Млини барабанні
Млини́ бараба́нні (рос. мельницы барабанные (гравитационные), англ. tumbling mills (gravity mills), нім. Gravitationstrommelmühlen f pl) — машини для подрібнення корисних копалин. Конструктивно являють собою циліндр, що обертається (барабан), завантажений молольними тілами. Торці барабана закриті кришками (завантажувальною і розвантажувальною). При обертанні подрібнюючі тіла під впливом відцентрової сили, а також тертя між собою і футеровкою барабана підіймаються на певну висоту, падають, розбиваючи і стираючи матеріал, що знаходиться в барабанних млинах. Подрібнюючі тіла: сталеві кулі (кульові барабанні млини), стержні (стержневі барабанні млини), короткі трубки — цильпепси, а при самоподрібненні — шматки руди.
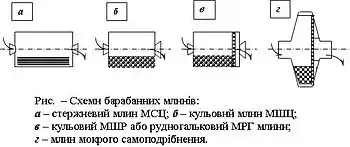
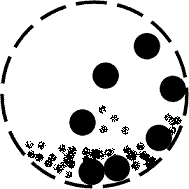
Для завантаження млинів застосовуються равликові, барабанні і комбіновані живильники.
Класифікація
Типи барабанних млинів відрізняються формою барабана, способами розвантаження, середовищем подрібнення тощо.
Конструкція барабанів визначається співвідношенням їх діаметрів (D) і довжин (L); у млинів первинного самоподрібнення типів «Каскад» і «Аерофол» 2:1<D:L<4:1 (при D до 10-11 м) і D:L<1:2 (при D до 5-6 м); в кульових, рудногалькових 1:2<D:L<1:1 (при D до 5-5,5 м); у стержневих D:L<0,8 (при D до 3,6-4,5 м); у трубних D:L<0,2.
За способом розвантаження при мокрому подрібненні виділяють барабанні млини зливного типу, з розвантаженням через ґрати, з периферійним розвантаженням. При сухому подрібненні — з розвантаженням через центральну цапфу або через вікна в розвантажувальному кінці барабана.
Велика кількість подрібнювальних машин різних конструкцій належить до відцентрових барабанних млинів.
Характерна особливість розвитку барабанних млинів — створення великогабаритного високопродуктивного обладнання. Барабанні млини найпоширеніші в промисловості. Вони порівняно прості щодо конструкції, зручні і надійні в експлуатації, забезпечують високий ступінь подрібнення і легко автоматизуються. Недоліки: низький к.к.д. — (0,01-0,05), високі витрати електроенергії 10-40 кВт•год/т матеріалу, значний знос мелючих тіл і футеровки — 1-3 кг/т матеріалу, велика металоємність і високий шум при роботі.
Кульові млини
Див. також Кульове подрібнення, млини кульові з центральним розвантаженням, млини кульові з розвантаженням через решітки.
Кульові млини зі сталевими, чавунними, кременевими, порцеляновими кулями діаметром 30-150 мм застосовують для тонкого (до 40-100 мкм) подрібнення матеріалів з початковою крупністю до 25-30 мм сухим і мокрим способами. Для однорідності помелу використовують суміш куль різного діаметра. Об'єм заповнення барабана кулями звичайно не перевищує 45 %.
Кульові млини з центральним розвантаженням (МШЦ) застосовують для одержання тонкоподрібненого продукту з максимальною крупністю до 0,2 мм. Подрібнений продукт кульових млинів виходить рівномірним по крупності. Щоб уникнути переподрібнення матеріалу, кульові млини звичайно використовують у замкненому циклі з гідроциклонами. Оптимальним живленням для млинів цього типу є подрібнений продукт стержневих млинів крупністю до 6 мм або інший аналогічний матеріал. Кульові млини з розвантаженням через решітки (МШР) застосовують для одержання продукту з максимальною крупністю частинок до 0,4 мм. Оптимальні результати подрібнення у млинах цього типу одержують при живленні їх продуктом дробарок дрібного дроблення крупністю до 10 мм. У млин можна завантажувати і більш крупний матеріал (до 40 мм) при відповідному зниженні питомої продуктивності. Млини типу МШР мають більшу питому продуктивність у порівнянні з млинами типу МШЦ, але складніші у конструктивному відношенні. Млини типу МШР застосовують у схемах переробки середньовкраплених руд і в першій стадії збагачення руд з агрегатним вкрапленням, які переробляють за багатостадійними схемами.
