи фізико-хімічні властивості, петрографічний і мінеральний склад брикетованого матеріалу;
3) обробка «сирих» брикетів з метою найшвидшого їх затвердіння (охолодження, пропарювання, карбонізація, сушіння, відновлювальний випал та ін.);
4) складування і відвантаження готових брикетів.
Організація технології брикетування кам'яного вугілля і антрацитів залежить від вимог споживачів до брикетів. Для брикетування найбільш доцільно використовувати збагачений вугільний дріб'язок та антрацитовий штиб. Якісні кам'яновугільні (антрацитові) брикети повинні відповідати таким технологічним показникам: маса — 75-85 г; механічна міцність на скидання — не нижче 85 %, вміст дріб'язку (грудок менше 25 мм) — не більше 10 %, вологовбирання — не вище 4 %, вихід летких речовин — не більше 10 %, теплота згоряння — 34000-35000 кдж/кг. Зольність брикетів встановлюється залежно від якості сировини та умов її переробки
- Підготовка зв'язуючих
Для брикетування кам'яного вугілля і антрацитів застосовують органічні зв'язуючі в рідкому та твердому стані. Найбільше поширен-ня одержало нафтозв'язуюче, яке використовується в рідкому вигляді. Рідше використовують тверде зв'язуюче — кам'яновугільний пек. Рідку сульфіт-спиртову барду, тверді глини і цемент застосовують в основному як модифікуючі добавки. Зв'язуюче в рідкому вигляді має ряд переваг порівняно із твердим адгезивом, зокрема воно легко диспергується, утворюючи тонкоплівкове покриття на вугільній поверхні. При цьому знижуються витрати зв'язуючого та поліпшується підготовка брикетної суміші. Для підготовки рідких зв'язуючих, зокрема нафтозв'язуючих, можливі два технологічних варіанти. У першому випадку використо-вується схема підготовки зв'язуючого, виготовленого на нафтопереробному заводі. У другому — схема, що включає підготовку наф-тозв'язуючого безпосередньо на брикетній фабриці.
На діючих брикетних фабриках більш поширена перша схема, за якою на брикетну фабрику з нафтопереробних заводів кондиційне зв'язуюче доставляється в залізничних піввагонах або цистернах. На-піввагони являють собою чотиривісні залізничні платформи, на яких установлені чотири самоперекидних бункери місткістю 10 т кожний. Для зливу нафтозв'язуючого вони обладнані паровою сорочкою (по-двійними стінками). Нафтозв'язуюче вивантажується із залізничних ємностей 6 у спеціальні сховища. Місткість резервуарів становить не менше 15-20 добового запасу зв'язуючого. Сховища виконуються у вигляді окремих відсіків 5, які являють собою залізобетонні ємності (іноді металеві) місткістю 500—1000 м3 із шиферним навісом, що запобігає дії атмосферних опадів.
У відсіку встановлений донний обігрів з паровими трубчастими змійовиками, що забезпечують нагрівання зв'язуючого до 100—110°С. Додатково відсік обладнується барботажною паровою системою, яка змучує тонкодисперсні осади, що накопичуються на дні. У торці від-сіку є невеликий прийомний збірник 4 з пов'язаними з ним шестерними насосами 3. Розігріте зв'язуюче, що надійшло в прийомний збірник, насосом подається у ємність 2, а з неї паровим високотисковим насосом 1 у трубчасту піч 9, де воно нагрівається до температури 220—230 °С. Із трубчастої печі зв'язуюче повертається у видаткову ємність, де змішується з «холодним» зв'язуючим, що надходить зі сховища. Такий технологічний прийом дозволяє заощаджувати тепло трубчастих печей, швидко зневоднювати «холодне» зв'язуюче та знижувати його температуру до оптимальних робочих значень (180—200° С)
Зв'язуюче, що має робочу температуру 180—200° С, з видаткової ємності високотисковим паровим насосом подається по кільцевому трубопроводу до форсунок-дозаторів 8 для змішування з вугіллям. Надлишок зв'язуючого повертається знову у видаткову ємність. Для створення необхідного підпору зв'язуючого перед форсунками на вихідній ділянці кільцевого трубопроводу встановлюється регулювальна засувка.
