Доменна піч
До́менна піч, до́мна — металургійна піч шахтного типу (вертикально розташована), призначена для виплавки чавуну (переробного чи ливарного) або феросплавів з залізорудної сировини (руди, агломерату, окатків). Побічними продуктами доменного процесу є шлак, доменний газ і колошниковий пил. Паливом доменної печі є кам'яновугільний кокс. У ролі часткових замінників коксу можуть бути використані природний газ, коксовий газ, мазут, пиловугільне паливо та деякі інші вуглеводні. Для зниження температури плавлення пустої породи шихтових матеріалів і утворення шлаку з потрібними властивостями у шихту доменної печі додають флюси (вапняк або інші).
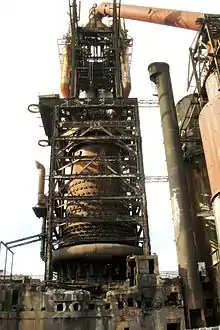
.jpg.webp)
.jpg.webp)
Особливістю доменного процесу, що відбувається в доменній печі, є його безперервність і протитечія відновлювальних газів, що утворюються внизу печі (у зоні горіння палива) й підіймаються вгору, і стовпа шихтових матеріалів, які завантажують у піч згори (колошник), а вони безперервно спускаються донизу. Опускання стовпа шихтових матеріалів відбувається через звільнення об'єму в нижній частині печі при спалюванні коксу, плавці шихтових матеріалів і випуску продуктів плавки. Шихтові матеріали завантажують у піч певними порціями (колошами) згори через засипний апарат, у нижню частину печі для спалювання коксу та його часткових замінників через повітряні фурми вдувається повітря, разом з ним вдувають також й вуглеводні замінники коксу та додатковий кисень. Внаслідок проходження фізико-хімічних процесів шихтові матеріали перетворюються на чавун, шлак і доменний газ. Час перебування порції шихтових матеріалів усередині печі від моменту завантаження на колошник до випуску продуктів плавки становить 5—8 годин.
Причиною одержання в доменній печі чавуну (містить понад 4 % C), а не сталі (містить менше 2 % С) є присутність в усьому об'ємі доменної печі вуглецю коксу, з яким відновлене залізо перебуває в постійному контакті й, розчиняючи його в собі, перетворюється на чавун.
Вступ
Виплавлений в доменній печі переробний чавун далі переплавляється у сталеплавильних печах на сталь, тобто є лише проміжним продуктом у двоступеневому процесі отримання кінцевого продукту — сталі. Таким чином, виплавка переробного чавуну на доменній печі є початковим етапом у виробничому ланцюгу металургійного заводу. Ливарний чавун відрізняється від переробного хімічним складом і властивостями і використовується для виготовлення виливків. Феросплави (спеціальні чавуни) використовуються у сталеплавильному виробництві для розкиснювання сталі.
У 2016 році у доменних печах всього світу було виплавлено близько 1,15 млрд т чавуну.[1] Понад 95 % всього виплавлюваного у світі доменного чавуну припадає на переробний чавун. У доменних печах виплавляються лише деякі види феросплавів і порівняно в дуже невеликій кількості. У 2014 році в доменних печах в усьому світі було виплавлено 496 тис. т феросплавів (0,042 % продукції доменних печей, 0,86 % всіх феросплавів, виплавлених у різних печах).[2] Точних даних щодо кількості доменного ливарного чавуну немає, однак вона становить вкрай незначну частку від всього доменного чавуну.
На сучасному рівні розвитку чорної металургії (2017 рік) доменна піч є основним агрегатом для отримання заліза (у вигляді чавуну) з залізної руди, хоча постійно ведуться дослідження у напрямку створення інших агрегатів і робляться спроби замінити при відновленні заліза доменний процес іншими процесами — процесами безпосереднього (прямого) одержання заліза. За даними World Steel Association, у 2016 році світове виробництво процесами безпосереднього відновлення, що конкурують з доменним виробництвом, становило 54,026 млн т[1] (у 2014 році — 73,202 млн т[3]) заліза безпосереднього відновлення, тобто їхня частка у виробництві металу є значно меншою, ніж у доменного виробництва. Про значення доменного виробництва говорить також й те, що за 14 років у період між 2000 і 2014 роками світове виробництво чавуну у доменних печах зросло у понад як 2 рази — з 575,87 млн т до 1183,451 млн т відповідно.[4]
У 2004 році кількість доменних печей у світі оцінювалася у 800 одиниць.[5][6] В Україні у 2008 році було 43 доменних печі[7], станом на 1 вересня 2010 року було 36 доменних печей, з них в експлуатації перебували 31 доменна піч[8] (з початком війни на сході України в зоні ОРДЛО опинилися 9 доменних печей). [джерело?]
Однією з найважливіших характеристик доменної печі є її корисний об'єм, від якого за всіх інших рівних умов залежить продуктивність печі. Найменші доменні печі мають об'єм у кілька сотень кубічних метрів. Найбільша у світі доменна піч має об'єм 6000 м³, вона розташована на Кван'янському металургійному комбінаті (Південна Корея).[9][10] Найбільшою в Україні доменною піччю є доменна піч № 9 заводу «Криворіжсталь», що має об'єм 5034 м³, була найбільшою у світі.
Найбільші доменні печі світу
№ | піч | підприємство | місто | об'єм, м³ | рік побудови або реконструкції |
---|---|---|---|---|---|
1 | № 1 | Кван'янський металургійний комбінат, POSCO | Кван'ян ![]() | 6000[11] | 2013 |
2 | № 2 | Oita Works, Nippon Steel | Ойта ![]() | 5775[12] | 2004 |
3 | № 4 | Пхоханський металургійний комбінат, POSCO | Пхохан ![]() | 5600[11] | 2011 |
4 | № 5 | Северсталь | Череповець ![]() | 5580[13] | 1986 |
5 | № 4 | Kimitsu Works, Nippon Steel | Кіміцу ![]() | 5555[12] | 2003 |
6 | № 4 | Кван'янський металургійний комбінат, POSCO | Кван'ян ![]() | 5500[11] | 2009 |
7 | № 5 | Пхоханський металургійний комбінат, POSCO | Пхохан ![]() | 5220[11] | 2014 |
8 | № 9 | Криворіжсталь, нині ArcelorMittal | Кривий Ріг ![]() | 5034 | 1974 |
Доменна піч, залежно від її об'єму, за добу переплавляє від кількох тисяч до 18-20 тис. т (від 50 до 250 залізничних вагонів) шихтових матеріалів.[14][15] Продуктивність доменних печей, залежно від об'єму, становить від кількох сотень тонн до понад 12000 — 13500 т чавуну на добу,[10][15][16] найбільшої доменної печі — до 16000 т на добу.[16] Кампанія доменної печі, тобто тривалість безперервної роботи від «задування» (пуску) до «видування» (зупинки), становить 10 — 15 років,[10][17] іноді 20 років і більше.[17]
В Україні проектуванням доменних печей та їхніх допоміжних агрегатів займаються «Укрдіпромез», «Діпросталь» та декотрі інші проектні організації.
У доменних цехах металургійних заводів будується, як правило, кілька доменних печей. Більшість процесів на доменній печі механізовані і автоматизовані.
Етимологія
Назва «доменна піч» або «домна» (дав.-рус. дъмница), пов'язана з прасл. *dъmǫ, *dǫti («дму», «дути»), тобто «піч, яку роздувають». Аналогічно від «димати» («надувати міхом») утворене слово «демня» («горно», «кузня»)[18].
Історія
Загальна історія
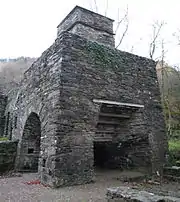
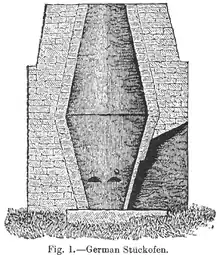
Доменні печі з'явилися у Європі приблизно в середині XIV — початку XV століть.[19][20][21] Їх почали будувати на території сучасної бельгійської провінції Намюр приблизно 1340 року.[21] Перший опис виплавлення чавуну, за деякими даними, міститься у працях французького єпископа Генриха з Пуатьє і датується 1371 роком.[22]
Доменна піч була створена чисто досвідним шляхом. До виникнення доменних печей протягом кількох тисячоліть основним способом отримання заліза з руди був сиродутний процес у так званих сиродутних горнах. Сиродутним процесом отримували залізо тільки у напівтвердому, тістоподібному стані — у вигляді так званого губчастого заліза, просяканого шлаком. При обробці його молотом, з нього видалявся шлак і отримували залізну заготовку, з якої виготовляли потрібні вироби.[23]
Сиродутне горно внаслідок розвитку перетворилося на більшу за розмірами сиродутну піч (такі печі також часто називають горном). Подальше збільшення розмірів сиродутної печі, головним чином у висоту, і кількості подаваємого повітря призвело до змін у процесах і перетворення її у домницю (штюкофен), що разом з напівтвердим губчастим залізом видавала новий продукт — рідкий чавун. Через те, що чавун не піддавався куванню, металурги спочатку вважали його браком. Однак, пізніше навчилися робити з чавуну виливки і переробляти його у кричному горні на ковке залізо. Подальший розвиток домниці перетворив її на доменну піч, що принципово не змінилася до нашого часу, продуктом якої став тільки чавун у рідкому стані, який потім переробляли у кричному горні. Таким чином, замість безпосереднього отримання готового до обробки заліза з руди у сиродутному горні, тобто одноступеневого процесу, з'явився двоступеневий процес — отримання чавуну у доменній печі і подальша переробка його на ковке залізо (пізніше — на сталь) у іншому агрегаті — кричному горні. Такий процес виявився економнішим і продуктивнішим. Весь подальший розвиток металургії проходив як вдосконалення цього двоступеневого способу виробництва сталі. Пізніше для переробки чавуну на сталь були розроблені пудлінгова піч, мартенівська піч, конвертер.[23]
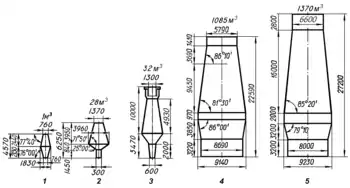
Розвиток доменної печі відбувався перш за все шляхом збільшення її розмірів. Якщо у XV—XVI століттях висота доменних печей становила 4,5 м, то у 18 столітті вона досягла 10—13 м, сучасні доменні печі мають висоту понад 33 м.[23][24] Збільшення розмірів доменних печей давало збільшення продуктивності. У 15 — 16 століттях продуктивність печей була 1,6 т на добу, у XVIII столітті — 16—17 т,[23] найбільші доменні печі кінця XX століття виплавляли до 12000 т чавуну на добу.[19] Збільшення розмірів печей стало можливим завдяки розвитку повітродувних засобів. Спочатку для подачі дуття використовувалися клиноподібні міхи, що приводилися у дію потужним водяним колесом. Потім з'явилися циліндричні міхи, пізніше — газові повітродувки, ще пізніше — турбоповітродувки.
Як паливо здавна використовували деревне вугілля. Розвиток металургії у Англії вже у XVI столітті призвів до вирубки більшої частини лісів країни, що викликало необхідність пошуку нових видів палива. У XVII столітті Дод Додлей здійснив вдалі доменні плавки на кам'яному вугіллі. З 1709 року А. Дербі I робилися спроби використання у доменній плавці кам'яновугільного коксу як домішки до деревного вугілля. В 1735 році А. Дербі II успішно застосував в доменній плавці кам'яновугільний кокс без домішки інших видів палива. Разом з тим, доменне виробництво на деревному вугіллі існувало до кінця XIX століття, а у країнах з великими запасами деревини — до другої половини XX століття й, навіть, до початку XXI століття (Бразилія).
1829 року Д. Нілсон здійснив гаряче дуття на доменній печі на заводі Клайд у Шотландії. Використання гарячого дуття дозволило економити значну кількість палива. У 1857 році Е. Каупер винайшов повітронагрівач регенеративного типу. 1850 року Дж. Паррі розробив конусовий завантажувальний пристрій, а 1907 року А. Мак-Кі запатентував обертовий розподільник шихти, що поліпшував розподілення шихти на колошнику печі.
Велике значення на розвиток доменного виробництва здійснило поліпшення підготовки матеріалів до плавки. У XX столітті залізні руди після збагачення почали грудкувати — виготовляти агломерат та з другої половини XX століття — окатки. У XX столітті розвиток технології доменного виробництва був пов'язаний з початком використання природного газу, пило-вугільного палива і кисню, підвищення тиску газу в печі тощо.[23]
Рік | 1820 | 1830 | 1840 | 1850 | 1900 | 1913 | 1920 | 1970 | 1980 | 1990 | 2000 | 2010 | 2016 | 2017 |
---|---|---|---|---|---|---|---|---|---|---|---|---|---|---|
Виробництво, млн. т | 1 | 1,8 | 2,7 | 4,7 | 39,81 | 79,3 | 62,85 | 427 | 497,46 | 530,26 | 577,03 | 1025,77 | 1159 | 1174,4 |
Найбільшим виробником чавуну до XVII століття була Велика Британія, у XVII столітті на перше місце вийшла Швеція, з 1740 по 1804 роки перше місце посідала багата лісами (необхідними для виробництва деревного вугілля) Росія, потім — знову Британія, в доменному виробництві якої почали широко використовувати кокс. З 1897 року на перше місце вийшли США, з 1970 року — СРСР, причому близько 48 % його чавуну в той час виплавлялося на заводах України.[22] [27] З 1992 року найбільшим виробником чавуну є Китай.[4]
У 1979 році у світі налічувалося загалом близько 1000 доменних печей,[28] у 1990 році їх у світі було близько 541,[29] однак, не дивлячись на зменшення їх кількості, у зв'язку з ростом їхньої продуктивності виробництво чавуну у світі при цьому навіть дещо зросло. У 2004 році кількість доменних печей у світі оцінювалася у 800 одиниць.[5][6]
Історія доменного виробництва в Україні
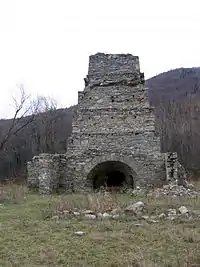
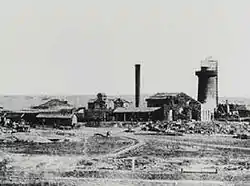
На території України перші доменні печі з'явилися у 60-х роках XVIII ст. на Закарпатті. До того, у XIV—XVIII століттях, на території України на Поліссі, в Галичині, на Полтавщині й Харківщині було поширене виробництво заліза у руднях в горнах і невеличких домницях (димарках). Перший на Правобережному Поліссі доменний завод «Висока піч» (Високопічанський) було введено в дію 1773 року. У 1799 році на Луганському чавуноливарному заводі було введено в дію першу доменну піч на сході України.[27]
У 19 і 20 століттях доменне виробництво України по багатьох показниках посідало провідне місце у доменному виробництві царської Росії та СРСР. Тут вперше впроваджувалися багато-які нове обладнання та нові технології виробництва.[27]
У 2-й половині 19 століття в Україні, що має потужну сировинну базу, будувались численні металургійні заводи, переважно за рахунок іноземного капіталу. На кінець 19 століття Україна стала у царській Росії основним виробником продукції чорної металургії загалом і доменного виробництва зокрема. На початку 20 століття доменні печі України були найпродуктивнішими у всій Російській Імперії. У 1913 році на заводах царської Росії працювала 151 доменна піч,[30] з яких на території України працювало 42 доменних печі, які давали 68 % загальноросійського виробництва чавуну (крім України, доменні печі працювали на заводах Польщі, Фінляндії та власне Росії).[31] Україна протягом десятиліть — до 1970-х років включно залишалася основним виробником продукції доменного виробництва в СРСР.[22][27]
З 1991 року, тобто з часу здобуття Україною незалежності, найпродуктивнішим для доменного виробництва країни був 2007 рік, коли було вироблено 35,647 млн т чавуну (данні за період 1991—2016 роки).[3]
План доменного цеху
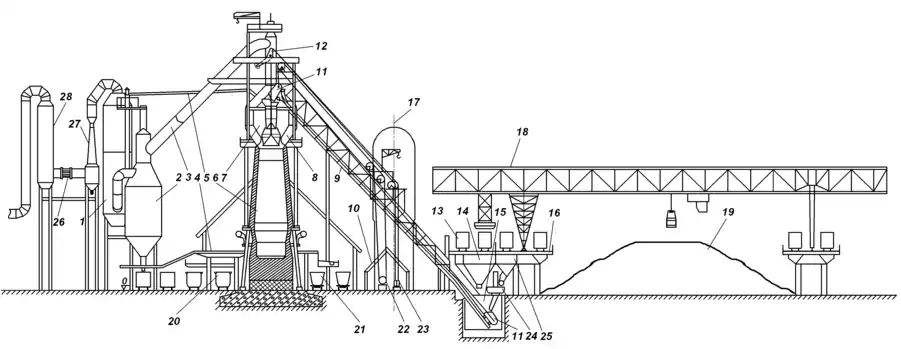
Доменний цех металургійного заводу являє собою комплекс споруд: доменних печей, повітронагрівачів, газоочисників, рудного двору, енергетичного господарства, залізничних шляхів тощо. Сировина і паливо надходять у доменний цех залізничним або водним транспортом, вони вивантажуються у бункери бункерної естакади або на рудний двір. Під бункерами бункерної естакади розташовані вагон-ваги, що встановлені на залізничні рейки й можуть пересуватися вздовж бункерів. Вони дозовано вивантажують шихтові матеріали з бункерів, перевозять їх до скіпової ями і вивантажують у скіпи. Скіпами шихтові матеріали по скіповому підйомнику пересуваються до верхньої частини печі — на колошник. Над колошником печі розташований колошниковий пристрій, до складу якого входять механізми завантаження шихти, відведення доменного газу, а також допоміжні пристрої і механізми. Через засипний апарат матеріали завантажуються у доменну піч. На багатьох доменних печах великого об'єму використовуються не скіпові підйомники, а стрічкові конвеєри. Через колошник по газовідводах з печі відводиться доменний газ, що утворюється в ній внаслідок хімічних процесів. Газ виносить з печі дрібні часточки щойно завантажених матеріалів, тому він спрямовується у систему газоочищення, де звільняється від пилу. До системи газоочищення відносяться пиловловлювач, скрубер, труба Вентурі та дросельна група.
