Оксидування
Оксидува́ння (від нім. oxydieren — окиснювати) — оброблення поверхні металевих або напівпровідникових матеріалів хімічним чи електрохімічним (анодування) способом, внаслідок якого на поверхні утворюється плівка з їхніх оксидів[1]. Такі плівки (завтовшки від частин мікрометра до 500…600 мкм) підвищують корозійну стійкість, стійкість проти зношування та електроізоляційні властивості виробів, надають виробам естетичного вигляду.
Види оксидування
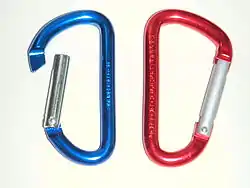
Термічне оксидування
Термічне оксидування проводиться при нагріванні в атмосфері кисню або водяної пари. Оксидування вуглецевих та легованих сталей називають також, воронуванням або чорнінням.
Наприклад, термічне оксидування заліза та маловуглецевих сталей, проводять у термічних печах, нагрітих до 300…350 °С, або при безпосередньому нагріванні виробів на повітрі, добиваючись необхідного кольору поверхні обробки. Леговані сталі термічно оксидують при вищих температурах (400…700 °C) протягом 50…60 хв. Магнітні залізонікелеві сплави (пермалої) оксидують при 400…800 °С протягом 30…90 хв.
Хімічне оксидування
Хімічне оксидування — обробка розплавами або розчинами окиснювачів, таких як хромати, нітрати тощо, переважно, для захисту від корозії або створення покриттів декоративного призначення на поверхні чорних та кольорових металів і сплавів.
Хімічне оксидування чорних металів проводять в кислотних (кислотне воронування) або лужних (лужне воронування) розчинах за температури 30…100 °С. Зазвичай використовують суміші соляної, нітратної або ортофосфатної кислот з додаванням сполук Ca(NO3)2 тощо. Лужне оксидування проводять у розчині лугу з додаванням окиснювачів за температур 30…180 °С. Оксидні плівки на поверхні чорних металів отримують також у розплавах, що складаються з лугу NaNO3 та NaNO2, MnO3 при температурах 250…300 °С. Після оксидування вироби промивають, сушать й інколи піддають обробці в окиснювачах (K2Cr3О7) або промаслюють[2].
Хімічне оксидування застосовують для обробки деяких кольорових металів. Найпоширенішим є хімічне оксидування виробів з магнію та його сплавів у розчинах на базі К2Cr2О7. Мідні або міднені вироби окиснюють у розчинах, які містять NaOH та K2S2O2. Іноді хімічне оксидування використовують для алюмінію та сплавів на його основі (дюралюмінію). У склад розчину входять Н3РО4, СrО3 і флуориди. Однак за якістю оксидні плівки, отримані хімічним оксидуванням поступаються плівкам, нанесених анодуванням.
Електрохімічне оксидування
Електрохімічне оксидування (анодування стосовно деталей з алюмінію та його сплавів) — оксидування в електролітах (рідких, рідше в твердих), мікродугове оксидування, процес електролітичного окиснення, при якому поверхневий шар металу перетворюється у покриття з захисними, декоративними чи функційними властивостями[1].
Поверхня матеріалу, що підлягає оксидуванню перебуває при обробленні під додатнім електричним потенціалом у рідких або твердих електролітах. Він забезпечує високонадійні плівки наступних типів:
- тонкошарові покриття з товщиною від 0,1 до 0,4 мікрометрів;
- електроізоляційні і зносостійкі шари товщиною від 2…3 до 300 мікрометрів;
- захисні покриття від 0,3 до 15 мікрометрів;
- спеціальні емалеподібні шари на поверхні деталей з алюмінієвих сплавів (іменуються в середовищі фахівців ематаль-покриттями).
Для утворення товстих оксидних шарів застосовують переважно розчини H2SO4 та CrO3. Тонкі оксидні плівки отримують у розчинах на основі Н3РО4 та Н3BO3. Кольорове анодування проводять у розчинах, що містять органічні кислоти (щавлеву, малеїнову, сульфосаліцилову та ін.). Ематаль-покриття отримують в електролітах, що містять, зазвичай, СrO3. Анодування магнію та його сплавів проводять у розчинах, що містять гідроксид натрію, флуориди, хромати металів. Анодне оксидування сталі проводять в розчинах лугу або CrO3.