Другий варіант схеми підготовки рідких зв'язуючих — виготовлення їх безпосередньо на брикетних фабриках. Така підготовка має ряд переваг: спрощується технологія зливу і розігріву вихідної сировини; поліпшується якість зв'язуючого за рахунок скорочення його багаторазових нагрівів і перекачувань; здешевлюється вартість зв'язуючих.
Найбільш простим і дешевим є безкомпресорний метод, осно-ваний на ефекті всмоктування повітря шляхом диспергування його відцентровим імпелером. Технологічна схема прийому сировини аналогічна наведеній вище схемі прийому готового зв'язуючого. Підготовлена для окиснення сировина надходить у реактор (рис. 10.8), який являє собою горизонтальний п'ятисекційний апарат, обладнаний імпелерами для диспергування повітря в рідкій фазі. П'ять робочих секцій за своїми розмірами і технологічним виконанням ідентичні. Остання секція є буферною ємністю перед відкачкою готового зв'язуючого. Секції відділені одна від одної гідравлічними затворами. У кожній робочій секції 6 установлюється диспергатор з електроприводом 3. Частота обертання диспергатора складає 750 хв-1. У зону окиснення повітря надходить безпосередньо через диспергатор з використанням ежектора 2. Подача сировини здійснюється через патрубок 1, видача — через патрубок 5. Для зняття надлишкового тепла екзотермічної реакції в кожну секцію подається вода. Рівень рідини в реакторі регулюється за допомогою шибера 4 в останній секції. У реакторі передбачені спеціальні пристрої для термопар 7 і відбору проб 8.
Процес окиснення відбувається в такий спосіб. Диспергатор, обертаючись, засмоктує повітря у фазу гарячої сировини. Створюються умови тісного контакту з рідким середовищем, що прискорює процес окиснення за рахунок максимального використання кисню повітря. У процесі окиснення відбувається швидкий підйом температури в секціях до 300—320° С. Для підтримки постійної температури в реактор подається вода. Пар води і газу відокремлюються в сепараторі від конденсату нафтопродуктів (віддуву), що повертається для доокиснення в п'яту секцію реактора. Відпрацьовані гази спалюються. Рівень регулюється шибером, встановленим після останньої робочої секції.
- Охолодження і відвантаження брикетів
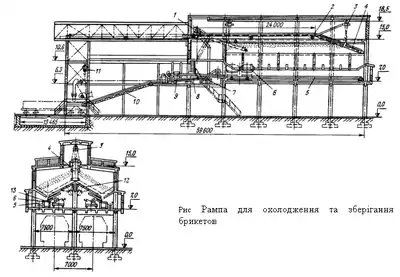
Охолодження і відвантаження готових брикетів — заключні операції технологічного комплексу брикетування. Охолодження — це операція, що забезпечує необхідну механічну міцність в готових брикетів. У процесі охолодження підвищується в'язкість зв'язуючого за рахунок зниження температури брикетів від 60-65 до 20-25° С. Для охолодження брикетів потрібне певний час перебування їх в атмосфері примусово подаваного або природно омиваного повітря. Інтенсивність охолодження пропорційна відношенню обєму брикету до його поверхні. Великі брикети охолоджуються повільніше, чим дрібні. Погіршується охолодження при багатошаровому укладанні брикетів на стрічці конвеєра. Оптимальною вважається завантаження брикетів в один — два шари.
Охолодження брикетів відбувається тим швидше, чим нижче витрати зв'язуючого. При малих (6-7 %) витратах зв'язуючого досягається рівномірне зниження температури в повному об'ємі брикету. При більш високих витратах температура в брикеті знижується повільно і нерівномірно. Поверхневі шари охолоджуються значно швидше, ніж глибинні, що викликає їх деформацію і злипання.
Брикети з підвищеним вмістом зв'язуючого вимагають застосування інтен-сивних мір охолодження: обдування повітрям, зрошення водою та ін. Інтенсив-ність охолодження залежить від типу структури зв'язуючого. Так, процес твердіння кам'яновугільного пеку проходить в 2,5-3 рази швидше, чим нафтозв'язуючого. Для охолодження брикетів з нафтозв'язуючим потрібні подовжені тракти конвеєрів із сітчастою металевою стрічкою замість прогумованої. Одночасно застосовується інтенсивний обдув повітрям і зрошення водою.
Охолодження брикетів здійснюється на спеціальних конвеєрах, що відрізняються від звичайних своєю конструкцією, довжиною і шириною. Швидкість руху такого конвеєра не перевищує 0,1-0,2 м/с.
