Лазерне різання
Ла́зерне рі́зання (англ. laser cutting) — технологія термічного різання й розкроювання матеріалів, при якій як джерело енергії використовується лазер високої потужності. Сфокусований лазерний промінь, керований системою числового програмного керування забезпечує високу концентрацію енергії й дозволяє розтинати практично будь-які матеріали незалежно від їх теплофізичних властивостей. Випромінювання, з енергетичними параметрами які достатні для використання лазерів при технологічних процесах розрізання (розкроювання), має діапазон довжини хвиль від 0,4 до 10,6мкм. Зокрема, для різання різних матеріалів найбільший ефект дає довжина хвилі 10,6 мкм, яка генерується газовими СО2-лазерами з активним середовищем суміші вуглецевого газу з азотом і гелієм. Випромінювання з цією довжиною хвилі добре поглинається більшістю неметалічних матеріалів і у дещо меншій мірі металевими сплавами. Матеріали з великим коефіцієнтом відбивання (мідь, алюміній) гірше піддаються лазерному різанню.
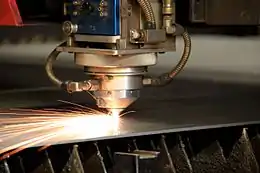
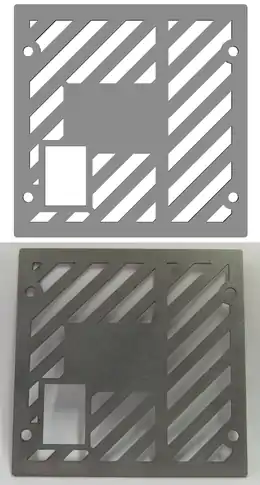
Загальні принципи
У процесі різання, під впливом лазерного променя матеріал у зоні розрізу плавиться, займається, випаровується та виноситься струменем газу, завдяки чому такий процес отримав назву «газолазерне різання». При використанні такої технології можна отримати вузькі прорізи з мінімальною зоною термічного впливу. Лазерне різання відрізняється відсутністю механічного впливу на матеріал оброблення завдяки чому при його використанні деформації, що виникають як у процесі різання, так і залишкові після повного остигання є мінімальними. Тому лазерне різання, навіть легкодеформованих й нежорстких заготовок та деталей, можна проводити з високим ступенем точності. Завдяки великій потужності лазерного випромінювання забезпечується висока продуктивність процесу у поєднанні з високою якістю поверхонь різання. Легке й порівняно просте керування переміщенням джерела лазерного випромінювання дозволяє проводити лазерне різання уздовж складного контуру плоских та об'ємних деталей (заготовок) за високого ступеня автоматизації процесу.
Матеріали обробки
Лазерне різання може застосовуватись до більшості видів сталі (маловуглецеві, низько- та високолеговані) у будь-якому стані у тому числі з покриттям, титану та його сплавів, цирконію, ніобію, танталу, нікелю і сплавів цих та інших кольорових металів. Зазвичай розрізають листи таких товщин:
- Сталь від 0,2 мм до 20 мм
- Неіржавна сталь від 0,2 мм до 50 мм
- Алюмінієві сплави від 0,2 мм до 20 мм
- Латунь від 0,2 мм до 12 мм
- Мідь від 0,2 мм до 15 мм
Для різних матеріалів застосовують різні типи лазерів.
Найкраще обробляються метали з низькою теплопровідністю, так як в них енергія лазера концентрується у меншому об'ємі металу, і навпаки, при лазерному різанні металів з високою теплопровідністю може утворюватись ґрат.
Також, обробці піддаються і неметали, такі як деревина, пластмаси, шкіра, гума, натуральні та синтетичні тканини. Крім того можливе різання неорганічних матеріалів: кераміки, кварцу, порцеляни, скла, азбесту, графіту, тощо.
Різновиди процесів
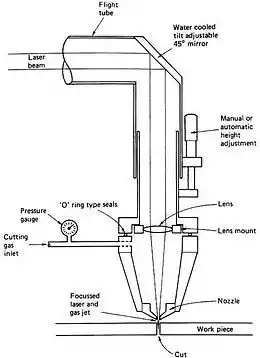
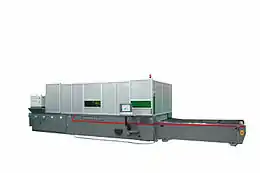
Для лазерного різання металів застосовують технологічні установки на основі твердотільних, волоконних лазерів та вуглекислотних лазерів, що можуть працювати як в безперервному, так і в імпульсно-періодичному режимах випромінювання. Промислове застосування газолазерного різання постійно зростає, хоча цей процес не може повністю замінити традиційні способи розділення металевих заготовок. У порівнянні з іншим устаткуванням для різання на виробництві вартість лазерного обладнання для різання є досить високою, хоча й намітилася тенденція до її зниження. У зв'язку з цим процес лазерного різання стає ефективним лише за умови обґрунтованого вибору області застосування, коли використання традиційних способів є трудомістким чи взагалі неможливим.
При різанні в імпульсному режимі безперервний розріз отримується в результаті послідовного накладення отворів один за одним. Імпульсний характер обробки забезпечує мінімальну глибину прогрівання матеріалу. Лазерні установки різних типів дозволяють вести обробку за наступних режимів: енергія випромінювання 0,1…1 мДж, тривалість імпульсу 0,01…100 мкс, густина потоку випромінювання досягає 100 МВт/см², частота імпульсів 100…5000 імп/с.
