Історія доменного виробництва
Історія доменного виробництва — розділ історії металургії заліза, що вивчає виникнення і розвиток доменного виробництва.
Доменне виробництво сьогодні (2021 рік) є основним способом отримання заліза з залізних руд, хоча розробляються і існують також інші способи — безпосереднє виробництво заліза.
Доменна піч була створена суто досвідним шляхом, задовго до будь-якого пояснення процесів, що відбуваються в ній. Виникнення доменного виробництва відносять звичайно до ХІІІ — середини XIV століть. В той же час найелементарніше пояснення доменного процесу було запропоноване лише у другій половині XIX століття.[1]
Назва «доменна піч» походить від старослов'янського слова «дмети», тобто дмути, подавати дуття. Таким чином, «доменна піч» означає «дуттьова піч».
Щоб зрозуміти масштаби розвитку доменного виробництва достатньо порівняти масштаби світового виробництва чавуну за останні 200 років. 1820 року світове виробництво чавуну становило 1 млн т,[2] світове виробництво чавуну сьогодні становить приблизно 1,15 млрд т чавуну (2016 рік),[3] тобто зросло за цей період у понад як 1000 разів. Достатньо сказати, що сучасні найбільші за об'ємом доменні печі виплавляють до 10 — 11 тисяч тонн чавуну на добу, для виробництва якого потрібно майже вдвічі більше залізорудної сировини і флюсу і біля 5-ти тисяч тонн палива.
Металургія заліза до виникнення доменного виробництва
Хоча сьогодні доменне виробництво є основним способом отримання заліза з залізних руд, воно було далеко не першим в історії металургії заліза. Доменне виробництво виникло приблизно через 2,5 тис. років після першого знайомства людини з залізом, отриманим із руди.
Відкриття заліза людиною
Перше залізо, з яким мала справу стародавня людина було самородне залізо — метеоритне і телуричне. Згодом, можливо випадково, людина навчилася отримувати залізо з залізних руд. Освоєння виплавки заліза з руд стало великим досягненням людства, яке згодом викликало бурхливе зростання виробничих сил. Більш високі якості заліза і сталі, а також загальнодоступність залізних руд (на відміну від відносно рідкісних покладів міді і особливо олова залізні руди, хоча й низького ґатунку (бурі залізняки) трапляються майже всюди) і дешевизна нового металу забезпечили витиснення ним бронзи і каміння, що залишалося важливим для виробництва знарядь праці і за бронзової доби.
Припускається, що відкриття способів отримання заліза з руд відбулося незалежно у різних частинах світу у різних народів. Вперше людина навчилася отримувати залізо з залізної руди у західній частині Азії у 2-му тисячолітті до н. е.[4][5]
Спочатку для отримання заліза з руд, можливо, використовували багаття. У ньому можна було отримати залізо лише з легковідновлюваної руди. В окремих випадках у великих багаттях, що довго горіли, первісна людина несподівано створювала умови, необхідні для відновного процесу. Якщо в середину такого великого багаття потрапляли шматки легко відновлюваного залізняку, то він міг перетворюватися на залізо. Так, мабуть, людина повільно і наполегливо вчилася одержувати і застосовувати залізо[6][7].
Одними з перших агрегатів для отримання заліза були тиглі і «вовчі ями». Значно прогресивнішим від цих способів отримання заліза було отримання заліза сиродутним способом у сиродутних горнах.
Сиродутний процес
Сиродутний процес протягом більше тисячі років — від його виникнення до появи доменного виробництва у XIV столітті — на більшій території світу, зокрема в Європі, був єдиним способом отримання заліза з руди. Першими почали отримувати залізо сиродутним способом хатті — народ в Малій Азії — у 2 тисячолітті до н. е.[8]
Спочатку сиродутний процес здійснювався у невеличких сиродутних горнах заввишки 1 м, потім у більших за розмірами сиродутних печах, що сягали висоти кількох метрів, які в літературі називаються сиродутними горнами або сиродутними печами. Термін «сиродутний» отримав свою назву у XIX столітті після застосування в доменній плавці нагрітого дуття замість холодного (тобто «сирого»). Під час сиродутного процесу залізо отримували у тістоподібному стані — у вигляді так званого губчастого заліза (криці, лупи).
По мірі вигорання вугілля у піч завантажували суміш руди з деревним вугіллям. Плавка продовжувалася до тих пір поки не було витрачено певну кількість руди, після чого випускали з нижньої частини горну шлак і випалювали залишки вугілля. На цьому плавка завершувалася, стінка горну розбиралася і з нижньої частини виймали розжарений шматок губчастого заліза. У шпаринах криці містився шлак. Крицю проковували під молотами, при цьому з неї видалявся шлак, а шматок заліза ставав більш суцільним, після чого вона ставала придатною для виготовлення виробів. За одну плавку у горні залежно від його розмірів отримували від 8 до 80 кг заліза. Тривалість плавки становила 2 — 2,5 години. Нагрів горну до 1000—1150 °C був достатнім для відновлення заліза, але недостатнім для його плавлення. Європейським металургам до Середньовіччя, тобто до появи доменного виробництва, залізо у розплавленому (рідкому) стані не було відоме. Варто зазначити, що чавун у рідкому стані був відомий у стародавньому Китаї, де його виплавляли у маленьких печах з дутьовими ящиками.
Сиродутне го́рно і сиродутна піч
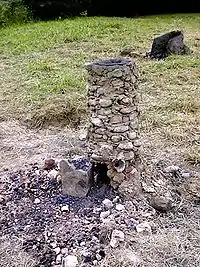
Сиродутні горна влаштовували прямо на землі, звичайно на схилах пагорбів і ярів. Вони мали вид труби, заповненої деревним вугіллям і залізняком. Вугілля запалювали, і вітер, що дув у схил, підтримував горіння. Якщо на перших сиродутних горнах повітря потрапляло до нього самопливом, то згодом на них почалося використання міхів, якими роздмухували вогонь у сиродутному горні.
Внаслідок вдосконалення сиродутне горно перетворилося у більшу за розмірами сиродутну піч, яка згодом перетворилася у печі, відомі у різних народів під назвами штукофен, блауофен, домниця.
Каталонське го́рно
На півдні Європи, у Каталонії, внаслідок вдосконалення сиродутного горну з'явилися сиродутні горни, відомі під назвою каталонських. Вони являли собою невелике поглиблення квадратної або прямокутної форми (завширшки і завдовжки близько 70-80 см, глибиною 40-50 см). На відміну від звичайних сиродутних горен, у каталонських горнах процес був непереривчастий і тому вони були продуктивнішими.
Домниці
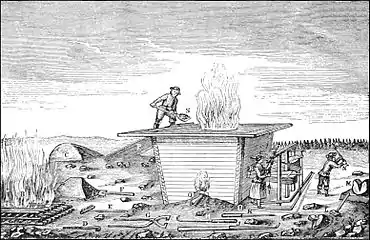
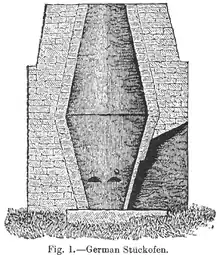
Протягом багатьох сторіч виробництво заліза у сиродутних горнах і потім у більших за розмірами сиродутних печах було єдиним способом отримання заліза з руд. Однак зрослі вимоги суспільства вимагали шукати шляхи збільшення продуктивності виробництва заліза, бо продуктивність сиродутної печі була низькою. Це призвело до збільшення сиродутних печей, переважно у висоту, і кількості повітря, що подавалося в неї. Наслідком цих конструктивних змін стало зниження температури у горішніх і підвищення її у нижніх частинах печі, що викликало докорінні зміни процесу, що відбувалися в печах. Ці зміни завершилися перетворенням сиродутного горну (печі) у цілком новий агрегат — домницю. Домниця разом з крицею, залежно від того, як відбувався процес, могла давати вже й новий продукт — чавун — рідкий продукт плавки, що витікав з печі разом зі шлаком. Такі печі почали будувати у Європі у XIII столітті. У німців такі печі звалися штюкофенами (або вольфофенами), у французів «forneau a loupe», у англійців «high blooomery-furnace», у шведів осмундівськими, або селянськими.
Подальший розвиток домниці перетворив її у доменну піч, продуктом якою був один лише чавун.
Середньовічні металурги не знали ні властивостей чавуну, ні можливостей його застосування. Чавун містив не 0,1 % вуглецю, як криця, а до 4 % вуглецю і через це на відміну від криці був крихким — його неможливо було кувати. В той же час вони помічали, що створення чавуну веде до великого скорочення виходу криці. Тому отриманий при відхиленні сиродутного процесу від норми чавун спочатку вважали браком. Лише згодом його почали використовувати для виготовлення відливок, а потім повторно переплавляти з рудою, випалювати вуглець і отримувати крицю, а вже з неї — м'яке ковке залізо. Для цього використовувалися кричні горна, а процес називався кричною переробкою.
Таким чином, замість безпосереднього отримання заліза з руди у сиродутному горні або сиродутній печі, тобто одноступеневого процесу, з'явився двоступеневий процес — отримання чавуну у доменній печі і подальша переробка його на ковке залізо у кричному горні, а пізніше — на сталь у пудлінговій печі (1774, Г. Корт), конвертері (1856, Г.Бессемер), мартенівський печі (1864, П. Мартен).
Перехід до двоступеневого отримання сталі мав величезну економічну ефективність. Весь подальший розвиток металургії проходив як вдосконалення цього двоступеневого способу виробництва сталі, який дотепер залишається найекономічнішим і найпродуктивнішим.[1]
Порівняння процесів у сиродутному горні і у домниці
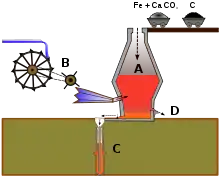
Внутрішній об'єм горна заповнювався шарами залізної руди і деревного вугілля. У нижній частині горна відбувалося горіння палива. Гази, що виділялися при горінні палива, підіймалися вгору, проходячи крізь стовп шихти. При цьому вони взаємодіяли з залізною рудою, нагріваючи її й відновлюючи оксиди заліза.
Нагрівання горну до 1000—1200 °C було достатнім для відновлення заліза, але не достатнім для його плавлення. Відновленні зерна напіврозплавленого заліза злипалися, зварювалися, утворюючи губчасту масу. Відразу ж починався процес навуглецювання металу при контакті його з оксидом вуглецю СО і вуглецем С деревного вугілля[1].
Через те, що сиродутні горна і сиродутні печі були невеликого об'єму, руда в них швидко нагрівалася і, не до кінця відновлена, плавилася. Залізо, що не встигло відновитися, переходило у шлак. З всієї маси шихти у металеву крицю встигало перейти не більш як 60 — 70 % заліза. Вся інша маса заліза (30 — 40 %) не встигала відновитися з руди до його плавлення й залишалася у шлаку у з'єднанні фаяліту Fe2SiO4 ((2FeO)·SiO2). Залізистий фаялітовий шлак легко плавиться.[1]
У нижній частині горна навуглецьоване губчасте залізо потрапляло у масу рідкого залізистого шлаку, що містив 50 — 55 % монооксиду заліза FeO. Навуглецьоване залізо реагувало з цим шлаком, в наслідок чого основна частина розчиненого в залізі вуглецю вигорала за реакцією: C + FeO = Fe + CO.
