Жароміцні сплави
Жароміцні́ спла́ви або суперспла́ви (англ. superalloy) — сплави на нікелевій, залізохромонікелевій, кобальтовій або змішаній основі, що відзначаються високим опором пластичній деформації та руйнуванню в умовах високих температур та окиснювальних середовищ.
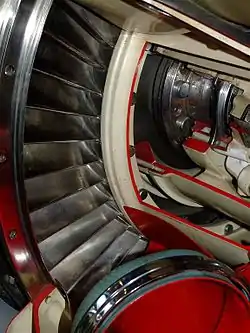
Основними фізико-механічними характеристиками жароміцних сплавів є значний опір повзучості, втомлюваності, а також, висока тривала міцність.
Природа жароміцності
Висока жароміцність сплавів визначається двома основними фізичними чинниками — міцністю міжатомних зв'язків в сплаві і його структурою. Зазвичай необхідну для високої міцності структуру отримують термічною обробкою (гомогенізувальним гартуванням і старінням металів), що приводить до гетерогенізації мікроструктури, а також у процесі легування тугоплавкими хімічними елементами (вольфрамом, молібденом, ванадієм) і елементами-зміцнювачами (титаном, алюмінієм, ніобієм, бором). В цьому випадку зміцнення обумовлене головним чином появою в сплавах рівномірно, розподілених вельми дрібних часток хімічних сполук (інтерметалідів, карбідів та ін.) і мікроспотвореннями кристалічної решітки основи сплаву, викликаними наявністю цих часток. Відповідна структура жароміцного сплаву утрудняє утворення і рух дислокацій, а також підвищує кількість зв'язків між атомами, що одночасно беруть участь в опорі деформації. З іншого боку, високе значення величини міжатомних зв'язків дозволяє зберегти необхідну структуру при високих температурах протягом тривалого часу.
Крім того, високу жароміцність забезпечують, зменшуючи вміст свинцю, олова, сурми, вісмуту і сірки, додаючи рафінуючі елементи (кальцій, церій, барій і бор). Якщо вироби з жароміцних сплавів призначені для тривалої експлуатації при температурі понад 800° С, їхню поверхню додатково піддають дифузійній термохімічній обробці (алітуванню, хромоалітуванню, емалюванню, нанесенню тугоплавких оксидів тощо). Різновидом жароміцних сплавів є композити: сплави, зміцнені дисперсними частинками тугоплавких оксидів або високоміцними волокнами. Такі матеріали характеризуються надзвичайно високою стабільністю властивостей, мало залежних від часу перебування в умовах високих температур.
Класифікація та використання
Жароміцні сплави застосовують для виготовлення деталей двигунів внутрішнього згоряння, парових і газових турбін, авіаційних, суднових і залізничних газотурбінних двигунів, в енергетичному машинобудуванні, тощо.
Жароміцні сплави за умовами роботи можна розділити на 3 групи:
- сплави, які піддаються значним, але короткочасним (від секунд до годин) механічним навантаженням в умовах високих температур;
- сплави, які знаходяться під навантаженням при високих температурах протягом десятків і сотень годин;
- сплави, які призначені для роботи в умовах великих навантажень і високих температур протягом тисяч, десятків, а інколи сотень тисяч годин.
Залежно від цього істотно змінюються вимоги до структури сплаву. Наприклад, будь-яка причина, що обумовлює нестійкість структури сплаву за робочих умов, викликає прискорення процесів деформування й руйнування. Тому сплави, що призначені для тривалої служби, піддаються спеціальній стабілізуючій обробці, яка, хоча і може привести до деякого зниження міцності при короткочасному вантаженні, робить сплав стійкішим до тривалої дії навантажень.
Жароміцні сплави класифікують також, за їх основою: нікелеві, залізні, титанові, берилієві тощо. Назва за основою дає уявлення про інтервал робочих температур, який залежно від прикладених навантажень і тривалості їх дії складає 0,4…0,8 від температури плавлення основи. Залежно від призначення жароміцні сплави виготовляють з підвищеним опором втомі і ерозії, з малою чутливістю до надрізів, термостійкі, для експлуатації при значних, але короткочасних навантаженнях та ін. Наприклад, жароміцні сплави, що використовуються у космічній техніці, повинні мати низьку випаровуваність.
