Ультразвукова дефектоскопія
Ультразвукова дефектоскопія — пошук дефектів у матеріалі виробів ультразвуковим методом, тобто шляхом випромінювання та прийняття ультразвукових коливань, і подальшого аналізу їх амплітуди, часу приходу, форми та ін за допомогою спеціального обладнання — ультразвукового дефектоскопа.
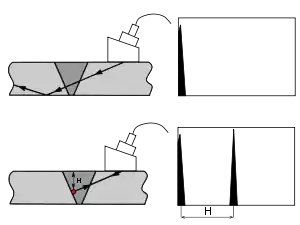
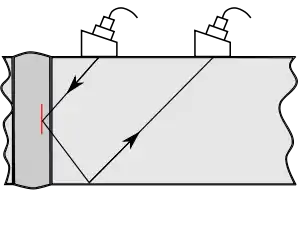
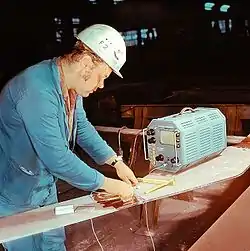
Принцип роботи
При ультразвуковій дефектоскопії кільцеві зварні з'єднання контролюють шляхом послідовного прозвучування їх по периметру з'єднання плавним переміщенням шукача - п'єзоперетворювача по поверхні труби.
Звукові хвилі не змінюють траєкторії руху в однорідному матеріалі. Відображення акустичних хвиль походить від розділу середовищ з різними питомими акустичними опорами. Чим більше розрізняються акустичні опору, тим більша частина звукових хвиль відіб'ється і повернеться до приймача при проходженні фронту хвилі через межу розділу.
Так як включення в металі часто містять повітря, що має на кілька порядків більше питомий акустичний опір, ніж сам метал, то за включення хвилі практично не проходять.
Розширенння акустичного дослідження визначається довжиною використовуваної звукової хвилі. Це обмеження накладається тим фактом, що при розмірі перешкоди менше чверті довжини хвилі, хвиля від нього практично не позначається. Це визначає використання високочастотних коливань — ультразвуку.
Випромінювання ультразвуку проводиться за допомогою резонатора, який перетворює електричні коливання в акустичні за допомогою зворотного п'єзоелектричного ефекту і вводить їх в досліджуваний матеріал. Відображені сигнали потрапивши на п'єзопластин через прямий п'єзоелектричний ефект перетворюються в електричні, які й реєструються вимірювальними схемами.
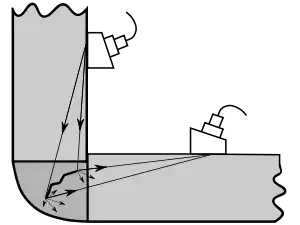
П'ять методів проведення дослідження[1]
- Луна-метод (луна-імпульсний метод) — найпоширеніший: резонатор генерує коливання (генератор) і він же приймає відбиті від дефектів сигнали (приймач)
- Тіньовий — використовуються два резонатора, які знаходяться по два боки від досліджуваної деталі на одній лінії. У цьому випадку один з резонаторів генерує коливання (генератор), а другий бере їх (приймач). Ознакою наявності дефекту буде значне зменшення амплітуди прийнятого сигналу, або його пропажа (дефект створює акустичну тінь).
- Дзеркально-тіньовий — використовується для контролю деталей з паралельними двома сторонами, розвиток тіньового методу: резонатор генерує коливання і приймає їх відображення від протилежної грані деталі, ознакою дефекту, як і при тіньовому методі буде вважатися пропажа відбитих коливань. Основна перевага цього методу на відміну від тіньового полягає в доступі до деталі з одного боку.
- Дзеркальний — використовуються два перетворювача з одного боку деталі: згенеровані коливання відбиваються від дефекту в бік приймача. На практиці використовується тільки для специфічних дефектів (це пов'язано зі складністю прогнозування відображення сигналів від дефектів) і тільки разом з іншими методами.
