Металургія
Металу́ргія (через фр. métallurgie від дав.-гр. μεταλλουργός — «металороб, рудокоп») — наука, техніка і галузь промисловості, які пов'язані з одержанням металів з руд. У прикладному плані — сукупність зв'язаних між собою галузей і стадій виробничого процесу від видобутку сировини до випуску готової продукції — чорних і кольорових металів та їх сплавів (стопів).
Металургія | |
![]() | |
Частково збігається з | Q19724861? |
---|---|
![]() |
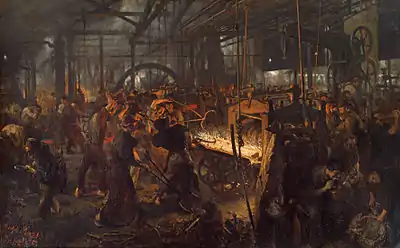
До чорних металів відносять метали й сплави на основі заліза, марганцю, хрому. Всі інші — кольорові. За фізичними властивостями та призначенням кольорові метали умовно ділять на важкі (мідь, свинець, цинк, олово, нікель), легкі (алюміній, титан, магній), дорогоцінні (золото, срібло, платина), лужні (калій, натрій, літій), лужно-земельні (кальцій, барій, стронцій).
Властивості металів та методи їхньої модифікації вивчає металознавство.
Історія
Перші свідчення про виробництво людьми металу на території Європи датуються бльзько 3 тис. до н. е. Вони були знайдені при розкопках у Майданпеку, Ярмоваці та Плочнику (Сербія). Знайдена в Бєловоде, мідна сокира культури Вінча свідчить про добування міді. Інші свідчення про існування металургії датуються були знайдені археологічними розкопками в різних країнах Європи: у Пальмелі (Португалія), Кортес-де-Наварра (Іспанія), Стоунхендж (Англія). Однак, як часто буває при вивченні доісторичних часів, місце й час винаходу не може бути встановлений точно, і археологи час від часу отримують нові артефакти у різних куточках світу.
Срібло, мідь, олово й метеоритне залізо можна знайти у вигляді самородків, завдяки чому вже ранні культури могли в обмеженому обсязі використовувати обробку металів. Єгипетська зброя з метеоритного заліза, виготовлена приблизно за 3 тис. років до Христа, високо цінувалася як «кинджали з Небес». Однак уміння отримувати мідь та олово з породи й сполучати ці два метали у сплав під назвою бронза дало початок справжній металургії приблизно 2 тис. років до н. е., й розпочало епоху в історії людства, яка отримала назву Бронзова доба.
Видобування заліза з руди та його обробка набагато складніші процеси. До виробництва залізних інструментів та зброї, додумались хетти, близько 1200 років до н. е. і започаткували залізну добу. Надалі свідчення розвитку чорної металургії археологи знаходять у різних культурах та цивілізаціях. Серед них стародавні й середньовічні держави Середнього й Близького Сходу, стародавнього Ірану, Стародавнього Єгипту, Нубії, Анатолії, культури Нок, Карфагену, а також Стародавня Греція й Стародавній Рим, Стародавній Китай, стародавня Японія. Стародавній Китай збагатив металургію значними винаходами, такими як вдосконалення доменної печі, чавуну, гідравлічних молотів, ковальських міхів.
У 16 ст. Георг Агрікола видав книгу De Re Metallica, в якій описав складний процес видобування руди, виплавки та обробки металу, що відповідала розвитку металургії на той час. Агріколу називають «батьком» металургії[1].
Особливо швидкими темпами металургія стала розвиватися з початком промислової революції. Зріс об'єм виробництва металів, вдосконалювалися способи їх отримання, зростала якість. У сучасну епоху зростає роль високотехнологічних матеріалів, таких як сплави, леговані й композитні матеріали з металевими матрицями.
Металургія як науково-технічна галузь
Металургія — це наука про одержання металів з руд або речовин, які містять метали, і про надання металевим сплавам необхідних властивостей.
