Поверхнева лазерна обробка
Поверхне́ва ла́зерна обро́бка (англ. laser surface processing) — це локальне нагрівання, локальне плавлення чи локальне випаровування матеріалу, що обробляється за рахунок впливу тепла, поглинутого матеріалом в місці впливу лазерного променя. Залежно від величини щільності потужності лазерного впливу, матеріал може нагрітися, розплавитися чи випаруватися. Щільність потужності це величина потужності, віднесена до одиниці площі, зазвичай, квадратному сантиметру. Більшість металів випаровується при щільності потужності, що перевищує кілька мільйонів ват на квадратний сантиметр.
На режимах, що не викликають руйнування матеріалу, реалізуються різні процеси лазерної поверхневої обробки. В основі цих процесів лежать незвичайні структурні та фазові зміни в матеріалі, що виникають внаслідок надвисоких швидкостей його нагріву і подальшого охолодження в умовах лазерного опромінення. Важливу роль при цьому відіграють можливість насичення поверхневого шару елементами навколишнього середовища, зростання щільності дислокацій в зоні опромінення і інші ефекти[1].
Лазерну обробку використовують для таких операцій: вирізання заготовок, модифікація поверхні матеріалу, нанесення маркування, локальне легування, пайка, зварювання, наплавлення, легування тощо.
Види поверхневої лазерної обробки
Залежно від ступеня розвитку зазначених явищ в матеріалі розрізняють кілька видів поверхневої лазерної обробки (табл. 1), можливість реалізації яких визначається основному рівнем щільності потужності випромінювання.
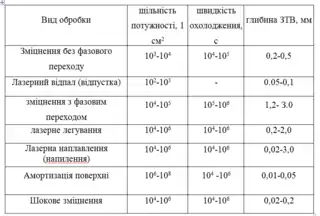
Лазерне наплавлення (напилення) дозволяє нанести на поверхню оброблюваного матеріалу шар іншого матеріалу, що поліпшує експлуатаційні характеристики основного. Новий різновид лазерного зміцнення — аморфування поверхні сплаву в умовах швидкісного опромінення (дуже коротким імпульсом або скануючим променем). Надвисокі швидкості тепловідведення, що досягаються при цьому, забезпечують своєрідне «заморожування» розплаву, утворення металічного скла або аморфного стану поверхневого шару. В результаті досягаються висока твердість, корозійна стійкість, поліпшені магнітні характеристики та інші специфічні властивості матеріалу[2].
Процес лазерного аморфування можна здійснити при обробці сплавів спеціальних складів (у тому числі і на основі заліза), а також інших матеріалів, попередньо покритих спеціальними складами, які самостійно або спільно з матричним матеріалом схильні до аморфування.
Перші чотири види поверхневої лазерної обробки до теперішнього часу набули найбільшого поширення. Для практичної реалізації аморфування і шокового зміцнення потрібні додаткові дослідження. Всі ці види обробки можна здійснити за допомогою як імпульсного, так і безперервного випромінювання, причому зміцнення без фазового переходу більш придатне для прецизійної обробки поверхонь порівняно невеликих розмірів, продуктивність процесу обмежується порівняно невисокою частотою проходження імпульсів устаткування, що випускається. Безперервне випромінювання дозволяє проводити обробку з високою продуктивністю поверхонь великих розмірів.
Обробка імпульсним випромінюванням
До технологічних характеристик зміцнення імпульсним випромінюванням відносяться розмірні параметри (діаметр одиничної зони зміцнення, ширина лінійного зміцнення, глибина зміцненої зони), ступінь зміцнення (мікротвердість), шорсткість обробленої поверхні та ін. На ці характеристики впливають вид оброблюваного матеріалу, схема обробки, енергетичні параметри опромінення, ефективність поглинання випромінювання, середовище і т. п .
Підвищення ефективності зміцнення може бути досягнуто збільшенням поглинальної здатності матеріалу при обробці імпульсним інфрачервоним випромінюванням. Для цього використовують покриття, наприклад, колоїдний розчин графіту, або попередню хімічну обробку опромінюваної поверхні розчином на основі пікринової кислоти. Глибина зміцнення залежить від виду матеріалу (марки сталі) і меншою мірою від навколишнього середовища. У загартованих сталях глибина зміцнення при одних і тих же умовах опромінення на 30 — 60 % більше, ніж у відпалених сталях. Ступінь зміцнення також залежить як від виду матеріалу, так і від його вихідного стану. Для загартованих сталей рівень зміцнення вище, ніж для відпалених.
При реалізації лінійного зміцнення обробка зазвичай ведеться з перекриттям зон лазерної дії. У перекритих ділянках відбувається відпустка вогнезміцненого матеріалу в результаті дії наступного імпульсу. У результаті в поперечному перерізі зміцнений шар являє собою характерну «лускату» структуру. При двокоординатному зміцненні додаткове перекриття дещо ускладнює процеси, що відбуваються в зоні обробки. Зокрема, це проявляється у вузлових точках, де матеріал чотири рази піддавався опроміненню.
По закінченню лазерного імпульсу при наступному швидкому охолодженні за рахунок тепловідведення в масив матеріалу в цій зоні відбулася повний гарт з утворенням мартеїсітної структури, що володіє високою твердістю[3].