Жароміцні сталі
Перші жароміцні сталі для газотурбінних двигунів були створені у Німеччнині компанією «AG Krupp» у 1936–1938 роках. Високолегована аустенітна сталь тінідур створювалась як матеріал робочих лопаток турбіни на температури 600…700 °C. Тінідур — аустенітна сталь з дисперсним твердненням (Ni3Ti) і карбідним зміцненням. У 1943-44 роках річне виробництво сталі тінідур становило 1850 тонн. Інститутом DVL (нім. Deutsche Versuchsanstalt für Luftfahrt — Німецький науково-дослідний інститут авіації) і фірмою «Heraeus Vacuumschmelze AG» були розроблені аустенітні сталі DVL42 та DVL52 для вищих робочих температур 750…800 °C. Склади сталей подані у таблиці.
Назва | %C | %Mn | %Si | %Ni | %Co | %Cr | %Mo | %W | %Ti | %Al | % ін. елементів |
---|---|---|---|---|---|---|---|---|---|---|---|
Тінідур | до 0,14 | 0,6-1,0 | 0,6-1,0 | 29,0-31,0 | 14,5-15,5 | 1,8-2,2 | 0,2 | Fe основа | |||
DVL42 | до 0,1 | 0,6-1,0 | 0,4-0,8 | 30-35 | 22-25 | 12-17 | 4-6 | 4-6 | 1,5-2,0 | Fe основа | |
DVL52 | до 0,1 | 0,6-1,0 | 0,4-0,8 | 30-35 | 22-25 | 12-17 | 4-6 | 4-6 | 4-5%Ta | ||
Хромадур | 0,9-0,12 | 17,5-18,5 | 0,55-0,7 | 11,0-14,0 | 0,7-0,8 | V 0,60-0,70 0,18-0,23 N2 |
В Німеччині у 1940-х роках розробники авіаційних ГТД прагнули підвищити температуру газу перед турбіною до 900 °C. З цією метою інститут DVL спільно з низкою фірм експериментував з аустенітними складнолегованими сплавами. У ході війни була визнана неможливість подібного рішення по причині гострого дефіциту в Німеччині легувальних елементів. Перші серії реактивного двигуна «Jumo-004» випускались з 1942 року з монолітними робочими і сопловими лопатками з матеріалу тінідур. Згодом їх замінили пустотілі лопатки з охолодженням з того ж матеріалу, що дозволило підвищити температуру газу перед турбіною до 850 °C (серія «Jumo-004E»). З 1944 року на двигуні «Jumo-004» використовувались робочі лопатки з охолодженням з менш дефіцитної сталі хромадур.
В кінці 1940-х років припинилось, в основному, використання заліза як основи жароміцних сплавів, на користь сплавів на основі нікелю і кобальту. Це дозволило отримати міцнішу і стабільнішу гранецентровану матрицю.
Сучасні жароміцні сталі класифікують за температурою експлуатації. Для роботи при 500...550 °С використовують сталі марок 20X13, 15X11МФ, 13Х14НЗВ2ФР[4], з яких виготовляють лопатки парових турбін, важконавантажені деталі (диски, вали, стяжні болти), що працюють в умовах підвищеної вологості.
Для роботи при 650...850 °С застосовують сталі марок 40Х9С2, 40Х10С2Н, 45Х14Н14В2М[4], з яких виготовляють клапани автомобільних і тракторних двигунів, трубки рекуператорів, теплообмінники.
