Металообробка
Металообро́бка (англ. metalworking) — спільна назва низки технічних дисциплін і технологічних процесів, пов'язаних із вивченням та використанням методів і способів обробки металів (сплавів) у закінчені вироби або елементи машин із застосуванням відповідного обладнання, верстатів, інструментів та режимів впливу на об'єкт обробки.
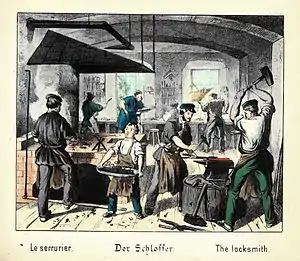
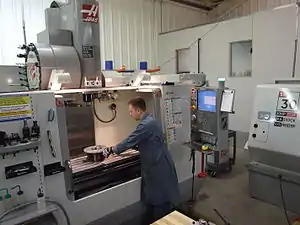
Під час технологічних процесів обробки металів різними методами змінюються форма і розмір об'єкту, а також можуть змінюватися фізико-механічні властивості металів.
Для обробки металів з метою їх зміни й досягнення поставлених цілей застосовуються різні методи обробки металів. Залежно від технологічних операцій, що застосовуються для надання виробам з металу певної форми, розмірів, шорсткості поверхні, точності, а також необхідних якостей і властивостей способи поділяються на види:
- лиття;
- обробка тиском (кування, вальцювання, штампування та ін.);
- механічна обробка за допомогою різних металорізальних верстатів та інструментів (точіння, свердління, фрезерування тощо);
- термічна обробка (гартування, відпуск та ін.);
- зварювання і паяння;
- хімічна і електролітична обробка (нанесення різних захисних і декоративних покриттів)
- газотермічне напилювання тощо.
Ливарне виробництво
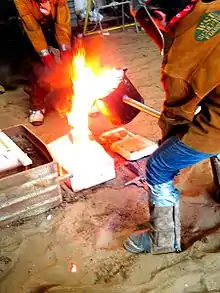
Ливарне виробництво — технологічний процес виготовлення виливків, що полягає в заповненні ливарної форми розплавленим матеріалом (ливарним металом чи сплавом) і подальшій обробці отриманих після твердіння виробів[1].
Ливарні форми можуть бути одноразовими і постійними. Одноразові форми виготовляють з формувальної суміші, вони придатні лише для однієї заливки; постійні — виготовляють з металу, вони придатні для виготовлення великої кількості відливок. Литтям виготовляють відливки різної конфігурації, розмірів і маси з необхідними фізико-механічними властивостями, вони можуть бути як готовими виробами, так і заготовками деталей для машинобудування.
Лиття часто не лише є найпростішим, але й найекономічнішим способом виробництва (литі деталі становлять близько 50 % від маси машини, а частка витрат на них — всього 15…25 %).
Виливки виготовляють з різних видів ливарних сплавів, які поділяються на чорні метали (сталь, чавун) і кольорові (сплави міді, алюмінієві сплави, магнієві сплави тощо).
Плавку чавунів проводять у вагранках, сталей в конверторах, електричних індукційних або дугових печах, кольорових металів та їх сплавів виконують у дугових печах, електричних печах опору, полуменевих печах, іноді в тиглях.
Розрізняють такі основні види лиття[1]:
- лиття в одноразову піщану форму — лиття металу, яке здійснюється заливанням ливарної форми, що виготовлена з піщаної формової суміші;
- кокільне лиття — лиття металу, яке здійснюється вільним (гравітаційним) заливанням кокілів;
- лиття під тиском — машинне лиття металу у прес-форму під тиском;
- лиття вакуумним всмоктуванням — лиття металу, що здійснюється у кокіль, який заповнюється металом за допомогою створеного в ньому вакууму
- відцентрове лиття — лиття металу, яке здійснюється при заливанні у відцентрову виливницю;
- лиття по витоплюваній (випалюваній) моделі — лиття металу, яке здійснюється заливанням суцільної ливарної форми, що виготовлена по витоплюваній (випалюваній) моделі.
Лиття застосовують для виготовлення: станин металообробного устаткування, блоків циліндрів і поршнів двигунів внутрішнього згоряння, радіаторів системи опалення тощо.
