Лиття пластиків під тиском
Лиття́ пластиків під ти́ском — технологічний процес виготовлення виробів з пластиків, що базується на заповненні формувальної порожнини прес-форми розплавом з подальшим його ущільненням за рахунок тиску і охолодженням.
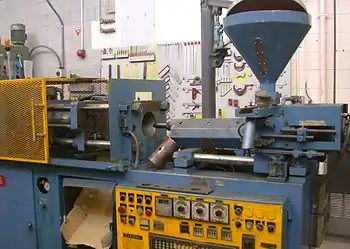
Прес-форма — металева ливарна форма для виробництва виливків на машинах лиття під тиском[1].
Лиття під тиском — найпоширеніший і найпрогресивніший метод переробки пластиків, оскільки дозволяє отримувати вироби порівняно складної конфігурації при невеликих затратах праці та енергії.
Обладнання для лиття під тиском
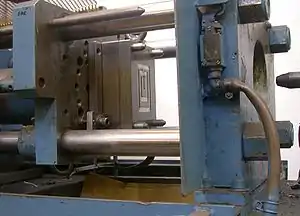
Лиття пластиків під тиском здійснюється на спеціальних інжекційно-ливарних машинах, які бувають двох типів:
- вертикальні, у яких впорскування матеріалу здійснюється вертикально вниз, а основна площину розняття прес-форми розташована горизонтально. Вертикальні машини зазвичай використовуються для виготовлення виробів з закладними елементами.
- горизонтальні — з горизонтальним уприскуванням матеріалу і вертикально розташованою площиною розняття форми.
Лиття під тиском — періодичний процес, у якому технологічні операції виконуються в певній послідовності по замкнутому циклу. Тому процес лиття під тиском порівняно легко автоматизується як з використанням найпростіших серійних приладів, таких, як реле часу, регулятори тиску та електронні потенціометри, так і з використанням давачів, що перетворюють технологічні параметри в електричні сигнали з керуванням від програмованих контролерів. Це дозволяє істотно підвищити ефективність виробництва.
Автоматизоване обладнання для лиття пластиків під тиском має назву термопластавтомат.
Технологія лиття під тиском
Технологічний процес лиття виробів з термопластичних полімерів складається з таких операцій:
- плавлення, гомогенізація і дозування полімеру;
- змикання форми, підведення вузла впорскування до форми;
- впорскування розплаву;
- витримування під тиском і відведення вузла вприскування, охолодження виробу;
- розкриття форми і витягання виробу.
Плавлення, гомогенізація і дозування полімеру
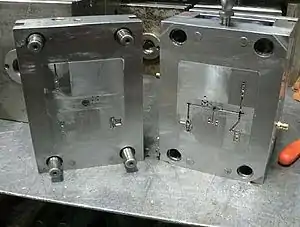
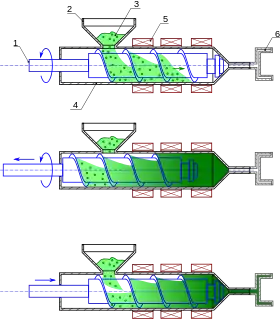
1 — шнек;
2 — бункер;
3 — гранульваний матеріал;
4 — циліндр ливарної машини;
5 — система нагрівання;
6 — формувальна порожнина прес-форми
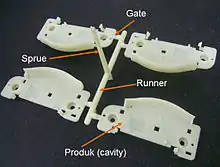
Sprue — центральний ливник;
Runner — ливникова система;
Gate — точковий ливник;
Produk (cavity) — продукт (деталь)
Гранульований матеріал, дозований з бункера, подається на обертовий шнек всередині циліндра спеціальної конструкції. Циліндр ливарної машини підігрівається від електричних (іноді, масляних) нагрівних елементів. Матеріал нагрівається як від стінок циліндра, так і внаслідок тертя. Обертання шнека забезпечує рух матеріалу в циліндрі ливарної машини а також інтенсивне його перемішування, що сприяє вирівнюванню температури. За допомогою поршня приводу вузла вприскування на шнеку створюється зусилля підпору, тому шнек відходить не вільно, а долаючи тиск підпору. Слід зауважити, що тиск підпору збільшує температуру розплаву і підвищує її однорідність по перерізу в каналах шнека. Шнек створює високий тиск. Поєднання високої температури і тиску призводить до розплавлення матеріалу. Частоту обертання шнека і температуру по зонах циліндра визначають експериментально або розраховують з врахуванням розмірів шнека і тиску підпору.
