Схеми дроблення
Схеми дроблення — сукупність стадій дроблення.
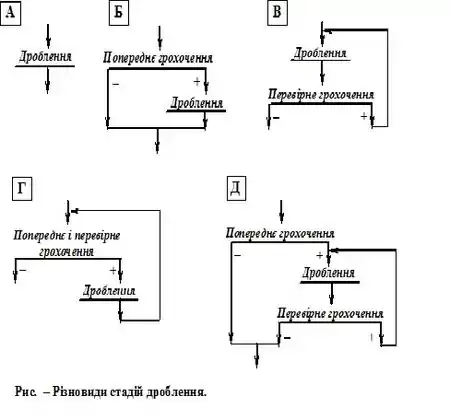
Загальний опис
Операції дроблення на збагачувальних фабриках застосовуються: при крупному вкрапленні мінералів — для підготовки корисних копалин до операцій збагачення, при дрібному і тонкому вкрапленні — для підготовки до операцій подрібнення. На дробильно-сортувальних фабриках операції дроблення мають самостійне значення.
Операція дроблення й операції попереднього та перевірного грохочення складають стадію дроблення, а сукупність стадій дроблення — схему дроблення. Залежно від наявності і призначення операцій грохочення в схемах дроблення розрізняють п'ять різновидів стадій (одностадійних схем) дроблення (рис.).
Різновиди стадій, які використовуються в схемах дроблення такі: стадія А — відкрита; стадія Б — відкрита з попереднім грохоченням; стадія В — замкнута з перевірним (контрольним) грохоченням; стадія Г — замкнута з поєднанням попереднього і перевірного грохочення; стадія Д — замкнута з роздільними попереднім і перевірним грохоченням.
Схема підготовчих операцій визначається виходячи з речовинного складу і фізичних властивостей корисної копалини, а також крупності матеріалу, прийнятої в схемі збагачення.
При збагаченні корисних копалин, у яких корисні і породні мінерали розкриваються при крупному дробленні, схеми підготовчих операцій можуть обмежитися крупним (середнім) дробленням і грохоченням.
При наявності в корисних копалинах крупновкраплених корисних мінералів або агрегатів мінералів з контрастними фізико-хімічними властивостями, що використовується при їх розділенні, схема підготовчих операцій може розмикатися з включенням операції попередньої концентрації, що дозволяє виділити частину збагаченого матеріалу, відвальних відходів, або розділити корисну копалину на продукти, що надалі переробляються за різними схемами. На збагачувальних фабриках, що переробляють дрібно- і тонковкраплені руди кольорових, рідкісних і чорних металів, схеми рудопідготовки включають операції дроблення і подрібнення з операціями грохочення і класифікації.
При виборі раціональної схеми дроблення необхідно вирішити два основних питання:
– про число стадій дроблення,
– про необхідність операцій грохочення в окремих стадіях.
Число стадій дроблення визначається початковою і кінцевою крупностями матеріалу, що дробиться. Максимальна крупність грудок у вихідному матеріалі, що надходить на дроблення, залежить від продуктивності гірничодобувного підприємства і системи гірничих робіт. Найбільш крупна руда (до 1200 мм) одержується при відкритих роботах і великій продуктивності кар'єру, найбільш дрібна (до 300 мм) — при підземних гірничих роботах і малій продуктивності шахти. Оптимальна крупність дробленого продукту, який подається в стержневі млини повинна становити 15–25 мм, у кульові — 10–15 мм. Критерієм, який враховує співвідношення між максимальними розмірами зерен матеріалу, що подається на дроблення, і дробленого, служить загальний ступінь дроблення: Sзаг = Dвих / dдр,
де Dвих — розмір максимальної грудки матеріалу, що подається на дроблення, мм; dдр — розмір максимальної грудки дробленого матеріалу, мм.
