Безперервний розлив сталі
Безперервний розлив сталі — процес отримання з рідкої сталі злитків-заготовок (для прокатки, кування або пресування), що формуються безперервно в міру надходження рідкого металу з одного боку виливниці-кристалізатора і видалення частково затверділої заготовки з протилежного боку. Відбувається на установках безперервного розливу сталі (УБРС), що також називаються машинами безперервного розливання заготовок (МБРЗ).
-2_NT.PNG.webp)
-1_NT.PNG.webp)
Прискорене твердніння металу в кристалізаторі відбувається внаслідок того, що виливниці виготовлені з високотеплопровідних матеріалів (міді, латуні) і охолоджуються водою. Зливок, що виходить з кристалізатора, перерізається киснево-ацетиленовими різаками на заготовки потрібної довжини, які ще раз охолоджуються водою з форсунки.
На машинах безперервного розливання сталі виготовляються сляби й блюми.
Історія
Спосіб отримання продукції безпосередньо з рідкого металу (так звана беззлиткова прокатка) був запропонований у 1855 Г. Бессемером. Експериментальні роботи, проведені в цій галузі у ряді країн, не дали позитивних результатів. Перспективнішим виявився спосіб отримання з рідкого металу не готового виробу, а проміжної заготовки з розмірами, як правило, меншими, ніж при литві у виливницю. У 30-х рр. ХХ ст. почало розвиватися безперервне лиття через водоохолоджувальну виливницю-кристалізатор заготовок з кольорових металів і сплавів, головним чином алюмінієвих і мідних. Сталеві заготовки таким методом були вперше отримані З. Юнгансом (Німеччина) у 1939. У СРСР роботи з освоєння безперервного розливання сталі були початі в 1944, а в 1955 на Горьківському заводі «Червоне Сормово» введена в експлуатацію перша промислова установка безперервного розливання сталі (УБРС). У 1973 в СРСР на 21 заводі було 36 УБРС; в усьому світі працювало понад 500 УБРС. Крім СРСР, велике поширення цей спосіб отримав у США, Японії, ФРН та Італії.
Техніка і технологія
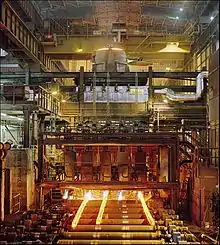
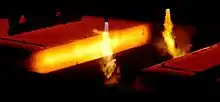
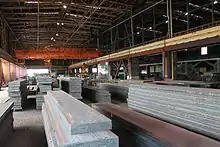
Безперервне розливання сталі має наступні переваги перед звичайним розливанням: на 10-15 % скорочується витрата металу на 1 т придатного прокату внаслідок зменшення обрізу головної і донної частин заготовки; скорочуються капітальні витрати на спорудження металургійного заводу, оскільки виключаються парк чавунних виливниць, відділення для їх підготовки та вилучення зливків з виливниць, дорогі блюмінги або слябінг, на яких великі злитки обжимаються в заготовку для подальшої прокатки; створюються умови для повної механізації і автоматизації процесу розливання; завдяки прискоренню затвердіння підвищується ступінь однорідності металу, поліпшується його якість.
При безперервному розливанні сталі рідкий метал надходить в наскрізну виливницю-кристалізатор. Стінки кристалізатора (виготовленого зазвичай з міді) інтенсивно охолоджуються водою, що циркулює по наявних у них каналах. На початку процесу в кристалізатор вводиться тимчасове дно — так звана затравка. Метал твердне поблизу стінок кристалізатора й поблизу затравки, і оболонка заготовки починає витягуватися з кристалізатора із заданою швидкістю. Зверху в кристалізатор безперервно подається рідкий метал в такій кількості, щоб його рівень був постійним у процесі всього розливання. Для зменшення зусиль витягування кристалізатору надається зворотно-поступальний рух по поздовжній осі, а на його стінки подається мастило. Поверхня рідкого металу охороняється від окиснення шаром синтетичного шлаку або захисною атмосферою з інертного газу. Заготовка що виходить з кристалізатора з рідкою серцевиною потрапляє в зону вторинного охолодження, де на її поверхню подається з форсунок розпорошена вода. Після затвердіння по всьому перетину заготовка розрізається на частини необхідної довжини. Відстань L (м) від рівня металу в кристалізаторі до місця, де закінчується кристалізація заготовки товщиною а (м), відливається зі швидкістю v (м / хв), так само: L = (240—340) a2 × v. Значення коефіцієнта пропорційності залежить від профілю та розміру заготовки та від марки разливаємої сталі.