Металургія ґрунтується на досягненнях фізичної хімії, фізики, металургійної теплотехніки, електротехніки, електроніки, кібернетики, економіки, на теорії металургійних процесів, автоматизації виробництва й керування ним, а також, на космічних технологіях.
Металургія вивчає проблеми підготовки руд, яка полягає у їхньому дробленні і подрібненні, розділенні (грохочення, класифікація), збагачуванні, випалі або сушінні, окускуванні, агломерації та брикетуванні. Досліджує гідрометалургійні, пірометалургійні, у тому числі металотермічні, електротермічні а також електрохімічні (електроліз) процеси одержання металів (сплавів) з наступним їх рафінуванням.
Крім того, металургія вивчає проблеми виготовлення металевих порошків і виробів з них (порошкова металургія), термічної обробки, обробки металів тиском, лиття, зварювання, паяння, нанесення на поверхню металів захисних покриттів. Важливою галуззю металургії є металознавство.
Металургія як галузь промисловості
Металургія як галузь важкої промисловості поділяється на чорну і кольорову.
Чорна металургія
Чорна металургія — галузь важкої промисловості, підприємства якої виробляють чавун, сталь, прокат, сталеві й чавунні труби, феросплави, металеві вироби промислового призначення. До чорної металургії належать також підгалузі по видобуванню залізної і марганцевої руд та по виробництву їх концентратів, агломерату, котунів, флюсових вапняків, вогнетривкої сировини і вогнетривів, коксу та іншої продукції, що її використовують в основному як сировину для виробництва чорних металів
Кольорова металургія
Кольорова металургія — галузь важкої промисловості, що займається видобуванням і збагаченням руди, виробництвом і обробкою кольорових металів, рідкісних і дорогоцінних металів та їхніх сплавів, видобуванням природних алмазів та іншої мінеральної сировини. До кольорової металургії належать також заготівля і переробка вторинних кольорових металів. Виробничий комплекс галузі складається з гірничодобувних підприємств, збагачувальних фабрик, металургійних й металообробних заводів. Підприємства кольорової металургії, як матеріаломісткої й енергоємної галузі, будуються в місцях добування сировини й виробництва дешевої електроенергії.
Металургія як галузь технологій
Метали трапляються в природі як у вільному стані (самородні метали), так і, переважно, у вигляді хімічних сполук. У вигляді самородних металів перебувають найменш активні метали. Типовими їх представниками є золото і платина. Срібло, мідь, ртуть, олово можуть існувати в природі як у самородному стані, так і у вигляді сполук, решта металів — лише у вигляді сполук з іншими елементами.
Мінерали і гірські породи, що містять метали або їхні сполуки і придатні для промислового добування металів, називаються рудами. Найважливішими рудами металів є їх оксиди і солі (сульфіди, карбонати тощо). Якщо руди містять сполуки двох або декількох металів, то вони називаються поліметалічними (наприклад, мідно-цинкові, свинцево-срібні та ін.).
Добування металів з руд — завдання металургії. Сучасна металургія як сукупність основних технологічних операцій виробництва металів і сплавів та їх первинної переробки включає в себе:
- підготовку руд до отримання металів (в тому числі збагачення);
- процеси отримання і рафінування металів: пірометалургійні, гідрометалургійні, електролітичні;
- процеси отримання виробів з металевих порошків шляхом спікання;
- кристалофізичні методи рафінування металів і сплавів;
- процеси розливання металів і сплавів (з отриманням злитків або виливків)
- обробку металів тиском;
- термічну, термомеханічну, хіміко-термічну та ін. види обробки металів для додання їм відповідних властивостей;
- процеси нанесення захисних покриттів.
Гірничо-збагачувальне виробництво
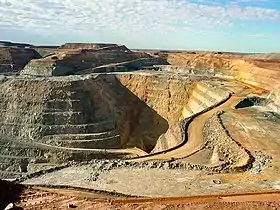
Гірничо-збагачувальне виробництво охоплює усі види видобування та збагачування корисних копалин (руд) та передбачає їх видобування (шахтним або відкритим способом) та збагачення.