На великих збагачувальних фабриках загальний ступінь дроблення може досягати 100 і більше. Одержати такий ступінь дроблення за один прийом неможливо, він коливається звичайно в межах 4 — 6. Тому найчастіше зустрічаються схеми дроблення, що складаються з трьох стадій — крупного, середнього і дрібного дроблення. Число стадій дроблення вибирають виходячи з загального ступеня дроблення, що дорівнює добутку ступенів дроблення в окремих стадіях.
Sзаг = S1ּ S2ּ…ּ Sn ,
де Si — ступені дроблення в окремих стадіях.
Правила вибору схеми дроблення
З огляду на сказане, перше правило вибору схеми дроблення говорить: число стадій дроблення при підготовці руд до подрібнення повинно дорівнювати двом або трьом.
Виняток з цього правила може бути зроблено:
– у випадку використання інерційних, молоткових і роторних дробарок, що мають високі ступені дроблення (20—40);
– для фабрик дуже малої продуктивності (до 100 т/добу), де з метою спрощення схеми дроблення вона приймається одностадійною і при цьому допускається підвищена крупність грудок у живленні млинів;
– для фабрик дуже великої продуктивності (понад 40000 т/добу), що переробляють тверді руди плитнякової будови (типу криворізьких магнетитових кварцитів), приймається чотиристадійна схема дроблення.
Операції попереднього грохочення в схемах дроблення застосовують для зменшення кількості матеріалу, що надходить в операцію дроблення, а також для збільшення рухливості матеріалу в робочій зоні дробарки, що особливо важливо при дробленні в конусних дробарках середнього і дрібного дроблення, схильних до забивання рудним дріб'язком. У той же час застосування операцій попереднього грохочення викликає збільшення капітальних витрат і приводить до ускладнення цеху дроблення. Тому попереднє грохочення варто застосовувати при досить високому вмісті підрешітного класу у вихідному матеріалі (не менше 15 %), а також при високій вологості цього класу, що приводить до зниження продуктивності дробарки.
Звичайно на першій стадії дроблення попереднє грохочення встановлюють при необхідності збільшення пропускної спроможності дробарки.
На другій стадії дроблення в більшості випадків передбачають попереднє грохочення. Однак якщо дробарки середнього дроблення мають великий запас продуктивності в порівнянні з дробарками дрібного дроблення, зв'язаними з ними, то попереднє грохочення не передбачається. Але в цьому випадку варто врахувати властивості корисної копалини (вміст глини, шламу) і її вологість. При несприятливому співвідношенні зазначених параметрів використання попереднього грохочення є необхідним, тому що без попереднього відсіву дріб'язку можлива підпресовка дробарки.
На третій стадії дроблення при малих розмірах розвантажувальних щілин (6 — 7 мм) попереднє грохочення застосовують завжди. Звідси випливає друге правило вибору схеми дроблення:
- попереднє грохочення перед першою стадією застосовується рідко, його застосування повинно бути обґрунтоване;
- попереднє грохочення перед другою стадією, як правило, передбачається, відмова від нього повинна бути обґрунтована;
- попереднє грохочення перед третьою стадією передбачається завжди.
Операції перевірного грохочення застосовують для повернення в дробарку надрешітного продукту. Вміст надрешітного продукту в дробленому може досягати 60 %, при цьому розмір грудок надрешітного продукту може в 2 — 3 рази перевищувати розмір розвантажувальної щілини дробарки. Отже, при наявності перевірного грохочення в останній стадії крупність кінцевого продукту може бути зменшена в 2 — 3 рази і тим самим підвищені показники роботи цеху. Однак введення в схему перевірного грохочення приводить до ускладнення конструктивного оформлення цеху, збільшення капітальних витрат, погіршення санітарних умов праці.
З викладеного випливає третє правило вибору схеми дроблення: в останній стадії дроблення повинна бути операція перевірного грохочення.
