Плазмове оброблення
Пла́змове обро́блення — вид електрофізичного оброблення матеріалів низькотемпературною плазмою, яка генерується дуговими (оброблення плазмовою дугою) або високочастотними (оброблення плазмовим струменем) плазмотронами.
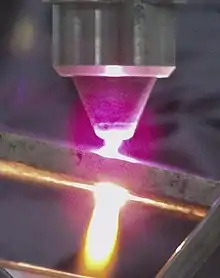
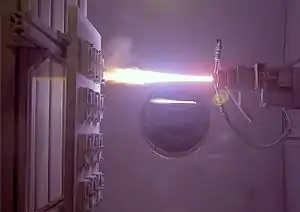
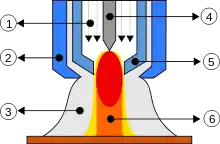
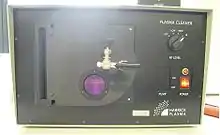
Основні принципи
Плазмове оброблення набуло поширення унаслідок високої за промисловими стандартами температури плазми (~ 104 К), великого діапазону регулювання потужності і можливості зосередження потоку плазми на виробі, що обробляється. При цьому ефекти плазмової обробки досягаються як тепловою, так і механічною дією плазми (бомбардуванням виробу частками плазми, що рухається з дуже високою швидкістю, — так званий швидкісний натиск плазмового потоку).
Питома потужність, що передається поверхні матеріалу плазмовою дугою, досягає 105…106 Вт/см², в разі використання плазмового струменя вона становить 103…104 Вт/см². В той же час тепловий потік, якщо це необхідно, можливо розосередити, забезпечуючи «м'який» рівномірний нагрів поверхні, що використовується при наплавленні чи нанесенні покриттів.
Види плазмового оброблення
При плазмовому обробленні змінюється форма, розміри, структура оброблюваного матеріалу або стан його поверхні. Плазмове оброблення включає: розділове і поверхневе різання, нанесення покриттів, наплавлення, зварювання, руйнування гірських порід (плазмове буріння), активування поверхні а також, плазмово-дугове «стругання» і рафінування (оплавлення).
Плазмове різання
Різання металів та виготовлення отворів (лазерне свердління) здійснюється стисненою плазмовою дугою, яка горить між анодом (металом, що підлягає розрізанню) і катодом плазмового пальника. Стабілізація і стискування струменевого каналу дуги, що підвищує її температуру, здійснюються соплом пальника і обдуванням дуги потоком плазмоутворюючого газу (Ar, N2, H2, NH4 чи їх суміші). Для інтенсифікації різання металів використовується хімічно активна плазма. Наприклад, при різанні повітряною плазмою O2, окислення металу, дає додатковий енергетичний внесок у процес різання. Плазмовою дугою ріжуть неіржавні і хромонікелеві сталі, Cu, Al та ін. метали і сплави, що не піддаються кисневому різанню. Висока продуктивність плазмового різання дозволяє застосовувати його в потокових безперервних виробничих процесах. Потужність установок сягає 150 кВт. Неелектропровідні матеріали (бетони, граніти, тонколистові органічні матеріали) також обробляють плазмовим струменем (дуга горить у соплі плазмового пальника між його електродами).
Плазмове напилення
Нанесення покриттів (напилення) здійснюється для захисту деталей, що працюють при високих температурах, в агресивних середовищах та зазнають інтенсивної механічної дії. Матеріал покриття (тугоплавкі метали, оксиди, карбіди, силіциди, бориди та ін.) вводять у вигляді порошку або дроту в плазмовий струмінь, в якому він плавиться, розпилюється, набуває швидкості ~ 100–200 м/с і у вигляді дрібних часток (20—100 мкм) наноситься на поверхню виробу. Плазмові покриття відрізняються зниженою теплопровідністю і добре протистоять термічним ударам. Потужність установок для напилення становить 5…30 кВт, максимальна продуктивність 5…10 кг напиленого матеріалу на годину. Розмір часток може регулюватися в межах від декількох мікрометрів до 1 мм. Дрібніші (ультрадисперсні) порошки з розмірами часток 10 нм і менше отримують випаровуванням вихідного матеріалу в плазмі з подальшою його конденсацією.
Плазмове наплавлення
Плазмове наплавлення металу можна реалізувати двома способами:
- струмінь газу захоплює і подає порошок на поверхню деталі;
- у плазмовий струмінь вводиться присадочний матеріал у вигляді дроту, прутка, стрічки.
Як плазмоутворюючий газ можна використовувати аргон, гелій, азот, кисень, водень і повітря. Найкращі результати наплавлення виходять з аргоном і гелієм.
Газ подається при тиску в 2…3 ат, утворюється електрична дуга із силою струму 400…500 А і напругою 120…160 В, іонізований газ досягає температури 10…18 тис. °C, а швидкість потоку — до 15 000 м/с. Катодом служить неплавкий вольфрамовий електрод.
Плазмове зварювання
Властивість плазмової дуги глибоко проникати в метал використовується для зварювання металів. Сприятлива форма ванни, що утворюється, дозволяє зварювати метал товщиною до 10…15 мм без спеціального оброблення кромок. Зварювання плазмовою дугою відрізняється високою продуктивністю і унаслідок великої стабільності горіння дуги, хорошою якістю. Малопотужна плазмова дуга при струмах 0,1…40 А є зручною для зварювання тонких листів (0,05 мм) при виготовленні мембран, сильфонів, теплообмінників з Ta, Ti, Мо, W, Al.
Плазмове буріння
Для плазмового буріння застосовують плазмотрони спеціальної конструкції — плазмо-бури. За їхньою допомогою створюють бурові свердловини і шпури, розширюють їх, видобувають і обробляють поштучний камінь, ріжуть бетон
Плазмове стругання
Плазмо-дуговим «струганням» (здуванням оплавленого металу струменем газу) і рафінуванням обробляють поверхневі шари металів і сплавів.
Плазмове активування поверхні
Плазмове активування — обробка поверхні плазмою (як правило, з невеликою кількістю кисню) для утворення вільних радикалів на оброблюваній поверхні з метою формування хімічно активного поверхневого шару. Застосовується з метою очищення і поліпшення властивостей поверхні для подальших технологічних операцій.
Див. також
Джерела
- Антосяк В. Г., Могорян Н. В. Электрофизические методы обработки материалов / Под ред. Н. К. Фатеева; Кишиневский политехнический институт им. Лазо — Кишинев: Штиинца, 1987. — 145 с.
- Справочник по электрохимическим и электрофизическим методам обработки / Г. Л. Амитан, И. Е. Байеупов, Ю. М. Барон и др.; Под общ. ред. В. А. Валосатого. — Л.: Машиностроение, 1988. — 719 с. — ISBN 5-217-00267-0
- Хасуи А., Моригаки О. Наплавка и напыление. / Пер. с яп. В. Н. Попова; под ред. В. С. Степина, Н. Г. Шестеркина. — М.: Машиностроение, 1985. — 240 c.
- Квасницький В. В. Спеціальні способи зварювання: Навч. посібник. — Миколаїв: УДМТУ, 2003. — 437 с.
Посилання
- Плазмова обробка // Українська радянська енциклопедія : у 12 т. / гол. ред. М. П. Бажан ; редкол.: О. К. Антонов та ін. — 2-ге вид. — К. : Головна редакція УРЕ, 1974–1985.