Стержневі млини
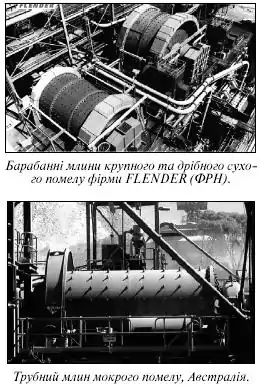
Стержневі млини (зі сталевими стержнями діаметром 40-125 мм і довжиною, сумірною з довжиною барабана, або короткими циліндрами — цильпебсами діаметром до 25 мм і довжиною до 40 мм) застосовують для грубого сухого або мокрого помелу (до 500–1000 мкм) сировини. Конструктивною відмінністю стержневих М. від кульових є збільшений діаметр розвантажувального отвору, що дозволяє знизити рівень пульпи при зливі, збільшити швидкість проходження матеріалу і знизити його переподрібнення. Об'єм заповнення барабана стержнями до 35 %. Використовуються в основному в комплексах збагачення тонковкраплених руд. Стержневі млини з центральним розвантаженням (МСЦ) застосовують для мокрого грубого подрібнення різних матеріалів крупністю до 20 мм (іноді до 40 мм) з одержанням подрібненого продукту з максимальною крупністю 0,5-6 мм. Подрібнений продукт виходить одноманітним і рівномірним за крупністю і являє собою ідеальне живлення для кульових млинів. Стержневі млини звичайно працюють у першій стадії багатостадійних схем збагачення при подачі подрібненого продукту першої стадії в цикл збагачення (наприклад у схемах збагачення магнетитових, олов'яних, вольфрамітових руд). Стержневі млини застосовують також у першій стадії подрібнення поліметалічних руд.
Трубні млини застосовують для отримання найбільшого ступеня подрібнення в одному апараті при роботі у відкритому циклі. Для підвищення ефективності роботи з можливістю подрібнення в декілька стадій трубні М. виконують багатокамерними. Камери розділяють між собою ґратчастими перегородками для пропуску матеріалу і заповнюють тілами (кулями, цильпебсами) зменшуваного розміру.
Стержневі млини з центральним розвантаженням (МСЦ) встановлюють у першій стадії подрібнення. Вони застосовуються для дрібного дроблення перед кульовими млинами, а також для підготовки дрібновкраплених руд перед гравітаційним або магнітним збагаченням (для подрібнення матеріалу до 0,5 — 3 мм). Стержневі млини з центральним розвантаженням (МСЦ) застосовують для мокрого грубого подрібнення різних матеріалів крупністю до 20 мм (іноді до 40 мм) з одержанням подрібненого продукту з максимальною крупністю 0,5 – 6 мм. Подрібнений продукт виходить одноманітним і рівномірним за крупністю і являє собою ідеальне живлення для кульових млинів. Стержневі млини звичайно працюють у першій стадії багатостадійних схем збагачення при направленні подрібненого продукту першої стадії в цикл збагачення (наприклад, у схемах збагачення магнетитових, олов’яних, вольфрамітових руд). Стержневі млини застосовують також у першій стадії подрібнення поліметалічних руд.
