Блок циліндрів
Блок цилі́ндрів (англ. cylinder block) — група циліндрів поршневої машини, виготовлених в одному загальному виливку, який є основною деталлю дво- і більше циліндрового поршневого двигуна внутрішнього згоряння або поршневого компресора.
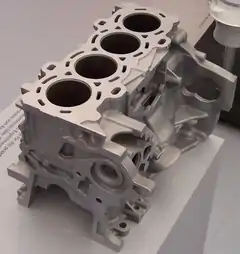
.jpg.webp)

.jpg.webp)
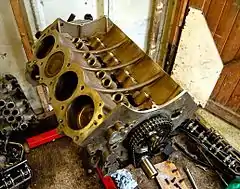
Конструктивні особливості
Будова та умови роботи
У нижній частині блока циліндрів розташовані опорні поверхні для встановлення колінчастого вала, у верхній частині блока, зазвичай, кріпиться головка блоку циліндрів. Нижня частина блока циліндрів є одночасно верхньою частиною картера. Крім того у нижній частині блока циліндрів двигуна розташовуються опорні поверхні розподільного вала механізму газорозподілу для конструкцій двигунів із нижнім його розташуванням (типи SV та OHV). Отже, блок циліндрів є базовою (корпусною деталлю) двигуна чи компресора, до якої так чи інакше кріпляться решта їх компонентів.
Самі циліндри у блоці циліндрів можуть бути як частиною виливка блока циліндрів, так і бути окремими змінними втулками («гільзами»), які можуть бути «мокрими» або «сухими» — в залежності від того, чи контують вони безпосередньо з охолоджувальною рідиною у сорочці охолодження двигуна. Окрім функції корпусної деталі, блок циліндрів має додаткові функції: є основною частиною системи змащення — по каналах у блоці циліндрів моторна олива під тиском подається до місць змащення, а у двигунах рідинного охолодження — і системи охолодження: охолоджувальна рідина циркулює порожнинами блока циліндрів, що утворюють сорочку охолодження.
Стінки внутрішньої порожнини циліндра слугують також напрямними поверхнями для поршнів при їх переміщеннях між крайніми положеннями. Тому довжина твірної циліндра зумовлюється величиною ходу поршня.
Зношування циліндрів автомобільних двигунів відбувається внаслідок комплексного впливу на стінки циліндра численних швидкоплинних фізичних і хімічних процесів, які за характером прояву поділяються на три основних види зносу:
- ерозійний, що виникає внаслідок механічного стирання, схоплювання та інших руйнівних процесів при безпосередньому контакті металевих поверхонь тертя;
- корозійний, що виникає при різного роду окисyювальних процесах на поверхнях тертя;
- абразивний, що викликає руйнування поверхонь тертя за наявності між ними твердих (абразивних) частинок, у тому числі і продуктів зносу.
Циліндр працює в умовах змінних тисків у надпоршневій порожнині. Його внутрішні стінки контактують з полум'ям та гарячими газами, температура яких сягає 1500…2500°С. Середня швидкість ковзання поршневих кілець по стінках циліндра в автомобільних двигунах досягає 12…15 м/с в умовах недостатнього змащування. Тому матеріал стінок циліндрів повинен мати високу механічну міцність, а конструкція стінок — підвищену механічну жорсткість. Поверхні стінок циліндрів повинні добре протистояти згаданим вище видам зношування. Крім цього матеріали для виготовлення циліндрів повинні мати добрі технологічні (ливарні та здатність до обробки різанням).
Матеріали для блоків циліндрів
Матеріалом для виготовлення блоків циліндрів зазвичай слугує перлітний сірий чавун з невеликим додаванням нікелю та хром, високолеговані чавуни та сталі, алюмінієві, рідше, магнієві сплави. На початку історії розвитку автомобілів могли також використовуватись латунні блоки циліндрів, що пояснювалось високою технологічністю цього сплаву при литті.
Чавунний блок циліндрів має більшу механічну жорсткість і менше чутливий до перегрівання, що забезпечує його роботоздатність у важких умовах експлуатації. Недолік — велика маса, схильність до корозії, нижча у 4 рази ніж в алюмінієвих сплавів теплопровідність, що ставить високі вимоги до роботи системи охолодження.
Блоки циліндрів з алюмінієвих сплавів є легкими за масою і краще охолоджуються, однак у них виникає проблема із забезпеченням зносостійкості та ремонтопридатності стінок циліндрів.