Конструкція охолоджувального конвеєра виконується такою, щоб брикети розташовувалися на стрічці горизонтальним шаром. Для цього приводний барабан робиться діаметром не менш 1500 мм, ширина стрічки 1800—2200 мм, а довжина залежно від продуктивності від 50 до 300 м. У конвеєрах охолодження використовують обидві гілки. Брикети спочатку завантажуються на верхню гілку і рухаються по ній до приводного барабана. Потім скидаються по жолобам на нижню гілку і направляються в протилежну сторону.
У більшості випадків природне охолодження виявляється недостатнім. За-стосовується примусовий обдув брикетів повітрям. Для цього до нижніх і верхніх гілок стрічки конвеєра підводять повітроводи від вентиляторів. Іноді на верхній гілці конвеєра встановлюється ряд форсунок для зрошення брикетів водою. Форсунки закріплюються в кілька рядів по довжині і ширині стрічки так, щоб факел розпилення охоплював всю поверхню охолоджуваних брикетів. Завдяки цьому водяна плівка з поверхні брикетів миттєво випаровується, не викликаючи вологовбирання. Для підвищення ефекту охолодження брикети обдувають гарячим повітрям, що викликає швидкий випар вологи та віддачу тепла. Витрати води становлять близько 100 л/ч, швидкість повітря, що обдуває, 15- 25 м/с, час обдуву — 30-40 с.
Відомий метод зрошення брикетів водяним розчином сульфіт-спиртової барди. Плівка барди після висихання закриває пори й тріщини в брикетах. Це підвищує їх міцність і перешкоджає злипанню. Брикети здобувають гладку блискучу поверхню, зменшується пилення при завантаженні.
У більшості випадків брикети після конвеєра охолодження надходять у рампу (рис.). Рампа є одночасно охолоджувачем і акумулятором брикетів. Вона споруджується в одному комплексі з навантажувальним пунктом брикетів. Брикети конвеєром 1 подаються на завантажувальний візок 2. З візка стрілою 4, що переміщується у вертикальному напрямку лебідкою 3, брикети розподіляються по довжині рампи. Похиле днище рампи являє собою колосникові ґрати 12. Через ці ґрати відбувається природна вентиляція повітря, а в жарку пору року — примусова. З рампи охолоджені брикети по похилій площадці 13 дисковим виштовхувачем подається у вагони. Стріла 10 переміщається у вертикальному напрямку за допомогою лебідки 11. Бій брикетів відокремлюється перед навантаженням на грохоті 9 і повертається в процес конвеєрами 7, 8.
Гіпотези брикетування бурого вугілля
Молоде буре вугілля, яке брикетують без зв'язуючого, можна розглядати як високомолекулярні сполуки нерегулярної будови, властивості яких багато в чому визначаються процесами колоїдного набухання. Брикетування такого вугілля можна розглядати як складний багатостадійний процес утворення міцного комплексу за рахунок високого тиску пресування. Існує декілька гіпотез утворення брикетів з бурого вугілля.
Колоїдна гіпотеза оцінює брикетованість бурого вугілля з позиції дії молекулярних сил. При зближенні частинок вугілля до відстаней, коли починається дія молекулярних сил, відбувається зчеплення поверхневих шарів з утворенням брикетів. Ця гіпотеза оцінює вологу як зв'язуючий прошарок, сприяючий ковзанню частинок одна відносно іншої.
За капілярною гіпотезою буре вугілля розглядається як пружний нееластичний гель, що має велику внутрішню поверхню за рахунок безлічі капілярів, всередині яких міститься вода. При пресуванні частина води видавлюється з капілярів, заповнюючи проміжки між зернами. У місцях контакту зерен через водний шар виникають сили капілярного натягу і сили зчеплення. У залежності від товщини плівки змінюється міцність брикетів. Максимальна міцність досягається при мономолекулярній плівці води.
Бітумна гіпотеза брикетування бурого вугілля розглядає процес як аналог брикетування зі зв'язуючим, роль якого відіграють бітуми, що містяться в бурому вугіллі. Бітуми, вміст яких в молодому вугіллі становить 5-20 %, плавляться при температурі близько 900 °C і в розплавленому стані володіють хорошою адгезійною (клеючою) здатністю. У самій вузькій частині формувального каналу штемпельного преса (буклі) вугілля нагрівається до 250—300 °C, і бітуми, що виділяються при цьому, обволікають тонкою рівномірною плівкою поверхню вугілля і в умовах підвищеного тиску пресування зв'язують окремі зерна в брикет чорного кольору з блиском, характерним для бітумів.