Млини самоподрібнення
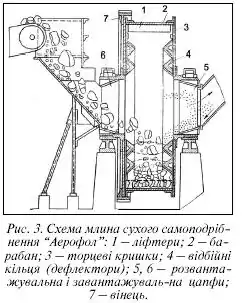
Див. також Млини самоподрібнення
Млини самоподрібнення мають діаметр до 10-12 м і привод потужністю до 7 кВт і вище. Такі М. здатні приймати великі шматки руд до 600–900 мм і видавати готовий продукт крупністю 0,074 мм до 60-80 %. М. самоподрібнення застосовуються переважно в Канаді, Фінляндії, ПАР для підготовки до збагачення азбестових, золотих, уранових, залізних і мідних руд тощо. Млини рудного самоподрібнення і рудногалькові (ММС і МРГ) використовують при переробці залізних, золотовмісних, мідномолібденових, алмазовмісних і інших руд. Крупні шматки виконують роль подрібнювального середовища, а дрібні — роль матеріалу, який подрібнюється. Розрізняють: рудне самоподрібнення, рудне напівсамоподрібнення, рудногалькове самоподрібнення. Рудне самоподрібнення — дроблена руда крупністю 0 — 300 мм після крупного дроблення надходить у млини сухого або мокрого самоподрібнення, що мають короткі барабани великого діаметра (діаметр барабана — до 12 м, співвідношення D/L = 3). Подрібнена руда має крупність 0 — 6 мм. Рудне напівсамоподрібнення відрізняється добавкою 5 % сталевих куль діаметром 100–125 мм у млин самоподрібнення. Рудногалькове самоподрібнення — руда крупністю 0 — 6 мм після рудного само-, напівсамоподрібнення або подрібнення у стержневому млині подрібнюється у рудногалькових млинах типу МРГ. Рудна галька (40 — 100, 30 — 75 мм), що використовується як подрібнювальне середовище, відбирається після другої стадії дроблення або виділяється при рудному самоподрібненні.
Відкритий і замкнений цикли помелу
У млинах відкритого циклу матеріал проходить через робочий простір однократно без класифікації. Замкнений цикл передбачає класифікацію матеріалу в спіральних класифікаторах, гідроциклонах або повітряних сепараторах, повернення некондиційного пром. продукту в млинах для доподрібнення. Робота млинів за замкненим циклом раціональніша, продуктивна і економічна.
Млини сухого помелу з одночасним підсушуванням застосовуються при пилоприготуванні вугільного палива на теплових електростанціях, неметалічних викопних (алуніту в алюмінієвій пром-сті, вапняку на агломерац. фабриках, шамоту і ін.), а також при самоподрібненні неміцних матеріалів. Мокрим способом подрібнюють більшість корисних копалин для їх збагачення, а також матеріали з високою природною вологістю, м'які і ті, що легко диспергуються у воді (крейда, вапняк, мергель, клінкер, а також гірничохім. сировина).
Подрібнююче середовище барабанних млинів
У залежності від матеріалу подрібнювальних тіл розрізняють металеве і неметалеве подрібнююче середовище, а у залежності від форми металевих тіл кульові, стержневі і цильпебсні млини.
Під терміном «первинне навантаження подрібнювальних тіл» розуміється їх спільна маса у барабані млина, а терміном «довантаження» позначається безперервна або періодична добавка подрібнювальних тіл у млин для компенсації їхнього зносу.
Сталеві кулі діаметром від 15 до 125 мм виготовляють прокатуванням, куванням або штампуванням із сталі з таким складом: 0,7 – 1,05 % С; 0,17 – 0,37 % Si; 0,25 – 1,65 % Cr; 0,25 – 0,3 % Ni; 0,02 – 0,045 % S; 0,02 – 0,45 % P; 0,2 – 1,2 % Mn, інше – Fe. Кулі повинні бути загартовані і мати твердість від 300 НВ (для куль діаметром 125 мм) до 400 НВ (для куль діаметром 80 мм і менше). На поверхні куль не повинно бути тріщин, пухирів, плівок шлакових включень.
Стержні виготовляють діаметром від 40 до 125 мм прокатуванням із зносостійких сталей 50Г, 60Г, 65Г, С55. Стержні не повинні скручуватись і розламуватись на короткі шматки після зносу до технологічно допустимої межі (приблизно 30 – 50 мм).
У процесі роботи млинів на збагачувальних фабриках відбувається знос куль, стержнів, цильпепсів і футеровки млина у результаті тертя при ковзанні і перекочуванні подрібнювальних тіл у середовищі абразивного матеріалу, при ударах подрібнювальних тіл між собою і футеровкою. Інтенсивність зносу залежить від: властивостей сталі, з якої виготовлені кулі, стержні, цильпепси, футеровки; розмірів подрібнювальних тіл; абразивності, крупності і міцності матеріалу, що подрібнюється; способу подрібнення; агресивності середовища (кисле, лужне); профілю футеровки; швидкісного режиму роботи млина; розміру барабана млина; схеми подрібнення та ін.