Три правила вибору схеми дроблення задовольняють при дрібному вихідному матеріалі схеми АБ, ББ, БГ і БД, при крупному вихідному матеріалі — схеми АББ, БББ, АБГ, ББГ, АБД і ББД. Операція грохочення на першій стадії не обов'язкова. Схеми АБ, ББ, АББ і БББ дозволяють одержати дроблений продукт крупністю до 25 мм, схеми БГ, БД, АБГ, ББГ, АБД і ББД — крупністю до 10—20 мм. Ці схеми і застосовують у більшості випадків на збагачувальних фабриках при підготовці корисних копалин до подрібнення. На збагачувальних фабриках дуже великої продуктивності, що переробляють міцні руди, які дають при дробленні куски плоскої форми, застосовують чотиристадійну схему дроблення ААББ.
Вибір варіанта схеми дроблення
При підготовці руд до подрібнення вибір схеми дроблення залежить від способу і схеми наступного подрібнення, типу руди і її фізичних властивостей (міцності, грудкуватості, злежуваності, змерзлості, грохоченості та ін.). Вибір схеми дроблення здійснюється з урахуванням досвіду роботи підприємств-аналогів, що переробляють подібні руди, і шляхом порівняння сумарних капітальних та експлуатаційних витрат конкуруючих варіантів. Якщо руда міцна або середньої міцності і відносно суха, з'ясовується можливість дроблення її за раціональними схемами до 10 ÷ 20 мм і уточнюється застосовність процесу самоподрібнення. У цьому випадку можливі варіанти:
– одностадійне дроблення руди до 300 мм за схемами А або Б і наступне рудне самоподрібнення;
– тристадійне дроблення руди до 10—15 мм за схемою АБГ і наступне одностадійне подрібнення в кульових млинах;
– тристадійне дроблення руди до 20—25 мм за схемою АБГ і наступне двостадійне подрібнення в стержневих і кульових млинах.
Для фабрик малої продуктивності застосування самоподрібнення, як можливий варіант, не розглядається, для них розглядається можливість використання двостадійних схем дроблення АГ з наступним одностадійним (у кульових млинах) або двостадійним (у стержневих і кульових млинах) подрібненням.
Якщо руди вологі і глинисті, то в схеми дроблення включають операції грохочення для відокремлення найбільш вологого дрібного класу, що направляється безпосередньо в млини. Залежно від конкретних умов дріб'язок виділяється з руди після крупного або середнього дроблення. При високому вмісті глини і вологи передбачають промивання руди і дроблення виконують з подачею води в робочу зону дробарки.
Порівняння варіантів здійснюється за такими показниками: числом машин і їхньою сумарною масою, загальною встановленою потужністю електродвигунів, загальною вартістю основного обладнання, сумарними експлуатаційними витратами на дроблення і подрібнення, технологічною надійністю, можливістю і надійністю автоматичного регулювання технологічних процесів, санітарними умовами праці.
Схеми дроблення при підготовці руд до збагачення
Результати збагачення залежать від ступеня розкриття корисних і породних мінералів. У кожному конкретному випадку ступінь розкриття мінералів повинен вибиратися шляхом техніко-економічних досліджень, тому що він залежить від речовинного складу корисної копалини, вкраплення мінералів, виробничої потужності фабрики, досконалості застосовуваних підготовчих і збагачувальних операцій та інших факторів.
При збагаченні вугілля, а також валунних залізних і крупновкраплених магнетитових руд дроблення виконують до 50—100 мм. Залежно від максимальної крупності сировини дроблення здійснюють за одну або дві стадії з попереднім грохоченням, але, як правило, без перевірного.
Якщо руда крупновкраплена і технологічною схемою передбачається її збагачення відсадкою або у важких суспензіях, то дроблення виконують до крупності 6-30 мм. Схема крупного і середнього дроблення вибирається звичайним способом. Для одержання постійної крупності дробленого продукту бажане застосування перевірного грохочення в останній стадії.
Підготовка до збагачення дрібновкраплених руд рідкісних металів здійснюється дробленням до 6 — 20 мм із наступним подрібненням у стержневих млинах до 0,3—2 мм.