У доменну піч безперервно подається гаряче повітря, нагріте у розташованих біля неї повітронагрівачах. Біля печі дещо нижче рівня повітряних фурм встановлюють ливарний двір, на якому розташовують жолоби для чавуну і шлаку, по яких чавун і шлак після виходу з печі через спеціальний випускний отвір, спрямовуються відповідно у чавуновози і шлаковози.
Будова доменної печі
Конструкція доменної печі
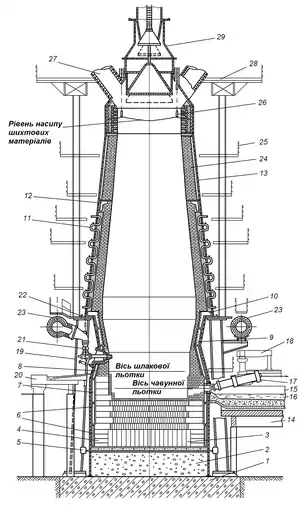
Доменна піч являє собою вертикально розташовану споруду, виготовлену зі сталі і вогнетривких матеріалів. Висота власне доменної печі становить від 20[32] до 33,5[23] — 35 м,[32] при цьому, висота всіх металоконструкцій найбільших доменних печей разом з колошниковим пристроєм і газовідводами може сягати до 100—130 м.[10]
Доменна піч споруджується на фундаменті, що призначений для рівномірної передачі тиску печі з завантаженими у неї сирими матеріалами на ґрунт. Він несе великі навантаження. Вага доменної печі об'ємом 5000 м (найбільша в Україні), заповненої шихтою, сягає 440 кН, а з врахуванням можливих динамічних ударів при обваленні завислих матеріалів — до 490 кН.[33] (с. 359) Фундамент поділяється на дві частини — верхню, надґрунтову, що зветься пнем, і нижню, що зветься підошвою. При слабкому ґрунті фундамент можуть спирати на штучні основи, наприклад на палі. Верхня частина фундаменту робиться з жароміцного бетону, бо фундамент доменної печі зазнає інтенсивного теплового впливу.
На горизонтальну поверхню верхньої частини фундаменту кладуть вогнетривке мурування дна горна — під.
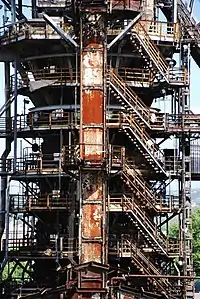
Доменна піч ззовні поміщається у металевий кожу́х, зроблений зварюванням між собою вальцьованих листів з високоміцної сталі. Товщина кожуха поду і горна становить 30 — 50 мм, заплечиків — 30 — 50 мм, шахти, колошника і купола печі — 22 — 45 мм. На печах об'ємом до 3000 м³ кожух поду, горна і заплечиків спирається на фундамент. Кожух шахти спирається на колони, для чого його нижня частина закінчується опорним кільцем (маратором). Опорне кільце підтримує кожух і вогнетривке мурування шахти й передає навантаження від конструкцій верхньої частини печі на колони. На печах об'ємом понад 3000 м³ мараторне кільце відсутнє і колошниковий пристрій спирається на шість колон або на шатро будівлі ливарного двору.
Нижня частина колон, на які спирається кожух шахти печі, кріпиться до фундаменту печі. На печах встановлюють чотири опорних колони. Для надання більшої стійкості й кращого доступу до горна колони встановлюють з певним нахилом.
Зсередини доменна піч футерується вогнетривким муруванням. Для футерування доменної печі використовують шамотну, високоглиноземисту і вуглецеву цеглу.
Для зменшення руйнування вогнетривкого мурування між кожухом і муруванням встановлена система охолодження. По периметру до кожуху кріпляться плитові або горизонтальні холодильники. Плитові холодильники являють собою металеву плиту з чавуну з розташованим у ній зміяком зі сталевих безшовних труб, по якому циркулює вода. Шахта печі на 2/3 висоти охолоджується вертикальними холодильниками або рядами труб, залитих у бетон стінок шахти. Для охолодження шахти печі використовують систему випарювального охолодження.
Для доступу до різних ділянок печі і обладнання, вона зовні оточується перехідними майданчиками.
У нижній частині доменної печі в її стінці і муруванні робляться спеціальні отвори для періодичного випуску рідких продуктів плавки — чавуна і шлаку — чавунні і шлакова льотки. На доменних печах великого об'єму встановлюють чотири чавунних льотки.
У верхній частині горна на фурменній зоні розташовуються фурменні прилади, через які у доменну піч подається нагріте повітря — дуття. Саме в цій ділянці печі відбувається горіння коксу і температури досягають найбільшого значення 1900—2000 °C. По мірі підвищення вгору температура знижується, і у колошника доходить до 200—350 °C.
Профіль
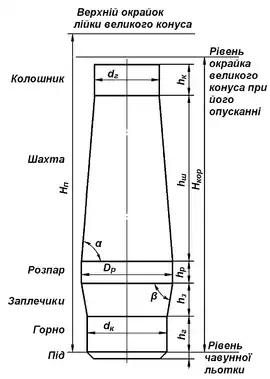
Доменна піч є плавильною піччю шахтного типу, вона має витягнутий у висоту робочій простір. Внутрішній обрис робочого простору печі по вертикальному перетину називається профілем доменної печі. У горизонтальному перерізі піч кругла. Профіль печі поділяється на п'ять частин, кожна з яких має свої геометричні обриси і технологічне призначення. Досвід багатьох століть встановив таку найраціональнішу форму профілю, яка описується певними закономірностями.[23]
Верхня частина доменної печі називається колошником. Вона має циліндричну форму і слугує для завантаження шихти. Через неї також виходять гази, що утворюються в печі (колошниковий газ). Нижче колошника розташована найбільша по висоті і об'єму частина домни — шахта, що за формою являє собою зрізаний конус, який розширюється донизу. Це розширення необхідне для полегшення опускання вниз завантажених твердих матеріалів при збільшенні їхнього об'єму при нагріванні. До нижньої частини шахти примикає найширша частина печі, що має форму циліндра — ро́зпар, в якому відбувається розплавлення шихти. Призначення розпару полягає в тому, що він, з'єднуючи шахту з заплечиками, ліквідує тупий кут, в якому могли б затримуватися грудки матеріалу. Нижче розпару розташовані заплечики, що мають форму зрізаного конуса з меншою основою внизу. Такий переріз тут пояснюється зменшенням об'єму матеріалів внаслідок вигорання коксу і утворення рідких продуктів плавки. Нижньою частиною профілю є горно, що має форму циліндра, у якому відбувається горіння коксу і збираються рідкі продукти плавки. Горно розділяється на дві частини, верхню — фурменну зону, в якій встановлені фурми для вдування повітря в піч, і нижню — металоприймальник, де збираються рідкі продукти плавки. Найнижча частина печі називається подом.[23]
Така будова робочого простору створює сприятливі умови для протікання необхідних аеродинамічних і фізико-хімічних процесів. Такий профіль доменної печі виник не відразу, а внаслідок накопичення досвіду і розвитку профілю протягом століть.
Параметри профілю
Основними розмірами профілю доменної печі є повна і корисна висота, висота окремих частин — колошника, шахти, розпару, заплечиків і горна, діаметри горна, розпару і колошника. Розміри профілю доменної печі визначають розмір доменної печі, що характеризується величиною корисного об'єму. Корисний об'єм є основним розміром доменної печі.
- корисна висота — відстань від чавунної льотки до поверхні матеріалів на колошнику. Через те, що рівень насипу матеріалів може змінюватися, то умовно за цей горизонт приймається положення нижня окрайка великого конуса при його опусканні. Максимальна висота сучасної доменної печі становить понад 33,5 м.
- повна висота — відстань від чавунної льотки до верхньої окрайки спірального кільця кожуха колошника, на якому лежить лійка великого конуса засипного апарату.
- корисний об'єм — об'єм, заповнений шихтовими матеріалами і продуктами плавки. Об'єм від осі чавунної льотки до пругу (окрайка) великого конусу у відкритому положенні. У СРСР будувалися типові́ доменні печі об'ємом 930, 1033, 1386, 1513, 1719, 2002, 2300, 2700, 3000, 3200, 5000, 5500 м³.[34] Окремі з них будувалися в Україні.
- висота горна — відстань від осі чавунної льотки до нижньої окрайки заплечиків.
Рудний двір
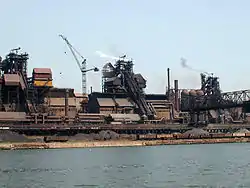
_-_U.S._Steel_Duquesne_Works%252C_Blast_Furnace_Plant%252C_Along_Monongahela_River%252C_Duquesne%252C_Allegheny_County%252C_HAER_PA%252C2-DUQU%252C3A-27.tif.jpg.webp)
Біля доменних печей облаштовують рудні двори — склади рудних матеріалів і палива, на яких створюється запас матеріалів, призначений для забезпечення безперебійної подачі матеріалів у доменні печі. Окрім створення запасу, рудний двір може використовуватися для усереднення матеріалів. При подачі сировини залізничним транспортом запас матеріалів на рудному дворі має забезпечувати безперебійну роботу доменного цеху протягом 1,5 — 2 місяців.[24]
У доменному цеху будується один рудний двір, що обслуговує всі доменні печі. Він розташовується біля доменних печей вздовж їхнього фронту. Розміри і будова рудного двору залежать від кількості матеріалів, які треба зберігати, віддаленості заводу від джерел сировини і способів доставки матеріалів у доменний цех. З одного боку рудний двір обмежений бункерною естакадою, а з іншого — приймальною траншеєю або стоянами, які розташовані вздовж нього по всій його довжині. Рудний двір обслуговується рудними перевантажувачами — грейферними кранами, що своїми прогонами перекривають всю ширину рудного двору і можуть пересуватися по всій його довжині. Ці крани призначені для перевантаження матеріалів всередині бункерної естакади, з рудної траншеї до рудного двору та складання матеріалів у штабелі.[24]
Шихтові матеріали постачаються на рудний двір залізничним або водним транспортом. Залізничним транспортом матеріали постачаються у саморозвантажувальних вагонах (напіввагонах, хоперах). Якщо біля рудного передбачена приймальна траншея, матеріали вивантажуються в неї за допомоги вагоноперекидача, а з траншеї на рудний двір — за допомоги рудно-грейферного перевантажувача. Якщо біля рудного двору немає приймальної траншеї і вагоноперекидача, вагони з матеріалами подаються на колію бункерної естакади, розташовану не над бункерами, а над рудним двором. З вагонів, встановлених на бункерну естакаду, вивантаження відбувається шляхом відкриття затворів і люків вагонів, при цьому матеріали з них висипаються на рудний двір. При постачанні матеріалів водним шляхом використовуються судна-рудовози і судна-коксовози, що розвантажуються грейферним краном.[24]
Іноді, за близького розташування копалень, доменні цехи не мають рудних дворів.
Бункерна естакада
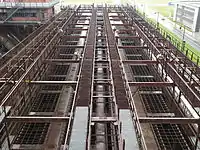
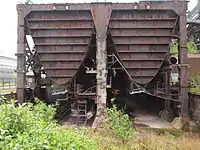
.jpg.webp)
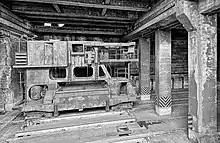
Всі шихтові матеріали надходять у доменний цех у залізничних вагонах. Вони завозяться на бункерну естакаду, побудовану біля доменних печей і зсипаються з вагонів у бункери бункерної естакади або на рудний двір. З бункерів рудна частина шихти, вапняк і кокс за допомоги спеціальних засобів подаються у скіпи або стрічковий конвеєр доменної печі і далі скіпами або конвеєром — у піч.
Бункерна естакада призначена для зберігання шихтових матеріалів і завантаження їх у піч. У доменному цеху будується одна бункерна естакада для всіх доменних печей. Вона являє собою конструкцію з залізобетону, на якій встановлено два ряди рудних бункерів і по два коксових бункера для кожної печі. Для заїзду на бункерну естакаду залізничних вагонів на ній прокладено кілька залізничних колій. Шихтові матеріали вивантажуються з залізничних вагонів у бункери. Для кожної печі є кілька десятків рудних бункерів і два коксових бункера, що будуються безпосередньо біля нахиленого мосту над скіповою ямою. Бункери мають спеціальні закриви, що не дозволяють шихтовим матеріалам висипатися з них. З рудних бункерів матеріали вивантажуються у спеціальний вагон, встановлений у підбункерному приміщенні на залізничних рейках — вагон-ваги, що має механізм для відкривання рудних бункерів, спеціальні бункери — кишені — для перевезення матеріалів і систему зважування матеріалів. Вагон-ваги необхідну кількість шихтових матеріалів перевозять до скіпової ями і висипають їх у скіп. Далі скіп по скіповому підйомнику доставляє шихту на колошник печі для завантаження у піч. Кокс з коксових бункерів потрапляє у скіпи через грохоти, на яких відбувається відокремлення коксового дрібняку, і далі через зважувальну лійку, в якій зважується потрібна для подачі кількість коксу.
Частина шихтових матеріалів вивантажується з вагонів на бункерній естакаді не у бункери, а на розташований біля бункерної естакади рудний двір, де створюється запас матеріалів на випадок перебоїв у їх постачанні.