При сухому подрібненні знос сталевих подрібнювальних тіл відбувається у основному за рахунок абразивної дії, тобто мікрорізання, мікродряпання металу частинками матеріалу, що подрібнюється, у вигляді стружки. При мокрому подрібненні абразивний знос доповнюється корозійним зносом: при подрібненні у агресивному середовищі корозійна складова зносу сталевих подрібнювальних тіл може складати від 10 до 60 % від загального зносу.
Знос подрібнювальних тіл на збагачувальних фабриках оцінюють їх питомою витратою на 1 т переробленої руди. Так питомі витрати куль складають 1,2 – 2,2 кг/т, стержнів – 0,4 – 0,5 кг/т, футеровки – 0,1 – 0,2 кг/т. Але такий показник, як витрати сталі на 1 т подрібненої руди, не є стабільним, тому що він пов’язаний з продуктивністю млина, яка, у свою чергу, залежить від властивостей руди. Більш надійним показником є витрата подрібнювальних тіл, віднесена до одиниці корисної енергії, витраченої на подрібнення. У цьому випадку середня витрата сталевих куль віднесена до 1 кВт•год корисної енергії складає 0,09 кг/кВт•год, стержнів – 0,12 кг/кВт•год.
Для компенсації зносу подрібнювальних тіл застосовується два способи довантаження: – регулярне – довантаження найбільш крупними подрібнюючими тілами (кулями, стержнями, рудною галькою) одного розміру; – раціонне – довантаження подрібнюючими тілами різних розмірів, при дотриманні визначеного співвідношення між масами тіл різних розмірів. Неметалеве подрібнююче середовище, що використається при рудногальковому самоподрібненні, довантажується безперервно або через малі проміжки часу. Металеве подрібнююче середовище звичайно довантажується періодично від трьох разів на добу до одного разу у три – п’ять діб. Розмір подрібнювальних тіл, що довантажуються у млин, режим їх довантаження і склад визначаються у результаті технологічних досліджень. Найбільший розмір тіл у довантаженні, при яких досягається найбільша продуктивність по новоутвореному контрольному класу крупності називають раціональним (оптимальним).
Металевий скрап і кулі неефективного розміру або неправильної форми, за своєю руйнуючою дією значно менш ефективні ніж великі кулі правильної форми, і тому повинні безперервно або періодично видалятись з млина.
Футеровка барабанних млинів
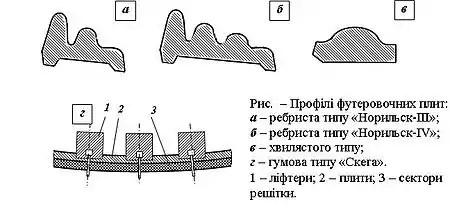
Конструкція футерувальних плит барабана повинна допускати легку їхню установку і заміну. Змінні броньові плити виготовляються із зносостійких матеріалів (легованого чавуну, марганцевистої і хромистої сталі). Товщина футерувальних плит приймається від 50 мм (для млинів малих розмірів) до 150 мм (для млинів великих розмірів). Від товщини і профілю футерувальних плит залежить характер руху подрібнювальних тіл, (висота підйому і коефіцієнт ковзання по футеровці), робочий об’єм барабана млина, знос футеровки, продуктивність млина, витрата електроенергії і подрібнювальних тіл.
Для кульових млинів першої стадії подрібнення, у які завантажують кулі діаметром 100 – 125 мм, кращим є профіль ребристої футеровки типу «Норильськ-ІІІ» (рис. а). Ця футеровка забезпечує надійне зчеплення з кулями і підйом їх на велику висоту, відсутність ковзання куль, рівномірний і більш повільний знос плит, зниження питомої витрати металу і електроенергії, підвищення продуктивності млина.
Для кульових млинів другої стадії подрібнення кращим є профіль ребристої футеровки типу «Норильськ-ІV» (рис.б). Для стержневих млинів частіше застосовують футеровку хвилястого типу (рис. в), але вона не рекомендується для кульових млинів внаслідок значного ковзання куль.