Інтенсивне зневуглецювання заліза шлаком призводило до отримання продукту, що містив не більш як 0,5 % С (частіше <= 0,3 %). Такий продукт, маючи температуру плавлення не нижче 1400 °C не міг плавитися у горні, в якому максимальна температура не перевищувала 1200—1250 °C.
Шлаки періодично випускалися з сиродутного горна і на поду горна залишалося залізо.
Нагріті до тістоподібного стану пластинчасті часточки заліза, злипаючись і зварюючись на поді горна, утворювали шпаристу грудку губчастого м'якого заліза — крицю, просякнуту шлаком. У такому стані його гарячим витягали з печі, для чого перед цим ламали її стінку. Крицю тут же обробляли молотками на ковадлі, під час чого з її шпарин видалявся шлак. Залишалося лише залізо, придатне для виготовлення виробів.
Через те, що ці процеси інтенсивно проходять вже при температурі 700 °C, а процеси шлакоутворення можуть відбуватися тільки при 1100—1200 °C, то вони розділилися — почали проходити у різних частинах печі: на горі проходило відновлення руди, а знизу — плавлення шлаку. Це призвело до того, що вміст FeO у шлаку (на момент його плавлення) різко знизився, вигорання вуглецю з відновленого навуглецьованного заліза зменшилося. Таким чином, залізо залишалося навуглецьованим. Це різко знизило температуру його плавлення, яка тепер становила 1200 °C. Розплавлене навуглецьоване залізо, тобто чавун, стікав у нижню частину печі як і шлак.
Коли металурги відкривали льотку сиродутної печі для випуску шлаку, разом з рідким шлаком з печі витікав і рідкий чавун.
Так лише одна конструктивна зміна сиродутної печі — збільшення її розмірів у висоту — призвело до появи цілком нового продукту — чавуну.
Залізо насичувалося вуглецем, тобто перетворювалося на чавун. Це різко знижувало його температуру плавлення (порівняно з крицею). Розплавлений чавун стікав у низ печі і випускався з неї у рідкому стані.
Зростання потреби в металі приводило до збільшення об'єму печей і, головним чином, за рахунок збільшення їхньої висоти. Збільшення поперечних розмірів агрегатів було неможливим у зв'язку з малопотужністю повітродуттєвих засобів. У міру збільшення висоти зростала область помірних температур, де протікає відновлення оксидів газами. В результаті шлак збіднювався оксидами заліза, зменшувалася його дія окислення на вуглець, розчинений в металі. Збільшення вмісту вуглецю в металі знижувало температуру його плавлення і забезпечило перехід твердої губчастої маси — криці — до рідкого розплаву.
Створення рідких продуктів плавки сприяло переходу на безперервний процес виплавки металу. Відпала необхідність зупинки печі для витягу криці. Поліпшивши економічну сторону процесу за рахунок встановлення його безперервності, істотно змінили якість одержуваного продукту — замість ковкого заліза, що служить безпосередньо для задоволення потреб людини, одержували чавун — сплав, що не піддається обробці тиском. Для повернення до м'якого ковкого стану тепер необхідно видалити надмірний вуглець з металу.
У період, що безпосередньо передував переходу від сиродутного до доменного виробництва, виготовлялася криця масою 150 кг, а на добу їх одержували 3 — 4 штуки, тобто продуктивність печі становила до 500 кг/добу. Виробництво більш крупної криці займало більше часу, так що добова продуктивність істотно не могла бути збільшена. Висота печей у той час становила 3,5 — 5 метрів.
Перехід від домниць до більш високих доменних печей міг відбутися тільки за умови збільшення потужності повітродувних засобів.
Пусту породу залізної руди без спеціальної добавки — флюсу, за рідкісним виключенням, не можна перетворити на рідкий шлак за відсутності в ньому великої кількості оксидів заліза. В доменному процесі, безперервність і висока продуктивність якого вимагає отримання металу в рідкому стані, майже завжди необхідно застосування флюсів. Проте час початку застосування флюсу точно не встановлений.
Перехід від періодичного сиродутного процесу до безперервного доменного з отриманням металу і шлаку в рідкому вигляді вимагав відповідного підбору шихти і тому скоївся не відразу. Припускається, що був період, коли метал одержували рідким, а шлак з печі доводилося вигрібати. Перший час в доменних печах виплавляли чавун головним чином для виготовлення відливок, тобто з деяким вмістом кремнію, очевидно, значно нижчим, ніж в сучасних ливарних чавунах. Потрібно було декілька століть, щоб розробити прийоми переділу чавуну в сталь в кричних горнах і встановити, що отримання рідкого вуглецевого металу в домницях і окислювальний переділ його в горнах вигідніше за сиродутний процес відносно продуктивності, витягу заліза і витрати палива, тому неможливо вказати, в якому саме сторіччі виникло доменне виробництво. Аж до середини XVI століття доменне виробництво не отримало широкого розповсюдження в Західній Європі.
Виникнення доменного виробництва
Точних даних щодо місця й часу появи перших доменних печей немає. Найпоширенішою є думка про те, що перші доменні печі з'явилися в Європі у XIV столітті.[9][10][11] Вважається, що перші доменні печі в Європі з'явилися приблизно 1340 року на території теперішньої провінції Намюр (тепер у складі Бельгії).[11] Звідти доменне виробництво розповсюдилося у Нормандію і далі у Англію в Сассекс (приблизно 1490 року).[12] Перший опис виплавлення чавуну міститься у працях французького єпископа Генриха з Пуатьє у 1371 році.
Разом з тим, на основі археологічних досліджень існує думка, що виробництво чавуну у доменних печах могло існувати ще приблизно у 1150—1350 роках у Швеції.[11][13] Загалом, виходячи з археологічних досліджень, деякими істориками називаються три регіони в Європі, де з'явилися перші доменні печі — Лаппхюттан (1150—1350 роки) (біля комуни Нурберг) у Швеції, Дурстел (Dürstel) (біля комуни Лангенбрук) у Швейцарії, Меркіш (1290—1395 роки) у Зауерланді в Німеччині.[14]
Процес у доменній печі докорінно був відмінний від процесу у сиродутній печі.
Доменні печі не відразу витіснили виробництво заліза у сиродутних горнах. Через можливість виробництва у печах типу блауофена і домниць або губчастого заліза або чавуну вони у де-яких регіонах Європи збереглися до кінця XIX століття.[15] Крім того, виробництво чавуну у доменних печах зростало повільно через те, що витрати на виробництво домен значно перевищували витрати на будівництво інших металургійних печей, доменні печі потребували потужніших повітродувних засобів. Різкий стрибок у розвитку доменного виробництва і повсюдне витіснення доменними печами інших агрегатів, що використовувалися для отримання заліза з руд, відбувся після вдосконалення дуттьових засобів, завдяки якому стало можливим суттєве збільшення висоти і продуктивності печі. Це відбулося під час промислового перевороту на зламі XVIII—XIX століть.
Розвиток будови доменних печей
Профіль доменної печі
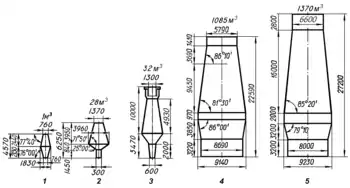
Профіль перших доменних печей нічим не відрізнявся від профілю домниць (штукофенів), являючи собою два зрізаних конуси, з'єднаних поміж собою широкими основами. Доменники помітили, що після певного часу роботи такої печі спостерігалися підвищення продуктивності печі і зниження витрати палива. Під час зупинки і видувки печі вони бачили, що її вогнетривке мурування (внутрішнє футерування) частково випалювалося і об'єм печі зростав. Збільшення продуктивності і зменшення витрати палива, які помітили доменники пояснюються цим збільшенням об'єму печі і часу контакту газу з шихтовими матеріалами, що створювало найкращі умови для процесів відновлення заліза і віддачі тепла газу шихтовим матеріалам. Тому розміри робочого простору печі почали збільшувати. Однак збільшенню висоти печі й діаметра горна перешкоджала мала потужність повітродувних засобів, розширенню колошника — ручне завантаження шихти.
Об'єм печі збільшували переважно шляхом розширення розпару. Внаслідок цього виник профіль з непропорційно широким розпаром. У таких печах погано використовувалися гази, бо вони обробляли тільки центральний стовп матеріалів, а на периферії розпару шихтові матеріали не брали участі у процесі. З початком використання парових машин і вдосконаленням повітродувних засобів, а також з переходом від використання деревного вугілля на міцніше від нього мінеральне паливо почали збільшувати висоту печей.
Низька продуктивність і неекономічна робота печей з широким розпаром і вузьким горном примусила доменників збільшити діаметр горна. Це призвело до збільшення продуктивності доменних печей і зниження питомої витрати палива внаслідок поліпшення умов опускання шихти у заплечиках і розподілу газового потоку у шахті печі. Тому почали вважати, що діаметр горна, незалежно від інших розмірів профілю, є єдиною величиною, що визначає продуктивність доменної печі.
Побоювання погіршити розподілення матеріалів при збільшенні діаметра колошника довгий час стримувало збільшення його розміру. Досвід експлуатації таких печей показав, що продуктивність їхня не збільшувалася пропорційно площі поперечного перетину горна. Це було спричинене тим, що вузький колошник перешкоджав проходженню великої кількості газів, що обмежувало продуктивність печі. Погана робота печей з горном великого діаметра і колошником малого діаметра призвела до збільшення діаметра колошника.
Сучасні доменні печі характеризуються профілем з пропорційними розмірами окремих елементів, що забезпечує високу продуктивність при низькій питомій витраті палива.[1] (с. 304—305)
Розвиток розмірів доменних печей
Якщо у XV—XVI століттях висота доменних печей становила близько 4, 5 м, то у XVIII столітті печі споруджувалися заввишки 10 — 13 м, а добова продуктивність їхня збільшилася з 1,6 до 16 — 17 т. За паливо для доменних печей використовувалося деревне вугілля. Воно було добрим паливом, але механічна міцність вугілля була недостатньою, що не давало можливості будувати доменні печі заввишки більш ніж 16 — 18,5 м.[1]
- Розвиток розмірів і профілю доменних печей.
- Доменна піч XVIII століття. Піч ще відносно невеликого розміру. Для завантаження такої печі було достатньо лише миски.
- Доменна піч другої половини XIX століття. Розміри печі значно збільшилися. Для завантаження печі потрібні вже великі ємності.
Розвиток конструкції доменної печі від її появи до наших часів відбувався перш за все шляхом збільшення її розмірів. Сучасна доменна піч має висоту понад 30 м.
Якщо на початку 1900-х років працювали печі з корисним об'ємом 300—400 м³, то у 1920-х роках він досяг 1000 м³.
Перші радянські печі були об'ємом 930 м³. Треба відзначити, що доменні печі такого об'єму були на окремих заводах у Російській Імперії за часів царату. [джерело?] 1938 року були збудовані дві найбільші на той час доменні печі об'ємом 1300 м³. 1974 рік — піч об'ємом 5000 м³. У 2011 році у Південній Кореї на Кван'янському металургійному комбінаті було задуто найбільшу в наш час (2017) доменну піч об'ємом 6000 м³.[16][17]
Конструкція доменних печей
Будова доменних печей з часу їхнього виникнення й до останнього часу неперервно протягом століть розвивалася. Це стосується як безпосередньо самої печі, так і різноманітних її елементів і обладнання.