Шахтне виробництво
Шахтне виробництво реалізується на базі підприємств (шахт, рудників) по видобуванню і переробці корисних копалин. Воно включає гірничопрохідницькі роботи (створення підземних гірничих виробок і камер різного призначення) і зведення комплексу поверхневих споруд: підйомних установок, копрів, компресорних станцій і вентиляційних надшахтних пристроїв, адміністративно-побутових споруд, збагачувальних фабрик, під'їзних колій тощо. Шахтному виробництву передують геологорозвідувальні роботи, розробка проектної і технічної документації. Гірничопрохідницькі роботи виконують, зазвичай, у складних гірничо-геологічних умовах на різних глибинах (іноді понад 1000 м) буропідривним, підривним або комбайновим способом. Одночасно вдаються до кріплення гірничих виробок.
Відкрита розробка родовищ
Відкриті гірничі роботи — видобування корисних копалин безпосередньо з земної поверхні. Провадиться в кар'єрах. Відкрита розробка складається з підготовки поверхні землі, осушення (в разі потреби) і розкриття родовища, розкривних і видобувних робіт. Підготовка поверхні полягає в основному у видаленні родючого шару (з подальшим нанесенням його на поверхню відвалів з метою відновлення родючості ґрунту) і відведенні поверхневих вод. Для осушення родовища (поверхневого і підземного, попереднього і паралельного — під час ведення робіт) використовують водознижувальні і вбирні свердловини, закриті дрени, спеціальні фільтри тощо. Розкриття родовища передбачає спорудження капітальних розрізних і транспортних траншей для забезпечення доступу до масиву корисних копалин і транспортного зв'язку з земною поверхнею. Розкривні роботи включають відокремлення від масиву і транспортування у відвали покривних порід, видобувні роботи — відокремлення корисних копалин від масиву з подальшим переміщенням їх на склади або місця переробки. Технічними засобами Відкритою розробки родовищ є екскаватори безперервної дії, транспортно-відвальні мости, консольні відвалоутворювачі, кар'єрні самоскиди, бульдозери тощо. Переваги відкритої перед підземною розробкою родовищ корисних копалин: більша безпека праці і кращі виробничі умови; менші втрати корисних копалин; можливість застосування потужнішої техніки; вища (в 3-6 разів) продуктивність праці і нижча (в 2-3 рази) собівартість продукції; менші (в 2-3 рази) питомі капіталовкладення і строки будівництва кар'єрів. Основним недоліком відкритої розробки родовищ є значний вплив на довкілля, який усувають частковою або повною рекультивацією земель.
Збагачування корисних копалин
Збагачування корисних копалин — сукупність процесів первинної обробки мінеральної сировини з метою відокремлення корисних копалин від порожньої породи, а іноді й від шкідливих домішок. Зумовлене зростанням потреби у вихідній сировині зі збільшеним вмістом корисних компонентів, що їх надалі технічними способами можливо і економічно доцільно переробляти й використовувати. Полягає у механічному розділянні сировини, яке ґрунтується на відмінності фізичних і фізико-хімічних властивостей корисних копалин. При збагачуванні, що його провадять у спеціальних цехах або на збагачувальних фабриках, одержують продукти (концентрати), які містять значну кількість корисних компонентів, і відходи, де зосереджена переважно порожня порода. За способом розділяння сировини розрізняють гравітаційне збагачування, магнітне збагачування, електростатичне збагачування і збагачування флотаційне. Є також збагачування залежно від форми частинок корисних копалин, їхнього тертя тощо. В разі потреби застосовують комбіновані способи (напр., флотогравітаційний), методи гідрометалургії, іноді — ручний. При збагаченні ступінь вилучення із сировини концентрату становить 92…95 %, вміст корисних компонентів у ньому 15…95 %. Перший систематизований опис багатьох процесів збагачування корисних копалин дав Г. Агрікола.
Добувна металургія
Сучасна металургія добуває понад 75 металів і численні сплави на їх основі. Залежно від способів добування металів розрізняють піро-, гідро- і електрометалургію.