Жароміцні сплави на основі нікелю
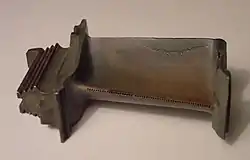
До 1942 року у Великій Британії створено жароміцний сплав німонік-80 (80%Ni — 20%Cr) — перший у серії високожароміцних дисперсно-тверднучих сплавів на нікель-хромовій основі. Творець сплаву — Вільям Гріффітс (англ. Griffiths W.T.)[5]. Ключовими легувальними елементами сплаву німонік-80 були титан (2,5%) і алюміній (1,2%), що утворювали зміцнювальну фазу. Кількісний вміст зміцнюючої γ'-фази у сплаві становив 25…35% за об'ємом[6]. Сплав виявив помітну перевагу за жароміцністю над ніхромами чи спеціальними легованими сталями.
Сплави Nimonic-80 та 80A використовувались в деформованому стані для виготовлення робочих лопаток турбіни одного з перших газотурбінних двигунів «Rolls-Royce Nene» компанії «Rolls-Royce Limited», стендові випробування якого розпочались у жовтні 1944 року. Лопатки турбіни із сплаву Nimonic-80 відрізнялись високою тривалою міцністю за температура 750…850 °C. Хімічний склад наступних марок сплавів типу «німонік» подані у нижче приведеній у таблиці.
Аналогами німоніків у США є сплави Інконель, за ГОСТ 5632-72[7] — це сплави ХН60ВТ (Inconel 600, Inconel 601), ХН56МВКЮ (Inconel 617), ХН75МБТЮ (Inconel 625), ХН60Ю (Inconel 718), ХН70МВТЮБ (Inconel X-750), ХН80ТБЮ, ХН77ТЮ, ХН73МБТЮ тощо.
Тоді ж була виявлена можливість додаткового зміцнення жароміцних сплавів шляхом легування молібденом. Згодом, з цією ж метою почали використовувати добавки таких елементів, як вольфрам, ніобій, тантал, реній та гафній[8]).
Легування
Легувальні елементи у жароміцних сплавах на основі нікелю можна згрупувати наступним чином:
- Елементи, що утворюють з Ni аустенітну -матрицю з гранецентрованою кристалічною ґраткою — Co, Fe, Cr, Mo і W
- Елементи, що утворюють зміцнювальну ' фазу (Ni3X) — Al, Ti, Nb, Ta, Hf. При цьому Ti, Nb і Ta входять до складу фази й зміцнюють її.
- Елементи, що утворюють сегрегації на границях зерен —B, C і Zr.
До карбідоутворюючих елементів належать Cr, Mo, W, Nb, Ta і Ti. Al і Cr, котрі утворюють оксидні плівки, що захищають вироби від корозії.
Сплав | %Ni | %Cr | %Co | %Mo | %Al | %Ti | %Nb | %C | %B | Zr | % ін. елементів |
---|---|---|---|---|---|---|---|---|---|---|---|
Inconel X-750 | 73,0 | 18,0 | - | - | 0,8 | 2,5 | 0,9 | 0,04 | - | - | 6,8% Fe |
Udimet 500 | 53,6 | 18,0 | 18,5 | 4,0 | 2,9 | 2,9 | - | 0,08 | 0,006 | 0,05 | |
Udimet 700 | 53,4 | 15,0 | 18,5 | 5,2 | 4,3 | 3,5 | - | 0,08 | 0,03 | - | |
Waspaloy | 58,3 | 19,5 | 13,5 | 4,3 | 1,3 | 3,0 | - | 0,08 | 0,006 | 0,06 | |
Astroloy | 55,1 | 15,0 | 17,0 | 5,2 | 4,0 | 3,5 | - | 0,06 | 0,03 | - | |
Rene 41 | 55,3 | 19,0 | 11,0 | 10,0 | 1,5 | 3,1 | - | 0,09 | 0,005 | - | |
Nimonic 80A | 74,7 | 19,5 | 1,1 | - | 1,3 | 2,5 | - | 0,06 | - | - | |
Nimonic 90 | 57,4 | 19,5 | 18,0 | - | 1,4 | 2,4 | - | 0,07 | - | - | |
Nimonic 105 | 53,3 | 14,5 | 20,0 | 5,0 | 1,2 | 4,5 | - | 0,2 | - | - | |
Nimonic 115 | 57,3 | 15,0 | 15,0 | 3,5 | 5,0 | 4,0 | - | 0,15 | - | - |
Сплав | %Ni | %Cr | %Co | %Mo | %Al | %Ti | %Nb | %C | %B | Zr | % ін. елементів |