Внутрішнє мурування — футерування шахти — домен, збудованих до середини XIX століття, робилося з вогнетривкого матеріалу і оточувалося ззовні масивним кожухом з плитняку або червоної цегли, або каміння. На під і стінки гону використовували каміння вогнетривкої гірської породи.
Для спроможності шахті розширятися від нагріву поміж кожухом і футеруванням залишався порожній простір, який заповнювався поганим провідником тепла: піском, вугільним сміттям тощо.
У нижній частині печі у зовнішньому муруванні навпроти тих місць, де мав би бути доступ до внутрішніх стін, виводилися склепіння, їх ніколи не було менше двох: одне фурменне, для підводу дуття, а інше робоче — для випуску чавуну. Для міцності зовнішнє мурування скріплювалося металевими обручами.[15]
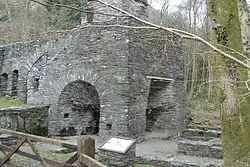
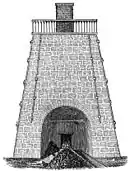
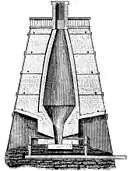
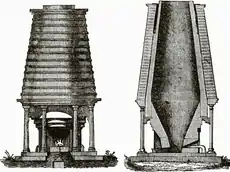
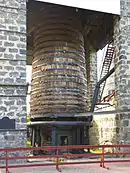
Домни, що з'явилися в середині XIX століття, різко відрізнялися від тих, що були збудовані до того. Замість колишнього зовнішнього кожуху на всю висоту домни, в цей час він робився тільки до розпару, вся же шахта печі містилася у циліндрі з казанового заліза, при цьому футерування стало спиратися на колонах і замість колишніх темних склепінь навколо горну всюди світло й доступ вільний.[15]
Перші три таких печі були збудовані у Франції у Еанж до 1849 року (можливо, 1845 року). Ці печі були заввишки 14 м, мали діаметр найширшої частини 4,88 м, діаметр колошника — 2,22 м. Вони були збудовані спеціально для роботи на коксі і за існуючими даними працювали чудово.[18]
До кінця XIX століття для мурування печей почали використовувати не каміння, а вогнетривку цеглу.[15]
Далі ця конструкція печей — залізний кожух зовні, колони тощо — була розвинута у XX столітті.
Повітродувні засоби
Один з основних факторів доменної плавки — дуття. Збільшення розміру агрегатів вимагало вдосконалення повітродуттєвих засобів. Тієї кількості дуття, потрібної для невеликого сиродутного горна, було недостатньо для шахтної печі. Прямим слідством цього з'явився розвиток повітродувних засобів: використання замість зусиль людини зусиль тварин, енергії водяного колеса.
До 1760 року на домнах в ролі повітродувних засобів використовувалися клиноподібні міхи, які приводилися у дію через водяні колеса енергією падаючої води. Їх завжди було не менше як два — для забезпечення безперервної подачі дуття: поки один міх розтискався і набирався повітрям, інший стискався і повітря, що виходило з нього, через повітропроводи потрапляло у піч.[15]
Перші циліндричні міхи, винайдені британським механіком Джоном Смітоном, були встановлені на заводі «Карон» у Шотландії у 1760 році.[15][19][20] Вони складалися з циліндра і поршня. Поршень був закріплений на штоку. Циліндричні міхи приводилися в дію водяним колесом. Починаючи з 1778 року почали широко використовувати для них парові машини. Використання циліндричних міхів дозволило збільшити кількість подаваного у доменну піч повітря й, відтак, збільшити розміри доменних печей і більш широко використовувати мінеральне паливо — кам'яне вугілля й кокс. У 1890-х роках в Англії були величезні міхи, що забезпечували дуттям відразу від 8 до 10 великих домен. Прилад цей давав від 1274 до 1416 м³ (45000 — 50000 куб. футів) повітря на хвилину.
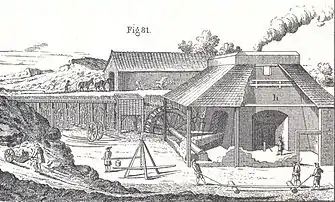
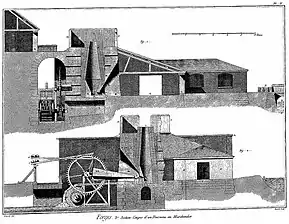
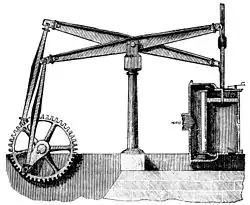
Сьогодні для подачі повітря у доменну піч використовуються спеціальні турбоповітродувки, які розміщуються у окремому цеху і повітря від яких до доменної печі подається по повітропроводах. Сучасні повітродувки мають продуктивність у кілька тисяч кубометрів повітря на хвилину з тиском у кілька атмосфер.
Повітронагрівачі
.png.webp)
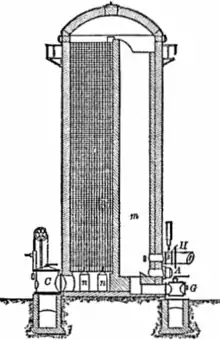
1829 року на заводі «Клайд» біля Глазго (Шотландія) винахідник Дж. Нілсон вперше в історії доменного виробництва використав нагріте дуття. Його повітронагрівач являв собою піч, в якій були прокладені чавунні повітропроводні труби у Л-подібній формі у кілька рядів. У печі спалювали паливо і гарячі продукти горіння віддавали своє тепло трубам, а ті — повітрю, що проходило по нім від повітродувних засобів до печі.
1832 — для нагрівання дуття почали використовувати колошниковий газ.
1835 року у Вюртемберзі на заводі Вассер-альфінген було поставлено апарат, що став прототипом всіх подальших змін повітронагрівачів такого типу.
1857 року англійський інженер Е. Каупер запропонував повітронагрівач принципово нової конструкції. Його повітронагрівач працював за принципом регенерації. Гарячі продукти горіння палива проходили крізь клітки, викладені з цегли — насадку й нагрівали її до високої температури — цегла насадки від нагріву ставала червоною або навіть білою. Після того, як насадка була достатньо прогріта, її припиняли нагрівати і через неї пропускали холодне повітря. Повітря нагрівалося, а насадка остуджувалася. Через певний час, коли насадка остигала, повітря пропускали через інший повітронагрівач, а цей ставили на нагрів — у ньому знову спалювали паливо і нагрівали насадку.
Ці дві принципово різні системи повітронагрівачів конкурували поміж собою до кінця XIX століття. Існували різновиди цих повітронагрівачів. Зокрема, були відомі повітронагрівачі конструкції 1835 року у Вюртемберзі на заводі Васер-альфінгене, а також англійського інженера Джона Плейера (John Player)[23]
Існували різні конструкції й апаратів регенеративного типу — власне Каупера, англійця Вітвеля (Thomas Whitwell), американця Кеннеді, системи Гордона-Каупера-Вітвеля, Массіка-Крукса (Massick & Crookes Stove), Форда-Монкера (Ford & Moncur Stove)
Наприкінці XIX століття конкурували переважно системи Каупера і Вітвеля. У повітронагрівачах Вітвеля повітря йшло як по одній трубі, кілька разів міняючи свій напрямок, а у Каупера розділявся на багато струменів — проходив по багатьох трубках у одному напрямку. На кінець XIX століття суперничали дві системи повітронагрівачів — Вітвеля й Каупера, що могли нагрівати повітря до 800 С.
Уперше апарат Вітвеля було встановлено на заводі Thornaby Iron Works у місті Скотон-он-Тіс у Англії 1865 року.[24] У США його апарат вперше було встановлено 1875 року.[23]
Відкрита передня стінка
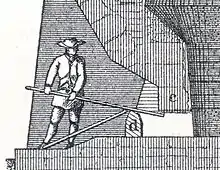
До 19 століття включно доменні печі будувалися з відкритою передньою стінкою — ця конструкція також називалася «відкриті груди». У домни передня стінка починалася не з самого поду, а з рівня фурм, таким чином між нижнім каменем передньої стінки — темпелем (tympe, Tumpel, tymparch) — і подом на всю ширину й висоту нижнього горну (металоприймача) залишався отвір. Навпроти цього отвору ззовні, на відстані приблизно 45 см від передньої стінки ставили пороговий камінь — поріг, таким чином між темпелем і порогом залишалася щілина, через яку ломом і коцюрбою зручно було відчищати металоприймач. Поріг ставився на місце після просушки домни, при її задувці. Чавун і шлак випускали з печі через випускний отвір у порозі, який закривали спеціальною глиною або піском.
За пропозицією Люрмана домни почали робити з закритими передніми стінками.[15]
Завантажувальний пристрій
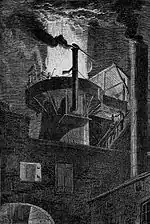
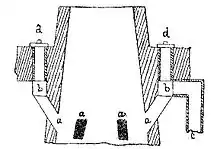
a — отвори в стінці печі, b — канал, з яким з'єднані отвори a, c — труба, з якою з'єднаний канал b.
Від моменту появи доменних печей до першої половини 19 століття колошник доменних печей був відкритим. Через нього у піч завантажували шихту, а доменний (колошниковий) газ, що утворювався в печі, виходив просто у атмосферу.
Коли стало зрозумілим, що доменний газ можна використовувати як паливо, його почали відводити з печі по спеціальних каналах до місць використання, але колошник як і раніше залишався відкритим. Найпростіший спосіб вловлювання газів (за Вассер-альфінгенським способом) полягав в тому, що нижче колошника, однак не більш як 1/3 всієї висоти домни, робили у стінці печі кілька отворів, з'єднаних з каналом, у який входять гази, що підіймаються біля стінок, від каналу гази потрапляли у трубу, якою відводилися від печі. Через те, що колошник залишався відкритим, то в такий спосіб вловлювали тільки частину газів, тому цей спосіб замінили привішеним залізним циліндром з кришкою (ковпаком), але виявилося, що циліндр швидко перегорає і, крім того, під час засипання шихтових матеріалів гази мало вловлюються.[15]
Крім того, закритий колошник не дозволяв регулювати розподіл матеріалів у печі. Доменники здавна знали, що продуктивність печі залежить від часу контакту газів, що йдуть вгору з низу печі до колошника, з грудками шихти, що спускаються вниз. Через те, що більшість газу проходить там, де опір менший, а саме біля стінок печі, то мілкі грудки шихти намагалися завантажувати по краях печі, а великі шматки у центр. Такий розподіл матеріалів забезпечували при ручному завантаженні матеріалів у піч через відкритий колошник.[26] Стор. 152.
Засипний апарат системи Паррі
З'явилася думка, що на колошнику доменної печі має бути встановлено такий пристрій, який забезпечував би рівномірний розподіл шихти при завантаженні у піч і не допускав би виходу газу через колошник.