Окремим випадком анодування вважається методика мікродугового оксидування, яка дозволяє отримувати унікальні покриття з високими декоративними, теплостійкими, захисними, ізоляційними і антикорозійними параметрами. Мікродугового процес здійснюється під дією змінного або імпульсного струму в слабколужних електролітах. Розглянутий спосіб нанесення спеціальних шарів забезпечує товщину покриттів на рівні 200…250 мікрометрів. Після виконання операції отримана поверхня виробу зовні схожа на кераміку. Під час перебігу процесу у повітря не виділяються небезпечні для людини речовини.
Плазмове оксидування
Плазмове оксидування проводиться у низькотемпературній плазмі із вмістом кисню, за допомогою розрядів постійного струму або ВЧ (НВЧ) розрядів. Якість одержуваних захисних плівок оксидів при плазмовому процесі дуже висока. Тому його застосовують для нанесення покриттів на відповідальні деталі:
- кремнієві поверхні;
- напівпровідникові вироби;
- фотокатоди.
Різновидом плазмового оксидування є іонно-плазмове оксидування, що проводиться у високотемпературній кисневмісній плазмі, утвореній струмами високої частоти або дуговим розрядом у вакуумі (за тиску близько 1 Па) й температурі поверхні обробки не вищій за 430°С. При такому способі оксидування іони плазми досягають поверхні виробу з енергіями, достатніми для їх проникнення у поверхневий шар та часткового розпилення. Такі плівки можуть переважати за якістю плівки, отримані термічним оксидуванням.
Використання
Оксидування використовують у приладо-, літако- і машинобудуванні, для оздоблення будівельних і архітектурних деталей, металевих виробів побутового призначення тощо.
Термічне оксидування є однією з важливих операцій планарної технології; створювані таким чином діелектричні плівки захищають готові напівпровідникові структури від зовнішніх впливів, ізолюють активні області дискретних напівпровідникових приладів та інтегральних схем. З початку 1980-х років у виробництві кремнієвих інтегральних схем оксидування проводять за підвищеного (до 107 Па) тиску кисню або водяної пари (термокомпресійне оксидування).
У виробництві електровакуумних приладів хімічне оксидування застосовують для чорніння деталей з метою отримання поверхні з низьким коефіцієнтом відбивання світла та високим коефіцієнтом теплового випромінювання.
Рідинне електрохімічне оксидування у водних та неводних розчинах електроліту застосовують для отримання захисних, декоративних покриттів та діелектричних шарів на поверхні металів, сплавів, напівпровідників при виготовленні приладів із структурами метал-діелектрик-напівпровідник та надвисокочастотних інтегральних схем, оксидних конденсаторів, комутаційних плат на основі алюмінію тощо.
Плазмове оксидування використовують при виготовленні напівпровідникових приладів та інтегральних схем, при створенні тунельних переходів на основі плівок Nb та Pb в кріо-електронних інтегральних схемах, а також для підвищення світлочутливості срібно-цезієвих фотокатодів.
Окрім цього, оксидування знайшло своє місце в ювелірному мистецтві. На даний момент, значна кількість срібних прикрас піддається оксидуванню (чорненню). Робиться це для виділення рельєфу прикраси. Даний шар розглядається ювелірами виключно в декоративних цілях, оскільки його легко видалити.
Див. також
Примітки
- ДСТУ 2491-94 Покриття металеві та неметалеві неорганічні. Терміни та визначення.
- Хім. окс. прм.
Джерела
- Лайнер В. И. Защитные покрытия металлов. — М.: Металлургия, 1974. — 559 с.
- Грилихес С. Я. Оксидирование и фосфатирование металлов. — Л., Машиностроение, 1971. — 120 с.
- Вайнер Я. В., Дасоян М. А. Технология электрохимических покрытий. — Л., Машиностроение, 1972. — 464 с.
- Аверьянов Е. Е. Справочник по анодированию. — М.: Машиностроение, 1988. — 224 с. — ISBN 5-217-00273-5.
- Юнг Л. Анодные оксидные пленки. — Л.: Энергия, 1967. — 232 с.
Посилання
- Оксидування сталі — всі способи нанесення захисного покриття на сайті «Будівельні технології».
- «Оксидування» на сайті «Обробка металу».
- «Оксидирование» на сайті «ХиМиК» (рос.)
- Оксидування — покриття в ювелірному мистецтві на сайті «Kochut»