Оброблення металів тиском
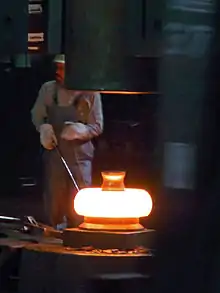
Оброблення металу тиском — сукупність технологічних процесів, внаслідок яких відбувається пластичне деформування або поділ металу на частини без утворення стружки[2].
При цьому виді обробки використовують властивість металу — пластичність (здатність під дією прикладених сил змінювати форму без руйнування) в холодному або у гарячому стані. Найпоширеніший механізм пластичної деформації — ковзання, зсув однієї частини тіла відносно іншої під дією дотичних напружень. Обробка металів тиском — один з найпоширеніших, найпродуктивніших і найдешевших методів виготовлення заготовок (деталей) різної маси та розмірів з металів та сплавів.
Тиском обробляють близько 90 % сталей та 55 % кольорових металів і сплавів.
Для отримання деталей та заготовок метали обробляють тиском наступними способами:
- вальцювання — це обробка металу тиском, за якої заготовка обтискується обертовими валками прокатного стану;
- волочіння — це процес протягування заготовок крізь отвір, що поступово звужується;
- пресування (екструзія) — витискання металу із замкненого об'єму крізь калібрувальний отвір;
- кування — це оброблення металу тиском місцевого прикладення деформуючих ударних навантажень за допомогою універсального підкладного інструмента або бойків із вільним переміщенням металу у всіх напрямах[2];
- штампування — це спосіб отримання заготовок за допомогою штампів[2];
- обкатування (розкатування) — вид обробки поверхонь металевих матеріалів при якому їх піддають обкатуванню чи розкатуванню роликами або кульками з метою зміцнення поверхневого шару й підвищення зносостійкості.
При обробці металів тиском втрати металів в порівнянні з іншими видами металообробки є меншими, тому цей метод обробки металів використовується дедалі ширше. Крім того, при обробці металів тиском існує можливість забезпечення високого рівня механізації і автоматизації технологічних процесів.
Обробкою металів тиском можуть бути отримані вироби з постійним або періодично змінним поперечним перерізом (вальцювання, волочіння, пресування) і штучні вироби різноманітних форм (кування, штампування), відповідні або близькі за формою і розмірами готовим деталям.
Обробка металів різанням
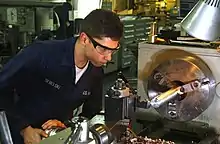
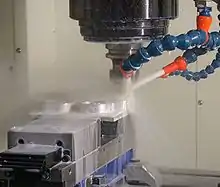
Оброблення різанням — вид механічного оброблення, яке полягає в утворенні нових поверхонь шляхом відділення поверхневих шарів матеріалу з утворенням стружки[3].
Основні принципи обробки різанням
Способи обробки металів тиском і литтям, зазвичай, не дають необхідної точності розмірів і чистоти поверхні заготовок (винятки складають спеціальні види лиття і холодне штампування). Тому куванням, штампуванням і литтям у більшості випадків виготовляють заготовки (напівфабрикати), що потребують додаткової обробки. Остаточна обробка виконується різанням, яке полягає в знятті з поверхонь заготовки визначеного шару металу, що залишається спеціально для цього. Шар металу, що знімається з металу, називається припуском на обробку. В результаті видалення припуску заготовка набуває точніших форми, розмірів та заданої шорсткості поверхонь, тобто перетворюється в деталь.
На цей вид оброблення припадає понад 90 % трудомісткості виготовлення більшості деталей. Для його реалізації існує ціла низка різноманітного металорізального обладнання, різного за розмірами, продуктивністю, ступенем автоматизації, яке забезпечує здійснення різних способів обробки різанням практично в усіх типах виробництва.
Обробка різанням є складним і дорогим процесом, який відрізняється значною трудомісткістю і значними втратами металу (при масовому виробництві зі стружкою втрачається 5 — 15 % металу, а при дрібносерійному і одиничному — до 25 %).
Класифікація методів обробки різанням
Обробка різанням включає дві множини способів її реалізації: лезову та абразивну обробки.