1850 року такий пристрій сконструював британець Джордж Паррі, працівник Еббу-Вейльського металургійного заводу, що в Уельсі. Засипний апарат системи Паррі являв собою лійку (чашу), закриту знизу конусом. Він виконував відразу роль газового затвору, що запобігав виходу газу через колошник, і засипного апарату, що завантажував й розподіляв матеріали в печі. На колошнику доменної печі з завантажувальним пристроєм системи Паррі матеріал вручну завантажувався у лійку й під час опускання конусу скочувався по його поверхні до стінок доменної печі. При цьому дрібні грудочки шихти залишалися там, де впали, а великі грудки скочувалися до центру печі. Газ відводився з доменної печі через бічні канали шахти печі. Початкова конструкція засипного апарату системи Паррі не могла повністю задовольнити поставленим вимогам, однак ця конструкція була проста, надійна і зручна в експлуатації. Засипний апарат системи Паррі мав низку недоліків. Неможливо було вирівнювати насип вугілля, крім того через те, що газова труба була розташована у самої лійки, то при низькому опусканні насипу зовнішнє повітря легко могло проникнути у газову трубу, наслідком чого міг бути вибух, ланцюг апарату легко перегорав, причому конус падав у домну.[15]
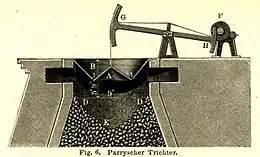
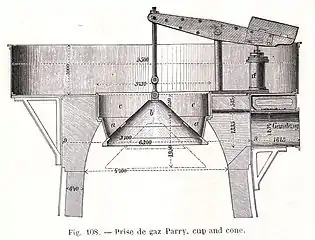

Засипні апарати інших систем
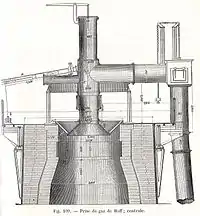
Ланген, намагаючись позбутися цих недоліків, розробив складний прилад, що не мав широкого вжитку. Являв собою лійку, закриту згори колоколом.
В наступні роки було запропоновано досить багато конструкцій засипних апаратів. У Німеччині були створені апарати системи Гоффа й Лангена.
Апарат Гофа подібний до апарату системи Паррі, але мав центральний газовідвод.
У Швеції інженер Шарлевіль сконструював засипний апарат, що був розповсюджений на деревновугільних доменних печах. Складовими частинами засипного апарату системи Шарлевіля є нерухома лійка з конусом і рухоме кільце трикутного перерізу, підвішене на штангах. При опусканні кільця матеріал зсипається одночасно до стінок і до осі доменної печі.
Однак всі засипні апарати були значно складнішими за конструкцією й менш надійними, ніж апарат Паррі. Тому у подальшому відбувалося вдосконалення саме цього апарату. Він досі (2013 рік) використовується на багатьх доменних печах світу.
Двоконусовий завантажувальний пристрій
Спочатку було додано другий малий конус з лійкою, розташований над великим нижнім конусом. Внаслідок було досягнуто повне усунення витоку газу через колошник, тому що при відкриванні одного конусу інший залишався зачиненим і навпаки. Але засипний апарат з двома конусами не усував нерівномірність у розподіленні матеріалів в печі, що виникала внаслідок вивантаження скіпів з шихтою на один бік лійки малого конусу. Ця нерівномірність в розподіленні матеріалу передавалася потім на нижній конус і далі у піч. Було запропоновано кілька конструкцій розподільчих пристроїв, які мали на меті рівномірно розподіляти матеріал по перерізу печі. Одним з найперших пристроїв був пристрій системи Кеннеді, що являв собою дві вузькі високі воронки, між якими встановлено кільце, меншого ніж кільце, діаметра. Шихта з верхньої лійки, проходячи повз кільце, перемішується і потрапяє у нижню лійку.
Обертові розподільники шихти
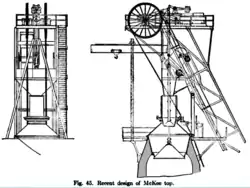
Потім з'явилися системи з обертальною горішньою лійкою. Одним з перших розподільників з горішньою обертовою лійкою був розподільник системи Брауна. Але всі розподільники були витіснені обертовим розподільником, створеним американським інженером Артуром Гленном Мак-Кі (1871—1956) з міста Клівленду (птент № 864798, 1907 року). У розподільнику системи Мак-Кі малий конус разом з лійкою обертається спеціальним електроприводом, що дозволяє рівномірно розподіляти матеріали. Великий й малий конуси, підвішені на штангах до балансирів, приводилися у дію від пневматичних циліндрів. Так була створена початкова конструкція апарату, що використовується на доменних печах досі (2013 рік).
У Російській Імперії перший розподільник шихти системи Мак-Кі був встановлений на одній з доменних печей у 1913 році.[26]
Ливарний двір
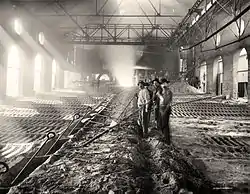
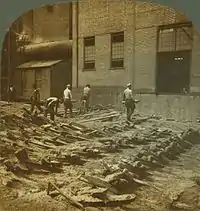
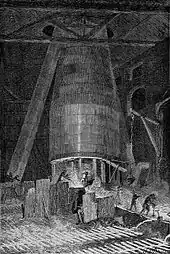
З моменту виникнення доменного виробництва і до кінця XIX століття, коли продуктивність доменних печей була не дуже високою, чавун під час випуску з печі випускали на ливарний двір, а шлак на спеціальний шлаковий майданчик (шлаковий двір), розташовані безпосередньо біля печі на землі. Чавун, що випускався з доменної печі, розливали по жолобках у піскові форми або у спеціальні виливниці. У цих формах чавун застигав у вигляді довгих плиток вагою приблизно по 30 або 40—80 кг кожна. Для скорішого охолодження бабок (чушок) їх поливали водою. Остиглий чавун витягали з форм і у візках відправляли для подальшої переробки у інші цехи. Таким чином на прибирання чавуну і шлаку витрачалося багато часу і фізичної праці. Це стримувало зріст продуктивності доменних печей.
На зламі XIX і XX століть продукти плавки під час випуску почали розливати по ковшах. Чавун розливали у чавуновози, шлак — у шлаковози. Так було вирішено проблему швидкого прибирання чавуну і шлаку. Крім того, можливість перевезення рідкого чавуну дозволила використовувати теплоту рідкого гарячого чавуну у сталеплавильних печах, що дозволило зменшити час і зайві витрати палива на процеси переробки.
З початком використання чавуновозних і шлаковозних ковшів ливарний двір разом з доменною піччю був піднятий над рівнем нульової позначки, щоб чавун і шлак, випущені з печі, могли по жолобах стікати у ковші, встановлені на залізничних коліях під ливарним двором.
Розвиток технології доменного виробництва
Паливо доменних печей
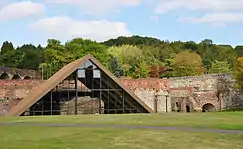
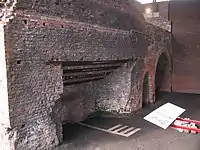
До XVIII століття єдиним паливом для доменних печей слугувало деревне вугілля. На його випал йшла велика кількість деревини, що призводило до вирубки лісів. Крім того, деревне вугілля витрачалося й на подальшу переробку чавуну на ковке залізо у кричних горнах. З ростом об'ємів виробництва металу, все більше вирубувалося лісів.
У Англії виникло побоювання, що розвиток металургії приведе до винищування лісів. У 1558 році королева Єлизавета спеціальним указом обмежила застосування деревного вугілля для потреб металургії. Лише декілька графства зберегли право користуватися деревним вугіллям для виробництва заліза, в решті місць це було найстрогіше заборонено. У зв'язку з нестачею деревного вугілля виплавка чавуну в Англії в 1740 році склала всього 17,3 тис. т, хоча до цього вона становила 180 тис. т, а число доменних печей скоротилося на три чверті.
На початку XVII століття почалися пошуки способів заміни дефіцитного деревного вугілля кам'яним, багатющі запаси якого були в Англії. Необхідність такої заміни викликалася сильно збільшеною в період розвитку промислового капіталізму потребою в металі та виснаженням лісових ресурсів у країнах Західної Європи, в першу чергу в Англії, яка у той час по промисловому розвитку залишила далеко позаду інші країни.
В Англії вже на початку XVII століття робилися спроби застосувати кам'яне вугілля замість деревного як паливо для доменних печей. Найбільш відомі тривалі пошуки, повні драматизму, в цьому напрямку лорда Дода Додлея, розпочаті в 1619 році, які мали певні позитивні результати, але не були доведені до кінця аж до смерті Додлея в 1684 році. Вся справа була обмежена лише особистим успіхом, інші заводчики вважали використання викопного палива цілком неможливим.
Важливою віхою в розвитку доменного виробництва з'явилося застосування коксу як палива і джерела відновника в доменній плавці.
Перші дослідження з використання коксу були розпочаті Аврамом Дербі І, який використав його 1713 року. Він використовував кокс як домішку до деревного вугілля, тобто зміг замінити лише частину деревного вугілля коксом. Лише в 1735 році, після п'ятирічних досліджень, англійському заводчику Авраму Дербі II вдалося здійснити систематичну виплавку чавуну на одному лише коксі, без будь-якої домішки деревного або кам'яного вугілля. Виплавка зросла до небувалих тоді ще ні в кого розмірів — 1365 пудів (21,84 т).[15]
Заміна деревного вугілля коксом вимагала від доменної плавки переходу на більш основні шлаки для отримання достатньо малосірчаного чавуну. Необхідність цього була встановлена емпірично в результаті довгих пошуків. Газопроникність стовпа шихтових матеріалів у доменних печах унаслідок заміни деревного вугілля коксом значно погіршувалася, тому знадобилося посилити потужність повітродувних засобів. Тільки після того, як в металургії почали застосовувати парові повітродувні машини Уатта (1775—1776 р.р.), доменне виробництво в Англії на коксі почало поширюватися.
Однак, перехід доменних печей відбувся не відразу, у Британії й у світі й надалі продовжували працювати окремі доменні печі на деревному вугіллі аж до кінця XIX століття. В Росії на Уралі також до початку XX століття основним паливом печей залишалось деревне вугілля. В Україні деревне вугілля використовувалося на окремих печах на Житомирщині до початку XX століття, в той час як на південних і східних заводах використовували кокс.
Таким чином, для освоєння плавки чавуну на коксі потрібно було близько двох сторіч: необхідно було переконатися в непридатності сирого кам'яного вугілля для виплавки чавуну, освоїти виробництво міцного коксу, визначити види коксівного вугілля і розробити способи коксування, знайти методи видалення сірки з металу в шлак, збільшити потужність повітродувних засобів.
Наприкінці XIX століття завдяки науковим розробкам, існувала можливість вести чавунну плавку на чистому деревному вугіллі, деревному вугіллі з додаванням до нього торфу й дров, на коксі, на сирому кам'яному вугіллі і, нарешті, на антрациті.[15] У XX столітті основним паливом доменних печей у всьому світі став кокс. У США ще помітним було використання антрациту, а у Бразилії — деревного вугілля, бо в умовах теплого клімату тут відновлення деревини відбувається значно швидше, ніж в інших регіонах з доменним виробництвом.
Коксівне вугілля є доволі рідкісним сортом вугілля, тому протягом другої половини XX століття велися пошуки з часткової заміни коксу іншими вуглеводами — природним газом, пило-вугільним паливом, мазутом тощо.
Розвиток підготовки рудних матеріалів для доменної плавки
Протягом століть у доменних печах використовувалася залізна руда без будь-якої попередньої обробки, потім збагачені руди.