Для кульових млинів другої стадії подрібнення також використовуються гумові футеровки (рис. г). Основним елементами гумової футеровки є ліфтери 1, плити 2 і сектори решітки 3. На торцеві кришки барабана млина радіально укладають плити товщиною 60 мм і затискують ліфтерами. Товщина гумової футеровки барабана складає від 50 до 80 мм, гумові сектори решітки мають товщину 54 мм. Футерувальні гумові плити укладають поздовж барабана і також затискують ліфтерами.
Оскільки гумова футеровка тонше сталевої, робочий об’єм млина збільшується на 5 – 6 %. Термін служби гумової футеровки на 15 – 20 % більше ніж сталевої. Питома витрата куль у млині з гумовою футеровкою менша, а продуктивність вища, ніж у млинів із стальною футеровкою. Інші переваги млинів з гумовою футеровкою: менша трудомісткість монтажу, більша герметичність, менший рівень шуму. Футеровка цапф гладенька або спіральна. Напрям спіралі завантажувальної цапфи повинен сприяти просуванню вихідного матеріалу у млин, а розвантажувальної цапфи – поверненню у млин куль і крупного матеріалу.
Режими руху подрібнювальних тіл у млинах
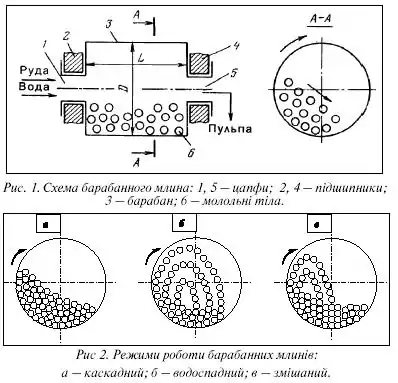
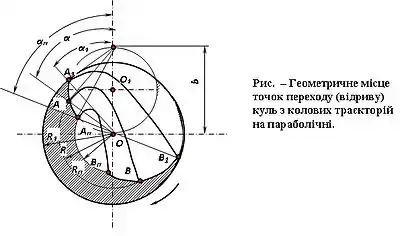
Див. також: Режими руху подрібнювальних тіл у млинах
Залежно від частоти обертання барабана млина розрізняють такі основні швидкісні режими руху подрібнювальних тіл: каскадний, водоспадний і змішаний (рис. 2). Критичною називається така частота обертання барабана, при якій подрібнювальні тіла притискаються відцентровою силою до внутрішньої поверхні барабана і обертаються разом з барабаном, не відриваючись. Каскадний режим (рис. 2а) здійснюється при малій частоті обертання барабана (0,5-0,6 критичної) за допомогою перекочування подрібнювальних тіл без польоту. При сталому каскадному режимі подрібнювальне середовище повертається на деякий кут у бік обертання і залишається в такому положенні.
Подрібнювальні тіла безупинно циркулюють усередині барабана, вони піднімаються по кругових траєкторіях на деяку висоту і потім скочуються «каскадом» рівнобіжними шарами вниз. Подрібнення матеріалу відбувається роздавлюванням і стиранням. Каскадний режим є найсприятливішим для стержневих млинів, тому що при водоспадному і змішаному режимі вільний політ стержнів може привести до їх перекосів і аварійної зупинки млина. Для кульових млинів каскадний режим застосовується при сухому подрібненні (при виробництві цементу, приготуванні пиловугільного палива тощо). При водоспадному режимі (рис. 2б) частота обертання барабана складає не менше 0,76-0,88 критичної. У цьому випадку основна маса подрібнювальних тіл піднімається по кругових траєкторіях на велику висоту і падає «водоспадом» по параболічних траєкторіях. Подрібнення руди відбувається г. ч. у результаті ударів подрібнювальних тіл і частково стиранням і роздавлюванням. Водоспадний режим застосовується при подрібненні більш крупного матеріалу (у першій стадії). Змішаний режим (рис. 2в) подрібнення характеризується поступовим переходом від чисто каскадного до чисто водоспадного режиму. Змішаний режим має місце при подрібненні руд у кульових млинах.
Тип застосовуваного млина визначається крупністю вихідного матеріалу, необхідним розміром подрібненого продукту, шламоутворенням матеріалу при подрібненні, а також вимогами до продуктів подрібнення за вологістю (сухі чи мокрі продукти).