Лезова обробка передбачає оброблення поверхонь заготовки одно- та багатолезовими інструментами — різцями, свердлами, фрезами, розвертками, протяжками та ін.
Абразивна обробка — це обробка поверхонь абразивними інструментами, виготовленими з природних або штучних абразивних матеріалів, — абразивними кругами, сегментами, брусками, стрічками та вільними абразивами у вигляді порошків, паст тощо.
Усі способи обробки різанням поділяють, у свою чергу, за точністю та шорсткістю обробленої поверхні на:
- чорнові;
- напівчистові;
- чистові;
- оздоблювальні.
Реалізація обробки різанням
Кожен з цих процесів може бути ручним (слюсарна обробка) і механічним (верстатна обробка).
Слюсарна обробка є низькопродуктивною і застосовується тільки для підгонки деталей при складанні і ремонті. Основні види слюсарної обробки:
- Розмічання — операція нанесення розмічальних рисок або ліній на заготовках (виливках, поковках тощо), що визначають контури майбутньої деталі та припуски на оброблення або місця, що підлягають обробленню;
- Слюсарне рубання — слюсарна операція, коли за допомогою різального (зубила, крейцмейселя та ін.) та ударного (слюсарного молотка) інструмента з поверхні заготовки видаляють зайвий шар металу або розділяють заготовку на частини.
- Слюсаре різання — слюсарна операція відділення частини заготовок від сортового або листового металу. Різання здійснюють ручними або спеціальними ножицями (без зняття стружки), або ножівками чи на відрізних верстатах (із зняттям стружки). До різання також належить надрізування металу;
- Випрямляння та рихтування — це операції з випрямлення металу, заготовок і деталей, що мають вм'ятини, випини, хвилястість, жолоблення, викривлення тощо;
- Обпилювання — операція з обробки металів та інших матеріалів зняттям незначного шару напилками вручну або на обпилювальних верстатах.
- Шабрування — це точна обробка поверхні деталі шляхом знімання мікроскопічно тонкого шару металу за допомогою спеціального однолезового слюсарного інструмента — шабера
- Притирання — метод чистової абразивної обробки поверхонь деталей шліфувальними порошками чи пастами, за якого обробний інструмент і заготовка одночасно здійснюють відносний рух із швидкостями одного порядку, або в разі нерухомості одного з них інший здійснює складний рух
- Гнуття — утворення чи зміна кутів між частинами заготовки або надання їй криволінійної форми.
Верстатна обробка — виконується на металорізальних верстатах. При обробці заготовок в механічних цехах технологічний процес розділяється на окремі операції, що виконуються на різних верстатах із застосуванням різноманітних різальних інструментів і пристосувань. Щоб виконати обробку поверхні заготовки і одержати деталь заданої форми, необхідно закріпити заготовку і різальний інструмент та переміщувати їх в процесі обробки один відносно одного. При цьому на верстаті повинно виконуватись два рухи:
- головний рух різання, при якому лезо інструменту врізується в метал і відділяє від нього стружку;
- рух подачі необхідний для підводу під лезо нових шарів металу.
Основні види верстатної обробки можна класифікувати за видом поверхні, що обробляється на:
- обробку зовнішніх циліндричних поверхонь, до якої належать
- токарна обробка,
- циліндричне шліфування,
- притирання,
- обробка абразивним полотном,
- суперфінішування;
- обробку внутрішніх циліндричних поверхонь, до якої належать:
- розточування,
- свердління,
- зенкерування,
- розвірчування,
- протягування,
- внутрішнє шліфування,
- притирання,
- хонінгування;
- ультразвукова абразивно-імпульсна обробка
- обробку площин, що включає:
- стругання,
- фрезерування,
- плоске шліфування,
- притирання;
Термічна обробка
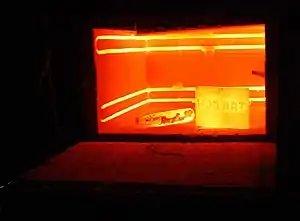
Термі́чне оброблення — оброблення, яке полягає в зміні структури та властивостей матеріалу заготовки внаслідок теплового впливу[3]. Застосовують також різні види хіміко-термічної обробки, сутність якої полягає в легуванні поверхневого шару виробів вуглецем, азотом або деякими металами (алюмінієм, хромом, берилієм тощо) з подальшою термічною обробкою або термомеханічного оброблення, при якому оброблення металів (сплавів) полягає у послідовному нагріванні їх до температури, вищої за верхню критичну точку поліморфного перетворення, пластичному деформуванні й гартуванні протягом одного технологічного процесу.