Схеми дроблення при підготовці руд до самоподрібнення
Див. також Самоподрібнення.
Схеми само- і напівсамоподрібнення використовують на збагачувальних фабриках великої і дуже великої продуктивності у випадку одержання технологічних переваг при заміні молольних тіл рудою або у випадках, коли фізичні властивості руди (вологість, глинястість) не дозволяють її дрібно дробити. Застосовуване на збагачувальних фабриках самоподрібнення може бути чотирьох різновидів:
– рудне самоподрібнення, що здійснюється при крупності живлення до 350 мм (іноді до 500 мм);
– напівсамоподрібнення, що здійснюється на матеріалі тієї ж крупності, але в цьому випадку в млин додають сталеві кулі в кількості 5 — 10 % від його об'єму;
– грубе рудногалькове подрібнення (первинне) дозволяє подрібнювати руду крупністю 15 — 25 мм; подрібнюване середовище (руда) подається разом з живленням і повинно мати крупність 100—300 мм;
– тонке рудногалькове подрібнення (вторинне) призначене для переробки руд крупністю 3 — 5 мм при крупності подрібнюваного середовища 25—100 мм.
Рудне самоподрібнення здійснюється в млинах сухого подрібнення типу «Аерофол» або в млинах мокрого подрібнення типу «Каскад». Оскільки сухе подрібнення вимагає складних пристроїв для пиловловлення, пневмокласифікації, регулювання вологості, то для фабрик, що використовують мокрі процеси, сухе подрібнення менш вигідне, ніж мокре.
При рудному самоподрібненні руда підлягає тільки крупному дробленню, при рудногальковому самоподрібненні схеми дроблення аналогічні схемам підготовки руди до подрібнення в стержневих і кульових млинах. Відмінність цих схем полягає лише в тім, що з продуктів дроблення потрібно грохоченням виділити певні класи крупності, які використовуються як подрібнююче середовище. Застосування процесу самоподрібнення приводить до підвищення продуктивності праці, значного спрощення схеми дроблення, зниження капітальних і експлуатаційних витрат, зменшення ошламлювання руди, що подрібнюється, а також забруднення продуктів подрібнення залізом. Однак процес самоподрібнення не універсальний — він не застосовний для м'яких, а також дуже твердих (неміцних, а також дуже міцних) руд, вимагає регулювання гранулометричного складу руди. Крім того, при рудногальковому самоподрібненні необхідно виділяти подрібнююче середовище, що ускладнює схему дроблення і транспортно-складське господарство цеху.
Розрахунок схем дроблення
Для розрахунку схеми дроблення необхідно мати наступні вихідні дані: продуктивність збагачувальної фабрики по вихідній сировині, характеристики крупності вихідної сировини і продуктів дроблення, задану максимальну крупність дробленого продукту, показники ефективності грохочення в окремих стадіях дроблення.
Характеристики крупності вихідної сировини і продуктів дроблення приймаються за результатами досліджень або за практичними даними роботи фабрик-аналогів. При відсутності дослідних даних можна виконати орієнтовний розрахунок з використанням типових характеристик крупності або аналітичних залежностей .
Після вибору й обґрунтування схеми дроблення виконують її розрахунок, послідовно визначаючи:
– Загальний ступінь дроблення,
– Умовну максимальну крупність дроблених продуктів в окремих стадіях,
– Ширину розвантажувальних щілин дробарок в окремих стадіях,
– Розмір отворів сит грохотів в окремих стадіях.
Розрахунок мас продуктів схеми дроблення здійснюється постадійно з урахуванням обраного варіанта стадії, ґранулометричного складу продуктів і ефективності використовуваного в стадії процесу грохочення.
Вибір обладнання до схеми дроблення
Дробарки
Вибір типу і розміру дробарки визначається міцністю корисної копалини, розмірами кусків вихідного і дробленого продуктів, а також необхідною продуктивністю.