Тому на першому поколінні двигунів з алюмінієвим блоком застосовували вставні «мокрі» гільзи з сірого чавуну, що слугували стінками циліндрів і безпосередньо омивалися охолоджувальною рідиною. Ця конструкція, розроблена у 1930-х роках, набула поширення у 1950-х, причому лише у Європі, де її використовували виробники спортивних і дорогих представницьких машин (BMW, Jaguar, Rover, деякі італійські виробники), і в СРСР, де алюмінієві блоки циліндрів використовувались на автомобілях власної розробки, що окрім згаданих переваг давало можливість проводити економічно вигідний капітальний ремонт двигуна простою заміною гільз.
Однак у цього рішення були і недоліки. Алюмінієвий блок з мокрими гільзами з нижнім фіксуванням гільз, що було технологічнішим, мав суттєво нижчу жорсткість у порівнянні з чавунним, внаслідок чого був чутливим до перегрівання і не мав запасу для форсування. Технологія виготовлення гільзованого алюмінієвого блока циліндрів має підвищену трудомісткість, що суттєво ускладнювало його виробництво. Крім того, деякі алюмінієві сплави відрізняються високою схильністю до корозії при контакті з антифризами окремих марок. Тому до 1980—90-х років основним матеріалом для виготовлення блоків циліндрів, особливо американських виробників залишався чавун.
Зустрічались конструкції чавунних блоків із знімними гільзами, що диктувалось необхідністю зниження затрат на капітальний ремонт, а також як матеріал для гільз використовувались якісніші чавуни із вищою зносо- та корозійною стійкістю.
Технології виготовлення
У 1980-х роках почала набувати поширення технологія, за якою в алюмінієвий блок запресовувались тонкостінні «сухі» чавунні або композитні гільзи, що по всіх зовнішніх поверхнях контактували з алюмінієвим матеріалом. Однак, такі блоки також не є позбавленими недоліків, оскільки коефіцієнти температурного розширення чавуну й алюмінієвого сплаву не є однаковими, що вимагає додаткових заходів для недопущення відривання гільзи від блока при прогріванні двигуна та потенційно зменшує його довговічність.
Альтернативний підхід до вирішення описаної проблеми передбачає використання суцільно алюмінієвого блока, стінки циліндрів у якому зміцнюють з використанням спеціальних технологій. Наприклад, на піонері цього напрямку — двигуні Chevrolet Vega 1971 року — блок виливався із алюмінієвого заевтектичного сплаву з вмістом до 17% кремнію (фірмова назва Silumal®), а спеціальна обробка стінок циліндрів хімічним травленням збагачувала поверхневі шари кристалами кремнію (кислота спеціально підібраного складу вимивала алюміній, не зачіпаючи кремній), доводячи таким чином поверхневі шари до потрібного стану та твердості. Тим не менше, досвід виявився невдалим: двигун був дуже чутливим до якості мастильних матеріалів та до перегрівання, мав незадовільний ресурс і часто виходив з ладу набагато раніше від вичерпання нормативного ресурсу через знос стінок циліндра, відновлення яких виявилось дорогим і неможливим у звичних умовах ремонтних підприємств. Це спричинило гучні скандали і потягло за собою мільйонні збитки для компанії GM.
У подальшому аналогічний матеріал і технологію його обробки було доведено до досконалості європейськими автовиробниками (Mercedes-Benz, BMW, Porsche, Audi) і у 1980— 90-х роках вона була запроваджена на серійних моделях авто під назвою Alusil® (марка сплаву AlSi17Cu4Mg) з використанням методу лиття під низьким тиском. Якщо глянути на шліф цього сплаву під мікроскопом, видно, що сплав не є однорідним: на фоні алюмінію видно темні острівці кремнію. Оброблене дзеркало такого циліндра своїми властивостями буде нагадувати хонінговане чавунне: моторна олива на ньому буде затримуватися, але не в борозенках від хона, а між виступаючими з алюмінію острівцями кристалів кремнію. Ці острівці, крім того, забезпечують необхідну твердість і створюють потрібну пару тертя «стінка блока — поршень». Такий блок циліндрів можна при ремонті навіть у певних межах розточувати, так як товщина зміцненого шару алюмінію з підвищеною концентрацією кремнію становить порядку декількох мікрон з повторним хімічним травленням після хонінгування з використанням спеціальних брусків. Тим не менше, чутливість таких блоків до перегрівання та якості мастильних матеріалів залишилась — такі двигуни вимагають високої культури експлуатації й обслуговування, а їх температурним режимом повинна керувати електроніка.