Пірометалургія
Пірометалургія — галузь металургії, що охоплює процеси одержання і очищення металу (сплаву) або сполук металу за температур, що забезпечують спікання, випалювання, плавлення, сублімацію, випаровування, а також тривання необхідних хімічних реакцій[2]. Вона посідає провідне місце в металургії. Вона охоплює способи добування металів з руд за допомогою хімічних реакцій відновлення, які проводять за високих температура. Як відновники застосовують вугілля, активні метали, оксид карбону(ІІ), водень, метан. Так, наприклад, вугілля і оксид карбону(ІІ) відновлюють мідь з червоної мідної руди (куприту) Сu2О:
- Cu2O + C = 2Cu + CO;
- Cu2O + CO = 2Cu + CO2.
Аналогічно відбувається добування чавуну і сталі із залізних руд.
У тих випадках, коли руда є сульфідом металу, її спочатку переводять в оксид окисним випалюванням (випалюванням з доступом повітря). Наприклад:
- 2ZnS + 2O2 = 2ZnO + 2SO2.
Далі оксид металу відновлюють вугіллям:
- ZnO + C = Zn + CO.
Відновлення вугіллям (коксом) здійснюють зазвичай тоді, коли метали, що їх добувають, зовсім не утворюють карбідів або утворюють неміцні карбіди (сполуки з карбоном); це залізо і багато кольорових металів — мідь, цинк, кадмій, германій, олово, свинець та ін.
Галузь металургії, яка використовує процеси відновлення металів з хімічних сполук активнішими металами або хімічними сполуками з великим виділенням тепла називається металотермією[2]. Ці процеси відбуваються також за високих температур. Як відновники застосовують алюміній, магній, кальцій, натрій, а також кремній. Якщо відновник — алюміній, то процес називається алюмінотермією, якщо магній — магнійтермією. Наприклад:
- Cr2O3 + 2Al = 2Cr + Al2O3;
- TiCl4 + 2Mg = Ti + 2MgCl2.
Металотермією звичайно добувають ті метали (та їх сплави), які при відновленні оксидів вугіллям утворюють карбіди. Це марганець, хром, титан, молібден, вольфрам та ін. Іноді метали відновлюють з оксидів воднем (воднeтермія). Наприклад:
- MoO3 + 3H2 = Mo + 3H2O;
- WO3 + 3H2 = W + 3H2O.
При цьому утворюються метали високої чистоти.
Гідрометалургія
Гідрометалургія — галузь металургії, що охоплює різні способи вилучення металів із руд, концентратів та відходів різних виробництв за допомогою розчинів (найчастіше водних) хімічних реагентів з подальшим виділенням металів або їхніх сполук з цих розчинів[2]. При цьому метал, що входить до складу руди, спочатку переводять у розчин за допомогою відповідних реагентів, а потім добувають його з цього розчину. Так, наприклад, під час обробки розбавленою сульфатною кислотою мідної руди, яка містить оксид купруму(ІІ) СuО, мідь переходить у розчин у вигляді сульфату:
- CuO + H2SO4 = CuSo4 + H2O.
Далі мідь добувають з розчину або електролізом, або витісненням за допомогою порошку заліза:
- CuSO4 + Fe =Cu + FeSO4.
Нині гідрометалургійним методом добувають до 25 % всієї міді. Метод є перспективним, оскільки він дає змогу добувати метали, не піднімаючи руду на поверхню. Цим же методом добувають золото, срібло, цинк, кадмій, молібден, уран та ін. Руду, що містить самородне золото, після подрібнення обробляють розчином ціаніду калію KCN. Все золото переходить у розчин. З розчину його видобувають електролізом або витісненням металічним цинком.
Електрометалургія
Електрометалургія — галузь металургії, яка охоплює процеси одержання, рафінування і оброблення металів і сплавів із руд та концентратів за допомогою електричної енергії[2]. Цим способом добувають переважно легкі метали — алюміній, натрій та інші — з їх розплавлених оксидів або хлоридів.
Електроліз використовують також для очищення деяких металів. З металу, що його очищають, виготовляють анод. При електролізі анод розчиняється, іони металу переходять у розчин, а на катоді вони осаджуються. Так добувають електролітично чисті метали: мідь, срібло, залізо, нікель, свинець та ін.