Залежно від крупності вихідного і дробленого продуктів розрізняють три стадії дроблення: крупне, середнє і дрібне. Крупне, середнє і дрібне дроблення порід великої і середньої міцності доцільно виконувати в дробарках, які працюють за принципом роздавлювання (щокових, конусних і валкових із гладкими валками); середнє і дрібне дроблення порід великої міцності і в'язких — у дробарках, які працюють за принципом роздавлювання за участю стирання (конусних і значно рідше валкових дробарках із гладкими валками).
Щокові дробарки установлюють переважно на збагачувальних фабриках невеликої продуктивності. Вони в порівнянні з конусними дробарками більш пристосовані для дроблення глинистих і вологих руд, займають менше місця у висоту, простіші конструктивно, але менш пристосовані для дроблення матеріалів пластинчастої форми.
Конусні дробарки переважніше встановлювати на збагачувальних фабриках великої продуктивності.
Обрана дробарка повинна забезпечити необхідну продуктивність при запроектованій крупності дробленого продукту. Ширина приймального отвору дробарки повинна бути на 15 % більшою від розміру максимального куска у вихідному матеріалі. Продуктивність щокових і конусних дробарок звичайно визначають за даними каталогів з урахуванням поправок на дробимість (kдр), насипну густину (kδ) і крупність матеріалу, що дробиться, (kd): Q = Qк kдр kδ kd , т/год,
де Qк — продуктивність дробарки за каталогом, т/год; kдр, kδ , kd — поправочні коефіцієнти.
Якщо дробарка працює в замкненому циклі, то її продуктивність на 30—40 % вища, ніж у відкритому.
На збагачувальних фабриках щокові дробарки використовують для крупного дроблення, а конусні відповідно до призначення — для крупного, середнього і дрібного дроблення гранітів, базальтів, кварцитів, вапняків, руд і інших гірських порід, що мають підвищену міцність.
Конусні дробарки крупного дроблення ККД-1200, ККД-1500 можуть працювати «під завалом».
Щокові дробарки і конусні дробарки крупного дроблення звичайно працюють при ступенях дроблення 3 — 4, конусні дробарки середнього і дрібного дроблення — при ступенях дроблення 4 — 7.
Для дрібного дроблення гірських порід, вогнетривів і інших матеріалів середньої і високої міцності застосовують конусні інерційні дробарки, які забезпечують високий ступінь дроблення (10—15) з одержанням дрібного дробленого матеріалу.
Валкові дробарки з гладкими валками застосовують для середнього і дрібного дроблення руд, коли неприпустиме переподрібнення цінного крихкого мінералу (марганцеві, каситеритові, вольфрамітові руди, калійні солі), іноді їх застосовують для середнього дроблення вугілля й коксу. При виборі дробарок із гладкими валками треба дотримуватися умови захоплення валками куска матеріалу, що дробиться: Dв = (15 ÷ 20) Dmax, де Dв — діаметр валків; Dmax — максимальний розмір кусків матеріалу, що дробиться.
На збагачувальних фабриках дробарки з гладкими валками звичайно використовують при ступені дроблення 3 — 4, їхня продуктивність визначається за формулою: Q = n π D L s δ k, т/год, де n — частота обертання валків, хв-1; D, L — діаметр і довжина хитка, м; s — ширина щілини між валками, м; δ — густина матеріалу, що дробиться, т/м3; k — коефіцієнт розпушення дробленого продукту в момент розвантаження (k = 0,1 — 0,3).
Крупне дроблення порід малої міцності і крихких виконують у дробарках, які працюють переважно за принципом розколювання (зубчатих, голчастих і пікових), а середнє і дрібне дроблення — у дробарках ударної дії (молоткових, роторних і дробарках вибіркового дроблення). Зубчаті дробарки призначені для крупного і середнього дроблення вугілля, антрацитів і сланців при необхідності одержати кусковий дроблений продукт з невеликим вмістом дріб'язку. Зубчаті дробарки працюють при ступенях дроблення 4 — 6. Продуктивність зубчатих дробарок розраховують за формулою (4.11). Для зубчатих дробарок також повинна виконуватися умова захоплення куска матеріалу, що дробиться: Dв = (1,5 ÷ 3,5) Dmax ,
де Dв і Dmax — діаметр валків і максимальний розмір кусків матеріалу, що дробиться, мм.