Подача шихтових матеріалів на колошник
У доменну піч за добу завантажується кілька тисяч тон шихтових матеріалів. Подача матеріалів від бункерної естакади до місця завантаження — на колошник — здійснюється за допомогою скіпових підйомників або стрічкових конвеєрів.
Скіповий підйомник
Скіповий підйомник складається з нахиленого мосту, двох скіпів і скіпової лебідки. Скіпи переміщуються по нахиленому мосту по залізничних рейках, встановлених на нахиленому мосту, за допомогою канатів, що протягнуті до них через шківи від лебідки. Скіпові канати прикріплюються на барабан скіпової лебідки таким чином, що при роботі лебідки канати одного скіпа намотуються на барабан, в той час як канати іншого скіпа розмотуються з барабана і відтак один скіп підіймається й везе шихтові матеріали на колошник, інший опускається до скіпової ями на завантаження. На горішній частині нахиленого мосту рейкові колії роздвоюються на дві криволінійні колії — для передніх і задніх коліс для перевертання і вивантаження скіпа.[23]
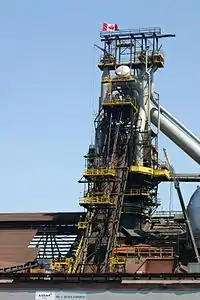
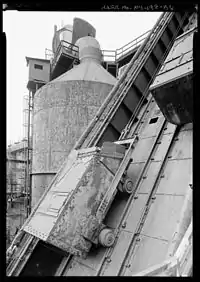
.jpg.webp)
Скипові лебідки розвивають тягове зусилля до 39 т. Місткість скіпів залежить від об'єму печі і становить від 6 до 20 м³, вантажопідйомність — до 35 т.[23]
Стрічковий конвеєр
Стрічковий конвеєр порівняно зі скіповим підйомником є продуктивнішим механізмом і використовується на доменних печах великого об'єму, понад 3200 м³. Конвеєр розміщений в закритій похилій галереї, що монтується на декількох опорах і з'єднує бункерну естакаду з колошниковим пристроєм печі. Кут нахилу конвеєра до горизонту залежить від сили тертя насипної маси матеріалу, необхідної для утримання його на стрічці, і становить 10—11°, що обумовлює велику довжину конвеєра (250—500 м), тому бункерна естакада розташовується на значній відстані від печі. На безперервно працюючому конвеєрі матеріали, що транспортуються, розташовуються окремими порціями з інтервалом, величина якого залежить від роботи завантажувального пристрою печі та інтенсивності плавки. Продуктивність стрічкових конвеєрів доходить до 30 тис. т на добу.[35] На доменній печі об'ємом 5000 м³ («Криворіжсталь») використовується стрічковий конвеєр з гумовою стрічкою завширшки 2 м. Швидкість руху стрічки — 2,0 м/с. Продуктивність конвеєра становить 4000 м³/год.[23]
Засипний апарат
На горішній частині доменної печі встановлюється засипний пристрій. Він слугує для завантаження і розподілення матеріалів у доменній печі. На доменних печах використовуються два типи засипних пристроїв — конусового і безконусового типу.
Засипний апарат конусового типу
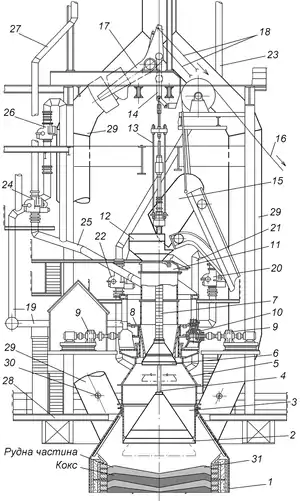
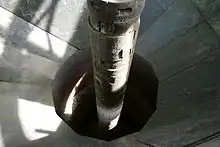
На засипних пристроях з газовідсічними клапанами встановлюються дві приймальні лійки — окремо для кожного скіпа, штанга малого конуса при цьому проходить між приймальними лійками.
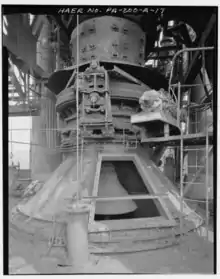
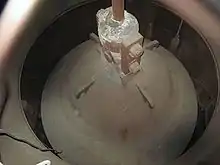
Конструкція конусового засипного апарату складається з приймальної лійки, газовідсічних клапанів, розподільника шихти, що складається з обертової лійки і малого конуса, чаші (лійки) великого конусу і великого конуса. Міжконусовий простір герметично перекрито кожухом, що зветься газовим за́кривом.
Шихтові матеріали, що подаються на колошник скіпами, вивантажуються через приймальні лійки і відкриті газоущільнюючі клапани у обертову лійку малого конуса. При зачиненому газоущільнюючому клапані малий конус опускається і шихтові матеріали з нього зсипаються у лійку великого конуса. Після кількох опускань малого конусу на великому конусі накопичується певна кількість шихтових матеріалів, що зветься подачею. Великий конус опускає шихту у піч при закритому малому конусі.
Однією з основних умов нормальної роботи доменної печі є рівномірне розподілення завантажених матеріалів, що необхідно для рівномірного розподілу газового потоку в печі. Однак, однобічне вивантаження матеріалів з скіпів призводить до утворення у лійці малого конуса однобічного відкосу, що дає нерівномірну за товщиною шару укладку матеріалів. Крім того, при висипанні матеріали сортуються за величиною — дрібняк зосереджується на боці висипання, а грубі грудки — на протилежному боці. Така нерівномірність укладки матеріалів зберігається при зсипанні на великий конус і з великого конуса у доменну піч, що є несумісним з рівномірним розподілом газового потоку.
Тому над великим конусом встановлюють обертовий розподільник матеріалів, за допомогою якого по окружності печі створюють рівномірне розподілення матеріалів і таким чином рівномірний опір проходу газів.
Розподільник шихти складається з обертової лійки, малого конуса зі штангою, обертового корпусу, трибово́ї передачі і приводу. На корпусі розподільника закріплено трибови́й вінець, що перебуває у зчепленні з шестернею, що насаджена на вертикальному валу штибової передачі. Вал приводиться в дію від привода через пару конічних шестерень. Між обертовим корпусом і нерухомим опорним кільцем розподільника є сальникове ущільнення, що облаштоване подвійним сальником, що запобігає виходу газу з міжконусного простору засипного апарату у атмосферу.
На доменних печах з середини 20 століття впроваджено роботу з підвищеним тиском у робочому просторі печі. Тому в середині печі на рівні колошника тиск газу перевищує атмосферний тиск на 1-3 атмосфери. Для опускання великого конусу за таких умов необхідно вирівнювати тиск газу під великим конусом (на колошнику) і тиск над великим конусом (у міжконусовому просторі). Для цього у простір над великим конусом по газонаповнюючому газопроводу подається доменний газ. При роботі з газовідсічними клапанами газ подається і у проміжну ємність над малим конусом. При підійманні скіпа, перед тим, як він перекинеться для висипання матеріалів на малий конус, з простору над малим конусом через спускний газопровід випускається у атмосферу доменний газ, внаслідок чого тиск над газовідсічним клапаном і під ним вирівнюється і таким чином створюються умови для відкривання клапана. Після зсипання матеріалів на малий конус, газовідсічний клапан зачиняється і у простір над малим конусом подається доменний газ для вирівнювання тиску під малим конусом і над ним, після чого малий конус може опускатися і з нього матеріали зсипаються на великий конус. Тиск над великим конусом підтримується рівним тиску під ним постійним подаванням доменного газу у міжконусний простір. Для вирівнювання тиску у різних частинах завантажувального пристрою використовується не повітря, а доменний газ або азот для запобігання створенню гримучої суміші в районі високих температур на колошнику й створення умов для вибуху, що може призвести до виходу з ладу обладнання.
Засипний апарат безконусового типу
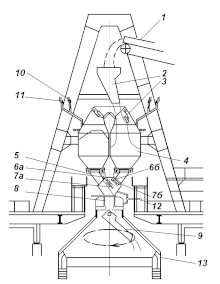
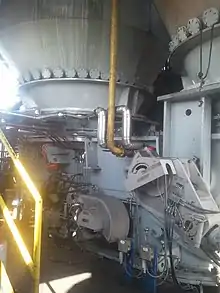
Широкого застосування набули також безконусові завантажувальні пристрої (БЗП) лотікового типу. Безконусовий завантажувальний пристрій спрощує необхідне розподілення шихтових матеріалів на колошнику.[36] Лотік обертається як по окружності, так і переміщається у радіальному напрямку. Визначенням відстані від стін шихту можна зсипати у різні зони по радіусу колошника — ближче до стінок, у проміжну чи осьову зони. Лотіковий засипний пристрій може працювати як зі станціями (фіксованими положеннями лотіка при зсипані однієї подачі шихти), так і у режимі завантаження з одночасним поворотом і нахилом лотіка. У цьому випадку виходить досить рівномірний шар матеріалів по радіусу печі.[37]
При використанні безконусового завантажувального пристрою шихту до нього подають скіпами або стрічковим транспортером через напрямний жолоб і відкритий верхній газовий затвор у два проміжних бункери. У нижній частині проміжних бункерів встановлюються розвантажувальні тракти із шихтовими затворами і нижніми газовими клапанами. Шихтові затвори зберігають нижні газові клапани від зношування матеріалами. Шихтові матеріали утримують матеріали в момент відкривання газоущільнюючих клапанів і контролюють швидкість витікання шихти, що вивантажується і через центральну тічку потрапляє в обертовий лотік. Лотік робить 8 обертів на хвилину, кут нахилу до вертикальної осі може змінюватися від 0° до 50°. Період висипання 80 секунд з урахуванням часу завантаження другого шлюзового тракту.[37]
У світі встановлено понад 500 БЗП різноманітних конструкцій, в Україні працює лише 5 доменних печей, оснащених БЗП (дані 2011 року). У Європі відомим виробником БЗП є люксембурзька фірма Paul Wurth, яка виготовила понад 350 завантажувальних пристроїв.[38] В Україні засипний апарат цієї фірми вперше було встановлено у 1980 році на доменній печі № 9 «Криворіжсталі».[39] В друге у 2011 році на доменній печі № 3 Єнакієвського металургійного заводу при технологічному супроводі Інституту чорної металургії ім. З. І. Некрасова НАН України[40][41]. Модифіковані або ліцензовані БЗП конструкції цієї фірми виготовляються у Японії і в Китаї. В Україні також розроблено лотіковий БЗП.[38]
Система очистки колошникового газу
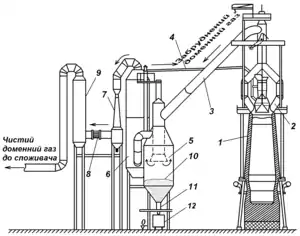
На працюючій доменній печі через колошник виходить велика кількість колошникового газу. Він є горючим газом й використовується для обігріву повітронагрівачів та як енергетичне паливо. Разом з колошниковим газом з доменної печі виноситься значна кількість дрібних фракцій шихтових матеріалів, що називаються колошниковим пилом. Наявність пилу у газі знижує його теплоту згоряння й призводить до засмічення й зносу агрегатів, що використовують колошниковий газ як паливо. В минулому, при роботі печей на непідготовленій шихті без підвищення тиску газу в робочому просторі печі вміст пилу в газі становив 50-60 г/м³, а іноді досягав 100 г/м³. Підготовлення шихти до плавки, зменшення швидкості газу при підвищенні його тиску на колошнику знижує вміст пилу в газі до 15-30 г/м³.[23]
Для уникнення негативної дії пилу газ перед використанням попередньо очищають у спеціальних пиловловлюючих агрегатах. Існує три стадії газоочистки: груба, напівтонка й тонка. Груба очистка здійснюється у пиловловлювачах сухим способом, при цьому вміст пилу в газі зменшується до 1-3 г/м³. Після цього газ проходить напівтонке очищення мокрим способом у скрубері, де вміст пилу знижується до 0,1-0,8 г/м³. Тонке очищення здійснюється у трубі Вентурі і дросельній групі. При тонкому очищенні вміст пилу в газі знижується до 0,005-0,01 г/м³. Розроблено також спосіб очищення газу сухим способом з використанням рукавних фільтрів.[23]
Дросельна група
Сучасні домені печі працюють з підвищеним тиском газу всередині печі. Підвищення тиску газу в робочому просторі печі дозволяє вдувати в неї більшу кількість повітря, підвищуючи тим самим продуктивність доменної печі. При підвищенні тиску газів на колошнику до 160—180 кПа (1,6—1,8 атм) продуктивність печі підвищується на 5—10 %, витрата коксу зменшується на 2—5 %. Крім того, винос пилу зменшується на 35—50 % за рахунок зменшення швидкості газів на колошнику. На сучасних печах тиск у горішній частині печі — на колошнику — підтримується на рівні 0,2—0,3 МПа (2—3 атм).[23]
Для підвищення тиску газу у робочому просторі вводиться додаткова перепона на шляху руху газу після виходу з доменної печі. Роль перепони на шляху доменного газу, за допомоги якої підвищується тиск газу на колошнику й, відтак, всередині всієї доменної печі, виконує дросельна група. Вона складається з трьох паралельних патрубків діаметром 750 мм, одного — діаметром 450 мм і одного перепускного патрубка діаметром 200—300 мм. На патрубках діаметром 750 і 450 мм встановлюються дросельні клапани. Великі клапани постійно закриті, при цьому підвищується опір у газопроводі і відповідно зростає тиск газу перед дроселями. Відкривають їх лише при переведені доменної печі на роботу з нормальним тиском на колошнику. Газ проходить лише через відкритий клапан, рівень відкриття якого автоматично змінюється залежно від змін газу в печі. Аби уникнути сильної абразивної дії запиленого газу дросельну групу встановлюють на ділянці газопроводу після значної очистки — за трубою Вентурі.[23]
Окрім створення підвищеного тиску, дросельна група бере участь у тонкому очищені доменного газу. Перед клапанами газ змочується водою, що подається у газопровід через форсунки. Патрубок діаметром 200—300 мм призначений для випуску шламу. При дроселюванні газу, тобто проходженні через дросельні клапани, газ має велику швидкість і розширюється. Внаслідок зниження температури газу відбувається конденсація випарів, коагуляція пилу і її осадження.[23]
Вогнетривке мурування
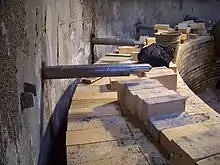
Доменна піч вимуровується вогнетривкою цеглою і блоками. В різних частинах печі вогнетривке мурування (футеровка) зазнає різного впливу, тому матеріал цегли і блоків, з якого воно виготовляється, може бути різним для різних частин печі.[23]
Нижня частина поду вимуровується з вуглецевих або графітованих блоків. Периферійна частина поду вимуровується з вуглецевих блоків. Центральна частина поду вимуровується з високоглиноземистої цегли, встановленої на торець. Нижня частина горна вимуровується з вуглецевих блоків, горішня — шамотною цеглою. Заплечики і тонкостінна частина розпару вимуровуються шамотною цеглою. Товстостінна частина розпару і шахта вимуровуються з високоглиноземистих блоків або з щільної шамотної цегли, що містить не менш як 42 % глинозему.[23]
При вимуровуванні футеровки доменної печі шви поміж цеглою заповнюють розчином, виготовленим з мертелів, що відповідають класу цегли. Для відповідальних видів мурування використовують пластифіковані мертелі, тобто мертелі з добавкою невеликої кількості пластифікаторів. Для заповнення швів між вуглецевими вогнетривами використовують вуглецеву пасту.[23]
Система охолодження
Щоб зменшити руйнування вогнетривкого мурування доменної печі, між кожухом і муруванням встановлюється система охолодження. Вона складається з плитових або горизонтальних холодильників, що встановлюються між муруванням печі й кожухом, по яких циркулює вода (або пара).[16] [23] (с. 231) Окрім стінок печі охолоджуються також всі елементи фурменних приладів.[23] Система охолодження доменної печі має працювати безперебійно, адже навіть короткочасна затримка подачі води призводить до прогару холодильників, а інколи й до тяжчих наслідків. Припинення роботи системи охолодження може стати причиною аварії на доменній печі, спричиненої, зокрема, контактом розплавленого гарячого металу з водою.[42]
Окрім охолодження самої печі, вода використовується також для охолодження шиберів гарячого дуття повітронагрівачів, встановлюваних між повітронагрівачами й трубою гарячого дуття, по якій повітря від повітронагрівачів потрапляє у доменну піч.