Порошкова металургія
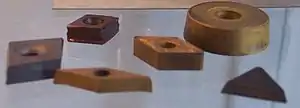
Порошкова металургія — галузь науки і техніки, яка охоплює виробництво металевих порошків, а також виробів з них або їхніх сумішей з неметалевими порошками[3]. Важливими відмінними рисами даної галузі є одержання речовин у порошкоподібному стані та проведення операції нагрівання (спікання) заготовок із порошків за температури нижчої від точки плавлення відповідного металу або, у випадку суміші різнорідних порошків, температури плавлення найменш тугоплавкого компонента основи. Отже, послідовне здійснення в єдиному циклі операцій одержання порошку і перетворення його у виріб становить суть порошкової металургії.
Кристалофізичне очищення металів
Для того, щоб забезпечити отримання матеріалу з граничним ступенем чистоти кристалізаційними методами необхідно, щоб при рафінувальному плавленні кристалізація починалася в заданому місці і відбувалася в певному напрямку, тобто слід створити чітку межу між твердою і рідкою фазами і забезпечити її повільний і рівномірний рух уздовж виливка, який очищується. Ці умови досягаються заданням градієнта температури, що забезпечує спрямоване відведення тепла і спрямоване просування фронту кристалізації. Залежно від співвідношення ступенів розчинності домішок у рідкому та твердому металі, будуть чистішими або частини злитка, що тверднуть пізніше, або початкова зона затвердіння злитка. При розгляді процесів очищення кристалів, отримуваних із розплаву, все різноманіття методів вирощування кристалів спрямованою кристалізацією можна звести до трьох типових схем: нормальної спрямованої кристалізації, витягування кристалів з розплаву і зонного плавлення.
Метод нормальної спрямованої кристалізації
У методах нормальної спрямованої кристалізації заготовка розплавляється цілком, а потім розплав кристалізується з визначеного місця. Спільним для цих методів є зростання кристала в контакті зі стінками тигля, що містить розплав. Переохолодження на фронті кристалізації здійснюють шляхом переміщення тигля з розплавом відносно нагрівача, що створює теплове поле з градієнтом температури, або шляхом переміщення нагрівача відносно тигля. Кристалізація також можлива і при охолодженні нерухомого тигля з розплавом в тепловому полі з температурним градієнтом при програмному зниженні потужності, що підводиться до печі. Залежно від розташування тигля з матеріалом розрізняють горизонтальний і вертикальний методи нормальної спрямованої кристалізації. Вертикальний метод отримав назву «метод Бріджмена»[4].
Метод Чохральського
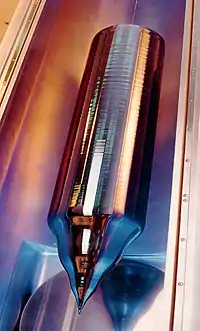
У методі витягування кристалів з розплаву (методі Чохральського) у вакуумі або середовищі інертного газу в розплав металу опускають затравку у вигляді невеликого монокристала, яку потім безперервно переміщають вгору. Затравка захоплює за собою рідкий стовпчик, який, потрапляючи в зону нижчої температури, безперервно кристалізується. Принцип методу витягування кристалів з розплаву вперше був запропонований Яном Чохральським у 1918 році[5]. Існує значна кількість різних модифікацій Методу Чохральського.
Зонне плавлення
Зонне плавлення (зонна перекристалізація) — метод рафінування металів і сплавів, який ґрунтується на перекристалізації твердих речовин під час переміщення вузької розплавленої зони вздовж довгого твердого стрижня із рафінованого матеріалу[2]
Цей метод очищення, базується на різній розчинності домішок у твердій і рідкій фазах. По мірі спрямованого просування зони розплавлення попереду зони відбувається плавлення речовини, а позаду — її кристалізація, що призводить до перерозподілу домішок. Якщо домішка краще розчиняється в рідкій фазі, то вона поступово накопичується в розплавленій зоні, рухаючись разом з нею. В результаті домішка скупчується в одній частині вихідного зразка. У порівнянні з спрямованою кристалізацією цей метод має більшу ефективність. Метод, що був запропонований В. Дж. Пфанном[6] в 1952 році використовується для очищення понад 1500 речовин і став одним з найпоширеніших кристалізаційних методів, що застосовують для глибокого очищення.