Валкові дробарки мають багато переваг: простота конструкції, компактність, надійність в експлуатації і невеликий вміст дріб'язку в готовому продукті. Однак вони мають низьку продуктивність і велику питому витрату електроенергії.
Дробарки ударної дії (молоткові і роторні) використовуються для дроблення матеріалів не тільки низької і середньої, але й підвищеної міцності. Переваги дробарок ударної дії — простота конструкції, надійність, компактність, велика продуктивність, високий ступінь дроблення (20 і більше) і порівняно невелика питома витрата електроенергії. Тому вони широко застосовуються для дроблення кам'яного вугілля, коксової шихти, вапняку, руд чорних, кольорових, рідкісних і благородних металів, калійних солей, баритових, флюоритових і азбестових руд, будівельних матеріалів.
Дробарки ударної дії виготовляються одно- і двороторними, з колосниковими решітками і без них, з реверсивними і нереверсивними роторами. Двороторні дробарки в порівнянні з однороторними менше забиваються і звичайно застосовуються для дроблення більш вологих матеріалів і матеріалів, що злипаються, також вони дозволяють завантажувати матеріал більшої крупності. Ширину щілини колосникових решіток і відстань між ними і кінцем бил (молотків) вибирають залежно від необхідної крупності дробленого продукту і вологості матеріалу, що дробиться. При дробленні глинистих вологих руд, щоб уникнути забивання колосникових решіток, відстань між колосниками збільшують. У важких випадках дробарки працюють без колосникових решіток. Продуктивність дробарок ударної дії визначають за ефективністю дроблення: Q = N η eет kдр kd ,
де N — установлена потужність електродвигуна, кВт; η — коефіцієнт використання потужності електродвигуна (η = 0,8 — 0,95); eет — ефективність дроблення еталонної дробарки, т/кВт•год; kдр — поправковий коефіцієнт на дробильність руди; kd — поправочний коефіцієнт на крупність руди.
Роторні дробарки випускають двох типів: ДРК — для крупного дроблення і ДРС — для середнього і дрібного. У роторних дробарок співвідношення між діаметром ротора (Dр) і максимальним розміром куска в живленні (Dmax) становить:
– для дробарок ДРК: Dр = (1,7 … 2) Dmax ,
– для дробарок ДРС: Dр = 3,3 Dmax .
Грохоти
У циклі підготовчих операцій за технологічним призначенням розрізняють попереднє, перевірне, підготовче грохочення і знешламлювання. Для цих цілей застосовують нерухомі і рухливі грохоти різних типів. Вибір типу грохота залежить від розміру кусків вихідного матеріалу, крупності розділення, необхідної ефективності грохочення і фізичних властивостей корисної копалини, з яких основна роль належить густині.
Нерухомі колосникові грохоти встановлюють на першій стадії дроблення при наявності у вихідному матеріалі понад 15 % дріб'язку (за масою) або при відсутності достатнього запасу продуктивності у дробарки крупного дроблення. При подачі корисної копалини з вагоноперекидача ширина грохота має дорівнювати довжині вагона, при завантаженні пластинчастим живильником — ширині живильника. Щоб уникнути зависання грудок матеріалу між бічними стінками грохота, мінімальна його ширина приймається: при великому вмісті великих грудок у вихідному B = 3Dmax, при незначному вмісті — B = 2Dmax + 100 (Dmax — розмір максимальної грудки у вихідному, мм).