Незважаючи на втрати тепла при охолодженні, тепловий ККД печі, що дорівнює відношенню використаного тепла до тепла, що виділилося, є відносно великим, він становить 78 — 87 %.[24]
Елементи системи охолодження
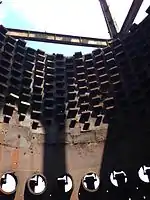
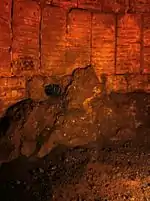
У системі охолодження доменної печі використовують або вертикальні, або горизонтальні холодильники.[16] [33]
Вертикальний плитовий холодильник являє собою металеву плиту, відлиту з чавуну, міді або сталі завтовшки близько 120—160 мм, з залитим в неї зміяком зі сталевих безшовних труб, по якому циркулює вода (або пара). Такі холодильники встановлюються по периметру печі кількома рядами (по висоті) від поду до шахти печі. Вони кріпляться до кожуха печі болтами. Між вогнетривким муруванням і плитовими холодильниками залишається прозір 100—150 мм, що заповнюється вуглецевою масою. Холодильники, призначені для різних ділянок печі, відрізняються формою і деякими конструктивними особливостями, однак принцип їхньої дії однаковий.[23] (с. 231—237) При використанні вертикальних холодильників площа охолодження становить 2 м²/м³ мурування.[33] Мідні холодильники порівняно з чавунними мають кращу теплопроводність. Коефіцієнт теплопередачі між поверхнею мідного холодильника і водою у 49 разів вищій, ніж у холодильників, відлитих з чавуну. Потреба в охолоджувальній воді при використанні таких холодильників на 30-35 % є нижчою.[35]
При використанні горизонтальної системи охолодження, холодильники встановлюються горизонтально у масиві мурування шахти, розпару, заплечиків і фурменної зони.[33] Горизонтальні холодильники встановлюються на відносно невеликій відстані один від одного, вони проникають у товщу мурування на 40 — 50 см.[16] Охолодження низу горна (металоприймача) і бокової поверхні поду здійснюється тільки вертикальними холодильниками. Переваги горизонтальної системи полягають у більшій поверхні охолодження, що сягає 3 м²/м³ мурування, можливості зміни холодильників без зупинки печі на довгий ремонт, кращому збереженні проектного профілю і співвідношення його розмірів.[33] Якщо горизонтальний холодильник протік, він може бути замінений під час зупинки за кілька годин.[16] Недоліками горизонтальної системи охолодження є погана герметичність кожуха, послаблення його вирізами для холодильників, відносна легкість прогару холодильників при оголенні їх по мірі зношення мурування або оповзання гарнисажу.[33]
Система охолодження доменної печі | ||||||
---|---|---|---|---|---|---|
|
Водяне охолодження
Системи охолодження технічною водою потребують великої її витрати — приблизно 1,5 — 1,6 м³/год на 1 м³ корисного об'єму печі.[23] (с. 237) [33] Наприклад, для печі об'ємом 2700 м³ витрата води становить 3320 м³/год, а з урахуванням всіх допоміжних об'єктів печі до 4600 м³/год при водогоні середнього тиску 7,5 атм.[33] Відведення тепла становить 42 КДж/кг води.[33] Вода для охолодження холодильників печі поступає зі спеціальних водних резервуарів (бризкальний басейн тощо). На насосних станціях поряд з працюючими обов'язково передбачені резервні насоси. Для очищення вода пропускається через фільтри, потім вона потрапляє у кільцеві водопроводні труби, що оточують доменну піч, звідки розподіляється по ділянкам печі. Найбільш відповідальні холодильники, прогар яких найнебезпечніший, живляться від індивідуального водопроводу. Інші холодильники об'єднуються у секції і вода перетікає послідовно з одного холодильника у інший.[43]
Випарне охолодження
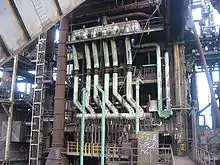
З кінця 1950-х років на багатьох доменних печах замість водяного використовується випарне охолодження. Сутність його полягає в тому, що для поглинання тепла від мурування печі використовується прихована теплота пароутворення. Вода, що поступає у холодильники шахти печі, нагрівається до температури кипіння й всередині холодильників відбувається випарювання води.[23] (с. 237) Аби уникнути утворення накипу всередині трубок холодильників, що різко знижує їхню теплопровідність, у системі випарного охолодження використовується хімічно очищена вода.[24] (с. 324—325) Шар накипу завтовшки лише 1 мм підвищує температуру робочого боку холодильника на 80-100 °C і різко погіршує його охолоджувальну здатність.[33]
Циркуляція води відбувається природним шляхом або із застосуванням насосів. Для циркуляції води і пароводяної суміші система устаткована баками-сепараторами, встановленими у верхній частині печі, що поєднані з холодильниками двома трубами. По одній з них вода потрапляє у нижні холодильники з бака-сепаратора, по іншій — утворювана у холодильниках пароводяна суміш потрапляє у баки-сепаратори, з яких пара йде по паропроводах до споживачів, а вода знову у холодильники. Випарне охолодження має низку переваг порівняно з водяним охолодженням. Випарне охолодження значно зменшує кількість необхідної для охолодження води. При повному переведенні доменної печі на випарне охолодження витрата води на охолодження зменшується у 60, а інколи й більше раз.[35] Однак, практикою встановлено, що випарне охолодження краще використовувати для шахти печі, а для інших її частин, особливо фурменного приладу — водяне. Крім того, при випарному охолодженні відпадає потреба у спорудженні водоводів великих діаметрів, великих насосних станцій, гідротехнічних споруд, а також зменшуються енергетичні витрати.[24] (с. 324—325) Крім того, пара використовується для опалення приміщень.
У систему подається вода при температурі 30 °C і вище. Внаслідок нагрівання й випаровування води від елементів, що охолоджуються, відводиться понад 600 ккал (2520 кДж на 1 кг води), з яких 70 ккал витрачається на нагрівання води до 100 °C (до кипіння), а 539 ккал — на випарювання води (539 ккал — прихована теплота пароутворення води при атмосферному тиску).[43] Постійна витрата технічної води при випарному охолодженні становить 60 — 70 % від витрати при водяному охолодженні. Для печей корисним об'ємом 2700 — 3200 м³ витрата води становить приблизно 1200 м³/год (дані 1989 року).[33]
Обладнання фурменної зони
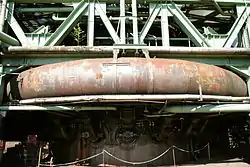
У верхній частині горна доменної печі, що називається фурменною зоною, у вогнетривкому муруванні і кожусі печі розташовані отвори, через які у піч подається повітря, необхідне для горіння палива. У ці отвори вставляються фурмені прилади, що складаються з трьох деталей — амбразури, холодильника й фурми. Деталі фурменних приладів охолоджуються водою, що циркулює по водопровідних трубках, залитих в тіло амбразури, та по порожнинах фурменого холодильника й фурми. Кількість фурм залежить від діаметра горна і становить 12 — 42 фурми,[10][23] (С. 239) [36] інколи до 50 фурм.[44][45] На найбільшій доменній печі в Україні (об'ємом 5000 м³) діаметр горна якої дорівнює 14,7 м, кількість фурм становить 42[46] (за першим проектом їх було 36[24] (С. 328) ). Внутрішній діаметр фурм коливається від 140 до 200 мм.[23]
Нагріте у повітронагрівачі дуття потрапляє з нього у повітропровод гарячого дуття, через який потрапляє у кільцевий повітропровод, що оточує (оперізує) доменну піч в районі заплечиків і монтується до колон печі. Від кільцевого повітропровода дуття підводиться до фурм за допомогою приладів для підводу повітря, що ще називаються фурменними рукавами (інколи їх називають фурменними приладами). Вони робляться з кількох складових частин і є розбірними, що викликано необхідністю можливості зміни перегорілих деталей фурменного прибору. У торці коліна фурменного приладу конструктивно передбачено невеличкий отвір, перекритий склом, через який можна зазирнути всередину працюючої доменної печі для візуального контролю роботи печі.
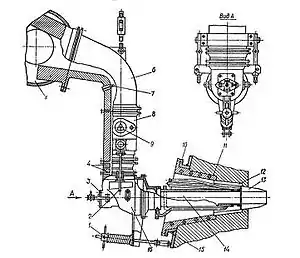
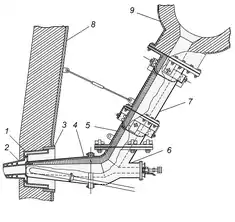
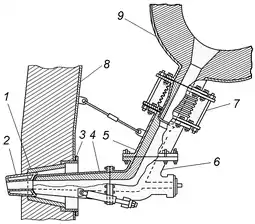
- Приклади фурменних рукавів
- Фурменні рукави з кульовими з'єднаннями.
- Фурменні рукави сильфонного типу. Індія.
- Сильфонні фурменні рукави карданного типу. Через спеціальний отвір у коліні приладу людина зазирає всередину печі.
Існує кілька широко вживаних різновидів приладів для подачі дуття (фурменних рукавів). Особливістю конструкції приладів сильфонного типу є абсолютна герметизація стиків на фурменому рукаві, безшумність і об'єднання в один комплект сопла і коліна. Прилад являє собою роз'ємний фурмений рукав, жорстко закріплений в робочому стані з патрубком повітропровода гарячого дуття і соплом. Сопло при зміні фурми знімають разом з нижньою частиною фурменного рукава за допомоги спеціального пристрою. Герметичність приладу забезпечується сильфонними пристроями, що знаходяться в місцях стику роз'ємної частини фурменного рукава і в з'єднанні його з патрубком повітропровода гарячого дуття. Фурменний прилад сильфонного типу чітко реагує на переміщення кільцевої труби щодо доменної печі і на переміщення кожуха під час їхнього нагрівання. Тому застосування фурменних приладів сильфонного типу не вимагає підбору сопел різноманітних довжин. Сопло футероване і охолоджується водою в місці з'єднання з фурмою.[47] Сильфонні рукави бувають з одним сильфонним компенсатором та з компенсатором карданного типу. Такі рукави забезпечують кращу герметичність і прискорення операцій по зміні фурменного пристрою.
- Фурма (вигляд зсередини доменної печі).
- Вид, що відкривається при знятті (вийманні) фурми з фурменого приладу (наприклад, для її заміни) на зупиненій печі. Матеріали — переважно кокс.
Фурменні прибори сильфонні широко застосовуються на закордонних доменних печах з 2-ї половини 20 століття. У СРСР подібний дослідний прилад, розрахований на роботу фурм з діаметром 140, 150, 160 мм і максимальну температуру гарячого повітря 1400 °C, було спроектовано Діпромезом, однак на доменних печах СРСР він не мав широкого застосування.[47] В Україні окремі машинобудівні заводи виготовляють пристрої для підведення дуття сифльфонного типу.[48]
Повітродувні засоби
.jpg.webp)
У доменну піч щохвилини безперервно вдувається велика кількість повітря, причому, чим більше вдувається повітря в одиницю часу, тим інтенсивніше проходить доменний процес й, відтак, продуктивніше працює доменна піч. Норма подачі повітря в піч становить 1,8 — 2,2 м³/хвил на 1 м³ корисного об'єму доменної печі. Тобто, в піч корисним об'ємом 2000 м³ подається 3600 — 4400 м³ повітря на хвилину,[23] у нормально працюючу доменну піч об'ємом 3800 м³ вдувається 6500 м³/хв дуття (збагаченого киснем до 26 %).[10][16]
В Україні для подачі повітря у доменні печі використовуються турбоповітродувки. Повітродувки дають повітря з тиском від 2,1 атм до 5 атм. В більшості випадків в ролі привода турбоповітродувки використовуються парові турбіни високого тиску, що працюють на парі під тиском 3,5 — 9,0 МПа. Для турбоповітродувки характерною є велика кутова швидкість ротора, що може сягати 2500 — 3400 об/хв.[23] Турбіни встановлюються в окремому цеху і повітря від них до доменних печей йде по повітропроводу, що зветься повітропроводом холодного дуття.
Повітронагрівачі
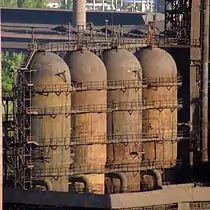
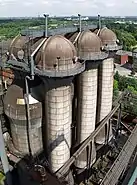
Повітря у доменну піч подається з температурою 900—1300 °C.[10] Для нагрівання дуття використовуються повітронагрівачі. На кожну доменну піч будується 3 або 4 повітронагрівачі. Сучасні повітронагрівачі є модифікаціями повітронагрівачів, винайдених 1857 року англійським інженером Е. Каупером, тому вони інколи також називаються «кауперами».
Каупер є повітронагрівачем регенеративного типу. Він являє собою металевий циліндр з куполом на горі заввишки близько 41 м. Всередині він розділений на дві частини — камеру горіння і насадку, викладену з вогнетривів спеціальної форми, що утворюють канали, по яких можуть проходити повітря і продукти згорання доменного газу. У камері горіння спалюється доменний газ, що є побічним продуктом доменного процесу. Повітронагрівачі споживають 25 — 30 % доменного газу, виробленого у доменному цеху.[49] До нього з метою підвищення калорійності інколи додають невелику кількість природного газу. Продукти горіння по камері горіння підіймаються вгору, проходять купольну частину і потрапляють у насадку, проходять крізь ню у напрямку зверху вниз, після чого потрапляють у димовий кабан і далі у трубу, через яку випускаються у атмосферу. При проходженні гарячих продуктів згоряння доменного газу через насадку, вони нагрівають її. Після нагрівання насадки подача газу у камеру горіння припиняється, він ставиться на дуття — через каупер пропускається холодне повітря, яке проходячи через нагріту насадку нагрівається до великих температур і після цього подається у доменну піч через повітропровод гарячого дуття.[23]
Повітронагрівчі працюють поперемінно — поки один з них стоїть на дутті, два або три інших стоять на нагріві.[23]
Чавунна і шлакова льотки
У нижній частині горна доменної печі міститься чавунна льотка, через яку випускають продукти плавки — чавун і шлак. Раніше використовувалися спеціальні шлакові льотки, однак за останні кілька десятиліть ввійшло у практику випускати чавун і шлак лише через чавунну льотку з розділенням їх один від одного у головному жолобі, який примикає до печі і у який продукти плавки потрапляють під час випуску з льотки. Льотка це отвір діаметром 40 — 60 мм і довжиною 2,5 — 3,5 м,[16] Залежно від об'єму доменної печі, на ній встановлюють від 1 до 2, на великих печах — 3 — 4 чавунних льотки.[10]
Ливарний двір
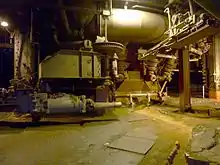
Безпосередньо до печі примикає ливарний двір, на якому розташовані жолоби і канави для транспортування чавуну і шлаку від льотки у ковші, а також прилади для розкриття чавунної льотки та для її закривання після випуску чавуну і шлаку. Від чавунної льотки відходить головний жолоб. Він виготовлений з металевих сегментів, з'єднаних поміж собою болтами. Всередині жолоб футерується вогнетривкою цеглою і зверху за допомоги вібромеханизмів набивається вогнетривкою глиною. Через різницю у густині чавун і шлак накопичуються в печі двома окремими шарами (шлак на поверхні чавуну), тому при випусканні продуктів плавки з печі спочатку з льотки виходить один лише чавун, а потім вони виходять одночасно.[16] Оскільки разом з чавуном через чавуну льотку виходить з печі й шлак, у головному жолобі передбачено пристрій для розділення чавуну й шлаку — скимер. Випущені з печі через льотку рідкі продукти плавки потрапляють у головний жолоб, в якому проходить розділення чавуну та шлаку завдяки різниці в густині. Від головного жолобу відходять у різні боки чавунний жолоб і шлаковий жолоб. По чавунному жолобу рідкий чавун зливається у чавуновози, а шлак по шлаковому жолобу — у шлаковози або надходить безпосередньо до установки припічної грануляції шлаку.