В кінці XIX століття підготовка руд була досить простою. Вона полягала в тому, що видобуту руду, якщо вона дуже щільна, залишали лежати на повітрі, при цьому вона вивітрювалася і від морозу розтріскувалася, потім її обпалювали. Палення робилося або у купах, або у спеціальних печах. При нагріві і достатньому притоці повітря магнітний залізняк і закис заліза перетворювалися частково у оксид Fe2O3, а бурий залізняк втрачав воду, сидерити втрачали вуглекислоту і перетворювалися в оксиди.[15]
Агломерація принципово відома з кінця XIX століття. Процес агломерації залізних руд був винайдений англійцями Ф. Геберлейном і Т. Хантінгтоном у 1887 році. Перша агломераційна стрічка була введена у експлуатацію у Бедборо (США) у 1911 році за патентом Дуайта, Ллойда (1906).
Друга половина 1950-х років — обкатування. Метод обкотування — перетворення на грудки тонко здрібнених концентратів був винайдений шведським інженером А. Андерсеном у 1912 році. Початок широкого застосування цього методу відноситься до другої половини 1950-х років.
Інтенсивність доменної плавки
У сучасній доменній печі час перебування шихтових матеріалів від моменту завантаження їх на колошник і до моменту випуску продуктів плавки становить 6 — 8 годин.
На доменних печах кінця XIX століття при сірому чавуні на деревному вугіллі руда в печі перебувала 16 годин, у коксовій — 40 годин, а з кам'яним вугіллям — 48 годин. Чим спалюваність вугілля важча, тим і час перебування руди у домні більший. При плавці білого чавуну було достатньо ¾ цього часу.[15]
Комбіноване дуття
Протягом століть доменні печі працювали на звичайному атмосферному дутті. Повітря бралося з атмосфери і повітродувними засобами подавалося у піч. Однак, вже у XIX столітті у різний час було запропоновано способи ведення доменної плавки на дутті, склад якого відрізняється від складу і температури атмосферного повітря.
Температура дуття
Перші спроби використання нагрітого дуття у металургійних печах були зроблені приблизно у 1827 році. Ботфільд, а потім Дево і Карболь у Франції намагалися нагрівати повітря, вводячи його під колосникові решітки паливні, таким чином дуття входило у фурми разом з продуктами згорання. 1828 року Джеймс Нілсон розробив свій метод підігрівання повітря спочатку для горнів і вагранок. Вперше нагрівання дуття було здійснено у 1829 році Д.Нілсоном на доменній печі заводу Клайд в Шотландії. Використання у доменній печі, замість холодного (тобто з температурою атмосферного повітря), нагрітого лише до 150 °C дуття, призвело до зниження питомої витрати кам'яного вугілля, що використовувався у доменній плавці, на 36 %. Через високу ефективність нагріте повітря дуже скоро отримало розповсюдження. Нагрівання дуття на окремих печах до 150—370 °C дало економію палива (деревного вугілля, коксу, кам'яного вугілля) на 20 — 40 % і збільшення продуктивності печей до 40 %. Жодний інший захід за весь час існування доменного виробництва не призвів до такого значного зниження питомої витрати палива, як використання нагрітого дуття.[1]
Вигоди від застосування гарячого дуття були настільки очевидні, що використання його почало розповсюджуватися з винятковою швидкістю: протягом приблизно десяти років майже всі доменні печі Шотландії були обладнані установками для нагріву дуття.
Однак, багато печей в світі і надалі працювали без використання нагрітого дуття. У Росії і в Україні аж до кінця XIX століття на окремих печах використовувалося холодне дуття.
Шведський учений Рихард Окерман першим (в 1873 році) пояснив причини економії тепла при нагріві дуття, запропонував метод розрахунку для визначення кількісних характеристик впливу нагріву дуття на доменну плавку.
До самої середини XX століття температура дуття не перевищувала 500—600 °C. Це було викликано тим, що перевищення цієї межі при роботі доменних печей на погано підготовленій шихті викликало нерівний хід печі, розлади у її роботі, підвисання. Більш нагріте дуття більше розширялося Тобто умови роботи печі лімітували підвищення нагріву дуття. Підготовка шихтових матеріалів, а також використання деяких домішок до дуття (пара, природний газ, мазут) дозволили підняти температуру дуття до 1000 °C, а на окремих печах і до 1200—1300 °C ще у 1970-х роках. В той же час в СРСР аж до 1991 року на багатьох доменних печах температура дуття була відносно невисокою.
Осушення дуття
1825 року Нільсон у Шотландії запропонував метод роботи на осушеному від вологи дутті, який був впроваджений 1890 року Фрайєром і 1904 року Дж. Гейлі[29] у США.[30] с. 11. [31] Повітря осушували шляхом його охолодження, вміст вологи при цьому знижувався з 10 — 12 до 3 — 3,5 г/м3. Однак, у разі роботи на мілких рудах для збереження газодинамічних умов температуру і до того не високу (~600 С), довелося понизити. Це викликало зниження приходу тепла з дуттям, тобто підвищення витрати палива, хоча робота печі внаслідок рівнішого ходу покращилася.[1] с. 281.
Зволоження дуття
Ідея про вдування у доменну піч пароповітряного дуття була висловлена 1830 року німецьким хіміком Штромейером.[30]
Мета зволоження дуття полягає у введенні у доменну піч водню Н 2 (у складі води Н 2 О), що як і СО є відновником заліза з залізних оксидів залізної руди. Це дозволяє інтенсифікувати доменний процес. Зволоження дуття також дає можливість підвищити температуру дуття. Також дозволяє регулювати тепловий стан печі (при гарячій печі — додавати пару у дуття, при холодній — зменшувати).
В СРСР було запропоновано підвищувати вологість дуття введенням у нього пари з одночасним підвищенням температури дуття для компенсації витрат тепла на розклад пари.
Перші досліди з вдування пари у дуття були проведені у 1927—1928 роках на Донецькому металургійному заводі і дали позитивні результати. Пізніше досліди було проведено на Кузнецькому й Магнітогорському металургійних комбінатах. Однак, попри поліпшення у роботі печей, використання зволоженого дуття затрималося на багато років. Декотрі металурги побоювалися, що зволоження дуття спричинить насичення чавуну воднем і той спричинить утворення у сталі флокенів, тобто погіршить якість сталі.[1]
Однак, досліди, проведені на Кузнецькому металургійному заводі і заводі ім. Дзержинського у 1950—1952 роках показали, що використання зволоженого дуття не підвищує вміст водню у чавуні і сталі, а продуктивність доменних печей залежно від умов роботи підвищується на 6 — 10 %. Після цього зволоження дуття до 25 — 30 г/м3 (3 — 4 % до об'єму дуття), а інколи й більше, набуло широкого розповсюдження.[1] с. 282. 1955 року 75 % доменних печей СРСР працювало на пароповітряному дутті. В цих печах було виплавлено 90 % вього виробленого в країні чавуну.[32]
У 1960-х роках з початком використання природного газу у дутті доменних печей, зволоження дуття вийшло з вжитку, але інколи ще використовувалося, у тому числі на окремих доменних печах України навіть на початку XXI століття.
Збагачення дуття киснем
1871 року Генрі Бессемер взяв патент на вдування у піч повітряного дуття, збагаченого киснем.
Збагачення дуття киснем дозволяє інтенсифікувати доменний процес. У повітрі міститься приблизно 21 % кисню. Взяте з атмосфери дуття також міститиме 21 % кисню. Однак, дуття можна збагатити, додавши до нього кисень перед вдуванням у піч. Чим більше кисню міститиме дуття, тим більше палива можна спалити у одиницю часу, тобто ве́сти доменний процес більш прискорено. 1 % додаткового кисню у дутті в залежності від технології дає збільшення виробництва приблизно на 3 % і, навіть, більше.[1] с. 285—287.
Ідея про доцільність збагачення дуття киснем була висловлена ще у XIX столітті. Однак, широке використання збагаченого киснем повітря у доменному виробництві і у металургії взагалі затрималося на довгий час. Це було зумовлено високою вартістю кисню, а також порушеннями у технологічному процесі, що виникали при виплавці переробних чавунів.
Після багатьох промислових дослідів була випрацювана теорія і технологія доменної плавки з використанням збагаченого киснем дуття. У 1972 році у СРСР зі збагаченням дуття киснем працювало 82 доменних печі, на яких було виплавлено близько 62 % всього чавуну.[1] с. 284.
Вдування у піч природного газу
Перші пропозиції про використання у доменній плавці газоподібних і рідких вуглеводів були висловлені ще у XIX столітті. Вдування у доменну піч природного газу, а також мазути і нафти у фурми було запропоноване Барнетом 1838 року.[30] с. 11. Однак, спроби здійснити ці пропозиції не мали успіху. Вперше у світовій практиці природний газ було успішно застосовано у доменній печі на Дніпропетровському металургійному заводі у жовтні 1957 року. У 1958 році з використанням природного газу в СРСР працювало 13 доменних печей. У 1972 році з використанням природного газу у СРСР працювало 106 доменних печей, на яких було виплавлено 85 % всього чавуну.[1] с.288.
Використання природного газу дозволяє зменшити питому витрату коксу на 10 — 20 %.[1] с.289.
Вдування у доменну піч відновлювальних газів
Висловлювалися ідеї про заміну атмосферного дуття відновлювальними газами.
У Японії запропоновано газифікація мазуту киснем і парою і вдування нагрітих до 1200 °C відновлювальних газів у відновлювальну зону печі з температурами дещо вище 1000 °C.
В СРСР у 1968 році здійснена дослідна плавка на Новотульському металургійному заводі з вдуванням у горн печі гарячих відновлювальних газів (1203 °C) і холодного технологічного кисню (85 %) замість атмосферного дуття. Дослід показав зниження витрати коксу майже на 20 %.
Вдування у доменну піч пилевугільного палива
1926 року Гескамп отримав патент, що передбачав вдування у доменну піч вугільного пилу через фурми разом з повітряним дуттям. Використання вугільного пилу дозволяє використовувати у доменній плавці замість частини дорогого коксу некоксівне вугілля.
В СРСР використання вугільного пилу у доменному процесі вперше було здійснено наприкінці 1960-х років на заводах України.
Підвищення тиску у робочому просторі печі
У 1870-х роках Г. Бессемер взяв патенти на роботу з високим тиском газів у робочому просторі доменної печі.[30] с. 11. Радянська історіографія перші промислові досліди у СРСР приписує І. Коробову, який провів їх у 1940 році. 1970 року з використанням цього режиму в СРСР працювало 108 печей, в тому числі 72 печі з підвищеним тиском газу на колошнику вище 100 кн/м², з них 20 — з підвищеним тиском газу 150—200 кн/м² і вище. В печах, що працювали із підвищеним тиском, було виплавлено понад 95 % всього чавуну.[1] с. 298.
Підвищення тиску у робочому просторі печі дозволяє у одиницю часу вдувати більше повітря і тим самим інтенсифікувати доменний процес, тобто отримувати більше чавуну.
Становлення і розвиток теорії та технології металургії чавуну
Перші книжки з доменного виробництва
Перший опис виплавлення чавуну міститься у працях французького єпископа Генриха з Пуатьє у 1371 році. Один з перших описів доменних печей міститься також у книзі італійського архітектора Антоніо Аверліні — Філарета — «Архітектура», що побачила сівт 1450 року. В книзі описано виробництво чавуну у доменній печі і переробка чавуну у кричному горні.[33][34]
Один з перших авторів книг з металургії Агрікола (Георг Бауер, 1494 — 1555 р.р.), який жив у Чехії, в своїй праці «De re metallika» («Про царство металу») що вийшла в 1556 році, не згадує про доменне виробництво і описує тільки сиродутне. Проте, в книзі італійського металурга Берингуччіо «De la pirotechnika» («Про піротехніку»), що вийшла раніше (1540 р.) описано технологію випалу деревного вугілля і доменної плавки.