Ливарне виробництво
Ливарне виробництво — виробництво литих заготовок або виробів (виливків) з розплавлених металів (сплавів)[7] методом лиття.
Лиття — технологічний процес виготовлення виливка, суть якого в заповненні ливарної форми розплавленим матеріалом (ливарним сплавом) з подальшим затвердінням[7]. Лиття з металу — один з основних способів виробництва заготовок деталей (в машинобудуванні), тому що дозволяє одержати виливок практично будь-якої форми і маси з необхідними фізико-механічними властивостями. Головною ознакою технологічного процесу лиття є метал виливків, залежно від якого відрізняють чавуно-, стале-, мідноливарне виробництво тощо.
Набули поширення такі різновиди лиття з металу:
- в піщані форми;
- в кокіль;
- по виплавлених моделях;
- по випалюваних моделях;
- лиття під тиском;
- вакуумне лиття;
- лиття металів з використанням ливарних машин відцентрового лиття.
Оброблення металів тиском
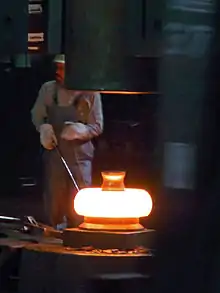
Оброблення металу тиском — сукупність технологічних процесів, внаслідок яких відбувається пластичне деформування або поділ металу на частини без утворення стружки[8].
При цьому виді обробки тиском використовують властивість металу — пластичність (здатність під дією прикладених сил змінювати форму без руйнування) в холодному або у гарячому стані. Найпоширеніший механізм пластичної деформації — ковзання, зсув однієї частини тіла відносно іншої під дією дотичних напружень. Обробка металів тиском — один з найпоширеніших, найпродуктивніших і найдешевших методів виготовлення заготовок (деталей) різної маси та розмірів з металів та сплавів.
Для отримання деталей та заготовок метали обробляють тиском такими способами:
- вальцювання — це обробка металу тиском, за якої заготовка обтискується обертовими валками прокатного стану;
- волочіння — це процес протягування заготовок крізь отвір, що поступово звужується;
- пресування (екструзія) — витискання металу із замкненого об'єму крізь калібрувальний отвір;
- кування — це оброблення металу тиском місцевого прикладення деформуючих ударних навантажень за допомогою універсального підкладного інструмента або бойків із вільним переміщенням металу у всіх напрямах[8];
- штампування — це спосіб отримання заготовок за допомогою штампів[8].
Термічне оброблення металів і сплавів
Термічне оброблення металів — оброблення, яке полягає в зміні структури та властивостей матеріалу заготовки внаслідок теплового впливу[9]. Технології термічного оброблення полягають у нагріванні металів (сплавів), витримуванні (якщо потрібно) у нагрітому стані й охолодженні із заданою швидкістю. Відомі з кінця 3-го тис. до н. е. Режими оброблення встановлюють за фазовими діаграмами стану, провадять його в термічних печах, використовуючи різні способи нагріву металу (у тому числі безокислювальний нагрів). Термооброблення застосовують як проміжну операцію, щоб поліпшити технологічні властивості металу (напр., оброблюваність тиском, різанням), і як заключну — для надання металові комплексу фізико-механічних властивостей.
До різних видів термообробки належать: відпалювання, відпуск металу, гартування, електротермічна обробка, ізотермічна обробка, нормалізація, патентування, штучне старіння металів, термомеханічна обробка, термохімікомеханічна обробка, хіміко-термічна обробка, лазерна обробка. Використовується, також, спосіб термоциклічного оброблення, яке полягає у чергуванні нагріву й охолодження металу без витримування при високій температурі. Це дає змогу одержувати дрібнозернисту структуру металу, підвищувати рівень його міцнісних і пластичних характеристик.