Змикання форми, підведення вузла вприскування до форми
Змикання форми і створення певного зусилля замикання здійснюється в результаті переміщення рухомої плити термопластавтомата разом із закріпленою на ній частиною прес-форми. Зусилля змикання Nзм необхідне для виключення розкриття форми в момент заповнення її розплавом, воно має дорівнювати
- Nзм ≥ pф(Fвирn+Fл),
де pф — тиск у формі, усереднений по площі виливка;
- Fвир і Fл — площа ливників у площині розняття форми.
У випадку, коли площа виливка дуже велика і розрахункове зусилля перевищує максимальне зусилля змикання машини, через надмірне зростання пружних деформацій замикальних ланок механізму вироби після лиття можуть мають товстий облой. Іноді з цієї ж причини може відбутися розкриття форми.
Підведення вузла вприскування до форми проводиться окремим механізмом, при цьому сопло циліндра впирається в ливникову втулку прес-форми та створюється необхідне притискання, що запобігає витіканню розплаву. У момент підведення вузла впорскування сопло повинне розташовуватися співвісно з ливниковим каналом форми.
Впорскування розплаву
Шнек ливарної може здійснювати два типи руху. Обертальний, що виконується для подавання та пластифікування матеріалу і вертально-поступний, що виконується при впорскуванні матеріалу. Шнек у другому випадку виконує роль поршня, що витискає розплав у форму. Зріджений матеріал потрапляє у порожнину сталевої форми через сопло (сопла) і систему ливникових каналів, виконаних у формі. Форма конструюється так, щоб час заповнення її порожнини був мінімальним (1…3 с). Тиск упорскування може досягати значень до 1000 бар.
Характер заповнення форми розплавом залежить від швидкості уприскування і розмірів формувальної порожнини. Так при, дуже високій швидкості уприскування розплав після виходу з ливників рухається у формувальній порожнині спочатку зигзагоподібно, а по мірі заповнення порожнини форми розплавом відбувається ущільнення окремих зигзагів і турбулентний режим переходить в ламінарний — течію суцільним потоком. Вихровий режим виникає переважно у тому випадку, коли глибина впускного ливника набагато менша за формувальний зазор. При литті тонкостінних виробів або впорскуванні розплаву з невисокою швидкістю заповнення форми відбувається суцільним потоком, який утворюється у безпосередній близькості до впускного ливника. Як у першому, так і в другому режимах заповнення розплав при зіткненні з холодними стінками форми прилипає до поверхні і на ній з'являється плівка затверділого полімеру. З одного боку, утворення плівки трохи зменшує глибину формувальної порожнини, а з другого, різко знижує подальше охолодження розплаву через малу теплопровідність полімеру. Оскільки заповнення форми відбувається з високою швидкістю, товщина утвореного твердого шару становить частки міліметра і не робить значного впливу на швидкість течії, особливо коли лиття проводиться при високій температурі розплаву і форми.
Витримування під тиском і охолодження виробу
Після заповнення форми розплавом відбувається його охолодження, в результаті чого збільшується густина і зменшується об'єм матеріалу. Внаслідок зменшення об'єму (усадки) через ливники у форму продовжує надходити додаткова порція розплаву і тиск в ній підтримується сталим. Таким чином, після закінчення операції впорскування настає деяке рівновага тисків у циліндрі машини та у формувальній порожнині і течія переходить в повільне додаткове нагнітання розплаву (підживлення); останнє компенсує усадку полімеру у формі при його охолодженні.