---|---|---|---|---|---|---|---|---|---|---|---|
B-1900 | 64,0 | 8,0 | 10,0 | 6,0 | 6,0 | 1,0 | - | 0,10 | 0,015 | 0,1 | 4,0% Ta |
MAR-M200 | 60,0 | 9,0 | 10,0 | - | 5,0 | 2,0 | 1,0 | 0,13 | 0,015 | 0,05 | 12,0% W |
Inconel 738 | 61,0 | 16,0 | 8,5 | 1,7 | 3,4 | 3,4 | 0,9 | 0,12 | 0,01 | 0,10 | 1,7% Ta, 3,6% W |
Rene 77 | 58,0 | 14,6 | 15,0 | 4,2 | 4,3 | 3,3 | - | 0,07 | 0,016 | 0,04 | |
Rene 80 | 60,0 | 14,0 | 9,5 | 4,0 | 3,0 | 5,0 | - | 0,17 | 0,015 | 0,03 | 4,0%W |
Фазовий склад
До основних фаз жароміцних сплавів належать:
- Гамма-фаза () є матрицею з ГЦК кристалічною ґраткою. У твердому розчині цієї фази міститься значна кількість Co, Cr, Mo, W.
- Гамма-штрих фаза (') утворює частинки преципітату, що також має ГЦК кристалічну ґратку. У цю фазу входять такі елементи, як Al та Ti. Об'ємна частка цієї фази, когерентної до аустенітної матриці є досить великою.
- Карбіди. Вміст вуглецю у сплавах відносно невеликий (0,05…0,2%). Він сполучається з карбідотвірними елементами — Ti, Ta, Hf
- Зерногранична '-фаза. Ця фаза утворюється у вигляді плівки по границях зерен в процесі термічної обробки.
- Бориди Виділяються на границях зерен у вигляді рідкісних частинок.
- Фази топологічно щільно упаковані мають пластинчасту морфологію. Приклад: фази , і фаза Лавеса. Ці фази спричиняють окрихчення матеріалу і є небажаними.
Сплави на основі кобальту
Ще на початку XX століття компанією «Гейнс» (англ. Haynes) були отримані патенти на сплави системи Co-Cr та Co-Cr-W. Ці сплави, що отримали назву «стеліти» використовувались при виготовленні різального інструменту та зносостійких деталей. В 1930-х роках було розроблено ливарний Co-Cr-Mo сплав віталіум (Vitallium®) для зубного протезування. Аналогічний за складом сплав HS-21 став використовуватись десятиліття по тому в турбонагнітачах і газових турбінах. Тоді ж почали використовувати сплав системи Co-Ni-Cr для напрямних лопаток газотурбінних двигунів. У 1943 році було розроблено ливарний сплав системи Co-Ni-Cr-W (X-40), що також знайшов застосування при виготовленні лопаток. У 1950–1970 роки було розроблено нові нікелеві жароміцні сплави, виготовлені шляхом вакуумного плавлення і зміцнювані за рахунок виділення фази '. Це привело до зменшення використання сплавів на основі кобальту.
Особливості жароміцних сплавів на кобальтовій основі
- Температура плавлення у сплавів на кобальтовій основі є вищою. З цієї причини характеристики тривалої міцності є вищими. Ці жароміцні сплави можуть працювати за вищих температур, у порівнянні зі сплавами на основі нікелю чи заліза.
- Високий вміст хрому підвищує стійкість до гарячої корозії.
- Сплави характеризуються підвищеною стійкістю до термічної втоми і мають добру зварюваність.
Монокристалічні жароміцні сплави
У 1970–1980 роках розпочалось використання литих жароміцних сплавів, отриманих методами спрямованої кристалізації й монокристалічних сплавів на нікелевій основі. Застосування цих матеріалів дозволило збільшити міцність і термічну довговічність лопаток газових турбін.