Види термічної обробки
Залежно від мети термічної обробки існують різні її види, що відрізняються температурою нагрівання, тривалістю витримування та швидкістю охолодження. Розрізняють такі види термічної обробки: Відпалювання, нормалізація, загартування і відпуск.
- Відпалювання (відпал) — вид термооброблення, який полягає в нагріванні матеріалу (метал тощо) до температури вище критичної точки, тривалій витримці за цієї температури і подальшому повільному охолодженні. Основними видами відпалювання є гомогенізувальне, графітизувальне, перекристалізаційне, рекристалізаційне, релаксаційне та сфероїдизувальне[4]. Графітизувальне та сфероїдизувальне відпалювання характерне лише для сталей. Відпалювання підвищує пластичність, зменшує внутрішні напруження та твердість сталей.
- Нормалізація — нагрівання до високої температури, видержування і повільне охолодження на повітрі. Нормалізація доводить сталь до дрібнозернистої та однорідної структури. Твердість і міцність сталі після нормалізації вищі, ніж після відпалу.
- Загартування — нагрівання до високої температури, витримування і швидке охолодження (у воді, мінеральній оливі та інших охолоджувачах). Є такі види загартування: в одному охолоджувачі; перервне; ступінчасте; ізотермічне; поверхневе та ін. Загартування сталей забезпечує підвищення твердості, виникнення внутрішніх напружень і зменшення пластичності. Твердість збільшується у зв'язку з виникненням таких структур: сорбіт, тростит, мартенсит. Практично загартуванню піддаються середньо- і високовуглецеві сталі.
- Відпуск — називають нагрівання до певної температури, витримування та повільне охолодження на повітрі. Розрізняють три види відпуску сталей: низький (нагрівання до температури 473 К; середній (573—773 К); високий (773—973 К). Після відпуску певною мірою зменшується твердість і внутрішні напруження, збільшується пластичність і в'язкість сталей. До цього приводить зміна структур після відпуску. Структура мартенситу сталі переходить відповідно в структуру трооститу і сорбіту. Чим вища температура відпуску, тим менша твердість відпущеної сталі і тим більша її пластичність та в'язкість.
- Відпуск, в основному, проводять після загартування для зняття внутрішніх напружень. Низький відпуск застосовують при виготовленні різального інструменту, вимірювального інструменту, цементованих деталей та ін; середній — при виробництві ковальських штампів, пружин, ресор; високий — для багатьох деталей, що зазнають дії високих напружень (осі автомобілів, шатуни тощо).
Види хіміко-термічної обробки
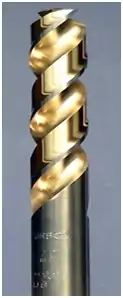
Хіміко-термічна обробка — це вид термічної обробки, що полягає в поєднанні термічного та хімічного впливу з метою зміни хімічного складу, структури і властивостей поверхневого шару металевого матеріалу виробу.
Мета хіміко-термічної обробки — надати поверхневому шару металевої деталі підвищеної твердості, зносостійкості, жаротривкості, корозійної стійкості тощо.
Хіміко-термічна обробка може передбачати:
- дифузійне насичення неметалами (вуглецем, азотом, бором та ін.);
- дифузійне насичення металами (дифузійна металізація — алюмінієм, хромом, цинком, титаном тощо);
- дифузійне видалення домішок (вуглецю, кисню, водню).
Найпоширенішими видами хіміко-термічної обробки сталі є:
- цементація — насичення поверхні сталевого виробу вуглецем з метою збільшення твердості на поверхні і збереження в'язкої серцевини;
- азотування — технологічний процес насичення поверхневого шару виробу азотом, щоб надати поверхневому шару виробу високої твердості, підвищити зносостійкість та опір агресивним середовищам;
- ціанування — насичення поверхневого шару виробів одночасно азотом (у більшій мірі) і вуглецем (у меншій мірі)
- дифузійна металізація — насичення поверхневого шару виробу різними металами (алітування, борування, хромування, силіціювання, берилізація тощо).