Довжина грохота звичайно береться в 2 рази більшою від ширини. Кут нахилу робочої поверхні колосникового грохота при грохоченні вугілля беруть 30—35о, при грохоченні руд — 40—45о, при грохоченні вологих матеріалів і матеріалів, що злипаються, кут нахилу збільшують до 55о. Необхідну площу грохочення розраховують за формулою: F = Q / (qoaδk), м2,
де Q — необхідна продуктивність, т/год.; qo — питома об'ємна продуктивність (м3/год•м2) на 1 мм щілині; a — розмір щілини сита грохота, мм; δ — насипна густина живлення, т/м3; k — коефіцієнт, що враховує ефективність грохочення (k = 1 при Е = 65 — 70 % і k = 2 при Е = 50—60 %).
Барабанні (циліндричні) грохоти застосовують в операціях попереднього грохочення вугілля, промивання легко- і середньопромивних руд, промивання і сортування щебеню, для вловлювання скрапу і крупних кусків руди зі зливу млинів.
Об'ємну продуктивність барабанних (циліндричних) грохотів визначають за формулою: Q = qo aφ, м3/год, де qo — питома об'ємна продуктивність (м3/год•м2) на 1 мм щілині; a — розмір щілини, мм; F — площа сита, м2; φ — коефіцієнт заповнення грохота (φ = 0,15—0,25).
Інерційні грохоти на збагачувальних фабриках використовують для попереднього і перевірного просіювання, зневоднення і знешламлювання, тонкої сухої і мокрої класифікації, промивання, виділення суспензії і відмивання обважнювача, розділення концентрату на товарні продукти. Залежно від насипної густини вихідного матеріалу інерційні грохоти підрозділяються на 3 типи:
• легкого типу Л — для грохочення матеріалів з насипною густиною до 1,4 т/м3;
• середнього типу С — для грохочення матеріалів з насипною густиною до 1,8 т/м3;
• важкого типу Т — для грохочення матеріалів з насипною густиною 2,8 т/м3.
З урахуванням траєкторії коливань грохоти мають такі виконання: І — інерційні з круговими або близькими до них коливаннями (ГІЛ, ГІС, ГІТ); С — самобалансні з прямолінійними коливаннями (ГСЛ, ГСС, ГСТ); ІС — інерційні з самосинхронізовуваними віброзбуджувачами (інерційно-самобалансні) з коливаннями, близькими до прямолінійних (ГІСЛ, ГІСТ).
Продуктивність інерційних грохотів може бути розрахована за спрощеними формулами: Q = q F, т/год, або
Q = qо δ F, т/год, де q — питома продуктивність грохота, т/годּм2; qo — питома об'ємна продуктивність грохота, м3/год•м2; δ — насипна густина вихідного матеріалу, т/м3; F — площа сита грохота, м2.
Питома продуктивність визначається за даними табл. 1.8 або табл. 4.2 залежно від вихідного матеріалу і розміру отворів сит грохота.
Дугові і конічні грохоти застосовують для мокрого грохочення дрібного і тонкого матеріалу, для зневоднення і знешламлювання, для відділення кондиційної суспензії від продуктів збагачення у важкосередовищних гідроциклонах, для рівномірного розділення матеріалу за шириною решета відсаджувальної машини при одночасному знешламлюванні.
Об'ємна продуктивність грохотів, які працюють під тиском, визначається за формулою: Q = 160 Fжv, м3/год, де Fж — площа живого перетину сита (коефіцієнт живого перетину щілинних сит дорівнює 0,3 — 0,4), м2; v — швидкість пульпи на вході в апарат (v = 3 — 8 м/c).
Див. також
Література
- Смирнов В. О., Білецький В. С. Підготовчі процеси збагачення корисних копалин. [навчальний посібник]. — Донецьк: Східний видавничий дім, Донецьке відділення НТШ, 2012. — 284 с.
- Мала гірнича енциклопедія : у 3 т. / за ред. В. С. Білецького. — Д. : Східний видавничий дім, 2013. — Т. 3 : С — Я. — 644 с.
- Білецький В. С., Смирнов В. О. Технологія збагачення корисних копалин. — Донецьк: Східний видавничий дім. 2000.