У вузлових точках (ділянки прямокутної форми) там, де чотири зони лазерної дії перекривають один одного, матеріал сильно труїться, і його твердість становить 5000-5500 МПа, що характерно для тростітної структури. Такі ділянки з'являються внаслідок багаторазової відпустки структур гарту, що раніше виникли при послідовному впливі на матеріал ряду імпульсів[4]
Обробка безперервним випромінюванням
Найбільш поширена схема обробки — однодоріжкове зміцнення. Залежно від траєкторії переміщення променя або закону переміщення заготовки конфігурація зміцненого ділянки поверхні може мати різний вигляд. Продуктивність П обробки залежить від швидкості v відносного змінність П обробки залежить від швидкості v відносного переміщення променя і поверхні, а також від ширини зони В: П= vB — якщо ж паралельно наноситься кілька доріжок зміцнення, то продуктивність також залежить від їх числа і коефіцієнта перекриття або кроку обробки. З схеми (рис. 1) видно, як змінюється мікротвердість по довжині L оброблюваної зони залежно від ступеня перекриття (кроку s) доріжок зміцнення. Як і при імпульсній обробці, в перекритих зонах спостерігається істотне зниження; твердості в результаті.
Однорідність і товщина покриття є важливими факторами забезпечення якісного зміцнення. Оптимальна товщина покриття — 20-50 мкм. Занадто тонке покриття знижує глибину зміцнення внаслідок швидкого випаровування, збільшення також товщини вище зазначених значень призводить до неоднорідності результатів обробки — освіті як оплавлених, так і недостатньо прогрітих ділянок поверхні.
Збільшення швидкості обробки також впливає на зміну мікротвердості в зміцненому шарі. Так, із збільшенням швидкості до 6.0 м/хв зміна мікротвердості може досягати 400 МПа.
Лазерні легування, наплавлення, маркування, гравіювання
Лазерне легування відрізняється від звичайного лазерного зміцнення тим, що підвищення твердості та інших експлуатаційних показників досягається не тільки за рахунок структурних і фазових перетворень в зоні лазерної дії, але і шляхом створення нового сплаву з відмінним від матричного матеріалу хімічним складом. Проте в основі цього нового сплаву лежить матричний матеріал. На відміну від легування при лазерному наплавленні матричний матеріал може перебувати лише в невеликому шарі між матрицею і спрямованим шаром, який служить сполучною середовищем.
Наплавлений же шар істотно відрізняється від матричного матеріалу.
Ці види поверхневої лазерної обробки дуже перспективні внаслідок зростання дефіциту чистих металів типу W, Mo, NiCr, Co. V. Гострої необхідності зниження витрати високолегованих сталей і у зв'язку з цим збільшення надійності і довговічності виробів з менш дефіцитних конструкційних матеріалів.
Процеси локального легування і наплавлення реалізуються за допомогою як імпульсного, так і безперервного випромінювання за тими ж схемами, що й звичайне лазерне зміцнення. Технологічні закономірності процесу, крім раніше розглянутих, залежать також від способу подачі в зону обробки легуючого складу, виду легуючого елемента (елементів), властивостей матричного матеріалу.
Існують такі способи подачі легуючого елемента (середовища) в зону лазерної дії[5]:
- Нанесення легуючого складу у вигляді порошку на оброблювану поверхню;
- Обмазка поверхні спеціальним легуючим складом;
- Легування в рідині (рідкої легуючої середовищі);
- Накочування фольги з легуючого матеріалу на оброблювану поверхню;
- Легування в газоподібному легуючому середовищі;
- Утримання феромагнітних легуючих елементів на матричній поверхні магнітним полем;
- Електроіскрове нанесення легуючого складу;
- Полум'яне нанесення покриття;
- Детонаційне нанесення легуючого складу;
- Електролітичне осадження легуючого покриття;
- Подача легуючого складу в зону обробки синхронно з лазерним випромінюванням.
При маркуванні лазерним випромінюванням досягається мініатюрність завдається знака. Ширина утворює знака може не перевищувати 10 мкм при розмірах самого знака до декількох десятків мікрометрів. Безконтактність методу і відсутність механічного впливу дозволяють маркувати тонкостінні, тендітні деталі, вузли і вироби в зборі. Висока точність і якості знаків гарантують надійність і стабільність їх зчитування фотоелектронні пристроями. До достоїнств лазерного маркування відносяться висока продуктивність і можливість повної автоматизації процесу.
Велике поширення лазерне маркування знаходить в електронній промисловості і приладобудуванні. Так, на мініатюрних конденсаторах з обкладкою площею 2мм2 за допомогою випромінюванні з модуліровкою добротністю лазера па алюмоптрієвому гранаті (ЛИГ) наносяться фірмовий знак і величина ємності.
Примітки
- Гладуш Г. Г. Фізичні процеси при лазерній обробці матеріалів. 2002 р. − 208 с.
- http://referat.ru
- http://lmaster.com.ua/ukr.php?lang=ukr&page_id=8
- Григорьянц А. Г., Соколов А. А. Лазерна техніка та технологія 1975 р. −191с.
- Рикалін М. М. Лазерна обробка матеріалів. «Машинобудування» 1995 р. −296с.
Див. також
Джерела
- Черненко В. С., Ківдрачук М. В., Дудка О. І. Променеві методи обробки: Навч. посібник. — К.: Кондор, 2004. — 166 с. — ISBN 966-7982-70-X
- Інженерія поверхні: Підручник / К. А. Ющенко, Ю. С. Борисов, В. Д. Кузнецов, В. М. Корж — К.: Наукова думка, 2007. — 559 с. — ISBN 978-966-00-0655-3
- Григорьянц А. Г. Основы лазерной обработки материалов. М.: Машиностроение 1989. — 304 с. — ISBN 5-217-00432-0
- Лазерное и электроэрозионное упрочнение материалов. Коваленко В.С, Верхотуров А. Д., Головко Л. Ф., Подчерняева И. А.