До 1963 в промисловому масштабі застосовувалися УБРС вертикального типу, у яких формування заготовки та різання її здійснювалися на вертикальній ділянці. При литві заготовок великої товщини ділянку її різання розташовується на відстані 15-20 м від кристалізатора, а загальна висота установки може перевищувати 40 м. Для розміщення такої установки потрібна споруда веж чи колодязів. Прагнення зменшити висоту УБРС призвело до створення установок радіального, і криволінійного типів. На радіальних УБРС кристалізатор і напрямні пристрої вторинного охолодження розташовані на дузі певного радіуса (зазвичай радіус дорівнює 30-40 товщинам відливається заготовки). В кінці радіальної ділянки заготовка проходить через правильно-тягнучі ролики і виводиться в горизонтальне положення, в якому проводиться різання на мірні довжини. На УБРС криволінійного типу кристалізатор і частина зони вторинного охолодження мають постійний радіус; потім радіус збільшується і відбувається поступове випрямлення заготовки.
УБРС радіального і криволінійного типів, у яких неповністю затверділа заготовка виходить на горизонтальну ділянку, дозволяють значно підвищити швидкість розливання при великих перерізах заготовки, так як ділянка різання може бути розташованою на досить великій відстані від кристалізатора (30-35 м). Загальна висота таких установок, як правило, не перевищує 12 м.
На УБРС відливаються заготовки квадратного перерізу розміром від 50x50 до 300×300 мм, плоскі сляби товщиною від 50 до 300 мм і шириною від 300 до 2000 мм, круглі заготовки (суцільні і з внутрішньою порожниною) діаметром від 100 до 550 мм, з яких отримують труби, сортовий і листовий прокат, поковки. Велика ступінь хімічної однорідності по довжині і поперечним перерізом безперервнолитих заготовок забезпечує стабільні механічні властивості і підвищує надійність роботи металовиробів. Завдяки своїм перевагам безперервне розливання сталі прийняте як основний спосіб розливання у всіх нових споруджуваних сталеплавильних цехах і буде широко використовуватися при реконструкції діючих заводів. Найбільша продуктивність УБРС забезпечується при їх роботі в поєднанні з кисневими конвертерами. У цьому випадку досягається рівність циклів випуску сталі з конвертера і розливання її на УБРС, завдяки чому рідкий метал може подаватися на установку безперервно протягом тривалого часу. У цехах з сучасними дуговими печами також може бути організоване розливання так званим методом «плавка на плавку» (одна установка безперервно приймає метал від декількох печей). Перспективні агрегати, в яких безперервне розливання сталі поєднується з безперервною прокаткою в єдиному потоці. При цьому знижуються витрати енергії, підвищуються якість злитка і вихід придатного, скорочується цикл виробничих операцій від виплавки сталі до одержання готового прокату. Такі агрегати вже стали до ладу.
Машини безперервного розливання сталі
Машини для безперервного розливання сталі можна поділити на три групи:
- 1) машини, в яких зливок і кристалізатор рухаються з однаковою швидкістю (машина М. Ф. Голдобіна);
- 2) машини, в яких зливок рухається відносно поверхні кристалізатора, встановленого вертикально або похило (кристалізатор нерухомий або має періодичний зворотно-поступальний рух);
- 3) машини періодичного розливання, в яких надходження металу в кристалізатор і виймання зливка періодично чергуються. Зливки виймають, розсуваючи піввиливниці кристалізатора.
Безперервне розливання сталі не потребує розливного устаткування (виливниць, піддонів, сифонних пристосувань тощо), відділень для підготовки виливниць і роздягання зливків та окремих нагрівальних колодязів і обтискних станів прокатних цехів. Вихід придатного металу при безперервному розливанні сталі іноді підвищується до 90—95 %. Швидке охолодження зливка сприяє одержанню хімічно однорідного, дрібнозернистого металу.Розповсюдження процесу
Безперервний розлив сталі є найпрогресивнішою технологією, і в індустріально розвинених країнах цей процес бурхливо розвивався в 1970-1980-х роках, і до 1995 р. практично у всіх вказаних країнах (у Китаї − в 2003 р.) частка безперервного розливу сталі перевищила 95 %. У Росії частка даного процесу у 2007 р. становила майже 55 %, а в Україні — 30 %.
Джерела
Література
- Безперервне розливання сталі. // Українська радянська енциклопедія : у 12 т. / гол. ред. М. П. Бажан ; редкол.: О. К. Антонов та ін. — 2-ге вид. — К. : Головна редакція УРЕ, 1974–1985.