1665 року було видано книжку «Metallum Martis» англійського металурга Дода Дадлея, в якій він описав свій досвід використання кам'яного вугілля у доменній плавці. 1722 року побачили світ книжки Рене Антуана Реомюра «Мистецтво перетворення ковкого заліза у сталь» і «Мистецтво пом'якшення виливаного чавуну».
В 1742 році була видана книжка російського ученого М. В. Ломоносова «Перші основи металургії або рудних справ». Він вперше [джерело?] зробив спробу дати теоретичне обґрунтування процесам плавки чавуну і явищам, що відбувалися при виробництві сталі.
Розвиток теорії доменного виробництва
Доменна піч виникла чисто досвідним шляхом, задовго до бодай якогось пояснення процесів, що відбуваються у ній. Доменна піч існує з XIV століття, однак найелементарніші пояснення доменного процесу були запропоновані лише близько 150 років тому — у другій половині XIX століття. Протягом довгого часу теоретичні узагальнення лише пояснювали практику, і лише з другої половини XX століття теорія почала визначати шляхи розвитку доменного виробництва.[1] стор. 9.
Однак, спроби дослідити і пояснити доменний процес були зроблені здавна. Наука зробила крок далеко вперед, і це дозволило металургам розробити теорію про хімічний склад сплавів заліза. Було встановлено, що чавун — це сплав заліза з вуглецем і деякими іншими елементами, і що вміст вуглецю в чавуні коливається від 3,2 до 4,3 %. При цьому вуглець в чавуні може знаходитися в декількох різних модифікаціях, а саме: хімічно пов'язаний із залізом у вигляді сполуки Fe3C, яка називається карбідом заліза, або механічно змішаний із залізом у вигляді графіту.
Сталь є також сплавом заліза з вуглецем, відмінним від чавуну за хімічним складом тим, що вміст вуглецю в ньому значно менше, а саме 0,15-1,75 %.
М. В. Ломоносов один з перших виказав ряд правильних і цінних думок про склад залізної руди, які збігалися з уявленнями про руди деяких зарубіжних учених. Було встановлено, що залізо в руді знаходиться в хімічній сполуці з киснем; окрім оксидів заліза в руді завжди присутня більша або менша кількість землистих речовин, які називаються в наш час[коли?] пустою породою.
Коли було встановлено, що чавун складається головним чином із заліза і вуглецю, і що залізняк в основному представлений оксидами заліза, металургам стало ясно, що в доменній печі відбувається процес руйнування хімічної сполуки заліза з киснем, або, як говорять хіміки, процес відновлення заліза. Цим був закладений науковий фундамент під теорію доменного процесу.
Перше дослідження роботи доменної печі було проведено хіміком Робертом Бунзеном, винахідником спектрального аналізу.
Бунзен відібрав у 1838 році проби доменного газу з декількох горизонтів по висоті доменної печі. На його думку можна розрізнити три області або зони, в яких готується, протікає і завершується процес відновлення. Перша область характеризується рясним утворенням водяних парів, тягнеться на глибину близько 1,2 метри нижче від рівня засипу і як би являє собою випалювальну піч: вільна (гігроскопічна, що міститься у порах шихтових матеріалів) і хімічно зв'язана (гідратна) вода шихти і палива випаровується, глинисті мінерали обпалюються, і відбувається виділення вуглекислоти (СО 2 ) з шихти при сприятливій дії присутньої водяної пари.
Друга область характеризується вмістом монооксиду вуглецю (СО) в газовій фазі, що перевершує 30 %, і тягнеться до рівня заплечиків. Її можна було б назвати ділянкою відновлення. Відновники заліза оксид вуглецю, метан і водень проникають у відкриті завдяки випаленню пори руди, починається відновлення оксидів заліза. При пануючій тут температурі рідкі матеріали не створюються.
Третя область включає горно. Тут починається створення шлаку, залізо повністю відновлюється і навуглецьовується, відбувається розділення чавуну і шлаку.
Наступне дослідження процесів, що відбуваються в доменній печі, було проведено французьким ученим Ебельманом в 1841 році. На підставі даних свого дослідження Ебельман прийшов до правильного висновку про те, що основна робота по відновленню оксидів заліза в доменній печі проводитися газом — монооксидом вуглецю СО. Цей газ, віднімаючи кисень від заліза, приєднує його до себе і перетворюється на інший газ — двооксид вуглецю СО2.
Це відкриття встановлювало лише загальний принцип процесу, що відбувається. Але воно не давало відповідь на питання про те, яка швидкість процесу відновлення залежно від температури і складу газу-відновника. Знадобилися довгі роки напруженої дослідницької роботи в лабораторіях і на доменних печах, щоб всебічно вивчити хід процесу відновлення оксидів заліза в доменній печі. Ж. Ебельман і Р. Бузен вперше дослідили склад колошникових газів.
Велика заслуга в справі вивчення доменного процесу належить Ісааку Лотіану Беллу, власнику залізоробного заводу Клівлендського округу. Він вперше встановив, які умови необхідні для успішного ходу відновлення оксидів заліза в доменній печі, а також якими є температури початку відновлення та найінтенсивнішого його ходу.
Умови, в яких доводилося працювати Беллу, були вельми несприятливими. Тодішня наука ще не мала ні точних способів для проведення різного роду хімічних аналізів, у тому числі аналізу колошникового газу, ні хоч трохи придатних пристосувань для вимірювання температур. Проводячи свої досліди, Белл вимушений був для визначення температур встановлювати декілька шматочків металу з відомою і поступово зростаючою температурою плавлення (наприклад, вісмут, свинець, цинк, сурма). Тому в працях Белла температура, при якій провадився той або інший дослід, дуже часто визначалася таким чином: «вісмут плавиться, свинець розм'якшується», що означає в перекладі на сучасну мову температуру близько 290 °C. Дуже часто Белл визначав температуру ще менш точним способом — за кольором прожарювання металу, і писав, що експеримент проводився при «температурі темно-червоного гартування» або «вишнево-червоного гартування» і т. д.
Не маючи обладнаної лабораторії, Белл проводив більшість своїх дослідів у заводській обстановці. Для визначення, наприклад, відновлюваності різних типів руд він поміщав їх у газопровід доменного цеху і т. д.
Велика заслуга належить Беллу в розробці питань про розвиток тепла в доменній печі та про витрату тепла на ті або інші процеси, що відбуваються в ній. Белл одним з перших склав тепловий баланс доменної плавки.
Подальший розвиток теорії про відновні процеси в доменній печі був зроблений французьким металургом Луї Грюнером. Він показав, що відновлення оксидів заліза в доменній печі може йти як за рахунок монооксиду вуглецю з утворенням вуглекислоти, так і за рахунок твердого вуглецю з подальшим утворенням монооксиду вуглецю без утворення вуглекислоти.
Ґрунтуючись на тому, що перший спосіб відновлення не вимагає витрат тепла, Грюнер вважав доцільним прагнути найбільшого його розвитку. Такий хід доменної печі, коли пряме відновлення (за рахунок твердого вуглецю) повністю усунеться, і все залізо повністю відновлюватиметься тільки за допомогою оксиду вуглецю, Грюнер назвав «ідеальним», вважаючи, що при ньому вийде найнижча витрата палива. Будучи автором ряду робіт, присвячених теорії доменного процесу, Грюнер мав серед металургів великий авторитет і популярність, тому висунуте ним положення про ідеальний хід доменної печі було сприйнято металургами без жодної критики і зведено в свого роду принцип. Пройшло декілька десятиріч, доки була доведена помилковість цього принципу. Спростував цю помилку і вніс ясність в одне з найважливіших питань теорії доменного процесу російський металург М. Павлов. Помилка Грюнера, як пояснив М. Павлов, полягає в тому, що він розглянув реакції відновлення оксидів заліза оксидом вуглецю і твердим вуглецем тільки з погляду приходу і витрати тепла, але абсолютно не займався питанням про те, скільки вуглецю витрачається на відновлення оксидів заліза в обох випадках. При прямому відновленні затрачується менше вуглецю, ніж при непрямому, оскільки наявність в пічному газі вуглекислоти вимагає великого надлишку оксиду вуглецю для успішного ходу відновлення. Тому теоретично якнайменшої витрати палива на виплавку одиниці чавуну в доменній печі можна досягти при оптимальному поєднанні обох способів відновлення. Проте, Грюнер мав рацію, що основна відновна робота повинна проводитися за рахунок оксиду вуглецю, тобто непрямим шляхом, для забезпечення мінімальних енерговитрат.
М. О. Павлов зробив важливі узагальнення, у тому числі ґрунтовні дослідження роботи великих доменних печей, що дозволили відкинути думку про неможливість збільшення поперечних розмірів доменних печей. М. Павлов систематизував дані про найпоширеніші співвідношення між основними розмірами доменних печей і рекомендував на основі цих даних і низки теоретичних міркувань найраціональніші співвідношення розмірів елементів профілю доменної печі.
Шведський учений Рихард Окерман першим (в 1873 році) пояснив причини економії тепла при нагріві дуття, запропонував метод розрахунку для визначення кількісних характеристик впливу нагріву дуття на доменну плавку.
Крім того, Окерман виконав велику роботу з визначення теплоти, затрачуваної на розплавлення шлаків. Ця робота озброїла металургів даними про ступінь важкоплавкості та легкоплавкості шлаків різного складу.
Дані Окермана довгий час залишалися єдиним критерієм, на основі якого металурги складали шихту і вибирали той або інший склад шлаку.
До другої половини XIX століття технологія доменного виробництва розвивалася цілком емпирічно. Потім почали з'являтися наукові обґрунтування.
Історія доменного виробництва на території України
Перші доменні печі на території України з'явилися у 60-х роках XVIII століття на Закарпатті. До 1773—1783 рр. відноситься будівництво доменних печей на Правобережному Поліссі.[35]
До появи доменних печей виробництво заліза відбувалося у руднях. Доменні мануфактури (заводи) були новим, більш високим етапом розвитку чорної металургії України. Ці підприємства значно перевершували старі за об'ємом виробництва металу, чисельністю робітників, мали досконалішу організацію праці, кращу технічну оснащеність.[35]
Першим металургійним заводом на сході України був казенний Луганський чавуноливарний завод, введений в дію 1798 року. Протягом XIX століття на сході України було збудовано 17 металургійних заводів з доменним виробництвом. На кінець XIX століття тут було створено новий металургійний регіон Російської Імперії, який значно випередив за технологією і кількістю продукції колишній основний металургійний центр Росії — Урал. Наприкінці XIX ст. Катеринославська губернія давала більше половини всього чавуну, виплавленого у Російській Імперії.
Як до набуття в 1918 році, так і після втрати Україною незалежності у 1919 році, вона протягом десятиріч була сировинною базою Росії, даючи половину всього чавуну в колишньому СРСР.
Основні віхи розвитку доменного виробництва
Техніка і технологія доменного виробництва, починаючи з його виникнення, безперервно удосконалюються під впливом постійно зростаючої потреби в металі й прагнення скоротити витрати на його виробництво. Відповідно розвивалися і методи підготовки до плавки сировини і палива. Нижче приводиться хронологія основних технічних і технологічних рішень розвитку і вдосконалення доменного виробництва[36][37][38].