Лазери безперервної дії на вуглекислому газі потужністю від декількох сотень Вт до декількох кВт застосовують для газолазерного різання, при якому в зону дії лазерного променя подається струмінь газу. Газ вибирають залежно від виду оброблюваного матеріалу. При різанні дерева, фанери, пластиків, паперу, картону, текстильних матеріалів в зону обробки подається повітря або інертний газ, які охолоджують краї розрізу і перешкоджають згоранню матеріалу і розширенню розрізу. При різанні більшості металів, скла, кераміки струмінь газу видуває із зони дії променя розплавлений матеріал, що дозволяє отримувати поверхні з малою шорсткістю і забезпечує високу точність різання. При різанні маловуглецевих чи легованих сталей та титану в зону нагрівання подається струмінь кисню. В результаті екзотермічної реакції окиснення металу виділяється додаткове тепло, що дозволяє значно підвищити швидкість різання. Характерні режими газолазерного різання: потужність випромінювання 300…3000 Вт (для високопродуктивних установок – до 6 кВт), густина потоку випромінювання в зоні обробки від 100 до 106 кВт/см², ширина різу 0,3…1 мм товщина матеріалу, що розрізається, до 10 мм; швидкість різання залежить від товщини і властивостей оброблюваного матеріалу і може бути від 0,5 до 10 м/хв, для тонких матеріалів (папір, тканина) до 50 м/хв і більше.
Лазери на вуглекислому газі застосовують для різання крихких матеріалів (скло, кераміка) методом керованого термічного розколювання. При локальному нагріві матеріалу по траєкторії руху променя створюється термічне напруження, що перевищує границю міцності матеріалу. Тріщина, що виникає, розвивається услід за променем, траєкторія якого може мати складну форму. Швидкість різання досягає декількох м/хв. Кероване термічне розколювання застосовується при різанні скляних трубок у виробництві електровакуумних приладів, керамічних підкладок інтегральних схем, для різання листового та фасонного скла.
Енергоспоживання та охолодження при роботі
Ефективність промислових лазерів може варіюватися від 5 % до 15 %. Енергоспоживання та ефективність будуть залежати від вихідної потужності лазера, його робочих параметрів і того, наскільки добре лазер підходить для конкретної роботи. При визначенні доцільності використання того чи іншого типу лазера враховується як вартість лазера в сукупності з обладнанням, що його обслуговує, так і вартість утримання та обслуговування лазера. У 2010-х роках експлуатаційні витрати оптоволоконного лазера становили близько половини від експлуатаційних витрат вуглекислотного лазера.
Лазер і його оптика (включаючи фокусуючі лінзи) потребують охолодження. Залежно від розмірів і конфігурації установки, надлишок тепла може бути відведено теплоносієм або повітряним обдуванням. Вода, що часто застосовується як теплоносій, зазвичай циркулює через теплообмінний апарат або холодильну установку.
Величина потужності, що споживається для різання, залежить від типу матеріалу обробки, його товщини, середовища обробки, швидкості обробки
Переваги
Лазерне різання має низку очевидних переваг перед багатьма іншими способами розрізування та розкрою а саме:
- мала ширина різу і невелика глибина зони термічного впливу;
- відсутність механічного контакту дозволяє обробляти крихкі і деформівні матеріали;
- обробці легко піддаються матеріали з твердих сплавів;
- можливим є високошвидкісне різання тонколистової сталі, що збільшує перспективи використання у крупносерійному виробництві;
- відсутність шкідливих відходів при різанні склопластиків;
- висока ефективність у дрібносерійному виробництві (при випуску невеликих партій продукції доцільніше провести лазерне розкроювання матеріалу, ніж виготовляти для цього дорогі прес-форми або форми для лиття);
- простота автоматизації процесу: для автоматичного розкрою матеріалу досить підготувати файл малюнка в будь-якій креслярської програмі і перенести файл на комп'ютер установки, яка забезпечить мінімальні похибки;
- оплавлення країв розрізу синтетичних текстильних матеріалів запобігає їх розпусканню
Лазерна порізка металу застосовується практично у всіх галузях промисловості, завдяки відсутності подальшої обробки і високої продуктивності даного методу. Вироби, виготовлені за допомогою лазерного розкрою, відрізняє висока якість контуру оброблення та економічність виробництва. При лазерній обробці однаково вигідно виробляти як великі партії так і дослідні експериментальні зразки. Довільний контур обробки дозволяє виробляти широку номенклатуру виробів на одному верстаті.
Джерела
- Корж В. М. Газотермічна обробка матеріалів:Навчальний посібник. — К. : Екотехнологія, 2005. — 195 с. — ISBN 966-8409-07-8.
- Черненко В. С., Кіндрачук М. В., Дудка О. І. Променеві методи обробки: Навч. посібник. — К. : Кондор, 2004. — 166 с. — ISBN 966-798-270-X.
- Коваленко В. С. Прогрессивные методы лазерной обработки материалов. — К. : Вища школа, 1985. — 88 с.
- Астапчик С. А., Голубев В. С., Маклаков А. Г. Лазерные технологии в машиностроении и металлообработке. — Минск : Беларуская навука, 2008. — 251 с. — ISBN 978-985-08-0920-9.
- Colin E. Webb, Julian D.C. Jones. Handbook Of Laser Technology And Applications (Справочник по лазерным технологиям и их применению) book 1. IOP. ISBN 0-7503-0960-1.
- Colin E. Webb, Julian D.C. Jones. Handbook Of Laser Technology And Applications (Справочник по лазерным технологиям и их применению) book 2. IOP. ISBN 0-7503-0963-6.
- Steen, Wlliam M. (1998). Laser Material Processing (вид. 2nd edition). Great Britain: Springer-Verlag. ISBN 3-540-76174-8.
- Малоотходные процессы резки лучом лазера / В.С. Коваленко, В.В. Романенко, Л. М. Олещук.— К.: Технiкa, 1987.—112 с, ил.— Библиогр.: с 109—111