Обкочування
Обкочування – процес грудкування зволожених тонкоподрібнених матеріалів, оснований на їх здатності при перекочуванні утворювати гранули сферичної форми (обкотиші або котуни) без застосування безпосереднього тиску. Для зміцнення зволожені обкотиші піддають сушці, випалу і іншим видам обробки.
Опис технології
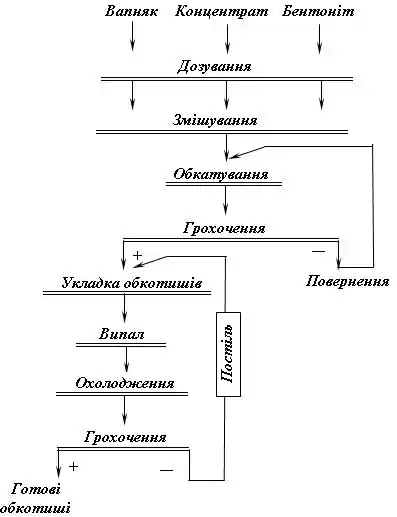
Процес одержання випалених обкотишів (рис. ) складається з трьох основних стадій: підготовки компонентів шихти до обкочування, одержання вологих обкотишів і їх зміцнюючого випалу. Вихідними матеріалами і в’яжучими компонентами для обкочування, можуть бути концентрат, дрібна руда, вапняк, зв’язуючі домішки, вода, тверде, рідке і газоподібне паливо.
Попередня підготовка матеріалів до обкочування полягає в усередненні концентрату, подрібненні флюсових і зв’язуючих домішок (бентоніту, вапняку і т.п.), а при несприятливому гранулометричному складі і в подрібненні концентрату і руди. Наступною операцією при підготовці до обкочування є дозування компонентів шихти. Для усереднення шихти за фізичними властивостями і хімічним складом її перед обкочуванням змішують в шнекових, роторних і барабанних змішувачах. При виробництві неофлюсованих обкотишів змішування виконують в одну стадію. При виробництві офлюсованих обкотишів до змішування висувають більш високі вимоги, тому його виконують в дві або три стадії. Обкочування виконується в барабанних і тарільчатих обкотувачах (грануляторах). Вибір і регулювання параметрів операції обкочування (кут нахилу чаші, частота обертання, вихідне шихтове навантаження) виконують в кожному конкретному випадку в залежності від властивостей шихти і необхідної крупності обкотишів.
Обкочують тонкоподрібнені концентрати корисних копалин, які в основному відносяться до гідрофільних речовин. При взаємодії з водою тонкі частинки концентрату утворюють окремі агрегати – «зародкові грудки». При русі матеріалу по обертальній поверхні апарату для обкочування вологі частинки накочуються на поверхню «зародкової грудки» і утворюють сферичні обкотиші.
Роль води в процесі обкочування надзвичайно велика, тому що визначає умови утворення обкотишів. Її оптимальний вміст залежить від хіміко-мінералогічних властивостей частинок, їх форми, вологоємності і т.п. Вологість шихти в кожному конкретному випадку визначається експериментально (вологість магнетитових і гематитових концентратів становить 8 – 10 %, бурих залізняків – 20 – 25 %, рудного дріб’язку – 6 – 8 % і т.д.). Зниження вологості в процесі обкочування викликає зменшення пластичності обкотишів, порушення гранулометричного складу і зниження продуктивності обладнання. Підвищення вологості веде до зниження міцності обкотишів, надмірного підвищення пластичності, в результаті чого обкотиші злипаються в грязеві грудки.
Під дією тиску, що виникає у точці контакту обкотишів з площиною обертання вони ущільнюються, структура їх стає однорідною. Найбільш ефективно обкочуються тонкі концентрати крупністю 90 – 95 % класу – 0,056 мм. Як зв’язуючі і ущільнюючі домішки використовують гідрофільні вологоємні мате-ріали, що утворюють з водою стійкі суспензії. Поширена домішка – бентоніт, невелика добавка якого (до 1 %) підвищує міцність зволожених, висушених і випалених обкотишів.
Випалюють обкотиші в агрегатах трьох типів: конвеєрних випальних машинах, комбінованих установках (колосникова решітка – трубчата піч) і в шахтних печах. При термічній обробці обкотиші послідовно проходять стадії сушки, підігріву, випалу і охолодження. При використанні шахтних печей і конвеєрних машин всі операції послідовно здійснюються в одному агрегаті.
Сушка – перша стадія термозміцнення обкотишів. Вона проводиться в щільному шарі, через який просмоктуються гарячі гази. Температура газів на вході в шар вологих обкотишів становить 250 – 400оС.
Після сушки відбувається зміцнюючий випал обкотишів. Він полягає в поступовому нагріванні обкотишів гарячими газами до 1250 – 1300оС. Зміцнення обкотишів з магнетитових концентратів відбувається в результаті твердофазного спікання окремих зерен концентрату, окиснення магнетиту в гематит і часткового утворення шлакового зв’язку при розм’якшенні пустої породи. Оскільки випал обкотишів з магнетитових концентратів зв’язаний з реакцією окиснення, склад газів, в атмосфері яких проводиться випал, повинен бути окиснювальним (вміст кисню в газах – 10 – 15 %). Випал обкотишів з гематитових концентратів зв’язаний не з окисненням, а тільки з твердофазним спіканням рудних частинок і утворенням в обкотишах шлакових зв’язків. На технологію випалу і якість випалених обкотишів впливає їх розмір, так як тривалість окиснення в дифузійному режимі прямо пропорційна квадрату їх діаметра. Крім того, зі зменшенням крупності обкотишів зростає їх міцність при відновленні. Структура випалених обкотишів значною мірою залежить від режиму їх випалу. Кращими металургійними властивостями володіють достатньо повно окиснені обкотиші з зернами магнетиту частково зцементованими шлаковим зв’язком. В результаті випалу обкотиші не руйнуються при перевантаженнях і при нагріванні в доменних печах.
Охолодження обкотишів - заключна операція термозміцнюючого випалу. Вона може здійснюватися або в тих же апаратах, що й випал, або в окремих охолоджувачах. Температура охолоджених обкотишів не повинна перевищувати 100 – 130оС.
Обкотиші з тонкоподрібнених концентратів однорідні за крупністю і хімічним складом, мають добру відновлювальну здатність і достатню міцність.
Обкочування використовується для підготовки тонкоподрібнених і пилоподібних матеріалів до металургійного переділу і транспортування їх на великі відстані. Обкочування набуло поширення для залізорудних концентратів. Обкочуванню підвергають також хромові, фосфористі і флюоритові концентрати, а в деяких випадках й концентрати руд кольорових металів.
Література
- Мала гірнича енциклопедія : у 3 т. / за ред. В. С. Білецького. — Д. : Донбас, 2007. — Т. 2 : Л — Р. — 670 с. — ISBN 57740-0828-2.
- Білецький В.С., Олійник Т.А., Смирнов В.О., Скляр Л.В. Техніка та технологія збагачення корисних копалин. Частина ІІІ. Заключні процеси. – Кривий Ріг: Криворізький національний університет. 2019. – 220 с.