Лазерна технологія
Ла́зерна техноло́гія (англ. laser technology) у промисловості — сукупність технологічних прийомів та способів впливу лазерним випромінюванням на об'єкт (речовину, матеріал, заготовку, виріб) з метою потрібної зміни його стану, властивостей, розмірів або форми.
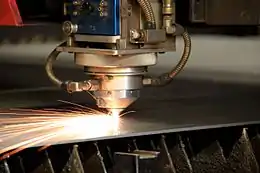

Історична довідка
Лазерна технологія зародилася на початку 1960-х років. За кілька років до того з'явилися перші лазери, почалися швидкий розвиток і виробництво лазерних систем. Висока густина потоку енергії і потужність лазерних пучків, а також монохроматичність, когерентність, спрямованість лазерного випромінювання і можливість його фокусування у пляму малого розміру (лазерний промінь) сприяли використанню лазерних технологій у різних областях науки і техніки. Найбільшого поширення вони набули у промисловості (англ. industrial laser applications). Власне поняття «лазерні технології» нині зазвичай охоплює саме промислове застосування. В основі цих технологій лежать різні фізико-хімічні процеси взаємодії лазерного випромінювання з речовиною — локальне нагрівання, розплавлення, випаровування, вибухове руйнування, нанесення або зчитування інформації, абляція тощо. Вони можуть фактично переходити від однієї операції до іншої шляхом зміни одного–трьох параметрів лазерного випромінювання — потужності або густини потужності, тривалості дії на матеріал, довжини хвилі. Завдяки забезпеченню високої локальності дії на виробництві досягають надзвичайної точності та якості оброблення, виконують унікальні мікро- та нанооперації. Крім того, поєднання лазерних технологій з програмним керуванням дозволяє керувати зміною сфокусованого лазерного випромінювання у часі та просторі, що відкриває унікальні можливості для виконання великого розмаїття технологічних завдань.
До лазерних технологій належать: прошивання отворів, різання, зварювання, модифікування, програмоване термодеформування, маркування та гравіювання, балансування, вирощування тримірних виробів, текстурування мікрорельєфу поверхні, поверхневе очищення тощо.
У лазерних технологіях використовують твердотільні (наприклад, на ітрій-алюмінієвому гранаті чи неодимовому склі) і газові (на діоксиді вуглецю, молекулах азоту) лазери з потужністю від одиниць до декількох сотень ват, що працюють в імпульсному, імпульсно-періодичному і неперервному режимах. Наукові основи лазерних технологій базуються на властивостях лазерного випромінювання, законах заломлення, поглинання та відбивання світла, а також, законах перебігу технологічних процесів у кожній конкретній галузі.
Лазерне свердління
Лазерне свердління (прошивання) отворів малих розмірів (від 10 мкм) застосовують при виготовленні діафрагм, сит та інших деталей у машино- та приладобудуванні. При цьому забезпечують регулювання форми отворів від циліндричної до конічної та навіть гранованої. Головним обмеженням під час виготовлення якісних отворів є товщина матеріалу (до 5…10 мм). Продуктивність прошивання малих отворів може досягати десятків і навіть тисяч на секунду. Особливо ефективним є оброблення мікро- та наноотворів у деталях із надтвердих матеріалів — діаманта, сапфіра, рубіна, новітніх композитів тощо. Прошивання отворів виконують переважно завдяки використанню густини потужності, що спричиняє не лише розплавлення, але і випаровування та навіть вибухове викидання матеріалу із зони дії сфокусованого лазерного випромінювання. На деяких режимах ініціюється процес локального руйнування матеріалу — абляція (сублімація), що дозволяє отримати вищу якість оброблення. Діапазон густини потужності для цієї операції становить 106…109 Вт/см².
Лазерне розділення (різання)
Різання матеріалів спочатку розглядалося лише як специфічна операція для розділення надтвердих кристалічних та аморфних матеріалів шляхом генерування локальних напружень з подальшим крихким терморозколюванням матеріалу в напрямку дії лазерного випромінювання. Лазерне терморозколювання забезпечує високоякісне розділення таких крихких матеріалів, як скло, ситали, сапфір, алюмооксидна кераміка при густині потужності лазерного випромінювання 103 Вт/см² і швидкості різання до 5 м/хв. Різновидом такої операції стало виготовлення мікрощілин і мікропазів у матеріалах (лазерне скайбування), що важко або зовсім неможливо було обробляти традиційними методами.
З появою нових ефективніших лазерних систем стало можливим використовувати лазерне випромінювання для розкрою габаритних деталей із листових матеріалів для різних машинобудівних галузей — автомобілебудування, авіакосмічної промисловості, суднобудування, енергетичного комплексу тощо. Швидкість розрізання таких матеріалів може досягати залежно від товщини матеріалу до кількох десятків метрів на хвилину при забезпеченні високої якості та точності і значної. Густина потужності сфокусованого випромінювання становить 108…109 Вт/см².