Продуктивність барабанних млинів
Продуктивність барабанних млинів вимірюється кількістю тонн подрібненого вихідного матеріалу (т/год., т/добу); кількістю новоутворених поверхонь-тонн за одиницю часу; кількістю тонн новоутвореного розрахункового класу крупності (звичайно – 0, 074 мм) за одиницю часу.
Продуктивність млинів визначається багатьма факторами, які розділяють на три групи:
– технологічні фактори, які залежать від властивостей матеріалу – крупності вихідного матеріалу і подрібненого продукту, подрібнюваності руди;
– конструктивні фактори, які залежать від конструкції млина, його розміру, форми футеровки;
– експлуатаційні фактори, які визначаються умовами роботи млина – відкритий або замкнений цикл, ефективність роботи класифікаційного апарата, заповнення млина подрібнюючим середовищем, характеристика крупності, форма, густина і твердість подрібнювальних тіл, розрідженість пульпи, число обертів млина.
Регулюванню при експлуатації піддаються тільки фактори третьої групи, а також крупність вихідної руди і продукту подрібнення.
Між продуктивністю млина і подрібнюваністю матеріалу, його крупністю і крупністю подрібненого продукту існує прямо пропорційна залежність. Практикою встановлено, що оптимальна крупність живлення стержневих млинів – 15 – 20 мм, а кульових – 10 – 15 мм (така крупність може бути отримана після тристадіального дроблення). Для млинів самоподрібнення крупність живлення – 300 – 500 мм (така крупність може бути отримана після одностадіального дроблення). Чим менше крупність вихідного матеріалу і чим крупніше подрібнений продукт, тим вище продуктивність млина.
Продуктивність млина пропорційна витратам енергії на подрібнення, а витрати енергії пов’язані з ступенем заповнення млина подрібнюючим середовищем. З ростом ступеня заповнення φ млина подрібнюючим середовищем зростає витрата енергії на подрібнення і досягає максимуму при ступені заповнення φ = 50 %. Відповідно зростає й продуктивність млина.
З підвищенням відносної частоти обертання спостерігається підвищення споживаної питомої потужності. Одночасно продуктивність і вихід класу – 0,074 мм в розрахунку на 1 кВт•год зростають приблизно так само, як і частота. Однак це справедливо до деякої межі (для млинів типу «Аерофол» до ψ = 0,95; для млинів типу «Каскад» до ψ = 0,85). Якщо у живленні млина самоподрібнення міститься багато дріб’язку, його продуктивність знижується, тому що немає достатньої кількості крупних грудок, які могли би подрібнити грудки середньої величини, руда подрібнюється дуже повільно і, головним чином, стиранням.
Розрідження пульпи у млині визначає масу або об’єм твердого мате-ріалу, який знаходиться у ньому у кожний даний момент, а також ефекти-вність дії подрібнювальних тіл. Загальний об’єм пульпи у млині приблиз-но постійний, тому зі збільшенням вмісту у пульпі води вміст твердого зменшується, і навпаки. При меншому вмісті води густина пульпи збіль-шується і, отже, подрібнювальні тіла при русі у більш густому середовищі будуть мати меншу силу удару.
Вміст води у пульпі визначає її текучість і здатність проходження через млин. При вмісті води близько 20 % матеріал достатньо вільно про-ходить через млин. Чим більше густина пульпи, тим більше крупних час-тинок досягає розвантажувального кінця млина. У млинах з центральним розвантаженням цей крупний матеріал іде у розвантаження і вміст крупно-го класу у продукті подрібнення збільшується. У млинах з решіткою густа пульпа, яка містить крупні частинки затримується решіткою і збільшення вмісту крупного класу у розвантаженні млина не спостерігається. При ве-ликих розрідженнях пульпи матеріал швидше проходить млин з решіткою, що приводить до укрупнення продукту подрібнення. У млинах з центральним розвантаженням великі розрідження, навпаки, спричиняють збільшення вмісту дрібних класів у подрібненому продукті.
Продуктивність млина тим вище, чим вище ефективність класифікації. Низька ефективність класифікації особливо негативно впливає на ро-боту млина при малих циркуляційних навантаженнях. Підвищення ефек-тивності класифікації визначає зменшення кількості переподрібненого матеріалу. Збільшення швидкості проходження матеріалу через млин, що спостерігається при зростанні циркуляційного навантаження, сприяє під-вищенню ефективності роботи подрібнюючого середовища, зменшенню ступеня переподрібнення і підвищенню продуктивності млина.