що отримуються методами направленої кристалізації[9]
Сплав | %Cr | %Co | %W | %Mo | %Ta | %Nb | %Ti | %Al | %Hf | %B | %Zr | %C |
---|---|---|---|---|---|---|---|---|---|---|---|---|
MAR-M200+Hf | 9,0 | 10,0 | 12,0 | - | - | 1,0 | 2,0 | 5,0 | 2,0 | 0,015 | 0,08 | 0,14 |
MAR-M246+Hf | 9,0 | 10,0 | 10,0 | 2,5 | 1,5 | - | 1,5 | 5,5 | 1,5 | 0,015 | 0,05 | 0,15 |
MAR-M247 | 8,4 | 10,0 | 10,0 | 0,6 | 3,0 | - | 1,0 | 5,5 | 1,4 | 0,015 | 0,05 | 0,15 |
RENE 80H | 14,0 | 9,5 | 4,0 | 4,0 | - | - | 4,8 | 3,0 | 0,75 | 0,015 | 0,02 | 0,08 |
Сплав | %Cr | %Co | %W | %Mo | %Ta | %Nb | %Ti | %Al | %Hf |
---|---|---|---|---|---|---|---|---|---|
Pratt & Whitney № 1 | 10,0 | 5,0 | 4,0 | - | 12,0 | - | 1,5 | 5,0 | - |
Pratt & Whitney № 2 (3% Re) |
5,0 | 10,0 | 6,0 | 2,0 | 8,7 | - | - | 5,6 | 0,1 |
CMSX-2 | 8,0 | 5,0 | 8,0 | 0,6 | 6,0 | - | 1,0 | 5,5 | - |
SRR99 | 8,5 | 5,0 | 9,5 | - | 2,8 | - | 2,2 | 5,5 | - |
Див. також
Примітки
- Luft.-Forschung, Bd 18(1941), N 8, S. 275–279
- Pomp A., Krisch A. Zur Frage der Dauerstandfestigkeit warmfester Staehle bei 600, 700 und 800 °C. Mitteilungen der KWI fuer Eisenforschung (Abhandl. 400), 1940
- Report on Visit to Germany and Austria to investigate Alloys for Use at High Temperature. BIOS Final Report N 396, London, 1946
- ГОСТ 5632-72 Стали высоколегированные и сплавы коррозионностойкие, жаростойкие и жаропрочные. Марки.
- High-Temperature Alloys // Aviation History. 1947, Oct. 30
- Giamei A. F., Pearson D. D., Anton D. L. Materials Research Society Symposium Proc. 1985, v. 39, pp. 293–307
- ГОСТ 5632-72 Стали высоколегированные и сплавы коррозионностойкие, жаростойкие и жаропрочные. Марки.
- Суперсплавы II / Под ред. Симса, Столоффа, Хагеля. Перевод на русский язык. М., Металлургия, 1995, т 1, стр. 29
- H. K. D. H. Bhadeshia Nickel Based Superalloys Архівовано 25 серпня 2006 у Wayback Machine.
Джерела
- Дурягіна З. А. Сплави з особливими властивостями / З.А. Дурягіна, О. Я. Лизун, В. Л. Пілюшенко. — Л. : Вид-во НУ «Львівська політехніка», 2007. — 236 с.
- Суперсплавы II. Жаропрочные материалы для аэрокосмических и промышленных энергоустановок. — М. : Металлургия, 1995.
- Строение и свойства авиационных материалов. — М. : Металлургия, 1989.
- Лекції про суперсплави на сайті університету Кембриджа.
- Химушин Ф. Ф. Жаропрочные стали и сплавы. — М. : Металлургия, 1969.
Посилання
- Жароміцність та жароміцні металеві матеріали // Енциклопедія сучасної України : у 30 т. / ред. кол. І. М. Дзюба [та ін.] ; НАН України, НТШ. — К. : Інститут енциклопедичних досліджень НАН України, 2001–2020. — ISBN 944-02-3354-X.