Вакуумне формування
Ва́куумне формув́ання (англ. vacuum forming) або техноло́гія гаря́чого ва́куумного формува́ння — це виготовлення виробів з листових термопластичних матеріалів у гарячому вигляді шляхом надання їм форми матриці під впливом підвищеної температури і вакууму або низького тиску повітря.
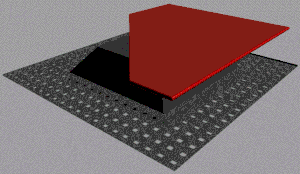
У процесі виробництва лист пластику нагрівається до температури розм'якшення і щільно облягає поверхню матриці за рахунок створення пониженого тиску між ним і матрицею[1]. Ця методика застосовується переважно при серійному виробництві об'ємних виробів з пластику, однак у низці випадків може застосовуватись і при одиничних тиражах.
Технологія вакуумного формування
Загальна характеристика
Вакуумне формування за суттю є варіантом технологічної операції витягування, при якому листовий пластик, розташований над або під матрицею (інструментом формування), нагрівається до певної температури, і повторює форму матриці за рахунок створення вакууму між пластиком і матрицею.
Особливістю методу вакуумного формування є можливість реалізації виробничого процесу з використанням невеликого розрідження. Такі процеси не вимагають наявності потужного устаткування, високоміцних матричних форм та значних витрат енергоносіїв. Внаслідок цього виробництво вважається економним, а готові вироби мають низьку собівартість.
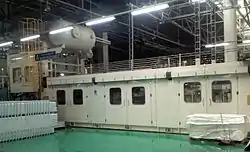
Широкі можливості для застосування автоматизованих виробничих процесів дозволяють налагодити безперервний цикл виготовлення продукції різного призначення. Важливу роль відіграє і те, що для формування використовуються готові листові заготовки, отримання яких не вимагає глибокої переробки сировини.
Стандартний метод вакуумного формування складається з декількох етапів, а саме:
- фіксування заготовки на матриці;
- нагрівання полімерного листа;
- попереднє розтягнення листа;
- відкачування повітря з матриці і втискання заготовки;
- охолодження матеріалу та вилучення виробу з матриці;
- остаточне оброблення виробу.
Стадії виробничого процесу
- Фіксування заготовки
Полімерні листи кріпляться до матриці за допомогою затискної рами. Елементи фіксування повинні забезпечувати притискне зусилля, достатнє для утримання листів завтовшки до 6 мм. При автоматизованому подаванні заготовок на формування робота рухомих елементів притискної рами повинна виключати можливість пошкодження готового виробу.
- Нагрівання заготовки
Головною особливістю цього етапу технології є забезпечення рівномірного прогріву всього об'єму заготовки, інакше не вдасться забезпечити щільність прилягання матеріалу до форми матриці. У технології вакуумного формування для нагрівання заготовок застосовуються, зазвичай, інфрачервоні випромінювачі та кварцові лампи.
Уся площа поверхні заготовки ділиться на декілька зон, кожна з яких нагрівається окремим елементом, а температура нагріву контролюється за допомогою спеціальних пірометрів. До закінчення процесу нагрівання лист полімеру повинен зберігати своє початкове положення. Провисання пластику компенсується подаванням стиснутого повітря для коригування форми заготовки. Завдяки цьому виключається можливість розриву матеріалу.
- Попереднє розтягнення листа
У деяких випадках у процес виробництва включають попереднє розтягнення матеріалу, що називають також роздуванням. Розтягування виконується після досягнення пластиком робочої температури формування і служить для вирівнювання товщини заготовки. Процес роздування необхідний при формуванні заготовок на глибоких матрицях зі складною геометрією поверхні.
- Відкачування повітря і втискання заготовки
Після попереднього нагрівання і розтягнення закріпленої заготовки в апараті для формування розпочинається відкачування повітря вакуумним насосом. При зниженні тиску всередині апарату полімерний матеріал, який досяг стану пластичності, починає облягати форму матриці.
Залежно від вимог, що ставляться до кінцевого продукту, технологія вакуумного формування, може поєднуватися з технологією штампування з використанням пуансона. У цьому випадку, крім відкачування повітря з однієї сторони, на заготовку з протилежного боку діє пуансон, профіль якого повторює профіль поверхні матриці.
Комбінацією цих методів можна добитися максимальної точності заданих форм деталей, а також забезпечити рівномірність розподілу полімерного матеріалу по поверхні матриці, повністю виключивши утворення складок та ділянок з різною товщиною.
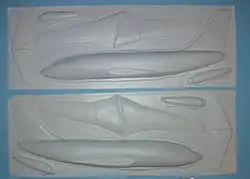
- Охолодження виробу та вилучення з матриці
Для уникнення пошкодження деталі, вилучення її з матриці проводиться після повного остигання матеріалу. Якщо обладнання, яке застосовується для вакуумного формування пластику, оснащене системами повітряного охолодження, час охолодження виробів може бути скорочено на 20—30 %. Вилучення деталі з матриці відбувається під дією надлишкового тиску, що створюється між деталлю та матрицею.
Для виготовлення відповідальних деталей вакуумні матриці оснащуються системами керування температурними процесами. Наявність таких систем дозволяє домагатися рівномірного охолодження виробу, що сприяє підвищенню його експлуатаційних характеристик.
- Остаточна обробка
Виріб, вилучений з матриці, слід відокремити по контуру від надлишків полімерного матеріалу. Сформована деталь може служити напівфабрикатом для подальшого складального виробництва. Для цього виріб може розрізатися, в ньому можуть висвердлюватись отвори для кріпильних елементів і робитися пропили для вставок.
Переваги виробництва методом вакуумного формування
- товщини пластику, що використовується, варіюються від 0,05 до 6 мм, а вироби за габаритами можуть сягати 5 м;
- можливість вилучення деталі з форму уручну;
- відносно низька вартість матриці;
- невисока вартість обладнання для вакуумного формування.
Застосування
Методом вакуумного формування виготовляються пластикові корпусні оболонкові вироби для багатьох галузей:
- для авіаційної, автомобільної та суднобудівної галузей промисловості;
- при виробництві пакувальної тари і ємностей усіх видів;
- для потреб харчового виробництва, хімічної промисловості, медицини;
- при виробництві побутової техніки, приладів та обладнання;
- для потреб будівництва та архітектури.
Матеріали для вакуумного формування можуть використовуватись різні: акрил, полістирол, АБС-пластик, полівінілхлорид, поліетилентерефталат, полікарбонат тощо. Товщина формувального матеріалу може бути від от 0,4 до 6 мм
Див. також
Примітки
- ДСТУ 2242-93 Склопластики конструкційні. Типи, технологія, властивості. Терміни та визначення.
Джерела
- D.E. Walsh Do It Yourself Vacuum Forming for the Hobbyist, Workshop Publishing, Lake Orion, MI, 2002
- Soroka, W Fundamentals of Packaging Technology. — IoPP, 2002. — ISBN 1-930268-25-4
- Yam, K. L. Encyclopedia of Packaging Technology. — John Wiley & Sons, 2009. — ISBN 978-0-470-08704-6
Посилання
- Вакуумне формування пластика, особливості технології на сайті «Будівельні технології»
- Вакуумне формування пластику[недоступне посилання з червня 2019] // «Епатаж Груп»
- Вакуумне формування пластичних матеріалів // «Інтмакс»