Термомеханічне оброблення
Термомеханічне оброблення — оброблення металів (сплавів), що полягає у послідовному нагріванні їх до температури, вищої за верхню критичну точку поліморфного перетворення, пластичному деформуванні й гартуванні протягом одного технологічного процесу, які обумовлюють формування підвищеної щільності дефектів кристалічної будови металу чи сплаву, що призводить до підвищення міцності[5].
Розрізняють декілька видів термомеханічної обробки, призначених головним чином для обробки сталей. Основні серед них — термомеханічне оброблення високо-(ВТМО) і низькотемпературне (НТМО). Якщо сталь піддавати високотемпературній обробці, її пластично деформують (ступінь деформування 20…30 %) в області температур стійкого аустеніту (вище від точки A3), що виключає (частково або повністю) рекристалізацію в процесі деформування. Під час низькотемпературного оброблення сталь деформують (Ступінь деформування 75…95 %) в області температур метастабільного аустеніту, нижчих від температури його рекристалізації. При гартуванні сталі після деформування мартенсит успадковує зміни структури аустеніту. В обох випадках після гартування проводять низький відпуск. ВТМО можна піддавати будь-які сталі, а НТМО — лише сталі з підвищеною стійкістю переохолодженого аустеніту (леговані сталі).
Зварювання та паяння
Зварювання
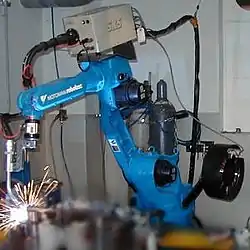
Зварювання — одержання нерознімних з'єднань шляхом утворення міжатомних зв'язків між з'єднуваними частинами в процесі їх нагрівання і (чи) пластичного деформування[3].
Відомо близько 70 способів зварювання. В основу їхньої класифікації покладено дві ознаки: агрегатний стан матеріалу в зоні зварювання та вид енергії, яка використовується для утворення з'єднання.
За видом енергії, що вводиться у виріб основні зварювальні процеси поділяють на:
- термічні;
- термомеханічні;
- термопресові;
- механічні;
- пресово-механічні.
За агрегатним станом матеріалу в зоні зварювання всі способи поділяються на зварювання плавленням (ручне дугове, газополум'яне, електрошлакове, плазмове, електронно-променеве тощо), тиском (зварювання вибухом, зварювання тертям) або поєднанням плавлення із стисканням (точкове зварювання, контактне зварювання, дифузійне зварювання тощо).
Паяння
Паяння — технологічний процес з'єднування заготовок нагріванням їх до температури плавлення металевого припою, нижчої від температури плавлення основного металу, з одночасним змочуванням розплавленим припоєм з'єднуваних поверхонь, затіканням його в щілини між ними та подальшою кристалізацією під час охолодження[6].
Електрофізичне оброблення
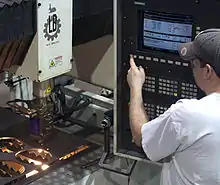
Електрофізичне оброблення — вид механічного оброблення, який полягає в зміні форми, розмірів та (чи) шорсткості поверхні заготовки із застосуванням електричних розрядів, магнітострикційного ефекту, електронного чи оптичного опромінювання, плазмового струменя[3].
До числа таких методів відносять:
- електроерозійні методи оброблення, котрі полягають у тому, що зміна форми, розмірів та якості поверхні заготовки відбувається під дією електричних розрядів. Електричні розряди виникають при пропусканні імпульсного електричного струму в зазорі величиною 0,01…0,05 мм між електродом-заготовкою і електродом-інструментом. Під дією електричних розрядів матеріал заготовки плавиться, випаровується і видаляється з міжелектродного проміжку в рідкому чи пароподібному стані. Електроерозійні методи у свою чергу за режимами поділяються на: електроіскрові та електроімпульсні
- променеве оброблення, що реалізується потоками високих енергій, котре поділяється на різновиди, що використовуються машинобудуванні: електроннопроменеве та світлопроменеве оброблення:
- плазмове оброблення — оброблення матеріалів низькотемпературною плазмою, що генерується дуговими або високочастотними плазмотронами.