Для подачі чавуновозів і шлаковозів під ливарний двір він встановлюється на колонах, під ним прокладають залізничні рейки. Робочий майданчик ливарного двору будується з залізобетонних плит, що спираються на колони. Будівля ливарного двору, що зветься шатром ливарного двору, виготовляється з металоконструкцій, що спираються на фундамент, й накрита згори дахом, що несе на собі аераційний ліхтар. Для пересування обладнання та матеріалів на ливарному дворі встановлюється мостовий кран.
Сировина і паливо
Матеріали, які завантажують у доменну піч — паливо, рудні матеріали, флюси — називаються шихтою, або шихтовими матеріалами. Всі шихтові матеріали являють собою матеріали у вигляді грудок.
Паливо
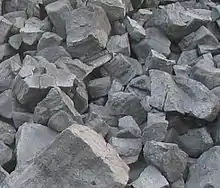
Основним паливом доменної печі є кам'яновугільний кокс. Окрім того, що він забезпечує високі температури в печі, вуглець коксу є відновником заліза з руди, а також кокс, будучи твердим паливом, є розпушувачем стовпа шихти у печі, забезпечуючи її високу газопроникність. У нижній частині печі кокс залишається єдиним твердим матеріалом (інші матеріали тут вже розплавлені) і утворює своєрідну решітку, через яку стікають у горно рідкі продукти плавки.[23] Кокс займає приблизно половину об'єму всієї шихти у працюючій доменній печі. Витрата коксу на сучасних доменних печах, залежно від рівня підготовки шихти і технології, на 1 т переробного чавуну становить 200—450 кг (в Україні — 450—550 кг[50]).
Кокс характеризується великим вмістом вуглецю — 83-87 % і великою теплотою згоряння — понад 6000 ккал/кг. Окрім вуглецю кокс містить певну кількість золи — близько 10 %. Зола являє собою пусту породу коксованого вугілля, яку не вдалося від нього відокремити при збагачуванні перед коксуванням. Чим менше золи в коксі, тим він є якіснішим. Основними компонентами золи є SiO2, Al2O3 (разом до 75 %) і Fe2O3 (10 — 20 %). Для ошлакування золи коксу в піч додають додатковий флюс. Важливим показником якості коксу є вміст в ньому сірки S, що є шкідливою домішкою. При роботі на рудах, що не містять сірки, наприклад, криворізьких, донецький кокс вносить в доменну піч 70 — 95 % всієї вносимої в неї сірки.[23]
Вартість коксу становить 40 — 50 % собівартості чавуну. Крім того, для виробництва коксу придатні лише певні марки вугілля. Тому вже довгий час ведуться пошуки з заміни частини коксу більш дешевим паливом. Частковими замінниками коксу є природний газ, коксовий газ, мазут, пиловугільне паливо (виготовлене з дешевших марок вугілля), відходи пластиків тощо.[36][23][44][51][52] Ці замінники коксу подаються в піч разом з дуттям через форми. З точки зору енергетики та теплового балансу весь кокс може бути замінений недефіцитним пиловугільним паливом (ПВП), виготовленим з неспікливого вугілля, вартість якого, як правило, вдвічі нижча за вартість коксу (для умов України в цінах 2012 року). Однак, оскільки кокс в доменній печі виконує роль не тільки палива (і відновника), але й роль розпушувача стовпа шихти, він не може бути повністю замінений ПВП та іншими замінниками.[23][50] Пиловугільне паливо та інші замінники коксу в наш час дозволяють замінити 30 — 40 % коксу.[36][50]
До початку використання коксу основним паливом доменних печей було деревне вугілля. У США широко використовувався також антрацит.[24] Починаючи з 2000 року, на печах доменного цеху № 1 «Криворіжсталі» почали частково замінювати кокс грудковим антрацитом з витратою його 70 — 100 кг/т чавуну.[53] На початку 21 століття у промислових масштабах деревне вугілля у доменній плавці використовується у Бразилії на печах малого об'єму. Деревне вугілля при цьому виготовляється з евкаліпту, вирощуваного на спеціальних плантаціях.[54]
Рудні матеріали
До 20 століття у доменній плавці використовувалася лише сира залізна руда, яка потрапляла у піч прямо з копалень майже без попередньої підготовки. Однак, руди містять велику кількість пустої породи, що призвело до розвитку у 20 столітті збагачення залізних руд — видалення з рудного матеріалу пустої породи. Перед збагаченням руди подрібнюють і, відтак, виникає необхідність подальшого їх грудкування — виробництва агломерату або окатків. У доменну піч завантажують лише окатки або агломерат, сира руда в доменну піч завантажується лише в окремих випадках у невеликій кількості і її частка у доменній шихті є дуже малою.
Агломерат і окатки містять набагато більше заліза, ніж сира руда, і набагато менше пустої породи. Окатки виготовляють з найбільш дрібнопомелених залізорудних концентратів, використання яких у виробництві агломерату призводить до зниження продуктивності агломашин.[23] Через специфіку виробництва агломерат і окатки дещо відрізняються поміж собою за хімічним складом.
Грудкування залізорудних матеріалів впливає на інтенсивність доменної плавки. Заміна пилуватих руд агломератом, що відбулася у 20 столітті, підвищила продуктивність доменної печі мінімум на 25-30 %, а витрата коксу при цьому знизилася щонайменше на 20 %. Крім того, агломерація дозволяє використання сірчастих руд бо при агломерації з руд видаляється до 85-90 % сірки.[23] Використання офлюсованого агломерату дозволяє вивести зі складу доменної шихти вапняк й, відтак, вивести процес розкладу вапняку з доменної печі на агломераційну стрічку, що помітно поліпшує техніко-економічні показники доменного виробництва. Виготовлення офлюсованих окатків не здобуло широкого застосування через невелику міцність таких окатків.
Флюси
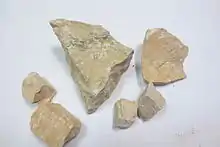
Флюсами називаються добавки, які вводять у доменну шихту для зниження температури плавлення пустої породи шихтових матеріалів. Пуста порода рудної частини і зола коксу складаються з мінералів, основу яких складають як правило кислі оксиди SiO2, Al2O3, які мають великі температури плавлення. Тому додаванням до них мінералів з вмістом осно́вних оксидів CaO і MgO, створюють в доменній печі умови для утворення рідкого первинного шлаку вже при температурі 1300—1400 °C (за участі оксидів FeO).
У доменному виробництві видом основного флюсу є вапняк, що являє собою мінерал кальцит CaCO3, використовується також доломитизоаваний вапняк, що є сумішшю CaCO3 і доломіту CaCO3•MgCO3.
Робота доменної печі
Сушка печі
Доменну піч після будівництва піддають сушці, метою якої є видалення вологи зі швів вогнетривкого мурування. Сушка провадиться гарячим повітрям. Повітря від повітродувної машини подається у піч через попередньо нагріті повітронагрівачі. Під час сушки температура подаваного повітря підвищується поступово, починаючи з приблизно 100 °C і доходячи до 800 °C, зі швидкістю 10 — 15 град/год бо за швидшого підйому температури спостерігається псування вогнетривкої цегли. Протягом сушки поступово підвищують також витрату повітря. Тривалість сушки становить 5 — 6 діб.
Підготовка до задувки
Після завершення сушки припиняють подачу повітря у піч і футеровка печі охолоджується до температури 50 — 60 °C. Охолодження футерівки перед початком завантаження шихти є необхідною для того щоб уникнути загоряння коксу від гарячих стінок печі до закінчення завантаження. Після охолодження печі починається підготовка її до задувки.
Горно доменної печі заповнюють коксом — або через завантажувальний пристрій або транспортером через отвори фурменних приладів. На рівні фурм також кладуть дрова для кращого загоряння коксу. Після заповнення горна коксом ведеться завантаження печі через завантажувальний пристрій до рівня колошника спеціальною задувочною шихтою. Аби захистити під печі від температурного удару від розжареного коксу, ще до завантаження горна коксом на під печі кладуть шар гранульованого шлаку.
Задувочна шихта розраховується на отримання ливарного чавуну, що містить 2 — 3 % Si2 і шлаку невисокої основності.
Задувка
Після того, як доменна піч завантажена по всій своїй висоті — від поду до колошника — шихтовими матеріалами, в неї через фурми подають нагріте у повітронагрівачах повітря — дуття. Початок подачі у піч гарячого повітря є задувкою доменної печі і початком її роботи. У момент задувки температура дуття становить 700—800 °C для швидкого запалення коксу.
Перший шлак з'являється через приблизно 15 годин після задувки, перший чавун з'являється через 20 — 24 години після задувки. Нормальна продуктивність печі досягається приблизно через кілька діб після задувки.
Процеси
Зони у працюючій доменній печі
У працюючій доменній печі утворюються кілька зон, кожна з яких характеризується певним фізичним станом матеріалів (тверді, розм'яклі, рідкі), хімічним складом і температурою матеріалів і газів, фізико-хімічними процесами, що відбуваються в цих зонах. Ці зони в печі можна виокремити у будь-який момент.
![]() | |||||||||||
Зона | Опис зони | ||||||||||
---|---|---|---|---|---|---|---|---|---|---|---|
1. Зона твердих коксу і руди | Кокс і рудні матеріали завдяки відповідній системі завантаження, розташовані окремими шарами, що зберігаються при їхньому опусканні аж до зони розм'якшення і плавління. Нараховується від 35 до 45 шарів рудної частини. Товщина шарів становить 0,5-1 м. Гази проходять між грудками матеріалів, нагрівають їх і відновлюють залізо з оксидів. | ||||||||||
2. Зона розм'якшення і плавління («злипання», або «когезії») | Ця зона має форму перевернутої латинської літери «V» (Λ-подібна зона) і складається з шарів твердого коксу та шарів пустої породи, флюсу і заліза, що розм'якли та плавляться. Шматки породи злипаються у єдине ціле, між ними зникають прозори, тому газ тут проходить переважно через шари коксу. | ||||||||||
3. Зона розпушеного коксу | В цій зоні у твердому стані залишається лише кокс, а шлак і чавун краплями і окремими струмками стікають між шматками коксу донизу. Це зона «рухомого коксу», переважно звідси кокс потрапляє у зони горіння. | ||||||||||
4. Зона щільно запакованого коксу | Кокс запакований щільно, він тут малорухомий, через нього проходить менше газу, ніж у зоні розпушеного коксу. | ||||||||||
Фурмена зона (зона циркуляції) | Вдуваєме у горно дуття реагує з коксом з виділенням тепла і утворенням урешті-решт відновлювального газу. | ||||||||||
Примітки. Подібна форма зон утворюється у печах великого об'єму при відповідній системі завантаження (велика кількість коксу в осьовій частині печі). За інших умов форма зон може бути іншою. Докладніше див. статтю «Доменний процес». |
Процеси окислення
Процес горіння коксу відбувається у горні доменної печі біля фурм. Кокс потрапляє на рівень фурм вже у розжареному стані (нагрівається за час опускання від колошника до фурм), при потраплянні у зону горіння температура коксу становить приблизно 1400—1500 °C. Через фурми у піч подається атмосферне повітря — дуття, попередньо нагріте у повітронагрівачах до температури 1000—1300 °C.[10][16] До дуття як додаток можуть подаватися природний газ, пиловугільне паливо (ПВП) та інші вуглеводні, водяна пара, а також дуття може бути збагачене додатковим киснем. Кількість дуття залежить від об'єму печі і становить 1,7 — 2 її об'єми. Наприклад у нормально працюючу доменну піч об'ємом 3800 м³ вдувається 6500 м³/хв дуття, збагаченого киснем до 26 %.[10][16] Дуття містить від 21 % до 30 % кисню. Кисень дуття з великою швидкістю спалює вуглець коксу і пиловугільного палива. Відбувається реакція
→ МДж
Вуглекислота СО2, що утворюється в ході цієї реакції, при високих температурах, що є у горні, взаємодіє з вуглецем коксу по реакції
МДж
Таким чином, кінцевим продуктом горіння вуглецю коксу і ПВП у горні є монооксид вуглецю СО. Процеси окислення вуглецю коксу і ПВП відбуваються біля фурм у невеликих за об'ємом зонах, що називаються зонами горіння, або зонами окислення. Зола коксу розплавляється і переходить у шлак, що стікає у низ горна і накопичується там. Якщо у піч разом з дуттям через фурми вдувається якесь інше паливо — природний газ, коксовий газ, мазут або пиловугільне паливо, воно так само згорає біля фурм у кисні дуття.
Припродний газ та інші вуглеводні згорають з утворенням CO2 та H2O, які реагують з вуглецем коксу й розпадаються з утворенням CO та H2. Для природного газу кінцева реакція має вигляд
МДж
Повітря, що вдувається у доменну піч, має певну природну вологість, тобто містить воду Н2О. Інколи до дуття додають пару, підвищуючи його вологість, інколи, навпаки, перед вдуванням у піч повітря висушують від вологи. При потраплянні у зони великих температур у горні печі, вода розкладається на водень Н2 і кисень О2. Кисень, що потрапив у піч з парами води, бере участь у процесах горіння палива до СО, а водень переходить у газ. Кінцева реакція описується рівнянням
МДж
При згоранні всіх видів палива у струмені дуття та розкладення водяної пари на відстані приблизно трохи більше 1 м від фурм утворюється газ, що вже не містить вільного кисню і складається з монооксиду вуглецю СО, водню Н2 і азоту N2, що потрапив у піч з повітрям. За атмосферного дуття і за відсутності додатків до дуття горновий газ має такий склад: 35-40 % CO, 1,5-2 % Н2, 58-63 % N2. При збагаченні дуття киснем і вдування вуглеводнів вміст CO та Н2 у ньому зростає, а N2 — знижується.[24]
Процес опускання шихтових матеріалів і рух газу
За одну хвилину в доменній печі залежно від інтенсивності процесу і кількості фурм згорає від 600 кг коксу і більше, тобто понад 1 м³ коксу. Згорання коксу у горні і плавлення матеріалів у нижній частині шахти печі та періодичний випуск продуктів плавки з печі звільняють певний об'єм печі у одиницю часу. У звільнений об'єм під дією власної ваги потрапляють кокс і матеріали з більш високих горизонтів. Так нові порції коксу потрапляють у зони горіння, а матеріали — у нижчі горизонти печі з більшими температурами. Внаслідок цього відбувається поступове опускання всього стовпа шихтових матеріалів і звільнення місця на колошнику для нових порцій шихти. Час перебування матеріалів всередині печі, тобто від моменту завантаження порції матеріалів на колошник і до моменту випуску їх у вигляді готової продукції, становить 5 —8 годин, тобто за добу доменна піч проплавляє приблизно такий об'єм матеріалів, що дорівнює 4 об'ємам печі.[10][16]
Газ, що утворюється у горні доменної печі внаслідок спалювання палива біля фурм і на відстані 1-2 м від фурм складається лише з CO, Н2 та N2, під тиском вдуваємого дуття підіймається вгору до колошника, проходячи крізь стовп шихтових матеріалів. Біля фурм горнові гази мають температуру близько 1900—2300 °C,[16] проходячи стовп шихтових матеріалів вони віддають своє тепло їм, нагріваючи їх, і виходять з печі через колошник з температурою 150—350 °C. По мірі проходження газу від горну до колошника внаслідок фізико-хімічних процесів, що проходять в печі, змінюється також хімічний склад газу — в ньому, наприклад, зменшується вміст CO і збільшується вміст CO2. Газ, що покидає доменну піч через колошник, називається колошниковим газом (або доменним газом). Відстань від фурм до колошника гази проходять, за різними даними, за 5-20 секунд[10] або 6 — 8 секунд.[16] Цього невеликого часу їм вистачає для того, щоб здійснити певну хімічну й фізичну роботу. Повітря вдувається в доменну піч через фурми з тиском 2-5 атм (при цьому на колошнику штучно створюється тиск 1 — 4 атм) і швидкістю близько 200 м/с, доменний газ покидає доменну піч через колошник зі швидкісттю близько 1 м/с (діаметр колошника набагато більший від діаметра фурм, тому тут така невелика швидкість газу).[16] Кількість газів, що утворюються у печі й, відтак, кількість колошникового газу залежить від технології й об'єму печі. У доменній печі об'ємом 3800 м³ за кількості дуття 6500 м³/хв, збагаченого до вмісту 26 % кисню, утворюється 10387 м³/хв (623220 м³/год, або 14 957 280 м³ на добу) колошникового газу.[16]
Розклад вапняку та інших карбонатів
Вапняк у доменній печі розкладається по реакції
МДж
Подібним чином розкладаються й інші вуглекислі солі, якщо вони потрапляють у піч (наприклад, при завантаженні шпатових залізняків).