Лазерне зварювання та наплавлення
Лазерне зварювання матеріалів стало вже майже традиційним у аерокосмічному комплексі, енергетиці, автомобілебудуванні, електроніці та інших виробничих галузях. Широке застосування цієї нової технології сталося завдяки високій якості оброблення, можливості досягнення значної швидкості, особливо в умовах автоматизації процесу, з'єднання різних за властивостями матеріалів. Зварювання проводять із забезпеченням густини потужності сфокусованого лазерного випромінювання на рівні 104…107 Вт/см², достатнього для розплавлення матеріалу із тривалістю впливу імпульсів від 10−2…10−3 с до неперевного випромінювання. Лазерне зварювання дозволяє з'єднувати деталі зі швидкістю формування зварного шва до 10 м/хв. Лазерним методом зварюють високоміцні сталі, сплави (титанові, алюмінієві, нікелеві, молібденові тощо), композиційні матеріали, кераміку, а також різнорідні матеріали (наприклад, сталь-мідь, сталь-вольфрам, сталь-кераміка).
Лазерне наплавлення — метод відновлення зношених або підвищення міцності нових деталей машин, за допомогою створення на поверхні виробу плакувального шару з порошкового матеріалу, із проплавленням його лазерним променем.
Існує три способи лазерного наплавлення:
- з подаванням матеріалу в зону плавлення (газопорошкове лазерне наплавлення);
- оплавлення попередньо нанесених порошкових паст (шлікерних покрить);
- оплавлення напилених шарів (лазерне переплавлення напилених покрить).
Лазерне модифікування
Модифікування матеріалу є результатом термічного впливу на нього. Воно проявляється у формі різних металографічних структурних перетворень під дією локалізованого нагрівання та надшвидкісного охолодження за рахунок високої теплопровідності металевих матеріалів. Такі процеси відбуваються в умовах опромінення металевих матеріалів лазерним променем з густиною потужності 103…104 Вт/см². Серед різновидів модифікування — поверхневе зміцнення та поверхневе легування. У машинобудуванні широко використовуються: лазерна обробка поверхні, що підвищує (у декілька разів, а іноді і у десятки разів) зносостійкість, границю витривалості та інші механічні властивості деталей.
Лазерне маркування і гравіювання
Одна з найпоширеніших лазерних технологій у різних галузях — маркування та гравіювання. Її особливість, на відміну від традиційних методів, — безконтактність, велика швидкість нанесення та зчитування інформації, можливість нанесення інформації на носії з будь-яких матеріалів. Завдяки цій технології глобального поширення набуло штрих-кодування виробів майже в усіх галузях виробництва. Головними механізми нанесення знаків: випаровування, розплавлення, абляція (для відповідальних виробів електронних приладів) тощо.
Інші галузі використання лазера
Балансування виробів лазерним випромінюванням — специфічна операція, яка виконується під час виготовлення прецизійних виробів, що обертаються з надзвичайно високою швидкістю (до кількох тисяч обертів на хвилину). У місці дисбалансу деталі за допомогою лазерного випромінювання видаляють зайвий матеріал з точністю до тисячних часток міліграма без зупинки обертання деталі.
Вирощування тримірних виробів у спеціальній літературі нині відоме під різними назвами: англ. 3D printing, Rapid Prototyping, Selective Laser Sintering, Free Form Fabrication, Additive Manufacturing, Laser Stereolitography, 3D Object Sintering та ін. Головний принцип виготовлення об'єкта полягає в пошаровому відтворенні запроектованого виробу за допомогою лазерного випромінювання, що сканує у просторі згідно заданої програми. Для цього використовують металеву порошкову суміш або фотореактивну полімерну рідину (для англ. laser stereolitography). Ці методи дають можливість виготовляти деталі складної просторової форми без використання затратних традиційних технологій та дорогого обладнання.
Текстуруванням поверхні матеріалу отримують заданий візерунок і профіль мікрорельєфу поверхні виробу для надання їй спеціальних експлуатаційних якостей. Це новий напрям, що активно розвивається для створення перспективних конструкцій машин і приладів для аерокосмічної, електронної та інших сучасних галузей.
Поверхневе очищення виробів за допомогою лазерного випромінювання використовують для видалення різних типів мікроскопічних забруднень з відповідальних виробів в електронній техніці, медицині, біології тощо.
Див. також
Джерела
- Черненко В. С., Ківдрачук М. В., Дудка О. І. Променеві методи обробки: Навч. посібник. — К.: Кондор, 2004. — 166 с. — ISBN 966-7982-70-X
- Картавов С. А., Коваленко В. С. Применение оптических квантовых генераторов для технологических целей. — К.: Техніка, 1967 — 80 с.
- Elion H. A. Laser Systems and Applications. — London; Edingburg: Elsevier, 1967. — 636 p. — ISBN 978-0080122366.
- Коваленко В. С. Обработка материалов импульсным излучением лазеров. — К.: Вища школа, 1977 — 44 с.
- Реди Дж. Промышленные применения лазеров / Пер. с англ. — М.: Наука, 1981. — 638 с.
- Коваленко В. С., Верхотуров А. Д., Головко Л. Ф., Подчерняева И. А. Лазерное и электроэрозионное упрочнение материалов. — М.: Наука, 1986. — 276 с.
- Коваленко В. С. Лазерная технология: учебник. — К.: Вища школа, 1989.
Посилання
- Лазерна технологія // Енциклопедія сучасної України : у 30 т. / ред. кол. І. М. Дзюба [та ін.] ; НАН України, НТШ. — К. : Інститут енциклопедичних досліджень НАН України, 2001–2020. — ISBN 944-02-3354-X.
- Лазерна обробка // Українська радянська енциклопедія : у 12 т. / гол. ред. М. П. Бажан ; редкол.: О. К. Антонов та ін. — 2-ге вид. — К. : Головна редакція УРЕ, 1974–1985.