Концентрація на столах
Концентра́ція на стола́х (рос. концентрация на столах, англ. table concentration, нім. Herdarbeit, Sortierung f auf Herden m pl) — у збагаченні корисних копалин — процес розділення сипкої суміші мінеральних частинок за їх густиною в тонкому потоці води, яка тече по нахиленій деці концентраційного столу, що здійснює зворотно-поступальний поздовжній рух.
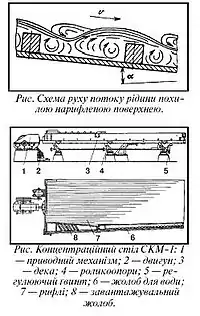
.JPG.webp)
Область застосування: за крупністю матеріалу — 0,074 — 13 мм; за густиною — 1 200—15 600 кг/м3.
Технологія процесу концентрації на столах
Технологічні параметри
До головних технологічних і конструктивних параметрів, які впливають на ефективність процесу концентрації на столах, належать: речовинний склад вихідного матеріалу і його підготовка до процесу, вміст твердого в живленні й витрати змивної води, частота коливань і хід деки, кут її нахилу і тип нарифлень .
Речовинний склад вихідного матеріалу характеризує можливість ефективного застосування процесу концентрації.
Форма зерен має важливе значення при збагаченні на столах. Зерна важких мінералів кубічної форми розташовуються у верхній частині віяла продуктів і виділяються у відходи, а плоскі або витягнуті зерна (тієї ж густини) розташовуються у віялі ближче до промпро-дукту. Видовжені або плоскі зерна краще зважуються у турбулентно-му потоці й тому виносяться або в промпродукт, або в концентрат.
Вміст твердого в живленні коливається від 15 до 40%. Оптимальним є вміст твердого 20–25%. При надмірній розрідженості живлення збільшується розпушеність матеріалу і значно зростає швидкість транспортування в поперечному напрямку, що приводить до виносу важких мінералів у легкий продукт. Щоб запобігти цьому зменшують поперечний кут нахилу деки. При недостатній розрідженості живлення зменшується розпушеність матеріалу, що перешкоджає проходженню частинок важких мінералів у нижні шари, при цьому смуга важких мінералів у віялі продуктів виділяється нечітко.
Підготовка матеріалу перед збагаченням на столах полягає в його класифікації за крупністю. Крупність вугілля, що збагачується на концентраційних столах, повинна бути в межах 0,2–6 мм. Тому первинна підготовка вугілля зводиться до класифікації по зерну 6 мм і знешламленню з метою одержання класу заданої крупності.
Збагачення ширококласифікованого матеріалу крупністю 0,04 – 3 мм можливе тільки в тих випадках, коли з економічних міркувань допускається невисока ефективність збагачення або коли в матеріалі немає зростків, а крупність важких зерен суттєво відрізняється від легких. У більшості випадків, особливо при збагаченні корінних олов’яних, вольфрамових руд і руд рідкісних металів, матеріал перед збагаченням на столах класифікують на гідравлічних класифікаторах з одержанням 4 – 6 класів. Чим менша різниця в густині розділюваних мінералів і чим більше зростків у вихідному продукті, тим вужчою повинна бути шкала класифікації. Іноді для підвищення ефективності класифікації вихідний матеріал перед подачею в гідравлічний класифікатор знешламлюють в гідроциклонах, механічних класифікаторах або в конусах.
Підготовка тонкозернистих і шламистих матеріалів крупністю дрібніше 0,02 мм до збагачення на столах полягає в їх знешламленні (відділення класу менше 15 мкм) і згущенні.
Змивна вода необхідна для видалення частинок легких мінералів у кінці деки. При невеликих витратах змивної води і малому поперечному нахилі деки матеріал верхніх шарів, що складається з частинок малої густини, може вилучатися у важкий продукт. Надмірний поперечний нахил деки, великі витрати змивної води і нерівномірний її розподіл приводять до виносу частинок великої густини з каналів між рифлями. Нестача змивної води спричиняє засмічення важкого продукту легкими частинками.
Продуктивність концентраційних столів залежить від крупності живлення, різниці в густині розділюваних мінералів і вимог до якості продуктів збагачення. В операціях перечищення промпродуктів продуктивність столів зменшують на 20 – 40 %, а в операціях доведення концентратів – на 50 % у порівнянні з продуктивністю операції основної концентрації.
Конструктивні параметри
Кут поперечного нахилу деки визначає швидкість руху водного потоку. Великі швидкості (при великих кутах поперечного нахилу) сприяють турбулізації потоку і знесенню дрібних зерен, що, у свою чергу, приводить до зниження якості продуктів збагачення. Тому при збагаченні дрібнозернистих матеріалів кут поперечного нахилу складає 1,5-2,5º, при збагаченні грубозернистих – 4-8º, а для особливо крупних і важких мінералів він може бути збільшений до 10º.
Кут поперечного нахилу деки і витрати змивної води взаємопов’язані та є основними регулюючими параметрами при експлуатації концентраційних столів.
Кут подовжнього нахилу деки невеликий: від –0,003º до +0,4º (знак «–» означає опускання розвантажувального кінця деки, знак «+» – його підйом). Подовжній нахил деки за ходом руху матеріалу при переробці тонкозернистих і шламистих продуктів збільшує транспортуючу здатність, а нахил деки в протилежному напрямку при переробці крупнозернистих продуктів, навпаки, зменшує транспортуючу здатність.
Нарифлення, що застосовують на практиці , поділяють в основному на такі типи: піскові (для матеріалів крупністю +0,2 мм) і шламові (для матеріалів крупністю –0,2 мм).
Практика збагачення вугілля на концентраційних столах
Збагачення на концентраційних столах знаходить обмежене застосування в практиці переробки дрібних і тонких класів вугілля. Воно використовується з метою одержання низькозольних концентратів і головним чином для знесірчення.
Збагачення вугілля з використанням концентраційних столів може провадитися за різними схемами в залежності від властивостей вихідного матеріалу і призначення продуктів збагачення. Розроблені технологічні схеми збагачення антрацитового штибу крупністю 0 – 6 мм, шламів згущувачів і відстійників, відсівів енергетичного вугілля, перезбагачення промпродукту відсаджувальних машин.
Основна перевага концентраційних столів перед апаратами інших типів полягає в можливості їх використання для ефективного виділення піриту з вугілля, що має значний вміст сірки.
Література
- Мала гірнича енциклопедія : у 3 т. / за ред. В. С. Білецького. — Д. : Донбас, 2004. — Т. 1 : А — К. — 640 с. — ISBN 966-7804-14-3.
- Смирнов В. О., Білецький В. С. Гравітаційні процеси збагачення корисних копалин. Навчальний посібник. — Донецьк: Східний видавничий дім, — 2005. — 300 с.
- Смирнов В. О., Сергєєв П. В., Білецький В. С. Технологія збагачення вугілля. Навчальний посібник. — Донецьк: Східний видавничий дім, — 2011. — 476 с.