Основною перевагою електрофізичних методів оброблення металів є можливість їх використання для зміни форми заготовок з матеріалів, що не піддаються обробці різанням, причому обробка цими методами відбувається в умовах дії мінімальних сил чи навіть при повній їх відсутності. Трудомісткість і тривалість цих методів обробки матеріалів підвищеної твердості (понад 400 HB) менша за трудомісткість і тривалість обробки різанням.
Важливою перевагою електрофізичних методів обробки металів є незалежність продуктивності більшості з них від твердості і крихкості оброблюваного матеріалу. Електрофізичні методи обробки металів охоплюють практично всі операції механічної обробки і не поступається більшості з них за шорсткітю обробленої поверхні і точністю виготовлення.
Електрохімічне оброблення
Електрохімічне оброблення — спосіб механічного оброблення електропровідних матеріалів, що полягає у зміні форми, розмірів і (або) шорсткості поверхні заготовки внаслідок анодного розчинення її матеріалу в електроліті під впливом електричного струму
Електрохімічне оброблення базується на явищі локального анодного розчинення металу при електролізі. Один з електродів (заготовка) приєднаний до позитивного полюса джерела живлення і є анодом, а другий (інструмент) — до негативного; останній є катодом. Особливостями електролізу є просторове окислення (розчинення) анода і відновлення (осадження) металу на поверхні катода.
Основними різновидами електрохімічного оброблення є.
- за метою обробки[7]:
- електрохімічне поверхневе оброблення (електрохімічні: шліфування, полірування, доведення тощо);
- електрохімічне розмірне оброблення (електрохімічні: об'ємне копіювання, прошивання, калібрування, точіння, видалення задирок, маркування тощо).
- за принципом реалізації:
- анодно-механічне оброблення — вид електрохімічного оброблення у рідкому середовищі, при якому відбувається розчинення матеріалу заготовки під дією електричного струму з утворенням на поверхні обробки окисних плівок та їх видалення механічною дією;
- катодне оброблення (катодне відновлення металу) — електрохімічний спосіб одержання металевого покриття на металі, який використовується як катод.
Газотермічне напилення
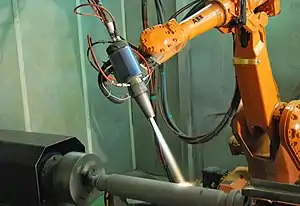
Газотермічне напилення — одержання покриття із нагрітих та прискорених частинок напилюваного матеріалу із застосуванням високотемпературного газового струменя, в результаті зіткнення яких з основою або напиленим матеріалом відбувається їх з'єднання за рахунок зварювання, адгезії та механічного зчеплення[8].
Під загальною назвою «газотермічне напилювання» (ГТН) об'єднують такі методи[9][8]:
- газополуменеве напилювання — газотермічне напилювання, під час якого використовується струмінь продуктів згорання суміші газів, які спалюються за допомогою пальника;
- високошвидкісне (надзвукове) газополуменеве напилювання (HVOF — англ. High velocity oxygen fuel — високошвидкісний киснево-паливний метод) — одна з технологій газотермічного напилювання захисних покриттів, при якій порошковий матеріал наноситься на підкладку на високій (зазвичай до 3 швидкостей звуку);
- детонаційне напилювання — газотермічне напилювання, під час якого використовується струмінь продуктів детонації;
- плазмове напилювання — газотермічне напилювання, під час якого використовується струмінь електронів, іонів та нейтральних атомів газу, з якого утворюється плазма, різновидами якого можна вважати:
- плазмово-дугове напилювання — плазмове напилювання, під час якого плазмовий струмінь створюється за допомогою електричної дуги;
- надзвукове плазмове напилювання — плазмово-дугове напилювання, під час якого плазмовий струмінь витікає з надзвуковою швидкістю;
- напилювання з оплавленням — метод газотермічного напилювання, що дозволяє отримати щільні зносостійкі корозійностійкі покриття з високою адгезією;
- електродугове напилювання — газотермічне напилювання, під час якого нагрівання та плавлення напилюваного металу у вигляді дроту, стрижня або стрічки здійснюється електричною дугою, а диспергування струменем стисненого газу, звичайно повітря.