Відносно недавно німецька фірма Kolbenschmidt[1] розробила технологію, за якою у звичайний блок з алюмінієвого сплаву запресовуються готові алюміній-кремнієві гільзи, із зміцненими стінками з підвищеним (до 27%) вмістом кремнію (технологія Locasil®), що дозволило знизити собівартість такого рішення і частково вирішити проблему ремонтопридатності. Це було першим поколінням такого роду технології, що наразі вже не використовується але ідея локального використання сплаву алюмінію з потрібними властивостями у вигляді вставних гільз набула подальшого розвитку.
Наразі застосовується технологія Locasil®II, яка краще задовольняє поставлені технічні вимоги. Пористі преформи із вмістом 25% дрібнодисперсного (30…70 мкм) кремнію виготовляють з використанням гель-сублімаційного лиття, з подальшим спіканням з доевтектичним ливарним сплавом вторинного алюмінію, що використовується для виливання блока. Для виготовлення блока використовується процес лиття під високим тиском який забезпечує поряд з повільним заповненням форми високий тиск для належного взаємного проникнення матеріалів. Завершальною операцією є спеціальний процес хонінгування з отриманням оптимальних трибологічних параметрів поверхні.
В іншому рішенні, спочатку фірма PEAK Werkstoff GmbH почала виготовляти гільзи зі сплаву AlSi17Cu4Mg методом лиття під високим тиском. Далі появилось технологічне рішення від Daimler AG — Silitec®. Суть цього методу полягає в тому, що у звичайний алюмінієвий блок запресовуються при виробництві кремнієвмісні гільзи, отримані методом відцентрового лиття з упорскуванням розпиленого розплаву (англ. spray compaction technology). Кремній у результаті швидкого охолодження при твердінні набуває дрібнозернистої щільної структури з високою однорідністю і довговічністю властивостей.
Отже, і Locasil®, і Silitec® при капітальному ремонті двигуна означають вибір традиційного способу гільзування.
Складніші технології підвищення характеристик поверхонь циліндрів з алюмінієвих сплавів передбачають поверхневе нанесення необхідних матеріалів в навантажених зонах.
Один з поширених і досить сучасних способів — газотермічне напилення на алюмінієву поверхню циліндра (Goedel®). Так поступає, використовуючи плазмове напилення, наприклад, VW при виробництві низки своїх двигунів. В результаті плазмового напилення отримують покриття товщиною 0,18...0,22 мм, має високу твердість та стійкість до зношування. Це покриття при первинній обробці нового блока, як і чавунну гільзу розточують під потрібний розмір та хонінгують. Плазмове покриття має ще одну особливість: воно пористе. А значить, здатне утримувати масло. Ця особливість дозволила змінити кут нахилу борозенок, що залишаються після хонінгування, зробити цей кут меншим — і тим самим зменшити витрату моторної оливи при експлуатації.
Ще одна технологія поверхневого зміцнення — це лазерне легування поверхні циліндра у блоці циліндрів, отриманому традиційними методами лиття при низькому тиску, що отримала назву Tribosil®. Поверхні циліндрів при локальному розплавленні скануючим променем лазера збагачуються частинками кремнію (розміром < 10 мкм), що подається у зону розплавлення у вигляді струменя пудри, аж до створення заевтектичної структури у товщині шару до 0,6 мм, яка після хонінгування характеризується високою зносостійкістю.
Альтернативою до напилення є технології Nikasil® та Galnical® — отримання гальванічним методом нікелевого покриття з вмістом (близько 10%) кристалів (розміром 1-3 мкм) карбіду кремнію на алюмінієвих стінках циліндрів. Цю технологію обмежено застосовували ще у 1960-70-х роках для двигунів дорогих спортивних авто. Обидві технології і Nikasil®, і Galnical® використовуються в серійному виробництві. Такі блоки мали двигуни M60 та M52 фірми BMW, причому їх продажі у деяких країнах супроводжувались скандалом — Nikasil руйнувався від хімічної реакції з деякими сортами пального, що містили підвищену концентрацію сірки[2]. Ця проблема суттєво обмежила застосування такої технології.
Див. також
Джерела
- Сирота В. І. Основи конструкції автомобілів. Навчальний посібник для вузів. К.: Арістей, 2005. — 280 с. — ISBN 966-8458-45-1
- Applications — Power train — Cylinder linings на сайті European Aluminium Association (EAA)
Посилання
- Assembly of Ford Duratec Engine 3D simulation — відео, яке демонструє будову та принцип роботи чотирициліндрового двигуна внутрішнього згоряння
- Автомобиль ЗАЗ 1102-1105. Глава 2. Силовой агрегат. Двигатель. Блок цилиндров. (рос.)
- Федоров Б. Такой разный алюминий (рос.)