Розклад кожної грудки вапняку починається на горизонті печі з температурами 760 °C і продовжується по мірі опускання стовпа шихти і подальшого прогрівання вапняку. Вуглекислий газ CO2, покинувши грудку вапняку, переходить у газ. Якщо CO2 виділилося до горизонту температур 1000 °C, то воно виходить з печі разом з газом, якщо виділилося при температурах, вищих за 1000 °C, то реагує з вуглецем коксу по реакції
МДж,
тобто збільшує вміст CO у газі і зменшує вміст C у коксі. За розрахунками, 66 — 75 % вуглекислого газу, виділеного з вапняку, реагує з вуглецем коксу.
Процеси відновлення заліза
Відновленням при доменному процесі вважається процес віднімання кисню у оксиду з перетворенням його у елемент або оксид, що містить менше кисню, аніж оксид, що відновлюється. Відновниками у доменній печі є вуглекислий газ CO та водень Н2, які мають більшу хімічну спорідненність до кисню, ніж елемент заліза, оксид якого відновлюється. Азот N2, будучи інертним газом, участі у хімічних процесах всередині доменної печі не бере. Вуглець коксу C поки матеріали перебувають у твердому стані майже не бере участі у процесах відновлення через малу площу контакту твердих матеріалів та коксу.
В умовах доменної печі окрім заліза, що відновлюється повністю, у невеликих кількостях відновлюються й інші елементи, наприклад, Si і Mn. Для відновлення Mg, Al і Ca з оксидів пустої породи температури в доменній печі є недостатньо високими.
Верхня частина доменної печі служить для завантаження шихти. В шихті є руда, кокс і шлакотворні матеріали, що сприяють зниженню температури плавлення шлаку і видаленню шкідливих домішок. У домні розплавляють не залізняк, а агломерат (дрібну породу, що спікається в шматки) або окатки (грудки сферичної форми, що отримуються з дрібної руди або тонкоподрібненого концентрату).
В печі на різній висоті встановлюється різна температура, завдяки чому протікають різні процеси переходу руди в метал.
Відновлення відбувається поетапно, з послідовним відокремленням кисню і переходом вищих оксидів у нижчі
Оксид вуглецю CO проникає у шпарини рудних матеріалів, віднімає кисень від оксидів заліза, перетворюючись на вуглекислий газ CO2, який переходить у газ. Відновлення кожного шматка залізорудних матеріалів починається від його поверхні й триває до середини шматка. Починаючись ще у зонах, близьких до місця засипання на колошнику, відновлення триває весь час поки матеріали опускаються до зон плавління.
Результуючі хімічні рівняння відновлення монооксидом вуглецю і воднем мають вигляд
Залежно від того, при яких температурах відбувається реакція відновлення, утворені при них CO2 і H2Oпара ведуть себе по-різному. У області температур нижче 950—1000 °C утворені CO2 і H2Oпара переходять у газ, збільшуючи у ньоу таким чином вміст CO2 і H2Oпара. У області температур вище 950—1000 °C утворена CO2 і водяна пара H2Oпара вступають у реакцію з вуглецем коксу. Наприклад, для FeO і CO реакція описується так
МДж
МДж
Результуюче рівняння реакції має вигляд.
МДж,
тобто врешті-решт витрачається лише вуглець коксу, а кількість CO у газі не змінюється. Відновлення заліза газами CO і H2 з утворенням CO2 і H2Oпара прийнято називати непрямим відновленням, а відновлення заліза за хімічною реакцією, при якій витрачається лише вуглець коксу та з утворенням CO — прямим відновленням. У нормально працюючій доменній печі прямим шляхом відновлюється лише частина FeO, реакції відновлення інших оксидів заліза — Fe2O3, Fe3O4 — і частина FeO встигають завершитися непрямим шляхом за той час, поки опускається шихта.
Утворення чавуну і шлаку
Відновлене залізо в присутності кокса насичується вуглецем і виходить сплав, що містить 2 — 4 % вуглецю. Такий сплав називається чавуном. Він крихкий. У нього входять невелика частка кремнію і марганцю. В кількості десятих часток відсотка до складу чавуну входять також шкідливі домішки — сірка і фосфор.
Чавун розплавляється і стікає в горн, а шлаки, на поверхню чавуну. Рідкі продукти плавки видаляються через чавунну льотку. Рідкий чавун має більшу питому вагу (7,2 т/м³) аніж шлак (біля 2,3 т/м³), тому в горні печі чавун накопичується на поді, а шлак — на поверхні чавуну. За сучасного рівня доменного виробництва в печі утворюється приблизно 320 кг шлаку на 1 т чавуну.[16]
безпосередньо до чавунної льотки прилягає головний жолоб в якому проходить розділення чавуну та шлаку завдяки різниці в густині. чавуну через чавунну канаву зливається у чавуновози або міксери, а шлак — у шлаковози або надходить безпосередньо до установки припічної грануляції шлаку.
Видувка доменної печі
Кампанія доменної печі, тобто її, умовно кажучи, безперевна робота, триває 15-20 років. По завершенні кампанії печі або для виконання великих капітальних ремонтів печі її робочій простір має бути звільнений від шихтових матеріалів. Звільнення робочого простору пчі від шихтових матеріалів називається видувкою доменної печі.
Видувка полягає у проплавленні шихтових матеріалів, що перебувають у печі, без завантаження нових порцій. При цьому висота стовпа матеріалів в печі зменшується і врешті-решт знижується до рівня фурм.
Наприкінці видувки металоприймач горну печі звільняється від так званого «козлового» чавуну, що накопичується нижче рівня осі чавунної льотки і випускається з печі через спеціально зроблений отвір, розташований нижче осі чавунної льотки.
Зупинки доменної печі
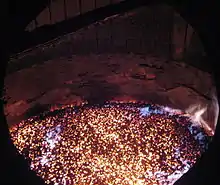
Доменний процес — безперервний, однак протягом кампанії доменна піч може бути зупинена з тієї чи іншої причини — на планово-запобіжний ремонт, а також для зміни фурми, для ремонту якої-небудь ділянки печі або її обладнання, який не може бути проведений на ходу. Зупинка доменної печі полягає у припиненні подачі дуття і припиненні завантажування шихтових матеріалів в піч. При цьому доменну піч відокремлюють від повітропроводів і газової системи заводу закриттям відповідних клапанів і заглушок. Перед зупинкою печі завжди роблять випуск чавуну, щоб звільнити горно печі від продуктів плавки для того, щоб при осіданні стовпа шихти, що відбувається за відсутності дуття (підтримуюча дія дуття зникає), не відбулося вичавлювання рідких продуктів плавки і залиття ними фурм.[24]
Зупинки доменної печі бувають короткочасні без запалювання газу на колошнику, довгочасні з запалюванням газу на колошнику та аварійні зупинки. Аварійні зупинки відбуваються при аварійних ситуаціях, викликаних несподіваним припиненням подачі повітря, води на охолодження печі і електроенергії та при появі ознак прогару вогнетривкого мурування і холодильників нижньої частини печі.
Робота біля доменної печі
Керування роботою печі
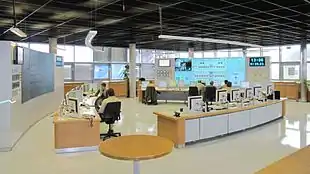
Для нормального проходження процесу плавки у доменній печі і одержання продуктів плавки потрібного складу необхідно слідкувати за процесом і вжити потрібних заходів для його регулювання: міняти співвідношення між залізорудними матеріалами і коксом, витрату флюса, параметри завантаження шихти, раціонально добирати температуру і кількість дуття.
При спільному розгляді показань приладів можна визначити причини окремих порушень ходу печі й вжити необхідних заходів по їх ліквідації.
Керування ходом доменної печі здійснюється зі спеціального приміщення, що облаштовується біля доменної печі, — пульту керування доменною піччю. Операції з керування ходом доменної печі здійснюють майстер печі й газівник.
Горнові виконують підготовуку ливарного двору до випуску чавуну і шлаку та беруть безпосереднью участь у випуску продуктів плавки.
- Ливарний двір під час випуску чавуну
- Розкриття чавунної льотки буровою машиною.
- Випуск продуктів плавки з чавунної льотки.
- Спостереження за випуском біля льотки.
- Головний жолоб, що в ньому відбувається розділення чавуну й шлаку.
- Обслуговування шлакового жолоба горновим під час випуску.
- Зливання чавуну у чавуновоз міксерного типу, що встановлюється під ливарним двором.
- Продувка льотки. Інколи супроводжується значним викидом з печі газу, коксу й крапель рідких матеріалів.
- Закриття чавунної льотки гарматою
Контрольно-вимірювальні прилади
Доменні печі устатковують великою кількістю контрольно-вимірювальних приладів для реєстрування і вимірювання різноманітних параметрів, по яких слідкують за ходом доменного процесу й за станом доменної печі. Ними вимірюють верхній рівень шихти в печі, тиск, температуру і склад колошникових газів[55]; витрату природного газу або ПВП і вміст кисню в дутті, тиск, кількість і температуру повітряного дуття, перепаду тиску по висоті печі; температуру вогнетривкого мурування різних частин печі[56][57][58]; роботу завантажувального пристрою тощо. Для контролю роботи на доменній печі здійснюється понад 1000 вимірювань, багато з яких використовуються для автоматичного керування окремими параметрами доменної плавки.[38]
Механізація і автоматизація
Керування більшістю процесів на доменних печах механізовано й автоматизовано. На печах автоматизовані операції набору, зважування і завантаження шихти, процеси нагрівання повітронагрівачів, розподіл на кожну фурму дуття, розподілення матеріалів на колошнику, регулювання теплового режиму. Вже у другій половині 20 століття єдиною операцією на доменній печі, якою керували вручну, був випуск чавуну й шлаку.[28]
Ремонти доменних печей
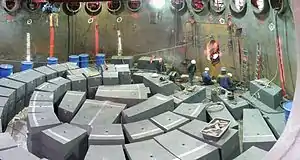
Доменні печі та їхні допоміжні прилади — повітронагрівачі, пиловловлювачі, повітропроводи, газопроводи — в процесі роботи зношуються й потребують періодичних ремонтів. Бувають короткочасні планово-запобіжні ремонти й більш довгострокові капітальні ремонти.
За характером й тривалістю робіт капітальні ремонти доменних печей поділяють на три розряди. При капітальному ремонті I розряду здійснюється заміна всього вогнетривкого мурування, всіх холодильників печі, захисних плит колошника і ремонт всі механізмів. За потреби цей ремонт супроводжується додатковими роботами, наприклад, заміною кожуха печі. Інколи капітальний ремонт I розряду виконується з повною реконструкцією печі зі збільшенням її корисного об'єму. При капітальному ремонті II розряду проводяться ті самі роботи за винятком заміни вогнетривкого мурування і холодильників горну й поду. При капітальному ремонті III розряду відбувається заміна засипного апарату й захисних плит колошника. Тривалість ремонтів регламентована й становить для ремонтів I розряду — до 30 діб, II розряду — 8-12 діб, III розряду — 2-2,5 діб. Міжремонтний період для ремонтів I розряду становить до 12 років, II розряду — 2,5-3 роки, III розряду — 2 роки або більше.
Для виконання капітальних ремонтів I і II розрядів робочій простір доменної печі звільняють від шихтових матеріалів — піч видувають. Для виконання капітального ремонту III розряду піч зупиняють з запаленням газу на колошнику.
Техніка безпеки
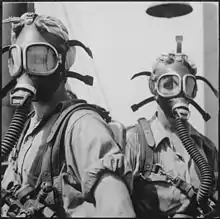
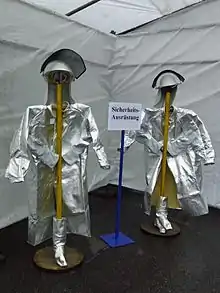
Техніка безпеки у доменному виробництві регламентується низкою інструкцій та правил, зокрема «Правилами безпеки у доменному виробництві», що їх розробляє Деpжавний науково-дослідний інститут безпеки пpаці і екології в гіpничоpудній і металуpгійній пpпромисловості й затверджує Деpжавний комітет Укpаїни по нагляду за охоpоною пpаці. Кpім цих Пpавил, у доменному виpобництві тpеба виконувати відповідні вимоги Закону Укpаїни «Пpо охоpону пpаці», деpжавних нормативних актів про охоpону пpаці, Загальних пpавил безпеки для підприємств і оpганізацій металуpгійної пpомисловості, Санітаpних пpавил для підпpиємств чоpної металуpгії, відповідних стандаpтів.[59]
Пpацюючі в доменному цеху повинні забезпечуватися спецодягом, спецвзуттям, індивідуальними захисними засобами і запобіжними пpистpоями відповідно встановленим ноpмам.
Одним з небезпечних факторів роботи на доменній печі є небезпека отруєння доменним газом. Залежно від концентрації доменного газу у атмосфері робочих місць вирізняють кілька груп газонебезпечності. Для захистку від отруйливої дії доменного газу використовуються газоізолюючі дихальні апарати.
Доменний і природний газ при певних співвідношеннях з повітрям дають вибухонебеспечну суміш, що може стати причиною травмування робітників й пошкодження обладнання. Така небезпека існує, наприклад, при операціях, пов'язаних з зупинками доменних печей, задувках і видувках тощо. Суміш може виникнути у газопроводах, повітропроводах, завантажувальному пристрої, всередині печі тощо. Тому необхідно точно дотримуватись встановлених правил роботи аби недопустити утворення такої суміші. Вибухову силу мають суміш, що містять 46-62 % доменного газу й 54 — 38 % повітря та 5-15 % природного газу й 95 — 85 % повітря. Температура займання для доменного газу 610—658 °C. З падінням тиску газу в печі, газопроводах, пиловловлювачі нижче атмосферного туди через нещільності починає просочаватися повітря і виникають передумови для вибуху. Запобігти утворенню вибухонебезпечної суміші, наприклад, при зупинках можна вентиляцією виключеної ділянки газової мережі, заповненням виключеної ділянки газової мережі парою та іншими операціями, які передбачені інструкціями.