За гуміново-кислотною гіпотезою брикетованість вугілля залежить від вмісту в ньому гумінових кислот, які виступають в ролі зв'язуючих, виділяючись в процесі пресування. Чим більше в бурому вугіллі гумінових кислот, тим вища його вологість і краща брикетованість.
Молекулярно-капілярна гіпотеза брикетування бурого вугілля стверджує, що в утворенні брикетів беруть участь як молекулярні, так і капілярні сили.
Найбільш сучасною і довершеною є гідраційно-молекулярна теорія. Згідно з нею, основними параметрами, що визначають брикетованість, є залишкова волога після висушування і крупність вугілля. Головними елементами цієї гіпотези є оптимальне співвідношення адсорбційної і капілярної вологи в зовнішніх і внутрішніх шарах вузьких класів крупності «сушонки» і кількість вологи, що видавлюється при певному тиску пресування.
Основні чинники процесу брикетування бурого вугілля
Основними чинниками, що впливають на процес отримання міцних брикетів з бурого вугілля, є вологість і крупність вугілля, тиск і температура пресування, висушування і охолоджування брикетів.
- Вологість «сушонки»
Оптимальна вологість «сушонки», що відповідає найбільшій міцності брикетів, залежить від тиску пресування, крупності «сушонки», природи і ступеня окиснення поверхні вугілля. Гранулометричний склад тісно пов'язаний з процесом пресування, оскільки при зниженні крупності меншає час і кількість енергії, що затрачуються на крихкі і пружні деформації матеріалу; збільшується частка енергії та часу на корисні пластичні деформації. Для брикетів, що використовуються в побуті, верхня межа крупності становить 4-6 мм, для технологічних брикетів — до 2 мм. У першому випадку це продиктовано умовами займистості, у другому — підвищеною щільністю структури, необхідною для подальшої термічної переробки.
Для ущільнення брикетної суміші при брикетуванні вугілля і антрациту зі зв'язуючими звичайно застосовують вальцеві преси, що розвивають зусилля пресування 20-50 МПа. Пресування бурого вугілля здійснюють в штемпельних пресах під тиском 80-120 МПа. Іноді буре вугілля брикетують в кільцевих пресах.
Брикетування є однією з перспективних галузей, що забезпечує високий потенціал паливно-енергетичного комплексу і комунального господарства.
- Тиск пресування.
У процесах структуроутворення брикетів велику роль відіграє і тиск пресування. Під дією тиску пресування пухка брикетна суміш перетворюється в міцний грудковий продукт — брикет. Деформованість брикетної суміші під час пресування є функцією пластичності.
Під пластичністю розуміють здатність брикетної суміші змінювати свою форму під впливом зовнішніх сил без утворення тріщин і зберігати отриману форму після припинення дії цих сил. Зі збільшенням температури суміші пластичність зростає, забезпечується висока брикетна здатність суміші при пресуванні.
- Температура пресування
Нагрівання вугілля поліпшує витиснення вологи з капілярів і переміщення її всередині брикету. Існує оптимальна температура, до якої може бути нагріте вугілля. Збільшення температури вище оптимальної шкідливе. Високі температури нагрівання вугілля підсилюють дію пружних деформацій у брикетах, що виходять із преса. В результаті зменшується міцність брикетів.
Для досягнення оптимальної температури вугілля перед пресуванням його охолоджують. Охолодження повинне бути короткочасним, щоб не допустити збільшення різниці в температурі великих і дрібних зерен. Чим менше різниця температур цих зерен, тим менше тріщин на поверхні брикетів.
- ущільнення брикетної суміші
Оцінюючи процес ущільнення брикетної суміші аналогічно струшуванню, його можна описати таким чином. Спочатку відбувається швидка усадка. Потім вона сповільнюється і в міру ущільнення суміші наближається до граничної величини. Першими ущільнюються верхні шари, що перебувають ближче до місця тиску. Тиск пресування поширюється хвилеподібно, зменшуючись у глибині брикету. Ущільнення припиняється внаслідок погашення тиску від місця по-рушення. Це відбувається лише через посилення тертя між частинками в результаті збільшення зусиль.