Нанесення захисних покриттів
Велике значення в металургії мають процеси нанесення на метал різноманітних покриттів, до яких крім хіміко-термічної обробки (алітування, титанування, берилізація тощо) належать, наприклад, плакування, газотермічне напилення (газополуменеве, електродугове, плазмове, детонаційне тощо), електрохімічне нанесення (хромування, цинкування, сріблення) тощо. Покриття найчастіше застосовуються з метою захисту металів від корозії. Покриття досить широко, також, використовуються в техніці для підвищення жаротривкості, зносостійкості, поверхневої твердості металевих виробів та з метою відновлення робочих поверхонь, пошкоджених внаслідок зношування, корозії, ерозії, кавітації.
Див. також
|
Примітки
- Karl Alfred von Zittel (1901) History of Geology and Palaeontology page 15
- ДСТУ 3790-98 Металургія кольорових металів. Терміни та визначення основних понять.
- ДСТУ 2751-94 Металургія порошкова. Терміни та визначення.
- Bridgman, Percy W. (1925). Certain Physical Properties of Single Crystals of Tungsten, Antimony, Bismuth, Tellurium, Cadmium, Zinc, and Tin. Proceedings of the American Academy of Arts and Sciences 60 (6): 305–383. doi:10.2307/25130058.
- J. Czochralski Ein neues Verfahren zur Messung der Kristallisationsgeschwindigkeit der Metalle [A new method for the measurement of the crystallization rate of metals], Zeitschrift für Physikalische Chemie, 1918, 92 : 219—221.
- William G. Pfann Zone Melting, 2nd edition. — John Wiley, 1966. & Sons
- ДСТУ 2541-94 Виробництво ливарне. Терміни та визначення.
- ДСТУ 2263 Операції кування та штампування металу. Терміни та визначення.
- ДСТУ 2391-94 Система технологічної документації. Терміни та визначення.
Література
- Мовчан В. П., Бережний М. М. Основи металургії. — Дніпропетровськ: Пороги, 2001. — 336 с.
- Основи металургійного виробництва металів і сплавів / Чернега Д. Ф., Богушевський В. С., Готвянський Ю. Я. та ін.; за ред. Д. Ф. Чернеги, Ю. Я. Готвянського. — К. : Вища школа, 2006. — 503 с. — ISBN 966-642-310-3
- Мала гірнича енциклопедія : у 3 т. / за ред. В. С. Білецького. — Д. : Донбас, 2007. — Т. 2 : Л — Р. — 670 с. — ISBN 57740-0828-2.
- Хомченко Г. П. Посібник з хімії для вступників до вузів [Текст]: [Пер. з рос.] / Г. П. Хомченко. — К.: А. С. К., 2004. — 480 с. — ISBN 966-539-424-Х
- Воскобойников В. Г. Общая металлургия [Текст]: учебник для вузов / В. Г. Воскобойников, В. А. Кудрин, А. М. Якушев. — 6-изд., перераб и доп. — М.: ИКЦ «Академкнига», 2005. — 768 с. — ISBN 5-94628-062-7.
- Технологія конструкційних матеріалів і матеріалознавство. Практикум [Текст]: [навч. посіб. для студ. вищ. навч. закл. за напрямом «Інж. механіка»] / В. В. Попович, А. І. Кондир, Е. І. Плешаков та ін. — Львів: Світ, 2009. — 551 c. — ISBN 978-966-603-401-7
- Матеріалознавство [Текст]: підручник / [Дяченко С. С., Дощечкіна І. В., Мовлян А. О., Плешаков Е. І.] ; ред. С. С. Дяченко ; Харківський нац. автомобільно-дорожній ун-т. — Х. : ХНАДУ, 2007. — 440 с. — ISBN 978-966-303-133-0
Посилання
- Металюрґія // Українська мала енциклопедія : 16 кн. : у 8 т. / проф. Є. Онацький. — Буенос-Айрес, 1961. — Т. 4, кн. VIII : Літери Ме — На. — С. 965. — 1000 екз.