ХІІІ — XIV століття, середина. Спорудження перших доменних печей у Західній Європі.
1371 рік. Перший докладний опис технології виплавки чавуну в працях Єпископа Генріха з Пуатьє (Франція).
1619 рік. Перша доменна плавка на спеціально підготовленому кам'яному вугіллі проведена Д. Додлеєм (Англія).
1620 рік. На металургійних заводах Герца сконструйовані дерев'яні міхи, які приводяться в дію водяним колесом (Німеччина).
1621 рік. Патент на випалювання коксу з торфу виданий у Фрайберзі (Німеччина) Ернесту і Михайлу Шейнлебенам.
1683 рік. Опис коксування кам'яного вугілля Іоганном Іохимом Бехером (Німеччина).
1697 рік. Початок застосування фурм, виготовлених з листового заліза на заводах у Герці (Німеччина).
1735 рік. Патент А. Дербі на коксування кам'яного вугілля й успішні досліди доменної плавки на коксі на заводі у місті Колбрукдейл (Англія).
1755 рік. Парова повітродувна машина Вількинсона на заводі в Бредлі (Англія).
1765 рік. Парова повітродувна машина Ползунова на Коливаново-Вознесенському заводі в Барнаулі (Росія).
1768 рік. Циліндрична повітродувна машина Джона Смітона з литими чавунними циліндрами (Шотландія).
1799 рік. Дослідження Седдегером можливості застосування гарячого дуття (Англія).
1802 рік. Порожнисті водоохолоджувані фурми винайдені Конді, встановлені на печах заводів Бредлі (Англія) і Кальдер (Шотландія).
1811 рік. Патент Оберто і перші досліди використання тепла колошникового газу для інших виробництв (Англія).
1825 рік. Пропозиція Д. Нельсона про осушення дуття (Англія).
1828 рік. Д.Нілсон отримав патент на «Нагрів дуття перед подачею його в доменну піч» і здійснив.
1830 рік. Пропозиція Штромейєра (Німеччина) про добавку пари до дуття.
1830 рік. Винахід бронзової водоохолоджуваної фурми в Англії.
1831 рік. Пропозиція Д. Дейвіса про вдування вугілля у фурми доменної печі (Англія).
1832 рік. Використання колошникового газу для нагріву дуття здійснив Фабер дю Фор на заводах у Вассеральфінгені (Німеччина).
1838 рік. Патент Барнета на вдування природного газу і нафти у фурми доменної печі.
1839 рік. Робота Д. Гіббонса про «природний» раціональний профіль доменної печі.
1839 рік. Перший аналіз колошникового газу деревновугільної печі у Фекергагені (Бунзен).
1840 рік. Винахід вугільного газогенератора Фабер дю Фором (Німеччина).
1873 рік. Винахід міксера В.Дейтоном. Перший міксер введений на заводі «Едгар Томпсон» (Піттсбург, США) в 1889 р.
1875 рік. Виплавка Брустлейном ферохрому в доменній печі (Франція).
1882 рік. Застосування вуглецевих вогнетривів для футерівки доменних печей Ф. Бургерсом (Німеччина).
1886 рік. Винахід Люрманом (Німеччина) газомоторних повітродувних машин.
1886 рік. Винахід Шмідтом газового клапана для відсікання доменної печі від газової мережі заводу.
1887 рік. Винахід технології агломеруючого випалення сульфідних руд Ф. Геберлейном і Т. Хантингтоном (Англія).
1887 рік. Конструкція горизонтальних холодильників для заплечиків реалізована Гейлі на заводі «Едгар Томпсон» (Англія).
1887 рік. Отримання феросиліцію в доменній печі, Джерс (Англія).
1892 рік. Винахід Гейлі і Скоттом коробчастих холодильників для шахти доменної печі й установка їх на заводі «Едгар Томпсон» (Англія).
1899 рік. Пуск до експлуатації першої печі з тонкостінною шахтою Бургерса на заводі «Вулкан» біля Дуйсбурга (Німеччина).
1902 рік. Пропозиція А. М. Брєзгунова про введення в доменну шихту мартенівських шлаків (Росія).
1902 рік. Винахід В.Джобом способу агломерації піритових огарків і дрібних залізних руд при продуванні шару повітрям знизу вгору (німецький патент № 137438). Перші досліди агломерації колошникового пилу проведені в Бельгії на заводі фірми «Кокеріль» в Люттіху.
1904 рік. Пуск першої коксової печі конструкції Копперса (Німеччина).
1905 рік. Вперше застосована водяна пара для запобігання вибухів у доменних газопроводах (Daugherty).
1910 рік. Введення в експлуатацію Янтценом першої установки сухої грануляції шлаку на заводі Будерус (Німеччина).
1911 рік. Патент на брикетування руд і концентратів за способом Грендаля.
1911 рік. Винахід газової агломерації А. Кролем (німецький патент № 271986).
1911 рік. Винахід двошарового спікання Х. Г. Торульфом (німецький патент № 384372).
1912 рік. У Швеції запатентовано спосіб згрудкування дрібних сипучих матеріалів (грануляція) А.Андерсеном. Патент США № 1103196.
1913 рік. Винахід В.Бартшем аглострічки для роботи з продувкою повітря знизу вгору (німецький патент № 276424).
1916 рік. У Німеччині виготовлені в промисловому масштабі випалені обкотиші.
1921 рік. Пуск першої промислової чашкової аглоустановки шведської фірми АІБ (круглі чаші діаметром 2,6 м).
1925 рік. Винахід Шпісом напівсухої грануляції доменного шлаку (Німеччина).
1926 рік. Патент Гескампа на спосіб вдування вугілля у фурми доменних печей (Англія).
1929 рік. Перші лабораторні досліди В. В. Лізунова щодо подачі нагрітого (500 °C) повітря під надмірним тиском (3 кПа) до опікуваного шару на чашковій установці (Росія).
1931 рік. Винахід круглої агломашини В. А. Сахарновим (Росія).
1932 рік. Винахід А. П. Ніколаєвим двозонного спікання аглошихти (Росія).
1935 рік. Досліди інженера Вересотського з спікання аглошихт під надмірним тиском 60 кПа на заводах ім. Дзержинського і «Азовсталь» (Україна).
1941 рік. Демонтаж двох доменних печей 930 м³ на Новоліпецькому і Новотульському заводах з подальшим монтажем на Челябінському заводі (задуті в 1944 р.) (Росія).
1943 рік. Перші досліди регулювання теплового стану доменної печі по складу колошникового газу, шихти і шлаку проведені А. М. Похвіснєвим на Магнітогорському меткомбінаті (Росія).
1946 рік. Винайдення системи випарного охолодження, що спочатку була застосована на мартенівських печах, а згодом — на доменних. Винахід приписується С. Андоньєву.
1950—1970 роки. Робота 10 низькошахтних доменних печей на буровугільному коксі в Кальбе (Німеччина).
1954 рік. Розробка конструкції (Гіпросталь) і спорудження цільновуглецевого поду з вертикальною установкою трьох рядів блоків на печі № 8 об'ємом 1371 м³ Магнітогорського меткомбінату (Росія).
1957 рік. Розробка конструкції та застосування на доменних печах екранованих сопел (авторське свідоцтво СРСР № 106368 на ім'я Н. С. Рєїзова і Л. Я. Шпарбера) (Росія).
1959—1975 роки. Розробка і реалізація на доменних печах галузі способу подачі шихти в скіпи безпосередньо з бункерів за допомогою віброгрохотів (авторське свідоцтво СРСР № 122155 на ім'я І. І. Сагайдака, Н. С. Кріволапова, І. С. Рєїзова, Л. Я. Шпарбера, Ю. П. Волкова) (Росія).
1965—1980 роки. Освоєння виплавки ванадієвого чавуну на Чусовському металургійному заводі та Нижньотагільському меткомбінаті (Росія).
1967 рік. Винахід агломераційної стрічки для спікання під тиском (авторське свідоцтво СРСР № 508647 на ім'я Є. Ф. Вєгмана, А. Г. Міхалєвіча, А. А. Буярова) (Росія).
1970 рік. У Швеції запрацювала перша фабрика з безвипалювального грудкування продуктивністю 1,6 млн. т/рік.
1974 рік. Розробка й освоєння установки припічної грануляції шлаку з кільцевими зневоднювачами на печі № 9 меткомбінату «Криворіжсталь» (Україна).
Основні риси сучасної доменної плавки були сформовані до кінця XIX століття. До того часу в більшості розвинутих країн завершився перехід на мінеральне паливо — кокс, а конструкція доменної печі знайшла форми, принципово не відмінні від нинішніх.
Найкращі доменні печі кінця XIX століття працювали з питомою продуктивністю 0,6-0,8 т/(м³•доб) (коефіцієнт використання корисного об'єму КВКО — 1,2 — 1,6 м³•доб/т) при витраті коксу 900 — 1200 кг/т чавуну; добова продуктивність одного агрегату становила 300—600 т. В сучасних крупних доменних печах виплавляють до 10 тис. т чавуну на добу. Їхня питома продуктивність становить 2,5 — 3,0 т/(м³•доб), а витрата коксу досягає 350 — 400 кг/т чавуну. Таким чином, результат розвитку доменної плавки протягом XX століття виражається в три-, чотирикратному збільшенні питомої продуктивності доменних печей і в (2,5 — 3,0)-кратному скороченні питомої витрати коксу. Сукупність відомих і розроблюваних заходів щодо вдосконалення доменної плавки дозволить поліпшити її показники приблизно в 1,5 рази, досягнувши питомої продуктивності 3,5-4 т/(м³•доб) і витрати коксу 250—300 кг/т чавуну, що близько до граничних можливостей доменної плавки в рамках характерних для неї властивостей.
Економіко-статистичні данні
Виробництво чавуну в Англії в 1500 році досягло 12 тис. тон.
У XVII столітті на перше місце з виробництва чавуну вийшла багата залізними рудами і лісами Швеція. З 1740 по 1804 рік перше місце у світі за виробництвом чавуну займала Росія з виплавкою 25000 — 180000 т чавуну на рік. Однак, після промислової революції на Заході з'явилися великі механізовані доменні цехи, в той час як у кріпацькій Росії всі роботи з обслуговування печей здійснювалися вручну. Протягом майже всього XIX століття у виробництві чавуну лідирувала Британія. В Англії за період від середини XVIII до середини XIX століття виплавка чавуну зросла у 90 разів. 1897 року на перше місце вийшли Сполучені Штати Америки, які дуже швидко залишили далеко позаду колись лідируючу Британію і всі інші країни світу. Царська Росія на початку XX століття виплавляла лише 3 млн т чавуну на рік, тобто втричі менше ніж Англія і у п'ять разів менше ніж США. Лише 1971 року СРСР уперше в історії спромігся випередити США за виробництвом чавуну. Тоді в СРСР його було виплавлено 120,6 млн.т, а у США — 111,6 млн т.[39] При цьому 60 % чавуну СРСР тоді було виплавлено з української руди на заводах України.