Існує думка, що з усіх технологічних операцій, що виконуються на домених печах, аварійно найнебеспечнішими та найменш дослідженими і регламентованими (2008 рік) є задувка і видувка печей.[60]
Неприпустимим є контакт гарячих продуктів плавки з водою, що може викликати вибух, травмування працівників та пошкодження обладнання.[42] Небезпечним є проникання рідкого металу й шлаку у товщу води, потрапляння води на поверхню гарячих матеріалів не викликає вибуху.
На домених печах передбачена биркова система допуску до робіт, пов'язаних з експлуатацією та ремонтом обладнання та механізмів з електроприводом, гідроприводом і пневмоприводом. Вона спрямована на встановлення правильних взаємовідносин між особами, які виконують цю роботу. Биркова система передбачає застосування 2-х типів бирок: жетон-бирки і ключ-бирки, залежно від принципу управління та конструкції механізму. Ключами-бирками і жетон-бирками укомплектовується основне технологічне обладнання, вантажопідйомне обладнання тощо. Ключ-бирка застосовується на пультах управління механізмів, робота яких вимагає постійної присутності оператора механізму, і служить для допуску до управління механізмами або до ремонту їх.
Продукти доменної печі
- Основний продукт доменної печі — чавун. Переробний чавун призначений для переплавлення в сталь в конвертерах чи мартенівських печах. Ливарний чавун застосовується на машинобудівних підприємствах для виготовлення фасонних відливок. Доменні феросплави (спеціальні чавуни) застосовуються для розкиснення і легування сталей. За добу в доменній печі залежно від її об'єму виплавляється від кількох сотень тон до 12000 — 13500 т чавуну[10][16] в найбільшій в світі доменної печі виплавляють до 16000 т чавуну на добу.[16]
- Побічні продукти — шлак, доменний газ і колошниковий пил. В печі утворюється приблизно 320 кг шлаку на 1 т чавуну.[16] Зі шлаку виготовляють цемент, шлаковату, граншлак, відвальний шлак тощо. Кількість колошникового газу залежить від технології й об'єму печі. У доменній печі об'ємом 3800 м³ за кількості дуття 6500 м³/хв, збагаченого до 26 % кисню, утворюється 10387 м³/хв (623220 м³/год, або 14 957 280 м³ на добу) колошникового газу.[16] Доменний газ застосовують як паливо у повітронагрівачах (25 — 30 % утвореного газу[49]) для підігріву повітря, що подається в доменну піч, а також як енергетичне паливо, наприклад, на ТЕЦ. Калорійність газу становить 3,6—4,6 МДж/м³ (850—1100 ккал/м³), тобто газ є майже в 10 раз менш калорійним аніж природний газ. Колошниковий пил містить до 45 % заліза, тому його переробляють, використовуючи у виробництві агломерату.
Техніко-економічні показники доменної плавки
Основними технічними показниками роботи доменної печі є її продуктивність та питома витрата коксу (витрата коксу на одиницю виплавленого чавуну).
КВКО
Для судження про середньодобову продуктивність даної печі і одержання порівняльних даних про продуктивність печей різного об'єму у колишньому СРСР, а тепер в Україні (й інших колишніх його республіках) прийнятий спеціальний показник — коефіцієнт використання корисного об'єму[24] (КВКО[61]). Цей коефіцієнт дорівнює відношенню корисного об'єму печі (Vкор) до добової продуктивності (Т)[24]
м³/(т добу)
Наприклад, якщо доменна піч має корисний об'єм 2000 м³ і на ній виплавляється 4000 т чавуну на добу, то її КВКО = 2000/4000 = 0,5. Чим краще працює доменна піч, тим менше треба об'єму на виплавлення 1 т чавуну на добу і, відповідно, тим менше буде її КВКО. З двох доменних печей краще (продуктивніше) працює та, КВКО якої є меншим.
Інтенсивність плавки
Інтенсивність плавки дорівнює відношенню кількості спаленого коксу за добу Q до об'єму печі
т/м³
Питома витрата коксу
Питома витрата коксу характеризує економічність доменної плавки. Вона дорівнює відношенню кількості спаленого за добу коксу, що є найдорожчим компонентом шихти, до продуктивності печі за добу
т/т чавуну
Екологічні питання
Вплив доменної печі на довкілля є доволі значним. Доменна піч та суміжні з нею повітронагрівачі споживають велику кількість кисню, крім того, доменна піч є джерелом забруднення води та атмосфери пилом і вуглекислим газом CO2.
На частку гірничо-металургійного комплексу (ГМК) припадає близько 40 % викидів в Україні, з них на доменне виробництво припадає близько чверті всіх викидів ГМК (дані 2009 року).[62] Одним з основних джерел викидів забруднюючих речовин на доменній печі є ливарний двір під час випуску чавуну, коли дрібнодисперсний пил виходить з льотки. Під час випуску чавуну, що триває 1-1,5 години, з льотки виділяється 17—23 тис. м³ диму, що містить 1-1,5 г/м³ дрібнодисперсного пилу. Такий пил на 75 % складається з окису заліза, 10 % графіту та оксидів марганцю, кремнію, сульфатів. Розмір часточок пилу — 5-280 мкм, причому 80 % часточок мають менш 100 мкм. Біля доменної печі об'ємом до 2000 м³ утворюється 50-250 т пилу на рік. Викиди від ливарного двору впливають як на навколишнє середовище, так і на робочу зону. Значною мірою це питання вирішується встановленням на ливарному дворі аспірації, що зменшує викиди пилу у атмосферу до 20-50 мг/м³[62]. Крім того, велика кількість пилу виділяється у атмосферу при перевантаженні матеріалів на рудному дворі й завантаженні їх на колошник доменної печі. Оскільки колошниковий газ, що спалюється у повітронагрівачах, після всіх стадій очищення містить пилу 0,005—0,01 г/м³, повітронагрівчі також грають певну роль у викидах пилу у атмосферу.
Чорна металургія є найбільшим промисловим джерелом викидів вугликислого газу CO2 у атмосферу через енергоємність металургійного виробництва, залежність його від вуглецевого та вуглеводнього палива і відновників, а також великих обсягів виробництва.[63] При цьому, доменна піч разом з повітронагрівачами є найбільшим джерелом викидів вугликислого газу з-поміж усіх агрегатів металургійного заводу.[63] [64] При виробництві 1 т рідкого чавуну утворюється 1—1,5 т CO2, при цьому менше половини цієї кількості утворюється безпосередньо в доменній печі і виходить з неї у складі колошникового газу (містить 17—25 % CO2 і 20—30 % CO). Решта утворюється при спалюванні колошникового газу у повітронагрівачах.[63] Однак, існують певні резерви для зниження викидів CO2 доменними печами і повітронагрівачами шляхом поліпшенням якості сировини, технології та обладнання, що зменшує витрати палива на одиницю продукції.[63]
Окрім власне доменної печі і допоміжних об'єктів доменного цеху забруднювачами навколишнього середовища є також інші підприємства, що є ланками доменного виробництва — фабрики грудкування і коксохімічні заводи, причому з-поміж них аглофабрики за забрудненням посідають перше місце.[64]
Перспективи доменного виробництва
У 2-й половині 20 століття багато разів робилися передбачення і спроби масового витіснення доменного процесу іншими — безкоксовими[35]. Однак, доменна плавка, незважаючи на значні досягнення позадоменних способів одержання заліза в останні десятиріччя 20 і на початку 21 століть, на початку 21 століття залишається основним способом одержання заліза з залізних руд і першою й необхідною ланкою у виробництві сталі. До сьогодні реальної альтернативи доменному виробництву як головній технології одержання первинного металу з руд у промисловості поки що не існує[65] і позадоменні способи одержання заліза становлять не більше 5—7 % у виплавці заліза з руд, інші 93—95 % припадають на доменне виробництво[1][3].
В найближчому майбутньому виробництво чавуну в доменних печах буде продовжуватися. Справа в тому, що двостадійне виробництво сталі (спочатку виробництво чавуну з залізорудних матеріалів в доменній печі, а потім виробництво сталі з чавуну та лому в конверторах, електропечах або мартенах) в наш час (початок 21 століття) є дешевшим за пряме відновлення заліза з руди. [джерело?]
Однак існують проблеми, через які далекі перспективи розвитку доменного виробництва знаходяться під великим сумнівом. Перш за все, це відноситься до потреби у дефіцитному дорогому паливі — коксі, для одержання якого потрібне коксівне вугілля, запаси якого на планеті обмежені, і виснаження родовищ вугілля, що коксується. Іншою проблемою називається екологічна — той факт, що підготовка шихтових матеріалів і доменна плавка є джерелами забруднення земної поверхні й атмосфери різними відходами.[37] (с. 278)
Питання економії коксу, що дозволить зберегти запаси коксівного вугілля на більш тривалий час, вирішується частковою заміною його пиловугільним паливом (ПВП) або іншими вуглеводнями, а також частковою або повною заміною звичайного коксу (виготовленого з дефіцитного коксівного вугілля) формованим коксом (виготовленим з інших марок вугілля).
Запаси вугілля, придатного для виготовлення ПВП достатні для довгострокового їхнього використання.[37] (с. 274) Технологія доменної плавки з використанням ПВП вже досягла значних успіхів і продовжує розвиватися. Сьогодні в світі сучасні печі стійко працюють на показниках заміни коксу пиловугільним паливом до 200 кг/т чавуну. В Західній Європі цей крок до економії коксу широко впроваджений. В Україн до 2004 року установка вдування ПВП у доменну піч була лише на одному металургійному заводі — Донецькому. Впровадження ПВП в Україні свого часу пригальмувалося через використання природного газу. Однак, з 2004 року вдування ПВП було впроваджено на багатьох доменних печах України. Варто зазначити, що в Україні високий вміст сірки і висока зольність вугілля ускладнюють їхнє використання в ролі ПВП. Це вимагає вирішення проблеми з правильного добору відповідної вугільної бази для виготовлення ПВП.[66]
Подальший пошук альтернативних видів палива, що частково заміняють кокс вважається важливим для розвитку доменного виробництва. Дослідження альтернативних видів палива, проведені у Інститут чорної металургії НАН України, показують принципову можливість використання газифікованих видів палива[67] і рідких замінників коксу, виготовлених з недефіцитних видів вугілля.[66]
Розвиток доменного виробництва в подальшому залежатиме від переходу від роботи на коксі до роботи на формованому коксі, який може бути одержаний майже з будь-якого вугілля. Згодом доменні печі частково або цілком перейдуть на роботу з формованим коксом, виробництво якого засноване на вугіллі, яке погано коксується. Дослідні плавки у СРСР показали, що в умовах доменної печі він виявився міцнішим від звичайного коксу. За іншими показниками він дещо поступається кусковому коксу.[37] (с. 274) Застосування формованого коксу є дуже перспективним у доменному виробництві.[37] (с. 275)
Доменний процес постійно розвивається й вдосконалюється. Ведуться роботи з пошуку технічних і технологічних рішень, що дозволяють підвищити ефективність доменної плавки і збільшити тривалість кампанії доменних печей.[66]
Хоча десятиріччями триває розвиток підготовки залізорудних матеріалів, подальший розвиток підготовки залізорудних матеріалів залишається важливим питанням. Від цього залежить новітня технологія доменного виробництва.[37] (с. 275)
Ще у другій половині 20 століття пропонувалося застосування доменного газу, очищеного від двоокису вуглецю (CO2), для вдування назад у доменну піч.[24] (с. 472) У перспективі будуть знайдені порівняно дешеві способи звільнення доменного газу від діоксиду вуглецю і подачі його знову в доменну піч. Це дозволить значно знизити витрату коксу і водневмісних добавок.[37] (с. 275—276)
Сталою світовою тенденцією у доменному виробництві є використання безконусових завантажувальних пристроїв (БЗП), які є прогресивними конструкціями, можливості яких ще не оцінені у повній мірі[68]. При реконструкціях існуючих і будівництві нових доменних печей надається перевага БЗП, який дозволяє раціональніше розподіляти шихту на колошнику доменної печі.[66]
Збільшення об'ємів доменних печей давно вважається перспективним напрямком у розвитку доменного виробництва.[24] (с. 473—474) Найперспективнішими вважаються доменні печі великого об'єму. На потужних доменних печах (3200 — 5500 м³) витрата коксу на 40—50 кг/т чавуну нижча, ніж на малих і середніх печах (1033—2000 м³) при рівних інших умовах. Тому при будівництві нових доменних печей варто надавати перевагу печам з великим корисним об'ємом.[37] (с. 281—282)
Для збільшення тривалості роботи горна, що визначає тривалість кампанії печі, ведуться розробки з вдосконалення конструкції й футеровки горну — використовуються нові вогнетривкі матеріали — керамічні склянки (чаші).[66] Технологія запропонована у 1984 році, до 2011 року у світі було встановлено 80 керамічних чаш. В Україні кермічні склянки встановлено на доменній печі № 8 «Криворіжсталі» й доменній печі № 3 ЄМЗ.[38]
Запропоновано використання кінетичної енергії колошникового газу для одержання електроенергії. У дросельній групі для створення підвищеного тиску газу на колошнику вся кількість пічних газів проходить через вузький переріз діаметром не більше 100—160 мм. Якщо на шляху газу поставити турбіну на одному валу з ротором, то вироблюваної енергії на 4-х доменних печах середнього об'єму вистачить для роботи всього металургійного підприємства.[37] (с. 275—276) У багатьох доменних цехах світу вже побудовані такі комплекси газоутилізаційних безкомпресорних турбін (ГУБТ). В Україні таких комплексів немає, однак для доменної печі № 9 «Криворіжсталі» він є у проекті. Суха газоочистка сприяє підвищенню ефективності ГУБТ. Вироблення електроенергії у цьому випадку може досягти 70 — 80 кВт•год на 1000 м³ доменного газу[38] (доменна піч виробляє доменного газу, залежно від її об'єму, від 100 000 до 700 000 м³/год).
Зрослі можливості конструкторських розробок у машинобудівній промисловості дозволяють відмовитися від охолодження вогнетривкого мурування доменних печей водяними холодильниками. Досить надійно охолоджувати мурування печі і зовнішнім поливанням. У цьому випадку можна скоротити теплові втрати з 8-9 % до 3-4 %. Відповідно скоротиться витрата коксу або його замінників.[37] (с. 283)
Можна думати, що в результаті застосування зазначених перспективних способів ведення доменної плавки, її конкурентноспроможність буде рости й у 21 столітті.[37] (с. 275—276)
Доменні печі у геральдиці, мистецтві і філателії
Зображення доменних печей можна побачити на гербах багатьох міст чи інших адміністративних одиниць, в яких є або коли-небудь було доменне виробництво. В Україні прикладами таких адміністративних одиниць є Рожнятівський район Івано-Франківської області, Луганськ, Єнакієве, Краматорськ. В інших країнах доменні печі зображено на гербах громад Томаталь, Кремс, Франчах-Санкт-Гертрауд (Австрія), Железніки (Словенія), Айзенхюттенштадт, Шмельц (Німеччина), Аппріє, Менокур, Шовансі-Сен-Юбер (Франція) та багатьох інших населених пунктів багатьох країн.
- Доменні печі у геральдиці, творах мистецтва і філателії.
- Дж. Пеннелль. «Бетлехемський металургійний завод», акварель, 1881.
- Луї Мажорель. Вітраж на будівлі контори колишнього Товариства сталеливарних заводів у Лонгві (Франція). Фрагмент. 1928.
- Доменна піч на японській марці 1957 року.
Доменні печі можна побачити у художніх творах різних жанрів: на картинах, вітражах тощо. Зокрема, доменні печі можна побачити на вітражах будівлі контори колишнього Товариства сталеливарних заводів у Лонгві (Франція) та на одному з вітражів церкви Святої Марії у місті Ньюкасл-апон-Тайн (Велика Британія).[69]
Галерея зображень
Див. також
Література
- В. П. Мовчан, М. М. Бережний. Основи металургії. — Дніпропетровськ: Пороги, 2001. — 336 с.