Зазвичай газотермічне напилення застосовують для створення на поверхні деталей та обладнання функціональних покриттів — зносостійких, корозійно-стійких, антифрикційних, протизадирних, теплостійких, термобар'єрних, електроізоляційних, електропровідних тощо. Матеріалами для напилення служать порошки, шнури і дроти з металів, металокераміки і кераміки.
Примітки
- ДСТУ 2541-94 Виробництво ливарне. Терміни та визначення.
- ДСТУ 2263 Операції кування та штампування металу. Терміни та визначення.
- ДСТУ 2391-94 Система технологічної документації Терміни та визначення.
- ДСТУ 3790-98 Металургія кольорових металів. Терміни та визначення основних понять.
- ДСТУ 2494-94 Метали. Оброблення зміцнювальне. Терміни та визначення.
- ДСТУ 3761.2-98 Зварювання та споріднені процеси. Частина 2 Процеси зварювання та паяння. Терміни та визначення.
- ГОСТ 25330-82 Обработка электрохимическая. Термины и определения.
- ДСТУ 3761.5-98 Зварювання та споріднені процеси. Частина 5. Газотермічне напилення. Терміни та визначення.
- Kuroda, Seiji; Kawakita, Jin; Watanabe, Makoto; Katanoda, Hiroshi (2008). Warm spraying—a novel coating process based on high-velocity impact of solid particles. Sci. Technol. Adv. Mater. 9 (3): 033002. doi:10.1088/1468-6996/9/3/033002.[недоступне посилання з квітня 2019]
Джерела
- Литейное производство. / Под ред. А. М. Михайлова. — М.: Машиностроение, 1987. — 256 с.
- Попович В. В. Технологія конструкційних матеріалів і матеріалознавство: [підручник для студ. вищ. навч. закл.] / В. В. Попович, В. В. Попович. — Львів: Світ, 2006. — 624 с. — ISBN 966-603-452-2.
- Матеріалознавство і технологія конструкційних матеріалів / [навч. посібник для учнів проф. навч. зал.] /Хільчевський В. В., Кондратюк С. Є., Степаненко В. О., Лопатько К. Г. К.: Либідь, 2002. — 328 с. — ISBN 966-06-0247-2
- Основи формоутворення поверхонь при механічній обробці: Навч. посібник / Н. С. Равська, П. Р. Родін, Т. П. Ніколаєнко, П. П. Мельничук.- Ж.: ЖІТІ, 2000. — 332с. — ISBN 966-7570-07-X.
- Металорізальні інструменти: Навч. посібник. Ч.2 / П. Р. Родін [та ін.]; Київський політехнічний ін-т. — К.: ІСДО, 1993. — 180 с. — ISBN 5-7763-1585-4.
- Богуслаєв В. О. Основи технології машинобудування: Навч. посібник / В. О. Богуслаєв, В. І. Ципак, В. К. Яценко. — Запоріжжя: Мотор СІЧ, 2003. — 336 с. — ISBN 966-7108-70-8.
- Хільчевський В. В. Матеріалознавство і технологія конструкційних матеріалів: Навчальний посібник. К.: Либідь, 2002. — 328 с. ISBN 966-06-0247-2
- Черненко В. С., Кіндрачук М. В., Дудка О. І. Променеві методи обробки: Навч. посібник. — К.: Кондор, 2004. — 166 с.
- Справочник по электрохимическим и электрофизическим методам обработки / Г. Л. Амитан, И. Е. Байеупов, Ю. М. Барон и др.; Под общ. ред. В. А. Валосатого. — Л.: Машиностроение, 1988. — 719 с. — ISBN 5-217-00267-0
- Житников В. П., Зайцев А. Н. Импульсная электрохимическая размерная обработка. — М.: Машиностроение, 2008. — 413 с.
- Інженерія поверхні: Підручник / К. А. Ющенко, Ю. С. Борисов, В. Д. Кузнецов, В. М. Корж — К.: Наукова думка, 2007. — 559 с. — ISBN 978-966-00-0655-3
- Газотермические покрытия из порошковых материалов / Ю. С. Борисов, Ю. А. Харламов, С. Л. Сидоренко, Е. И. Ардатовская / Справ. — К.: Наукова думка, 1987. — 544 с.