Вплив конструкції млинів і форми футеровки на їхню продуктивність встановлений на основі практичних даних. Млини, які працюють з низьким рівнем пульпи, мають продуктивність дещо більшу, ніж млини з високим рівнем пульпи. Так, продуктивність млинів з решіткою приблизно на 15 % вище продуктивності млинів з центральним розвантаженням. Цей факт пояснюється тим, що при низькому рівні пульпи елементи подрібнюючого середовища діють більш ефективно. Продуктивність млинів з гладкою футеровкою менше, ніж млинів з ребристою футеровкою.
Похідні конструкції
- Планетарні млини являють собою агрегат з декількох барабанних млинів, змонтованих на вертикальному водилі.
- Млин інтенсифікованого помелу - барабанний млин, усередині якого нерухомо закріплений робочий орган, який називають інтенсифікатором.
Експлуатація барабанних млинів
Головними факторами, які визначають роботу установки для подрібнення є: водний режим, рівномірність подачі корисної копалини у млин, фізичні властивості корисної копалини, подрібнювальне навантаження і механічні параметри апаратури.
Водний режим а агрегаті визначає технологічні параметри подрібнення: вміст твердого в зливах млина і класифікатора. Вологість пульпи в млині коливається в широких межах – від 17 до 60 %. Вважають, що для одержання максимальної продуктивності млина необхідно, щоб вміст води при подрібненні крупного матеріалу (від 13 мм і більше) складав 20 – 35 %, а при подрібненні більш дрібного матеріалу 30 – 50 %. В зливі млинів самоподрібнення підтримується вміст твердого в пульпі близько 70 – 75 %. В рудногалькових млинах вміст твердого в пульпі звичайно на 5 – 7 % менше, ніж в кульових. Кількість води, що додається в класифікатор або гідроциклон, залежить від необхідної густини зливу, яка визначає крупність твердого в зливі.
На процес подрібнення корисної копалини впливають крупність її грудок і подрібнюваність. На практиці ці властивості не залишаються постійними, а коливаються у досить широких межах.
Збільшення крупності корисної копалини, при незмінних інших факторах подрібнення, приводить до збільшення крупності матеріалу в зливах млина і класифікатора, збільшення циркуляційного навантаження і зниження густини зливу. Процес подрібнення у даному випадку регулюється зменшенням кількості корисної копалини і води, які подаються у млин. Зменшення крупності корисної копалини приводить до зворотних явищ і потребує регулювання шляхом протилежних дій.
Зміна міцності руди приводить до таких же явищ, що й зміна її крупності, тому у цьому випадку процес подрібнення регулюється аналогічно. Характер кульового і стержневого завантаження (ступінь його зносу), профіль футерувальних плит в значній мірі впливають на показники процесу подрібнення. Кульові млини заповнюються кульовим завантаженням на 40 – 50 % об’єму. При цьому в млинах з решіткою можна підтримувати більш високе заповнення кулями, ніж в млинах з центральним розвантаженням. Стержневе завантаження заповнює об’єм млина на 35 – 45 %.
Кулі і стержні виготовляють з високовуглецевої сталі, футеровку – з високомарганцевистої сталі. Питомі витрати куль на 1 т подрібнюваної корисної копалини складають від 0,5 – 1,5 кг/т при грубому подрібнені (перша стадія) до 0,3 – 0,6 кг/т при тонкому подрібнення (третя стадія). Питомі витрати стержнів складають 0,5 – 1,0 кг/т, а сталевої футеровки – 0,1 – 0,2 кг/т. Подрібнювальне навантаження періодично пересортовують з метою вилучення зношених куль і стержнів та довантажують нові.
Див. також
Література
- Мала гірнича енциклопедія : у 3 т. / за ред. В. С. Білецького. — Д. : Донбас, 2007. — Т. 2 : Л — Р. — 670 с. — ISBN 57740-0828-2.
- Смирнов В.О., Білецький В.С. Підготовчі процеси збагачення корисних копалин. [навчальний посібник]. – Донецьк: Східний видавничий дім, Донецьке відділення НТШ, 2012. – 284 с.