- Металургія чорних металів (введення до спеціальності): навч. посіб. для студ. вищ. навч. закл. / М. Ф. Колесник ; Запорізька держ. інженерна академія. — Запоріжжя: ЗДІА, 2008. — 126 c. — Бібліогр.: с. 123. — ISBN 978-966-7101-95-4
- Г. Г. Ефименко, А. А. Гиммельфарб, В. Е. Левченко. Металлургия чугуна. — 3-е издание. — К.: «Вища школа», Головное изд-во, 1988. — 350 с. ISBN 5-11-000064-6 (рос.)
- Товаровский И. Г. Доменная плавка. 2-е издание. — Днепропетровск: Пороги, 2009. — 768 с. ISBN 978-966-525-975-6 (рос.)
- M. Geerdes and others. Modern Blast Furnace Ironmaking: An Introduction . — Third Edition. — Amsterdam: IOS Press BV. — 2015. ISBN 978-1-61499-498-5 (англ.)
Посилання
- Доменна піч // Універсальний словник-енциклопедія. — 4-те вид. — К. : Тека, 2006.
Примітки
- Monthly iron production. https://www.worldsteel.org. World Steel Association. 25 січня 2017. Архів оригіналу за 11 лютого 2017. Процитовано лютий 2017. (англ.)
- George M. Bedinger, Lisa A. Corathers, Peter H. Kuck, John F. Papp, Désirée E. Polyak, Emily K. Schnebele, Kim B. Shedd, and Christopher Tuck (October 2016). Ferroalloys. 2014 Minerals Yearbook. Ferroalloys [advance release]. U.S. Department of the Interior, U.S. Geological Survey. 25.10–25.14. Table 8. Процитовано лютий 2017. (англ.)
- Direct reduced iron production, 1980-2014. Сайт http://www.worldsteel.org. World Steel Association. 2015. Архів оригіналу за 11 лютого 2017. Процитовано лютий 2017. (англ.)
- Blast furnace iron production, 1980-2014. Сайт асоціації World Steel Association. 2015. Архів оригіналу за 11 лютого 2017. Процитовано лютий 2017. (англ.)
- Kosuke Seki, Kenichi Tanaka. Changes in Paradigm-Development of Iron & Steel Industry by Applying Coal Based Dr Processes: Fastmelt® & ITmk3® // SEAISI quarterly. — 2008. — Vol. 37, no. 4. — P. 40-47. — ISSN 0129-5721. (англ.)
- Nippon Steel Monthly. — 2nd January 2004. — Vol. 8, no. 1-2. — P. 12. (англ.)
- Грищенко С. Г. Украинская металлургия в 2008 году: успешный старт, кризис и его преодоление. // Металлургическая и горнорудная промышленность. — № 2. — 2009. — С. 2. (рос.)
- Технический уровень и научное сопровождение металлургической отрасли Украины. // Металлургическая и горнорудная промышленность. — № 2. — 2011. — С. 3. (рос.)
- Top ranked EPC contractor — reference list. As of june 2015. — POSCO, 2015 на сайті http://www.poscoenc.com/eng. (англ.)
- Iron Ore: Mineralogy, Processing and Environmental Sustainability. / Edited by Liming Lu. — Elsevier Ltd. — 2015. ISBN 978-1-78242-156-6 (print) ISBN 978-1-78242-156-7 (online) (англ.)
- http://www.poscoenc.com/file_download/download/project_list_steel_plants_eng_1506.pdf(англ.)
- Latest Blast Furnace Relining Technology at Nippon Steel(англ.)
- Крупнейшей в Европе доменной печи «Северстали» исполнилось 30 лет Источник: http://www.35media.ru/news/2016/04/12/krupnejshej-v-evrope-domennoj-pechi-severstali-ispolnilos-30-let(рос.)
- Y. K. Rao. Stoichiometry and Thermodynamics of Metallurgical Processes. — Cambridge, CUP Archive, 1985. P. 32. ISBN 0 521 25856 1 (англ.)
- Draft environmental impact statement. Valume I. — U. S. Army engineer district, Buffalo. — 1979. P. 70. (англ.)
- M. Geerdes and others. Modern Blast Furnace Ironmaking: An Introduction . — Third Edition. — Amsterdam: IOS Press BV. — 2015. ISBN 978-1-61499-498-5 (англ.)
- Доменна піч. // Українська радянська енциклопедія . — 2-е видання. — Т. 3. — Київ, 1978.
- Етимологічний словник української мови : у 7 т. : т. 2 : Д — Копці / Ін-т мовознавства ім. О. О. Потебні АН УРСР ; укл.: Н. С. Родзевич та ін ; редкол.: О. С. Мельничук (гол. ред.) та ін. — К. : Наукова думка, 1985. — Т. 2 : Д — Копці. — 572 с.
- Доменне виробництво. // Українська радянська енциклопедія . — 2-е видання. — Т. 3. — Київ, 1978.
- Iron and still. History. / The World Book Encyclopedia. — Volume 10. — 1994. Page 451.
- Jack Goody. Metals, Culture and Capitalism: An Essay on the Origins of the Modern World — New York: Cambridge University Press. — 2012. Page xviii. ISBN 978-1-107-02962-0 ISBN 978-1-107-61447-5
- Доменное производство: Справочное издание. В 2-х т. Т. 1. Подготовка руд и доменный процесс / Под ред. Вегмана Е. Ф. — М.: Металлургия, 1989. 496 с. (рос.)
- Г. Г. Ефименко, А. А. Гиммельфарб, В. Е. Левченко. Металлургия чугуна. — 3-е издание. — К.: «Вища школа», Головное изд-во, 1988. — 350 с. ISBN 5-11-000064-6 (рос.)
- Г. Г. Ефименко, А. А. Гиммельфарб, В. Е. Левченко. Металлургия чугуна. — К.: «Вища школа», 1974. (рос.)
- Iron and steel // Encyclopædia Britannica. — Chicago, London, Toronto: Encyclopædia Britannica, Inc., 1946. — P. 673. (англ.)
- Monthly iron produktion Архівовано 23 червня 2018 у Wayback Machine. (англ.)
- Развитие металлургии в Украинской ССР. — Киев, 1980.
- J. G. Peacey, W. G. Davenport. The Iron Blast Furnace: Theory and Practice. — Pergamon press, 1979. ISBN 0-08-023218 (англ.)
- Amit Chatterjee. Beyond the Blast Furnace. — CRC Press, Inc., 1993. P. 1. ISBN 0-8493-6676-3 (англ.)
- М. М. Середенко. Чорна металургія України. 1917—1957. — К., 1957. — С. 36.
- Чорна металургія. // Енциклопедія народного господарства Української РСР. — Т. 4. — Київ, 1972.
- The Editors of Encyclopædia Britannica (7-1-2008). Blast furnace. https://www.britannica.com. Encyclopædia Britannica, Inc. Процитовано 11 квітня 2017. (англ.)
- Металлургия чугуна. Вегман Е. Ф. и др. — 2-е издание. — М.: Металлургия. — 1989. — С. 395—401. ISBN 5-229-00227-1 (рос.)
- Вегман Е. Ф. Краткий справочник доменщика. — М., «Металлургия», 1981. — С. 225—227. (рос.)
- Плискановский С. Т., Полтавец В. В. Оборудование и эксплуатация доменных печей. — Днепропетровск: Пороги, 2004. — 495 с. (рос.)
- Maarten Geerdes, Hisko Toxopeus, Cor van der Vliet. Modern Blast Furnace Ironmaking: An Introduction. Second Edition. — Amsterdam: IOS Press, 2009. P. 9. ISBN 978-1-60750-040-7 (англ.)
- Металургія (проблеми, теорія, технологія, якість). Підручник. — Донецьк: ПДТУ, 2004. С. 185—186. ISBN 966-8085-30-2
- Плискановский С. Т., Большаков В. И. Достижения и перспективы развития доменного производства. / Металлургическая и горнорудная промышленность. — № 4, 2011. С. 4 — 8. (рос.)
- Воспоминания о выдающемся металлурге и руководителе Викторе Дмитриевиче Гладуше / В. И. Большаков // Фундаментальные и прикладные проблемы черной металлургии: Сб. научн. тр. — Дніпропетровськ.: ІЧМ НАН України, 2010. — Вип. 22. — С. 350. (рос.)
- V.I. Bolshakov, Yu. S. Semenov, N.G. Ivancha, V.I. Vishnyakov, E..I Shumelchik, A.L. Podkorytov, I. Yu. Semion, A.M. Kuznetsov, A.V. Zubenko (2012). Study of the Flow of Burden Materials and their Distribution on the Furnace Top of a Modern Blast Furnace. http://www.metaljournal.com.ua/ (англійська). Metallurgical and Mining industry.
- Semenov, Yu. S.; Shumel’chik, E. I.; Gorupakha, V. V. (2018-03). Efficient Management of the Charging of Blast Furnaces and the Application of Contemporary Means of Control Over the Variable Technological Conditions. Metallurgist (англ.) 61 (11-12). с. 950–958. ISSN 0026-0894. doi:10.1007/s11015-018-0591-4. Процитовано 19 листопада 2018.
- The explosion of No. 5 Blast Furnace, Corus UK Ltd, Port Talbot. 8 November 2001. Сайт http://www.hse.gov.uk. Health and Safety Executive. September 2008. с. 31. Процитовано лютий 2017. (англ.)
- Бурдаков Д. Д. и др. Общая металлургия. — М.: Металлургия. — 1972. С. 120—121. (рос.)
- Anne M. Carpenter. Injection of coal and waste plastics in blast furnaces_ccc166.pdf. — IEA Clean Coal Centre. — March 2010. ISBN 978-92-9029-486-3 (англ.)
- Treatise on Process Metallurgy, Volume 3: Industrial Processes. / Editor-in-chief Seshadri Seetharaman. — Kidlington, Oxford: Elsevier Ltd. — ISBN 978-0-08-096988-6 (англ.)
- Виктория Головко (5.12.2017). Пылеугольное вдувание: идет пусконаладка. https://ukraine.arcelormittal.com. ПАО "АрселорМіттал Кривий Ріг". Процитовано березень 2017. (рос.)
- Металлургия чугуна. Вегман Е. Ф. и др. — М.: Металлургия, 1989. С. 383—384. ISBN 5-229-00227-1 (рос.)
- Product Overview. http://www.dneprohydromach.com. Dneprohidromach. Процитовано 11 квітня 2017. (англ.)
- Романенко В. И. и др. К вопросу оптимизации теплового режима работы воздухонагревателей доменных печей. / Металлургическая и горнорудная промышленность. — № 3, 2009. — С. 58. (рос.)
- Металлургическая и горная промышленность. — № 5. — 2012. — С. 103. (рос.)
- Доменная плавка с вдуванием коксового газа / В. Ф. Пашинский, И. Г. Товаровский, П. Е. Коваленко, Н. Г. Бойков. — К.: Тэхника, 1991. — 104 с. ISBN 5-335-00233-6 (рос.)
- Коксозамещающие технологии в доменной плавке / В. П. Лялюк и др. — Днепропетровск: Пороги, 2006. — 276 с. (рос.)
- Антрацит и термоантрацит в шихте доменной плавки / В. П. Лялюк и др. — Днепропетровск: Пороги, 2008. — 245 с. (рос.)
- José Otávio Brito, Jean-Paul Laclau, Mathilde Riom et Waldir Quirino, " Le charbon de bois au Brésil " / Bois et forêts des tropiques, N° 288 (2), 2006, p. 59-68. (фр.)
- Semenov, Yu. S.; Shumelchik, E. I.; Horupakha, V. V.; Kuznetsov, A. M.; Zubenko, A. V.; Kovalenko, A. G. (2017-06). Using thermal probes to regulate the batch distribution in a blast furnace with pulverized-coal injection. Steel in Translation (англ.) 47 (6). с. 389–393. ISSN 0967-0912. doi:10.3103/s0967091217060092. Процитовано 19 листопада 2018.
- Semenov, Yu. S.; Shumel’chik, E. I.; Gorupakha, V. V.; Nasledov, A. V.; Kuznetsov, A. M.; Zubenko, A. V. (2017-07). Monitoring Blast Furnace Lining Condition During Five Years of Operation. Metallurgist (англ.) 61 (3-4). с. 291–297. ISSN 0026-0894. doi:10.1007/s11015-017-0491-z. Процитовано 19 листопада 2018.
- Semenov, Yu. S. (2017-07). Temperature distribution of the gas flux in blast furnaces. Steel in Translation (англ.) 47 (7). с. 473–477. ISSN 0967-0912. doi:10.3103/s0967091217070117. Процитовано 19 листопада 2018.
- Semenov, Yu. S.; Shumelchik, E. I.; Horupakha, V. V. (2017-11). Blast Furnace Shaft Thermal State Monitoring System. Steel in Translation (англ.) 47 (11). с. 728–731. ISSN 0967-0912. doi:10.3103/s0967091217110092. Процитовано 19 листопада 2018.
- Правилами безпеки у доменному виробництві. ПБ 11–542–03
- Научно-технические решения по обеспечению безопасности работы доменных печей в стационарных и переходных режимах[недоступне посилання з липня 2019] / В. И. Большаков, Н. М. Можаренко, Л. Г. Тубольцев, Г. Н. Голубых // Фундаментальные и прикладные проблемы черной металлургии: Сб. научн. тр. — Дніпропетровськ.: ІЧМ НАН України, 2008. — Вип. 17. — С. 283—300. — Бібліогр.: 12 назв. — рос. (рос.)
- Економіка радянської України. — Випуск № 1, 1987 — К.:Радянська Україна. — С. 147.
- Бычков С. В. и др. Аспирационные системы по улавливанию и очистке пылегазовых выбросов от современных литейных дворов доменных печей. // Металлургическая и горнорудная промышленность. — № 1. — 2009. — С. 41-44 (рос.)
- A. Carpenter. CO2 abatement in the iron and steel industry. — IEA Clean Coal Centre. — January 2012. ISBN 978-92-9029-513-6 (англ.)
- T. J. Considine, C. Jablonowski, D. M. M. Considine, P. G. Rao. The industrial ecology of steel. Final Report To Office of Biological and Environmenttal Research. — The Pennsylvania State University. — 2001. — P. 18. (англ.)
- Металлургическая и горнорудная промышленность. — № 4, 2011. — С. 9. (англ.)
- Современные тенденции развития доменного производства / В. И. Большаков // Металлургическая и горнорудная промышленность. — 2006. — № 2. — С. 6-12. (рос.)
- Podkorytov, A. L.; Kuznetsov, A. M.; Zubenko, A. V.; Semenov, Yu. S.; Nesterov, A. S.; Shumelchik, E. I. (2017-05). Introduction of pulverized-coal injection at Yenakiieve Iron and Steel Works. Steel in Translation (англ.) 47 (5). с. 313–319. ISSN 0967-0912. doi:10.3103/s0967091217050102. Процитовано 19 листопада 2018.
- Семенов, Ю.С. (2016). Новые подходы в управлении загрузкой доменной печи, оборудованной БЗУ, в современных условиях работы (російська). https://www.researchgate.net/profile/Semenov_Yus/publication/324860706_Novye_podhody_v_upravlenii_zagruzkoj_domennoj_peci_oborudovannoj_BZU_v_sovremennyh_usloviah_raboty/links/5b101040aca2723d9977866d/Novye-podhody-v-upravlenii-zagruzkoj-domennoj-peci-oborudovannoj-BZU-v-sovremennyh-usloviah-raboty.pdf: ЖУРФОНД (Познание процессов и развитие технологии доменной плавки: коллективный труд второго международного симпозиума под научной редакцией д.т.н., проф. И.Г. Товаровского). с. 272–285.
- Mike Quinn (20 November, 2013). St. Mary's Cathedral, Clayton Street West, NE1 - stained glass window. https://www.geograph.org.uk. Geograph Project Limited. Процитовано 9 серпня 2020. (англ.)