Фізична сутність процесу пресування полягає в пластичній деформації матеріалу, що піддається обробці. Деформація в загальному випадку — це зсув однієї частинки матеріалу щодо іншої. Пластична деформація має місце, коли деформуюче зусилля змушує матеріал текти, подібно до рідини.
Якщо швидкість зростання напруги велика порівняно зі швидкіс-тю залишкової деформації, то деформація відстає від напруги. Це пов'язане з тим, що між напругою і внутрішнім тертям не встигає встановитися рівновага. У брикетній масі деформація помітно відстає від напруги. З'являються пружні сили, які компенсують різницю між напругою та тертям. Ці сили, названі внутрішнім напруженням, після зняття зовнішніх зусиль викликають пружний наслідок або релаксацію.
Після зняття тиску відбувається нерівномірне розширення брикету. Різнорідні матеріали — субстрат і зв'язуюче — по-різному сприй-мають пружні деформації та неоднаково відновлюються. Виниклі розтяжні зусилля протилежні за знаком зусиллям, що здавлюють, тому брикет розширюється. Розтяжні зусилля діють поступово, проявляючись із виходом брикету з-під преса. Спочатку вони спрямовуються тільки в одному напрямку, вирівнюючись у процесі видавлювання брикету з матриці. Такий розподіл зусиль негативно впливає на міцність, особливо коли пресування протікає при високих тисках. Негативна дія пружних деформацій приводить до виникнення в клейових плівках додаткових внутрішніх напружень, що послаблюють міцність брикетів.
Технологія брикетування молодого бурого вугілля і торфу
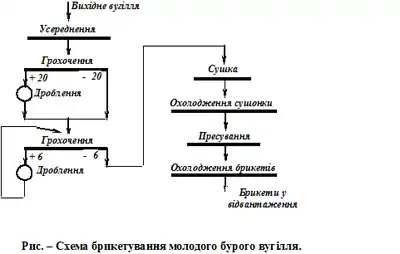
Технологія брикетування молодого бурого вугілля і торфу включає підготовчі операції, висушування, пресування, охолодження і відвантаження брикетів.
Підготовка бурого вугілля за крупністю (розміром, величиною) зводиться до забезпечення оптимального гранулометричного складу. Залежно від вихідної крупності вугілля піддається одно- або двостадійному дробленню. Дроблений до 6 мм матеріал направляється на сушіння, де його вологість знижується до 16 — 19 %. На швидкість і тривалість висушування впливають природа бурого вугілля, вміст вихідної вологи, крупність, питома продуктивність сушарки, інтенсивність перемішування матеріалу при русі по сушарці, температура, вологість і швидкість подачі теплового агента. Сушіння бурого вугілля звичайно здійснюється в парових сушарках. Оскільки вугілля після сушіння має достатньо високу температуру (70 — 85 °C), охолодження його є обов'язковою операцією перед пресуванням.
Пресування — основний процес в технології брикетування бурого вугілля. В процесі пресування під дією високих механічних зусиль (80 — 120 МПа) від-бувається обтискування вугільного дріб'язку, в результаті чого він перетворюється в брикет. Маса буровугільних брикетів становить 300—600 г. Брикетування бурого вугілля здійснюється в штемпельних, рідше в кільцевих пресах. Брикети після пресування мають температуру 70 — 80 °C, тому перед відвантажуванням вони повинні охолоджуватись (в охолоджувальних жолобах або конвеєрах). Брикети повинні зберігатись на складах закритого типу, щоб уникнути атмосферних впливів.
Технологія брикетування торфу не відрізняється від буровугільної.
Див. також
Література
- Елишевич А.Т. Брикетирование угля со связующими/ М., Недра, 1972.
- В. І. Саранчук,М. О. Ільяшов, В. В. Ошовський, В. С. Білецький. Хімія і фізика горючих копалин. — Донецьк: Східний видавничий дім, 2008. — с. 600. ISBN 978-966-317-024-4
- Сергєєв П. В., Білецький В. С. Дослідження брикетування антрацитових штибів // Збагачення корисних копалин. — 2012. — Вип. 50 (91). — С.13-16.
- Білецький В. С., Олійник Т. А., Смирнов В. О., Скляр Л. В. Техніка та технологія збагачення корисних копалин. Частина ІІІ. Заключні процеси. — Кривий Ріг: Криворізький національний університет. 2019. — 232 с.