- Дельта-метод — різновид дзеркального методу — відрізняються механізмом відображення хвилі від дефекту і способом прийняття. На практиці не використовується.
Сучасні дефектоскопи використовують одночасно кілька методів у різних поєднаннях, формують вузький промінь акустичних хвиль і точно заміряють час, що минув від моменту випромінювання, до прийому луно-сигналу, що дозволяє досягти високого просторового дослідження та достовірності прийнятого рішення про дефектності досліджуваної деталі. Комп'ютеризовані системи з фазованими ґратами випромінювачів дозволяють отримати тривимірне зображення дефектів у металі.
Реконструкція (3D)
Представлення даних про внутрішню структуру виробів у вигляді зображень дозволяє визначити місцеположення, розміри й форму дефектів і відповідно оцінити їх реальну небезпеку. На основі зображень вирішуються питання походження дефектів, і може бути відкоригована технологія виготовлення, приймаються рішення про можливості ремонту або про можливості подальшої експлуатації виробів.
Множина сучасних дефектоскопів мають інтегровані засоби візуалізації, але лише даних безпосередньо сканування. Тому для власної постобробки даних контролю й наступної їх реконструкції у 3-вимірне зображення необхідне створення власного засобу візуалізації[2].
Переваги
Ультразвукове дослідження не руйнує і не пошкоджує зразок, що є його головною перевагою. Так само можна виділити високу швидкість і достовірність дослідження при низькій вартості і небезпеці для людини
Застосування
Застосовується для пошуку дефектів матеріалу (пори, різні включення, неоднорідна структура тощо) і контролю якості проведення робіт — зварювання, паяння, склейки та ін.
Ультразвук використовують для неруйнівного контролю бетонних блоків будівельних конструкцій, зварних швів магістральних трубопроводів конструкцій, зварних швів магістральних трубопроводів, наявності дефектів у рейках і інших областях контролю. Широко ультразвук застосовують в медицині для виявлення змін в організмі людини.
Див. також
- Дефектоскопія
- Ультразвуковий дефектоскоп
Література
- Шрайбер Д. С. Ультразвуковая дефектоскопия //М.: Металлургия. — 1965. — Т. 392. — С. 29.
- Гурвич А. К., Ермолов И. Н. Ультразвуковая дефектоскопия сварных швов — Киев: Техника, 1972, 460 с.
- Выборнов Б. И. Ультразвуковая дефектоскопия — М.: Металлургия, 1985.
- Щербинский В. Г., Пафос С. К., Гурвич А. К. Ультразвуковая дефектоскопия: вчера, сегодня, завтра //В мире неразрушающего контроля. — 2002. — №. 4. — С. 18.
- Ермолов И. Н. Достижения в теоретических вопросах ультразвуковой дефектоскопии, задачи и перспективы //Дефектоскопия. — 2004. — №. 10. — С. 13-48.
- Кретов Е. Ф. Ультразвуковая дефектоскопия в энергомашиностроении. — Изд.3-е, перераб.и доп. -Санкт-Петербург: СВЕН, 2011, 312с., ISBN 978-5-91161-014-2
- Марков А. А., Шпагин Д. А. Ультразвуковая дефектоскопия рельсов, — Изд. 2-е, исправл. и доп. — СПб.: Образование — Культура, 2013, 283с., ISBN 5-88857-104-0
- КОРОТИН А. И., ЛАЗАРЕВ А. Л., СВЯТКИНА Г. Н. - ПРИМЕНЕНИЕ УЛЬТРАЗВУКОВЫХ МЕТОДОВ КОНТРОЛЯ ДЛЯ ОЦЕНКИ КАЧЕСТВА СОЕДИНЕНИЙ МЕТАЛЛИЧЕСКИХ КОНСТРУКЦИЙ В СОВРЕМЕННЫХ УСЛОВИЯХ.
- С.В. Зыков - 3D-ВИЗУАЛИЗАЦИЯ В УЛЬТРАЗВУКОВОЙ ДЕФЕКТОСКОПИИ.