Рік | Виробництво чавуну у світі | Велико- британія | США | Німеччина | Саар | Франція | Бельгія | Росія з всіма її колоніями і СРСР | Японія | Китай | Інші країни |
---|---|---|---|---|---|---|---|---|---|---|---|
1700[26] | 0,012 | 0,0025 | |||||||||
1720[26] | 0,017 | 0,01 | |||||||||
1750[26] | 0,022 | 0,033 | |||||||||
1770[26] | 0,032 | 0,084 | |||||||||
1800[26] | 0,156 | 0,1724 | |||||||||
1820 | 1,0,[2] за ін. дан. 1,026[26] | 0,406[26] | 0,140[26] | 0,153[26] | |||||||
1830 | 1,8[2] | ||||||||||
1840 | 2,7[2] | ||||||||||
1850[2] | 4,7 | 2,25 | 0,69 | 0,30 | 0,41 | 0,14 | 0,227[26] | 0,97 | |||
1860 | 7,22, за ін. дан. 7,4[39] | 3,90 | 0,82 | 0,50 | 0,88 | 0,32 | 0,336[26] | 0,80 | |||
1870[2] | 11,84 | 5,96 | 1,67 | 1,24 | 1,16 | 0,56 | 0,36 | 0,89 | |||
1880[2] | 18,16 | 7,75 | 3,84 | 2,43 | 1,70 | 0,86 | 0,56 | 1,20 | |||
1890[2] | 26,75 | 7,90 | 9,20 | 4,03 | 1,93 | 0,77 | 0,89 | 2,03 | |||
1900[2] | 39,81, за ін. дан. 40,70[39] | 8,95 | 13,79 | 7,43 | 2,67 | 1,0 | 2,85 | 3,11 | |||
1910[2] | 64,76 | 10,01 | 27,30 | 12,89 | 3,97 | 1,82 | 2,98 | 5,79 | |||
1913 | 79,30[39] | 10,425[40] | 31,464[40] | 12,287[40] | 9,071[40] | 2,484[41] | 4,635,[26] у кордонах 1945 року 4,216[26][40] | 0,24[26] | 0,16[26] | ||
1915[2] | 59,70 | 8,79 | 29,92 | 10,03 | 0,58 | 0,07 | 3,63 | 6,68 | |||
1920[2] | 62,85 | 8,03 | 36,93 | 6,93 | 0,88 | 3,38 | 1,10 | 0,11 | 0,73[26] | ||
1925[2] | 75,69 | 6,26 | 36,70 | 10,01 | 1,43 | 8,36 | 2,50 | 1,30 | 9,13 | ||
1929[2] | 97,41 | 7,59 | 42,61 | 13,19 | 2,07 | 10,20 | 3,98 | 3,95 | 1,1[26] | 0,44[26] | |
1930[2] | 79,24 | 6,19 | 31,75 | 9,54 | 1,88 | 9,88 | 3,31 | 4,90 | 11,79 | ||
1935[2] | 73,10 | 6,42 | 21,37 | 12,64 | 5,70 | 2,98 | 12,41 | 11,58 | |||
1936[2] | 90,10 | 7,72 | 21,37 | 15,06 | 6,14 | 3,16 | 14,09 | 12,99 | |||
1937[2] | 101,188 | 8,50 | 37,13 | 16,03 | 7,79 | 3,78 | 14,23 | 13,73 | |||
1938[2] | 79,344 | 6,70 | 19,34 | 18,20 | 5,65 | 2,33 | 14,85 | 12,27 | |||
1950[26] | 19,2 | 2,2 | |||||||||
1952 | 151,0[39] | ||||||||||
1966 | 300,0[39] | ||||||||||
1970 | 427[30] | 17,7[30] | 83,3[30] | 19,2[30] | 10,8[30] | 85,9[30] | 68,1[30] | ||||
1971 | 111,6[39] | 120,6[39] | |||||||||
1974 | 503[30] | 13,8[30] | 87,0[30] | 23,5[30] | 13,1[30] | 99,9[30] | 90,4[30] | ||||
Література
- Ефименко Г. Г. Металлургия чугуна / Г. Г. Ефименко, А. А. Гиммельфарб, В. И. Левченко.- Киев: Вища школа.- 1988.- 351 с.
- Коротич В. И. Металлургия черных металлов / В. И. Коротич, С. Г. Братчиков. — М.: Металлургия, 1987. — 240 с.
Див. також
Посилання
Виноски
- Металлургия чугуна. Ефименко Г. Г., Гиммельфарб А. А., Левченко В. Е. Изд. 2 — К.: «Вища школа», 1974 — С. 276.
- Iron and steel: world's statistics. / Enciclopædia Britannica. V. 12. Page 673.
- Monthly iron production. https://www.worldsteel.org. World Steel Association. 25 січня 2017. Архів оригіналу за 11 лютого 2017. Процитовано лютий 2017. (англ.)
- Железо. // Большая советская энциклопедия : в 30 т. / главн. ред. А. М. Прохоров. — 3-е изд. — М. : «Советская энциклопедия», 1969—1978. (рос.)
- Железный век. // Большая советская энциклопедия : в 30 т. / главн. ред. А. М. Прохоров. — 3-е изд. — М. : «Советская энциклопедия», 1969—1978. (рос.)
- Шалимова Н. И. Черная металлургия — что это? / Н. И. Шалимова.- М.: Металлургия, 1980. — 152 с.
- Красавцев Н. И. Очерки по металлургии чугуна / Н. И. Красавцев, И. А. Сировский .- М.: ГНТИ.- 1947. — 492 с
- Хатти // Большая советская энциклопедия : в 30 т. / главн. ред. А. М. Прохоров. — 3-е изд. — М. : «Советская энциклопедия», 1969—1978. (рос.)
- Доменне виробництво / Українська радянська енциклопедія . — 2-е видання. — Т. 3. — Київ, 1978.
- Iron and still. History. / The World Book Encyclopedia. — Volume 10. — 1994. Page 451.
- Jack Goody. Metals, Culture and Capitalism: An Essay on the Origins of the Modern World — New York: Cambridge University Press. — 2012. Page xviii. ISBN 978-1-107-02962-0 ISBN 978-1-107-61447-5
- B. Awty, C. Whittick and P. Combes, The Lordship of Canterbury, iron-founding at Buxted, and the continental antecedents of cannon-founding in the Weald, coll. " Sussex Archaeological Collections " (Vol. 140), 2004, p. 71-81.
- Catarina Karlsson, Ing-Marie Pettersson, Jensen Jonas Ros. Lapphyttans masugn Undersökning av grundkonstruktionen, under den medeltida masugnen — Västerås: Stiftelsen Kulturmiljövård. — 2011. ISBN 978-91-7453-067-4 (швед.)
- Jockenhövel, Albrecht, Willam, Chr., Abdinghoff, T., Overbeck, M., 1997.: Archaeological Investigations on the Beginning of Blast Furnace-Technology in Central Europe. pp. 56-58 In: Crew, Peter and Crew, Susan (editors) (1997) Early Ironworking in Europe: Archaeology and Experiment: Abstracts of the International Conference at Plas Tan y Bwlch 19-25 September 1997 Plas Tan y Bwlch Occasional Papers No 3 Snowdonia National Park Study Centre, Gwynedd, Wales. Archaeological investigation on the begginning of blast furnace — technology in central Europe.
- А. И. Скиндер. Δ. Доменное производство // Энциклопедический словарь Брокгауза и Ефрона : в 86 т. (82 т. и 4 доп. т.). — СПб., 1890—1907. — Т. 10 А (20). (рос. дореф.)
- Top ranked EPC contractor — reference list. As of june 2015. — POSCO, 2015 на сайті http://www.poscoenc.com/eng. (англ.)
- Iron Ore: Mineralogy, Processing and Environmental Sustainability. / Edited by Liming Lu. — Elsevier Ltd. — 2015. ISBN 978-1-78242-156-6 (print) ISBN 978-1-78242-156-7 (online) (англ.)
- William F. Durfee. The Development of American Industries Since Columbus: Iron and Steel Industry III / Popular Science Monthly. — Volume 38. — February 1891. — Page. 462.
- John Henry Alexander . Report on the Manufacture of Iron: Addressed to the Governor of Maryland. — Baltimore: FieldingLukas, Jr. — 1840. Page 60.
- James Moore Swank . History of the Manufacture of Iron in All Ages: And Particularly in the United States from Colonial Time to 1891. — New York: Cambridge University Press, 2011. Page 53. ISBN 978-1-108-02684-0.
- Manuel de la métallurgie du Fer, Tome 1, par Adolf Ledeburg, édition française traduite par Barbary de Langlade revu et annoté par F.Valton, publié par Librairie polytechnique Baudry et Cie, 1895. page 403.
- Planches de l'Encyclopédie de Diderot et d'Alembert, volume 3: Forges, 3rd section, Pl. II.
- The Popular science monthly. — Volume: 38. — New York: Popular Science Pub. Co., etc., 1890. Page. 455.
- Thomas Turner, William Chandler Roberts-Austen. The Metallurgy of Iron. — London: C. Griffin & company, limited, 1908. Page. 141. Також .
- Every Saturday. March 18, 1871.
- Зюзин В. И. Механическое и подъёмно-транспортное оборудование доменных цехов. — Москва, 1962. с. 419.
- Manuel de la métallurgie du Fer, Tome 1, par Adolf Ledebur, édition française traduite par Barbary de Langlade revu et annoté par F.Valton, publié par Librairie polytechnique Baudry et Cie, 1895 page 447.
- Joseph Esrey Johnson. Blast-furnace Construction in America. — New York, McGraw-Hill book company, inc. 1917. Page 79.
- James Gayley
- Металлургия чугуна. / Е. Ф. Вегман и др. — М.: «Металлургия», 1978. 479 с.
- Патенти, виданні Гейлі: Патент 715366, виданий 9 грудня 1902 року, Петент 746814, Патент 652179.
- Середенко М. М. Чорна металургія України. 1917—1957. — Київ, 1957. Стор. 152.
- The cast-iron produsing «blast» furnace. / Alan R. Williams. The Knight and the Blast Furnace: A History of the Metallurgy of Armour in the Middle Ages & the Early Modern Period. — Leiden, Boston, Köln, Brill, 2002. — P. 879.
- B. G. Awty, « The Blast Furnace in the Renaissance Period: Haut Fourneau or Fonderie?», Transactions of Newcomen Society, vol. 61, 1989-90, p. 67.
- Развитие металлургии в Украинской ССР. — Киев, 1980.
- Товаровский И. Г. Эволюция доменной плавки / И. Г. Товаровский, В. П. Лялюк. — Днепропетровск: Пороги. — 2001. — 428 с.
- Кожевников И. Ю. Окускование и основы металлургии / И. Ю. Кожевников, Б. М. Равич. — М.: Металлургия, 1991. — 304 с.
- Доменное производство: справочное издание. В 2-х т. — Т.1. Подготовка руд и доменный процесс / Под ред. Е. Ф. Вегмана. — М.: Металлургия, 1989. — 496 с.
- Металлургия чугуна. Ефименко Г. Г., Гиммельфарб А. А., Левченко В. Е. — К., «Вища школа», 1979. Стр. 15.
- Середенко М. М. Чорна металугія України. — Київ, 1957. Стор. 35
- Morris F. La Cross. Belgium. // The Iron and Associated Industries of Lorraine, the Saare District, Luxemburg, and Belgium. U.S. Government Printing Office, 1920. P. 80. (англ.)
Література
- Мовчан В. П., Бережний М. М. Основи металургії. — Дніпропетровськ: Пороги, 2001. — 336 с.