Витримування під тиском зазвичай продовжується до тих пір, поки розплав в центральній частині впускного ливника не охолодиться нижче за температуру текучості. Після затвердіння ливника маса розплаву у формувальній порожнині більше не змінюється (при відведенні сопла витікання розплаву не відбувається) то ці значення температури і тиску розплаву визначають подальшу зміну лінійних розмірів виробу при охолодженні. Чим довше витримування під тиском, тим сильніше знижується температура розплаву у формувальній порожнині, тому при наступному охолодженні розміри виробу будуть змінюватися у меншій мірі. Те ж спостерігається при підвищенні тиску в формі. Таким чином, витримування під тиском компенсує усадочні процеси, що відбуваються в формі, і залежить від розмірів ливника, температури розплаву і форми, а також від тепло-фізичних властивостей полімеру. Витримування під тиском доцільне, поки полімер в формувальній порожнині знаходиться у розплавленому стані, тому глибину впускного ливника зазвичай вибирають з урахуванням заданої усадки, але меншою за товщину стінки виробу.
При великій глибині ливника час витримки під тиском зростає і збільшується час, необхідний для охолодження деталі. Оскільки операція охолодження суміщається з дозуванням розплаву (пластикацією) за короткий проміжок часу не встигає накопичитися задана порція розплаву і необхідним буде збільшення тривалості циклу лиття або підвищення швидкості обертання шнека, що погіршує гомогенізацію. У зв'язку з цим не рекомендується застосовувати ливники великого перетину. При тривалому підживленні на розплав при його охолодженні в формі діють напруження зсуву, зростає ступінь орієнтації макромолекул і збільшується анізотропія властивостей виробу. Для запобігання цьому доцільно заповнити форму розплавом, ущільнити його під високим тиском, перекрити ливникові канали і припинити підживлення. У цьому випадку течія розплаву в формі припиняється і в результаті релаксаційних процесів відбувається дезорієнтація макромолекул. Такий процес можна здійснити при використанні ливників з невеликою глибиною (точкові ливники) або мундштуків із запірним клапаном. Однак у цьому випадку неможливо проводити підживлення, тому для зменшення усадки виробів необхідно створювати у формі високий тиск.
Фактично охолодження розплаву починається відразу після упорскування розплаву, проте як окрема технологічна операція охолодження задається часом після закінчення витримки під тиском. Таким чином, витримка при охолодженні необхідна для остаточного затвердіння розплаву полімеру і досягнення певної конструкційної жорсткості виробів, що виключає їх деформацію при витяганні з форми.
Температура полімеру перед розмиканням форми повинна бути такою, щоб при витяганні виробу не відбулося його жолоблення чи руйнування.
Розкриття форми і витягання виробу
Після закінчення операції охолодження відбувається розкриття форми. Рухома частина форми, що закріплена на плиті вузла змикання, відводиться, при цьому виріб рухається разом з нею. Виступаюча частина блоку штовхачів впирається в обмежувач і вони зупиняються разом з виробом, а рухома частина форми відводиться далі, за рахунок чого відбувається вилучення виробу. Одночасно з виробом з ливникової втулки витягується ливник. Розплав при витіканні з центрального ливника затікає в отвір плити, що має зворотний конус і застигає в ньому. В результаті утворюється замок, за допомогою якого при розкритті форми відбувається видалення ливника з ливникової втулки.
Див. також
Примітки
- ДСТУ 2541-94 Виробництво ливарне. Терміни та визначення.
Джерела
- Суберляк О. В. Технологія переробки полімерних та композиційних матеріалів : підруч. [для студ. вищ. навч. закл.] / О. В. Суберляк, П. І. Баштанник. — Львів : Растр-7, 2007. — 375 с. — ISBN 978-966-2004-01-4
- Бортников В. Г. Основы технологии переработки пластических масс. Л.: Химия, 1983.
- Основы технологии переработки пластмасс: Учебник для вузов/ С. В. Власов, Л. Б. Кандырин, В. Н. Кулезнев и др. — М.: Химия, 2004. — 600с. — ISBN 5-03-003543-5
- Брагинский В. А.. Точное литье изделий из пластмасс. — Л.: Химия, 1977. — 112 с.
- Видгоф Н. Б. Основы конструирования литьевых форм для термопластов. — М.: Машиностроение, 1979. — 261 c.
- Литье под давлением / М. Б. Беккер, М. Л. Заславский, Ю. Ф. Игнатенко и др. — 3-е изд., пефраб. и доп. М.: Машиностроение, 1990, — 400 с. ISBN 5-217-00847-4